Exploring Automatic Robotic Arms: Design and Impact
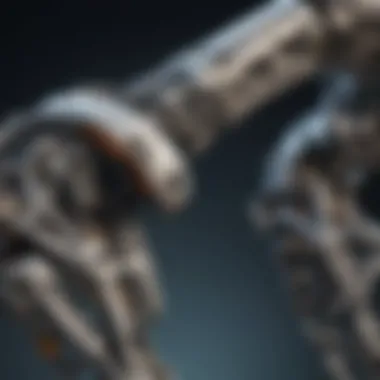
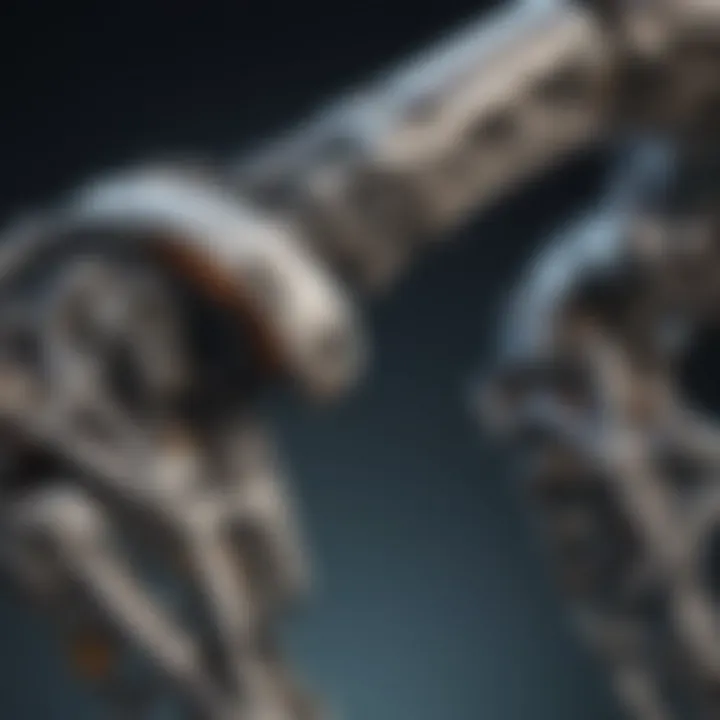
Intro
The advent of automatic robotic arms marks a significant transition in various sectors, from manufacturing to healthcare. As they gain presence in our daily lives, understanding their functionality and implications becomes vital. With their design rooted in both mechanical engineering and artificial intelligence, these tools not only streamline production but also open avenues for innovation and efficiency.
Automatic robotic arms utilize sophisticated algorithms to perform tasks with precision. Their operational mechanisms have evolved, integrating machine learning for improved adaptability. The implications of their incorporation into industries extend beyond mere efficiency; they raise crucial questions about labor dynamics and ethical standards in technology. As we journey through this fascinating realm, we’ll unravel the multifaceted roles these robotic arms play.
\n
Research Overview
Summary of Key Findings
Through extensive exploration, several key findings emerge:
- Versatility: Robotic arms are employed across diverse fields, displaying capabilities in assembly lines, surgical operations, and even domestic environments.
- Enhanced Precision: Due to AI integration, these devices can perform tasks with a level of precision that is often unattainable for human workers.
- Job Transformation: The introduction of robotic arms does not merely replace human labor; instead, it transforms the roles of workers, necessitating adaptation and skill evolution.
- Ethical Dilemmas: With increased functionality comes the moral responsibility of ensuring that these technologies are used equitably and do not exacerbate unemployment issues.
Importance of the Research
The significance of this research lies in its capacity to illuminate the transformation in industries driven by robotic technology. By understanding the intricate balance between innovation and ethical implications, stakeholders can better prepare for shifts in job markets, security concerns, and the societal impact of automation. This inquiry is pivotal not just for engineers and developers, but also for policymakers and business leaders seeking to navigate this rapidly changing landscape.
\n
Methodology
Study Design
This investigation employs a mixed-methods approach—both qualitative and quantitative. Surveys and interviews with industry professionals provide insight into the real-world applications and perceptions of automatic robotic arms.
Data Collection Techniques
- Surveys: Distributed to various sectors, gathering data about the implementation and effectiveness of robotic arms.
- Interviews: Conducted with engineers and managers to discuss design challenges and user experiences.
- Case Studies: In-depth analysis of specific industries that have integrated these technologies, offering practical examples of success and areas for improvement.
\n
"In many cases, robotic arms have been viewed as a double-edged sword, serving as both a pathway to greater efficiency and a source of labor displacement."
This comprehensive exploration builds the framework for understanding not only how robotic arms function, but also their broader implications for society and industry.
Intro to Automatic Robotic Arms
The landscape of technology has evolved rapidly, reshaping our interaction with machines and automation. Automatic robotic arms stand at the forefront of this transformation, particularly in industries where precision, efficiency, and repeatability are paramount. By deploying robotic arms, businesses can streamline operations, reduce human error, and enhance productivity. Their significance extends beyond mere functionality; they embody a shift in how tasks are perceived and executed.
Historical Background
The journey of robotic arms can be traced back to the mid-20th century. The first industrial robot, Unimate, was introduced in 1961, designed by George Devol and later commercialized by Victor Scheinman. It revolutionized assembly lines, particularly in the automotive sector, by performing repetitive tasks previously executed by human workers. Over the decades, technological advancements have propelled robotic arms from simple mechanical devices to sophisticated systems integrated with sensors, AI, and software. These developments were not just linear; they brought about significant shifts in various fields like manufacturing, healthcare, and logistics.
Definition and Characteristics
Automatic robotic arms can be defined as programmable mechanical devices capable of performing a range of tasks. In essence, these arms replicate human actions but with increased speed and accuracy. Key characteristics of these robotic arms include:
- Degrees of Freedom: This refers to the number of independent movements a robotic arm can perform. More degrees allow for more intricate tasks.
- End Effectors: These tools are attached to the end of the arm, enabling specific functions such as gripping, welding, or painting.
- Feedback Systems: Implemented to increase accuracy, these utilize sensors to provide information about the arm’s position and environmental conditions.
- Programs and Interfaces: Operating robotic arms involves programming languages and interfaces, which allow users to command the arm through scripts or visual programming tools.
In sum, understanding automatic robotic arms requires an appreciation of their historical context and an awareness of their defining characteristics. As industries continue to adopt automation at an unprecedented pace, the implications of these technologies are becoming ever more vital to our understanding of productivity and efficiency.
Design Principles of Robotic Arms
Understanding the design principles behind robotic arms is paramount. These principles create the backbone for how these machines operate, influencing everything from their efficiency to their application in various fields. The key focus remains on specific elements such as joints, actuators, sensors, kinematics, dynamics, and material choice. In this section, we will explore these components and their significance in optimizing the functionality of robotic arms.
Key Components
Joints
When it comes to robotic arms, joints serve as the connection points between segments of the arm. They play a critical role in defining the arm's range of motion. Understanding the specific types of joints, such as revolute and prismatic joints, can illuminate their contribution effectively.
A revolute joint allows for rotation around an axis, often found in applications requiring collision-avoidance strategies and tasks with a circular motion. In contrast, a prismatic joint enables sliding motion, crucial for extending the reach of robotic arms. The usage of combinations of these joints enables diverse movement patterns, thus enhancing the versatility of robotic arms.
The primary advantage of joints is their ability to facilitate various degrees of motion, allowing robotic arms to mimic human-like capabilities. However, a challenge lies in ensuring that these joints maintain precision over time, as wear and tear can lead to performance issues.
Actuators
Actuators essentially serve as the muscles of robotic arms, converting energy into physical motion. They come in various forms, including electric, hydraulic, and pneumatic actuators. The choice of actuator significantly influences both the speed and force output of the robotic arm, hence its effectiveness in meeting operational requirements.
Electric actuators stand out for their efficiency and simplicity but may fall short in high-load applications. On the other hand, hydraulic actuators offer immense strength but at a higher operational cost and complexity. Understanding the unique features of each actuator type is key to making informed design choices that align with specific applications – a high-speed packaging operation, for instance, might prioritize lighter electric actuators.
The major drawback of actuators can sometimes be their maintenance and operational costs, especially in a hydraulic setup. However, their critical role in algorithmic precision cannot be overstated.
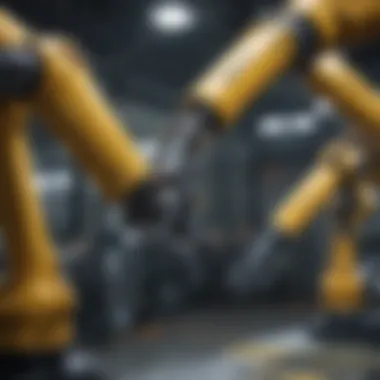
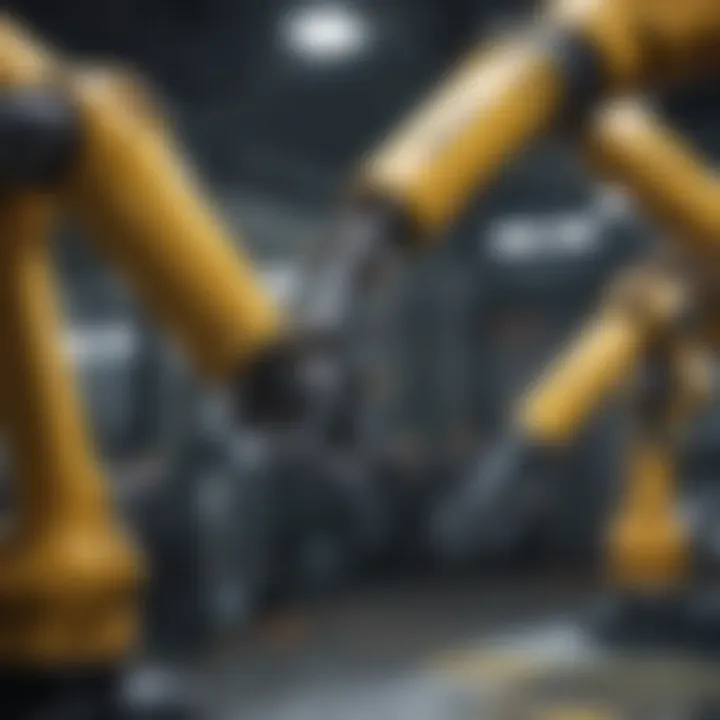
Sensors
Sensors transform robotic arms from simple machines into adaptive systems. They collect data and feedback that inform the robot's responses to its environment. Proximity sensors, force sensors, and vision systems are among the most prevalent types in modern robotic arms. Each type of sensor offers distinct advantages that can enhance the arm's responsiveness and accuracy.
For example, force sensors allow the robotic arm to detect resistance, critical for delicate tasks like assembling electronics, where too much force could cause damage. Meanwhile, visual sensors open the door to enhanced navigation and object recognition, necessary for complex manufacturing processes.
However, sensors must be carefully calibrated to avoid misreadings, which can lead to errors in operations. Balancing sensitivity and specificity is crucial, making the sensor choice a significant consideration during the design phase.
Kinematics and Dynamics
Forward Kinematics
Forward kinematics deals with calculating the position and orientation of the end effector of a robotic arm based on the given joint parameters. This mathematical approach helps to visualize how various joint configurations will result in specific end effector positions. Its benefit lies in the straightforward computation of outcomes, critical for programming tasks where predetermined positions are necessary.
The primary characteristic of forward kinematics is its predictability in motion. When programmed correctly, it can automate complex patterns without constant supervision. However, its simplicity also presents a limitation; it does not address reversibility, meaning feedback from the end effector can't be directly processed as joint angles.
Inverse Kinematics
On the flip side, inverse kinematics is considered a complex yet indispensable aspect of robotic design. This process calculates the necessary joint parameters needed to achieve a desired position or orientation of the end effector. It is particularly valuable in dynamic environments where the robotic arm must adapt its movements continually.
The main draw of inverse kinematics is its ability to facilitate intricate movements that would otherwise be impossible to calculate through forward kinematics alone. This often comes with higher computational requirements, particularly in complex configurations, leading to potential lag in real-time applications.
Materials and Construction
Lightweight Materials
The choice of lightweight materials is essential in robotic arm design, as it directly impacts agility and energy efficiency. Common materials include aluminum and carbon fiber, both offering high strength-to-weight ratios, allowing for faster movements with lower energy consumption. Their versatility makes them highly favored in applications requiring rapid response times.
The drawback, however, lies in the potential trade-off with durability. Lighter materials can compromise the structural integrity under certain loading conditions, which might require additional engineering to maintain a balance between weight and strength.
Durability Needs
Considering the durability needs in robotic arm construction is crucial. Materials often face wear and tear depending on their application, making it necessary to choose materials that can withstand the operational environment while also supporting long lifecycles. Steel and alloy compositions come into play where strength is non-negotiable, especially in manufacturing settings.
What's unique about the durability aspect is that it informs the maintenance regime. A highly durable robotic arm may demand less frequent maintenance and ultimately lead to cost savings in long-term operation. However, integrating durability often increases initial costs, which can be a worthwhile trade-off given the potential for increased reliability.
"The optimal performance of robotic arms largely lies in how well their design principles are integrated, making every detail count."
In summary, the design principles of robotic arms hinge on a blend of key components, kinematic considerations, and material choices. Understanding each principle allows designers to tailor their solutions, ensuring that robotic arms are adept at meeting a variety of ever-evolving operational demands across industries.
Operational Mechanisms
Understanding the operational mechanisms of automated robotic arms is crucial to grasp their broader implications in various industries. These mechanisms not only dictate how effectively a robotic arm performs its tasks but also determine its adaptability and precision across different environments. The choice of programming languages and control systems plays a pivotal role in transforming a conceptual design into a practical tool capable of executing intricate functions.
Programming Languages and Software
Programming languages form the backbone of robotic arm operation. They allow developers to create the software that guides these machines, translating human logic into executable instructions.
Python
Python, known for its simplicity and readability, has become a favorite among roboticists. Its large library ecosystem, particularly frameworks like TensorFlow or OpenCV, makes it an excellent fit for tasks that require machine learning or image processing.
- Key Characteristic: Python's syntax is approachable, making it easier for newcomers to learn and adapt.
- Unique Feature: The extensive libraries available facilitate quick development and prototyping, a major plus in the fast-paced world of robotics.
- Advantages: Its versatility allows it to be used in various applications, from basic control functions to more complex AI implementations.
- Disadvantages: However, it may not be the best choice for real-time control tasks where execution speed is critical. Python often runs slower compared to compiled languages.
++
On the flip side, C++ is heralded for its performance and fine-grained control over system resources, a valuable trait when it comes to robotic arms that require real-time operations.
- Key Characteristic: C++ is a compiled language, generally leading to faster run times compared to interpreted languages like Python.
- Unique Feature: It provides low-level access to memory, which allows for optimization critical in tasks demanding high precision, such as surgical robots.
- Advantages: The language’s capability to directly manipulate hardware makes it suitable for applications where speed and efficiency are paramount.
- Disadvantages: Nevertheless, its complexity can pose a steep learning curve for those unfamiliar with programming, potentially limiting its accessibility to non-experts.
Control Systems
Control systems are integral to managing the movements and operations of robotic arms, ensuring they function reliably in a variety of settings. Two primary types stand out - PID Control and Fuzzy Logic Control.
PID Control
PID Control (Proportional-Integral-Derivative Control) is widely acknowledged for its effectiveness in automation. This control mechanism adjusts outputs based on the difference between a desired setpoint and a measured process variable.
- Key Characteristic: It continuously modifies the output based on three parameters: proportional, integral, and derivative, allowing for stable and accurate operations.
- Unique Feature: PID controllers excel in scenarios requiring steady-state performance, making them efficient for tasks like positioning robotic arms in manufacturing.
- Advantages: This technique is straightforward to implement and tune, which is key for applications where consistency is paramount.
- Disadvantages: However, they struggle with non-linear systems and unexpected disturbances, requiring additional strategies to address these challenges.
Fuzzy Logic Control
Fuzzy Logic Control takes a different approach by allowing machines to make decisions based on vague or imprecise information, mimicking human reasoning. This system is particularly beneficial in unpredictable environments.
- Key Characteristic: It operates on degrees of truth rather than the usual true/false binary logic, making it more adaptable to changing conditions.
- Unique Feature: Fuzzy systems can handle uncertain data, making them ideal for robotic arms that must navigate unpredictable tasks or environments, like agricultural settings.
- Advantages: Their flexibility allows for smoother transitions in operations, as they can make adjustments based on real-time feedback.
- Disadvantages: The complexity of designing fuzzy logic systems may complicate their implementation and require more extensive tuning than simpler control methods.
The effectiveness of control systems truly determines the performance of an automaton, influencing its precision, speed, and reliability across diverse applications.
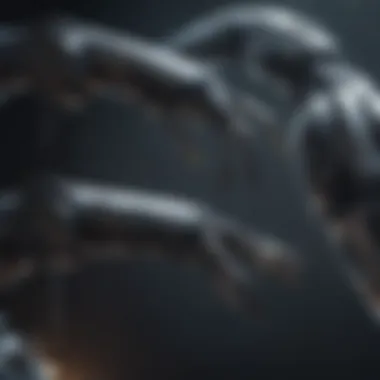

Integration of AI and Machine Learning
The topic of integrating artificial intelligence and machine learning into automatic robotic arms is not just timely; it’s essential in today’s technological landscape. The role of AI and machine learning in robotic systems transforms not merely how tasks are accomplished, but fundamentally reshapes the capability and efficiency of robotic arms in various settings. This integration has proven to streamline operations, enhance precision during complex tasks, and adaptively improve performance.
Enhancing Precision
Precision is the lifeblood of any robotic application, particularly when it comes to delicate procedures or intricate assembly tasks. Through the incorporation of AI-driven algorithms, robotic arms are now capable of executing movements with an astonishing degree of accuracy. The methodologies employed involve a combination of computer vision and real-time data processing.
For instance, a robotic arm used in a manufacturing line can utilize computer vision to analyze the alignment of components within milliseconds.
- Real-time Feedback: By continuously receiving data from sensors, these arms can adjust their movements instantaneously to ensure that every part is placed perfectly without oversight.
- Data Processing: Machine learning models can analyze past production data to predict and compensate for potential errors during operation. This all leads to finished products that adhere to strict quality standards, minimizing the risk of defects.
Furthermore, with advancements in deep learning techniques, the systems can learn from their experiences, refining their accuracy with each cycle they undertake. It’s remarkable how little adjustments, made in real-time, can lead to significant improvement in overall output.
"Robotics powered by AI isn’t just about automation; it’s about enhancing the intricate dance between machines and tasks, ensuring every choreographed move hits the mark."
Adaptive Learning
Adaptive learning is yet another compelling aspect of integrating AI into robotic systems. Unlike traditional robotic arms that follow pre-programmed instructions rigidly, these intelligent systems evolve their operational approaches based on accumulated experience.
- Dynamic Environmental Interaction: A robotic arm employed in agriculture, for example, can learn to interpret the diverse conditions of a field, such as soil type or growth patterns, and alter its method of planting or harvesting accordingly.
- User Interaction: In healthcare, surgical robots equipped with machine learning capabilities can adapt to a surgeon's specific style or technique over time, learning the nuances of their preferred approach, ensuring higher consistency in operations.
This level of adaptability not only aids in production efficiency but also significantly decreases downtime. As robotic systems become more adept at self-correction and learning, they’ll drive a new wave of advancement across industries, raising efficiency levels while also accommodating human operators through seamless collaboration.
Applications across Industries
The evolution of automatic robotic arms has cast a long shadow across various sectors, becoming a crucial tool that reshapes operational frameworks and elevates productivity. The importance of exploring Applications across Industries lies not only in understanding how these systems function but also in recognizing the broad spectrum of benefits they offer. Robotic arms serve not just as mere machines; they embody a marriage of technology and human ingenuity, poised to tackle both mundane and complex tasks at a scale previously thought unattainable.
Manufacturing
In the manufacturing arena, robotic arms have revolutionized processes, replacing or assisting human labor in repetitive tasks such as assembly line operations, packaging, and quality control. These machines enhance efficiency by executing tasks with precision and reliability that often surpasses human ability. For instance, the implementation of robotic arms in car manufacturing has enabled just-in-time production strategies, reducing waste and optimizing material use. Furthermore, they can operate in environments hazardous to humans, ensuring safety while maintaining output.
Adoption of robotic arms is not without challenges, as initial setup costs and maintenance can be a hurdle for smaller manufacturers. However, the long-term gains in productivity often outweigh the upfront investment, making them an essential part of modern manufacturing.
Healthcare
Within the healthcare sector, robotic arms are carving out remarkable niches, particularly in surgery and rehabilitation.
Surgical Robots
Surgical robots are changing the landscape of operations, offering surgeons enhanced dexterity and precision. The da Vinci Surgical System is a prime example, allowing minimally invasive procedures that reduce recovery times for patients. One of the key characteristics of surgical robots is their ability to perform complex maneuvers with utmost accuracy, utilizing high-definition 3D vision.
The unique feature of surgical robots lies in their robotic arms with multiple degrees of freedom, which allow for intricate procedures that would be difficult for a human surgeon to achieve alone. While these systems bring about substantial advantages, such as reduced patient trauma and shorter hospital stays, they also pose challenges, including high operational costs and the need for specialized training for healthcare professionals.
Rehabilitation Robots
Rehabilitation robots aim at restoring motor functions in patients recovering from strokes or injuries, offering a structured and measurable approach to physical therapy. An example of rehabilitation robots includes Lokomat, which supports patients during gait training. The key characteristic here lies in providing repetitive motion therapy, which is fundamental in regaining muscle strength and coordination.
The uniqueness of rehabilitation robots is their ability to tailor exercises to individual patient needs through adaptive feedback, enhancing the recovery process. On the flip side, while beneficial, there is a concern regarding accessibility for all patients, especially in underfunded healthcare systems.
Agriculture
In agriculture, robotic arms are vital for tasks such as planting, harvesting, and monitoring crops. They allow for precision agriculture, which utilizes data analytics to improve yield and efficiency. With climate change increasing unpredictability, leveraging robotics can help make farming more resilient by optimizing resource usage.
The deployment of robotic systems in agriculture not only enhances productivity but also reduces the strain on labor that traditional farming methods face. As demand for food grows, the role of these automation systems becomes imperative in ensuring sustainability and meeting consumer expectations.
Logistics and Warehousing
Robotic arms in logistics and warehousing transform how goods are handled from the moment they arrive until they are dispatched. Implementations like Amazon’s Kiva robots streamline warehouse operations by automating the sorting and retrieval processes. This results in faster order fulfillment — a critical competitive edge in today's consumer landscape.
These robotic arms are designed for speed and efficiency, working alongside human employees to boost productivity. However, questions arise about labor displacement and what that means for employment in this industry. Effectively integrating robotics while maintaining a skilled workforce is necessary to ensure a balanced approach as industries evolve.
In summary, the applications of automatic robotic arms across diverse sectors underline their transformative potential. Each industry wrestles with unique challenges and benefits, yet the overarching narrative revolves around efficiency, precision, and sustainability, leading to a future that leverages technological advancements for widespread betterment.
Ethical Considerations and Societal Impact
The deployment of automatic robotic arms instigates a myriad of ethical considerations and societal implications. As these machines gradually infiltrate various sectors, it becomes crucial to dissect their influence on human jobs, algorithmic biases, and the broader societal framework. Understanding these aspects not only enriches the discourse around robotics but also paves the way for addressing the potential pitfalls associated with their integration into everyday life.
Job Displacement Concerns
One of the most pressing issues surrounding the rise of robotic arms is job displacement. As these machines acquire the capability to perform tasks traditionally held by humans, the fear of losing employment becomes palpable. In manufacturing, for instance, a shift towards automation means that assembly line jobs, which once employed thousands, may dwindle as robots undertake routine and repetitive tasks. This can lead to significant economic shifts.
However, the narrative isn't entirely gloom and doom. While it is true that certain roles might vanish, it is equally important to consider the jobs that arise from increased automation. New roles in programming, maintenance, and oversight of these robotic systems may emerge, demanding a different skill set—a trend that often requires a recalibration of workforce training programs.
To mitigate the socioeconomic impact, there is a collective responsibility among industries, governments, and educational institutions to foster a culture of continuous learning and adaptation. Education systems must evolve in tandem with technological advancements, thereby equipping individuals with skills necessary for the future workforce.
Bias and Fairness in Algorithms
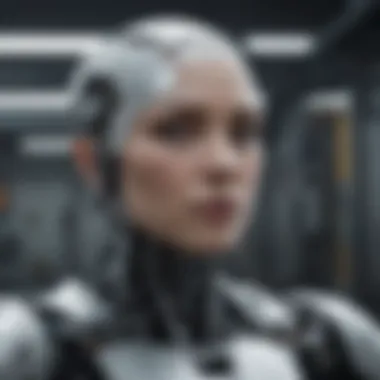
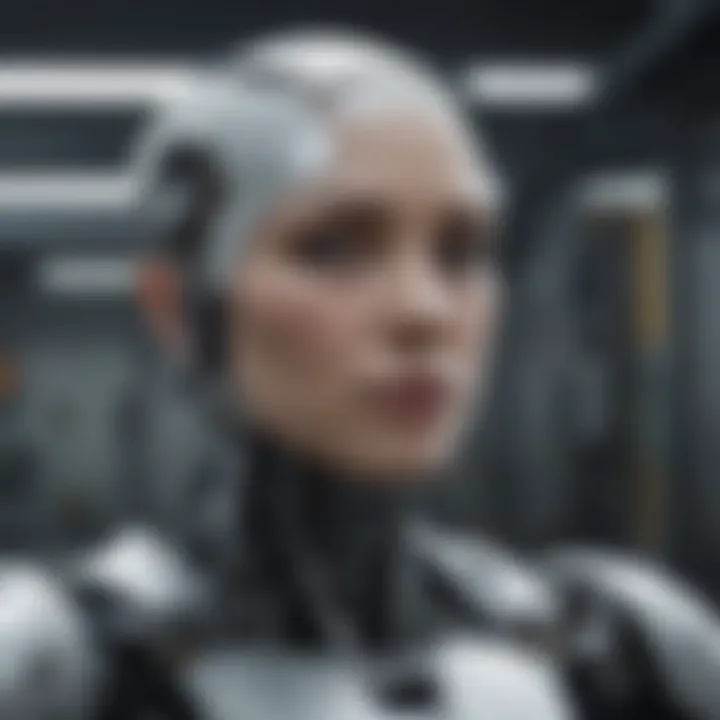
The algorithms steering robotic arms need scrutiny, especially in terms of bias and fairness. As these machines learn from vast datasets, they can inherit biases reflected in the data they process. For example, if a robotic system is trained on historical data that contains racial or gender biases, it may replicate those biases in its actions. This can lead to ethical quandaries—especially in applications like healthcare or law enforcement—where decisions made by robots can have substantial repercussions on individuals' lives.
To counter this tendency toward bias, developers must prioritize fairness in algorithm design, ensuring diverse datasets are utilized during the training phases. It is not merely a technical challenge but a sociocultural one, as programmers must consciously strive for inclusivity in their designs.
Moreover, transparency is key. Stakeholders must be aware of how decisions are made within these systems, fostering trust in robotic technologies. Highlighting how algorithms operate can encourage accountability, allowing individuals to understand and question the decisions made by robotic arms, whether in healthcare surgeries or logistical operations.
"The societal impact of robotic arms is a double-edged sword. While they can significantly boost productivity, they also hold the power to displace human workers and reinforce existing inequalities if biases go unchecked."
In summary, as we wind our way through the increasing integration of automated robotic arms, it’s essential to maintain a vigilant eye on these ethical considerations. Addressing job displacement and algorithmic bias head-on will not only facilitate smoother incorporation of robotics into society but ensure these advancements do not come at the cost of fairness and equality.
Future Trends and Innovations
The discussion surrounding automatic robotic arms isn't just about the present; it's also about what lies ahead. As technology evolves and industries adapt, understanding the future trends and innovations in this field is vital. Awareness of these changes can lead to enhanced productivity, improved safety measures, and even expanded roles for robotic arms in everyday life. Companies need to stay ahead of the curve to remain competitive in an increasingly tech-driven world. In this context, two noteworthy avenues stand out: collaborative robots, or cobots, and soft robotics.
Collaborative Robots (Cobots)
Collaborative robots, often dubbed cobots, are designed to work alongside humans rather than replacing them. This cooperation opens up a treasure trove of advantages. For instance, in manufacturing environments, cobots can handle repetitive tasks, allowing human workers to focus on more complex, value-added activities. The flexible deployment of these robots means they can adapt to various functions within a workspace based on current needs.
Furthermore, safety features are paramount in cobot design. These robots are equipped with sensors to detect human presence, enabling them to halt operations if someone comes too close. This attribute transforms potentially hazardous environments into safer workplaces, thus increasing employee morale and reducing the risk of workplace accidents.
- Benefits of Cobots:
- Enhanced human-robot collaboration.
- Increased productivity by managing repetitive tasks.
- Improved safety measures in industrial settings.
The ease of programming cobots often makes them more accessible for small to medium-sized enterprises. For example, using graphical programming interfaces, operators with minimal coding experience can easily adjust the functionalities of these robots. This accessibility not only democratizes automation but also accelerates the pace at which industries can implement robotic solutions.
Soft Robotics
Soft robotics introduces a different paradigm, focusing on flexibility and adaptability using materials reminiscent of biological organisms. Rather than rigid structures, soft robotic arms and grippers are made from silicone and other compliant materials, enabling them to conform to various shapes and objects. This adaptability makes them particularly useful in specific sectors, such as agriculture and delicate item handling.
The soft structures mean these robots can perform tasks that require a gentler touch, such as picking fruits or assembling intricate components without causing damage. Soft robotics redefines what robotic arms can achieve, moving beyond traditional functionalities into realms where precision and care are paramount.
- Key Aspects of Soft Robotics:
- Use of compliant materials for enhanced flexibility.
- Applications in tasks requiring delicate handling.
- Potential for innovative designs that mimic natural organisms.
As we step into the future, the amalgamation of cobots and soft robotics represents a trend where human and robotic capabilities converge, fostering environments where efficiency coexists with safety and precision.
"The future of robotic arms is not about machines replacing humans, but about teaming up to create a synergy that enhances productivity and safety for all."
By keeping an eye on these developments, stakeholders—be it students, researchers, or industry professionals—can better prepare for what comes next. The implications of these trends stretch far beyond mere gadgetry; they herald a new chapter in how we conceptualize work and collaboration across fields.
Challenges and Limitations
In the exploration of automatic robotic arms, it is crucial to address the challenges and limitations that come with their implementation. These factors not only affect the design and functionality but also impact broader applications in various industries. Acknowledging the hurdles leads to better solutions and innovations. The conversation around these challenges doesn’t merely highlight problems; it reveals opportunities for technological growth.
Technical Limitations
When we discuss technical limitations, one can’t overlook the complexities inherent in robotic systems. One major issue is achieving precise motion control, which is often hindered by discrepancies in sensor data or mechanical inaccuracies. For instance, even slight variations in joint angles can result in considerable deviations from intended paths. This becomes exceptionally vital in high-stakes environments like surgical procedures, where even a millimeter off can have serious consequences.
Moreover, software compatibility can be a thorny point. Various robotic arms rely on distinct programming languages or software systems. This can create no compatibility headaches, especially when integrating new robotic tech into existing setups.
Some examples include:
- Precision Range: Many robotic arms may have a limited range of motion, restricting their use in multifaceted tasks.
- Frame Impacts: The weight of components and materials can limit scalability and portability, making some arms bulky and less efficient.
As technology advances, the need for lighter yet robust materials becomes evident. It's like trying to balance a feather with a sack of potatoes; you want flexibility without compromising strength.
"In robotics, precision is not just a metric; it often defines success or failure in tasks that demand acute accuracy."
Cost-Effectiveness
Associated costs in deploying robotic arms pose significant considerations for companies. The up-front investment can be daunting, particularly for smaller firms. This might lead to an expensive outlay on equipment that may take time to recoup through efficiencies gained.
However, a long-term perspective is essential. When viewed through the lens of increased productivity and reduced labor costs, investing in robotic arms can offer a solid ROI over time. The key factors in determining cost-effectiveness include:
- Maintenance Costs: Regular maintenance can be a hidden drain on finances, necessitating skilled personnel and replacement parts.
- Training Expenses: Employees must be trained to operate and maintain the robotic arms effectively. These training costs can add up and should be factored into any budgeting.
- Energy Consumption: The energy cost to operate robotic arms can also be significant. Efficient energy use and operational downtime must be balanced against these ongoing costs.
Culmination
In wrapping up our exploration of automatic robotic arms, it’s essential to emphasize their significance in the modern technological landscape. These devices, once mere concepts in science fiction, are fundamentally reshaping industries, enhancing productivity, and sparking ethical discussions. The multifaceted design and operational mechanisms we discussed serve as the backbone to their functionality.
Summary of Key Points
Throughout this article, we delved into several critical aspects:
- Historical Development: Robotic arms have evolved from rudimentary machines to sophisticated devices, integrating advanced algorithms and materials science.
- Design Principles: Key components like joints, actuators, and sensors contribute significantly to their accuracy and dexterity.
- Operation Mechanisms: Programming languages such as Python and C++ are vital for the efficient control of these robotic arms.
- AI Integration: The infusion of AI and machine learning enhances precision, allowing these devices to adapt and learn from their environments.
- Ethical Considerations: The displacement of jobs and algorithmic bias raise vital ethical questions as robotic technology continues to advance.
- Future Trends: Developments in soft robotics and collaborative robots promise to further innovate their functionality.
Final Thoughts on the Future of Robotic Arms
The trajectory of robotic arms suggests an even more integrated presence in our daily lives. The future may hold an increased harmony between robots and humans, especially with the rise of collaborative robots or "cobots" that work alongside people. With advancements in soft robotics, we might see more gentle and adaptable systems suitable for intricate tasks in health care or delicate assembly lines.
Each leap in this field carries with it significant implications, not just for industries but for society at large. There is no doubt that as we propel further into the age of automation, the dialogue around ethical use and fairness in accessibility will only intensify. This will test our ability to balance innovation and responsible deployment. As we stand on the brink of an AI-driven future, the potential of automatic robotic arms reflects both excitement and responsibility.