Battery Electrode Manufacturing Process: An Overview
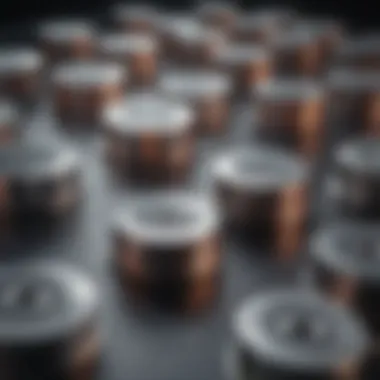
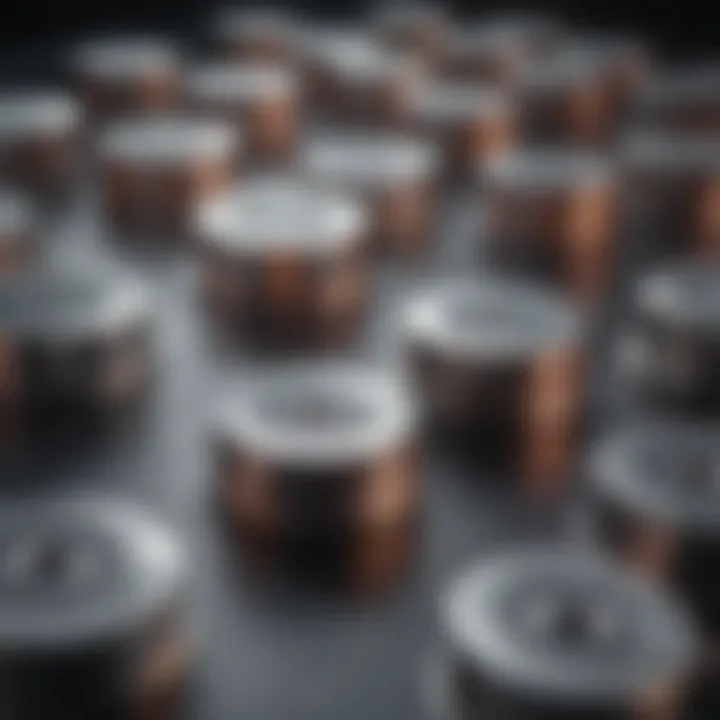
Intro
The manufacturing process of battery electrodes is crucial to the overall function and performance of energy storage systems. These electrodes are pivotal components in both rechargeable and non-rechargeable batteries. Their efficiency directly impacts energy density, charging cycles, and lifespan. Thus, understanding the intricacies of their production can unveil the pathway toward optimized battery technology.
Battery technology is evolving rapidly. As the demand for more efficient and sustainable energy storage solutions increases, innovations in electrode manufacturing have become paramount. This article examines the various stages of battery electrode production. It highlights essential materials, manufacturing techniques, and quality control practices that ensure high-performance outcomes. In doing so, readers will gain insights into the interdependencies of these processes and how improvements can accentuate battery sustainability.
Doing so is not just an academic exercise; it reflects a pressing need in the face of climate change and the transition to renewable energy systems. Whether for electric vehicles or grid storage, the advancements in battery performance hinge significantly on electrode manufacturing methodologies.
Foreword to Battery Electrode Manufacturing
The field of battery electrode manufacturing is crucial for the development of efficient energy storage solutions. With the increasing demand for high-performance batteries, understanding the processes behind their fabrication is essential for various stakeholders, including researchers, educators, and professionals. This section introduces the importance of battery electrode manufacturing and sets the stage for a deeper exploration of the materials, techniques, and innovations involved.
Significance of Battery Electrode Manufacturing
Battery electrodes play a pivotal role in determining overall battery performance, including energy density, power output, and cycle life. The manufacturing of these electrodes directly influences factors like conductivity, capacity, and charge-discharge rates. High-quality electrodes can lead to significant improvements in battery efficiency and sustainability, addressing the growing concerns over environmental impact and resource utilization. Consequently, investment in advanced manufacturing techniques and materials is a major consideration in the battery industry today.
In addition, as the world transitions to renewable energy and electric vehicles, the need for reliable and long-lasting battery systems has become increasingly urgent. Hence, the manufacturing process should evolve to keep pace with technological advancements.
"Quality electrode manufacturing can be a game-changer in enhancing the performance of batteries, aligning with environmental goals."
Overview of Battery Technologies
An understanding of battery technologies is integral to appreciating electrode manufacturing processes. Batteries come in various chemistries, such as lithium-ion, nickel-metal hydride, and solid-state. Each type of battery has unique requirements for its electrodes.
- Lithium-Ion Batteries: Currently dominate the market, particularly in consumer electronics and electric vehicles. They utilize lithium-based materials as the primary components of the electrodes.
- Nickel-Metal Hydride (NiMH): Commonly used in hybrid vehicles and rechargeable batteries. These have different electrode and performance characteristics compared to lithium-ion batteries.
- Solid-State Batteries: Emerging technology that promises increased safety and efficiency. They utilize solid electrolytes and require specialized electrode fabrication methods.
The evolution of these battery technologies shapes the techniques and materials used in electrode manufacturing. As new materials and designs emerge, manufacturers must adapt to remain competitive.
Materials Used in Electrode Manufacturing
Understanding the materials used in the manufacturing of battery electrodes is essential. These materials fundamentally influence the performance, longevity, and cost-effectiveness of batteries. The composition of the electrode determines its electrical, thermal, and mechanical properties. Therefore, selecting suitable materials is a critical component in the manufacturing process.
Adopting advanced materials can enhance battery performance significantly. However, considerations include not just the performance but also the economic factors involved. Prices for materials like lithium, nickel, and cobalt fluctuate, impacting overall production costs. Therefore, manufacturers must continuously assess material choices to ensure economic viability while maintaining quality. This section will explore three main categories of materials: active materials, conductive additives, and binders.
Active Materials: An In-depth Analysis
Active materials are the core components of battery electrodes. They undergo electrochemical reactions that allow the battery to store and release energy. Lithium-ion batteries commonly use materials such as lithium cobalt oxide, lithium iron phosphate, and lithium nickel manganese cobalt oxide. Each material has unique characteristics.
Lithium cobalt oxide, for instance, offers high energy density, making it suitable for portable electronics. However, it poses challenges in terms of thermal stability. Conversely, lithium iron phosphate is robust and stable but generally exhibits lower energy density.
The choice of active material has direct implications on efficiency, cycle life, and safety. It is pertinent for manufacturers to balance between energy capacity and safety concerns. Future innovations may include the exploration of alternative materials like sodium-ion or solid-state options, which promise to revolutionize the landscape of battery technology.
Conductive Additives: Enhancing Performance
Conductive additives play a vital role in enhancing the electrical conductivity of electrode materials. Without these additives, electrodes may suffer from poor performance. Commonly used additives include carbon black and graphite. These materials improve electrical connections between the active particles and the current collector, thereby enhancing overall energy transfer.
Moreover, the use of conductive additives can lower the overall resistance of the electrode. This alteration facilitates better charge and discharge rates, leading to improved battery performance. It is essential, however, to strike a balance; excessive addition may lead to undesirable impacts on other properties, such as mechanical strength. Continuous research aims to improve the efficiency of conductive additives, ensuring they maintain performance without compromising structural integrity, which is crucial for the longevity of batteries.
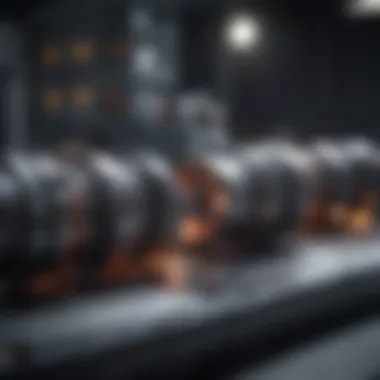
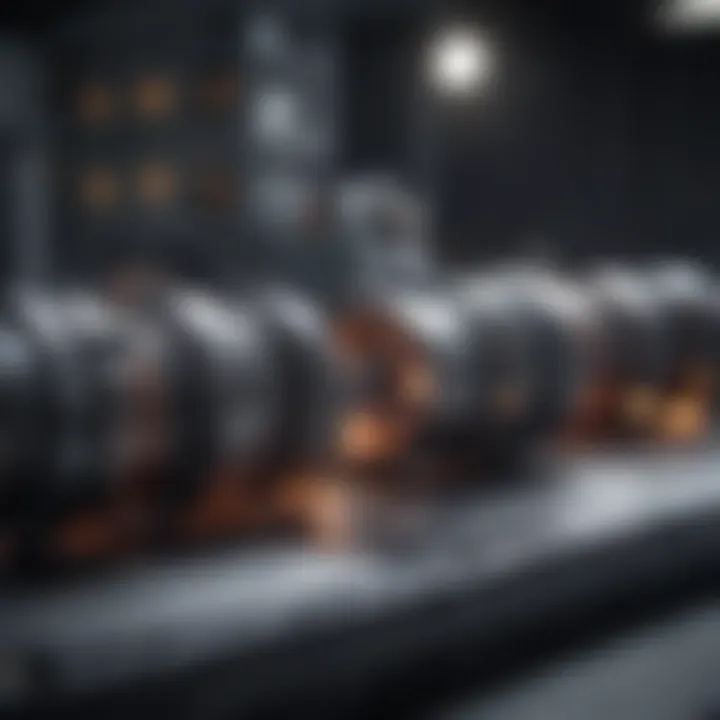
Binders and Their Role in Electrode Integrity
Binders are often overlooked but serve a vital role in maintaining the structural integrity of the electrode. The primary function of a binder is to hold the active materials together and ensure that they adhere to the current collector. Polyvinylidene fluoride (PVDF) is a common binder used in lithium-ion batteries due to its chemical stability and effectiveness. However, the hydrophobic nature of PVDF can impede ionic conductivity.
Alternative binder materials, such as carboxymethyl cellulose, are gaining attention due to their water solubility and environmental friendliness. The binder selected can affect the mechanical properties of the electrode, influencing factors like flexibility and tensile strength. Understanding the interactions between binders and other materials is critical for achieving optimal performance and durability of electrodes.
In summary, the materials used in electrode manufacturing are pivotal to the performance and efficiency of batteries. Every choice made during the selection of active materials, conductive additives, and binders greatly influences the overall integrity and functionality of battery systems.
Manufacturing Techniques
The realm of battery electrode manufacturing hinges on well-defined techniques that dictate the quality and performance of the final product. Understanding these techniques is crucial as they directly influence electrode efficiency, longevity, and overall battery performance. One should find that advancements in manufacturing methods can result in significant improvements not only in charge capacity but also in the sustainability of battery production.
Slurry Preparation and Its Impact
Slurry preparation is a fundamental step in electrode manufacturing. It involves mixing active materials, conductive additives, and binders with a solvent to create a homogenous slurry. The properties of this slurry are critical because they affect the uniformity of the electrode coating applied onto current collectors.
Factors influencing slurry preparation include:
- Viscosity: Affects the coating process.
- Particle size distribution: Ensures uniform distribution of active materials.
- Solid content: Influences coating thickness.
Improper slurry preparation could lead to inconsistencies, reducing the performance of the electrodes. The careful balance of these elements ensures optimal electrode performance and contributes to the reliability of energy storage systems.
Coating Processes: Methods and Innovations
Coating processes are vital in transferring the slurry to the electrode substrate. There are several methods in use today, such as slot-die coating, doctor blade coating, and gravure coating. Each method has its advantages and considerations.
- Slot-die coating: Provides uniform coating with high accuracy.
- Doctor blade coating: It is cost-effective for large-scale production but might lead to variations in thickness.
- Gravure coating: Excellent for high-speed production and precise control of thickness.
Recent innovations focus on increasing coating efficiency while reducing waste. Methods like electrostatic coating and spray coating are evolving to enhance film quality and minimize defects.
Drying Techniques: Vacuum vs Conventional
The drying stage is essential after coating, as it removes the solvent from the slurry. Two primary methods are often discussed: vacuum drying and conventional drying.
- Vacuum drying offers advantages such as:*
- Rapid solvent removal
- Lower energy consumption
- Enhanced electrochemical performance
In contrast, conventional drying utilizes:
- Hot air or infrared radiation
- Simplicity in setup
- Often presents longer drying times
While conventional methods are widely used, vacuum drying is becoming more prevalent due to its efficiency, which directly affects the integrity of the electrodes.
Calendering: Enhancing Electrode Density
Calendering is a process applied after drying, where electrodes are passed through rollers to achieve desired thickness and density. This step is crucial as it improves the electrode’s mechanical properties and compaction.
Benefits of calendering include:
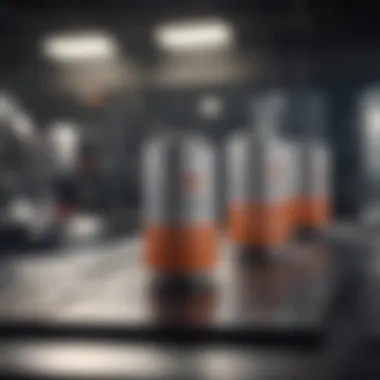
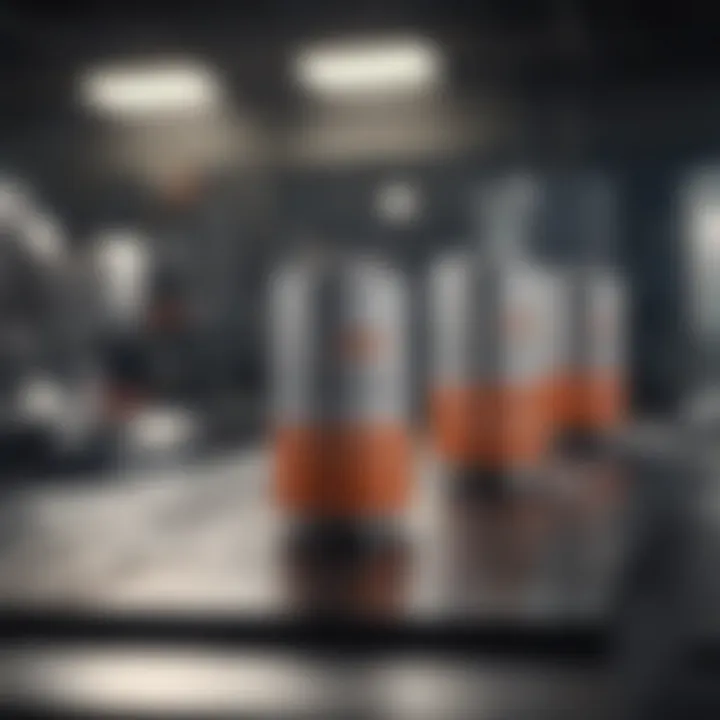
- Increased density: Enhances energy density of the electrode.
- Uniformity: Reduces variations in the thickness of the electrode
- Mechanical stability: Improves the overall stability during charge and discharge cycles
Calendering is not merely a finishing touch; it significantly influences the electrochemical performance of the electrodes and, by extension, the battery as a whole.
Cutting and Packaging Considerations
After the manufacturing process, cutting and packaging are final but critical phases that determine how electrodes will be integrated into battery systems. Precision in cutting ensures that each cell's specifications are met, preventing complications during assembly.
Important considerations include:
- Cutting techniques: Precision is key, with methods like laser cutting gaining popularity for their accuracy.
- Packaging materials: Should provide protection against environmental factors while maintaining electrical connections.
Packaging affects not only the electrodes' performance but also their room for innovation during design and application.
"The choice of manufacturing techniques is pivotal in determining the trajectory of advancements within battery technology. It sets the stage for performance and sustainability."
Quality Control in Electrode Manufacturing
Quality control in electrode manufacturing is a critical aspect that ensures both the performance and safety of battery systems. The significance of maintaining high quality throughout the manufacturing process cannot be overstated. Flaws or inconsistencies in battery electrodes can lead to reduced efficiency, safety hazards, and overall failure of energy storage solutions. This section elaborates on the key components, benefits, and considerations regarding quality control that are essential for producing reliable and effective battery electrodes.
Quality control encompasses various steps, from raw materials selection to final product testing. This process not only helps in identifying defects early on but also ensures that all products meet regulatory requirements. An effective quality control system can greatly enhance the manufacturing process's efficiency while simultaneously reducing costs associated with product recalls or failures.
Testing Methodologies: Ensuring Compliance
Testing methodologies in battery electrode manufacturing serve as the foundation for ensuring compliance with industry standards. These methodologies are designed to assess the various characteristics of electrodes, including physical, chemical, and electrochemical properties. Some common testing methods include:
- X-ray diffraction (XRD) to analyze the crystalline structure of active materials.
- Scanning electron microscopy (SEM) for surface morphology assessment.
- Fourier-transform infrared spectroscopy (FTIR) for functional group analysis.
Moreover, electrochemical testing is vital for assessing the performance of battery electrodes. Techniques such as cyclic voltammetry and galvanostatic charge/discharge testing are employed to measure charge storage capacity and cycle life.
Implementing these testing methodologies ensures that the electrodes meet specific performance criteria and safety standards, such as those set by environmental and industry regulations. This step also allows manufacturers to trace back any inconsistencies to their source, facilitating improvements in the manufacturing process.
Monitoring and Process Control Techniques
Monitoring and process control techniques are essential for maintaining quality throughout the production of battery electrodes. These techniques involve the continuous observation and adjustment of manufacturing parameters to ensure optimal conditions. Some of the key elements include:
- Real-time monitoring of slurry viscosity to ensure uniformity in electrode coating.
- Temperature control during drying to avoid defects such as cracking or uneven surfaces.
- Automated systems for calendering that ensure consistent electrode density and thickness.
Using advanced technologies, such as Industry 4.0 solutions, can significantly enhance the quality control process. Employing sensors and data analytics allows manufacturers to gather insights into production patterns and identify any deviations in real time. This proactive approach aids in maintaining high quality, minimizing waste, and improving overall efficiency.
Environmental and Economic Considerations
In recent years, the focus on environmental and economic considerations in battery electrode manufacturing has intensified, driven by the growing demand for sustainable energy solutions. This section highlights the critical elements that influence both the ecological impact and economic viability of producing battery electrodes.
The ecological footprint of battery production includes resource extraction, energy consumption, and waste generation. As companies strive to align with environmental regulations, understanding the impact of battery manufacturing on the environment is crucial. Sustainable practices can lead to significant benefits such as minimizing waste, reducing greenhouse gas emissions, and conserving resources. Adopting recycling and reuse methods not only promotes sustainability but also finds applications in the circular economy, where materials are kept in use for as long as possible.
Moreover, the economic considerations surrounding battery manufacturing are equally imperative. Investments in sustainable technology may require initial capital expenditures but can result in lower operational costs over time through energy savings and material efficiency. It is essential for manufacturers to analyze the cost-effectiveness of their processes, weighing potential savings against the upfront costs of implementing sustainable practices. This analysis allows companies to balance quality and economy effectively, ensuring their products remain competitive in a growing market.
"Sustainability and cost-efficiency must coexist for the future of battery production."
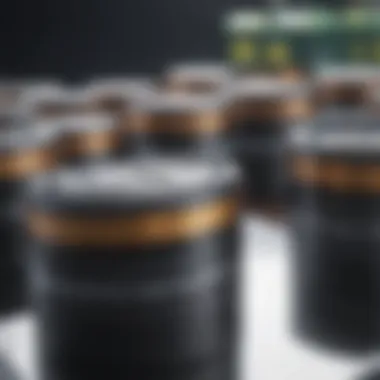
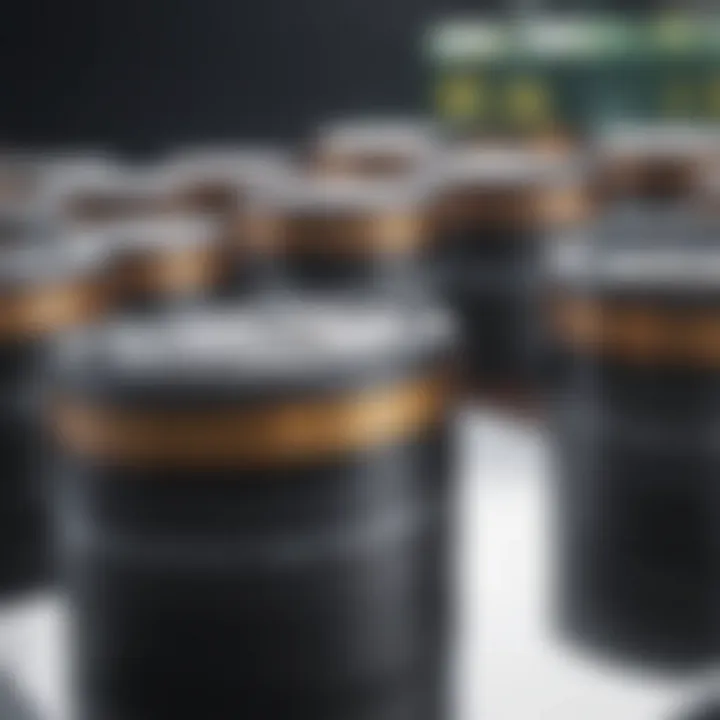
The interplay between environmental responsibility and economic performance establishes a framework where advancements in one area can lead to improvements in the other. For example, innovations in materials can enhance electrode performance while also minimizing environmental harm, thus contributing to a healthier planet and a more viable economic model.
Sustainability in Battery Electrode Production
Sustainability in battery electrode production involves responsible sourcing of materials, energy-efficient manufacturing processes, and effective waste management systems. The use of renewable materials is becoming increasingly important in this sector. For instance, researchers are exploring alternative active materials that minimize reliance on rare earth elements like cobalt, which have complex mining impacts on ecosystems.
Additionally, energy-efficient manufacturing can significantly reduce the carbon footprint of battery production. Techniques such as using solar or wind energy for manufacturing operations contribute positively to environmental sustainability. Companies must also invest in comprehensive waste management strategies to handle by-products and end-of-life products effectively, adopting practices that align with global sustainability goals.
To enhance sustainability further, manufacturers can engage in lifecycle assessments to evaluate the total environmental impact of battery electrodes from raw material extraction to disposal. Engaging with stakeholders can drive collaborative approaches to reduce the industry's overall environmental burden.
Cost Analysis: Balancing Quality and Economy
Cost analysis in battery electrode manufacturing requires an in-depth evaluation of material costs, production techniques, and market demand. Manufacturers face the challenge of maintaining high-quality standards while also cutting costs to remain competitive. A thorough understanding of cost drivers can assist producers in making informed decisions about where investments will yield the most significant benefits.
Investing in high-quality materials, such as advanced conductive additives and efficient binders, can enhance battery performance. However, these materials often come at a premium price. Therefore, companies must evaluate the trade-offs between short-term costs and long-term performance benefits. Sometimes, lower-quality materials may reduce initial production costs but could lead to higher failure rates and warranty claims in the long run.
In the context of continuously evolving technology, the cost of automation also plays a vital role. Automation technologies can improve production efficiency and reduce labor costs, but the initial investment can be daunting. Firms must balance investing in automation with their current market position and potential growth opportunities. Ultimately, achieving this balance can enhance profitability while ensuring that the produced battery electrodes meet or exceed customer expectations.
Recent Innovations and Future Trends
Recent innovations in battery electrode manufacturing are pivotal for propelling the performance of energy storage systems. As the demand for energy-efficient solutions intensifies, these advancements are reshaping how electrodes are designed, produced, and integrated into battery systems. Understanding these trends is essential for students, researchers, educators, and professionals aiming to stay at the forefront of battery technology.
Advanced Materials for Enhanced Performance
Recent research has shifted to advanced materials to enhance battery performance significantly. Lithium iron phosphate, silicon-based anodes, and cobalt-free chemistries are key examples of these materials. Each offers unique advantages, such as improved energy density or reduced environmental impact.
- Lithium Iron Phosphate: Offers excellent thermal stability and safety, making it a preferred choice for electric vehicles and stationary storage.
- Silicon-Based Anodes: Provide higher capacity compared to traditional graphite, potentially tripling the energy storage capability. However, they face challenges related to expansion and durability.
- Cobalt-Free Chemistries: Lower the reliance on cobalt, addressing ethical sourcing issues and indicating a shift towards sustainability in battery manufacturing.
Integrating these novel materials can lead to higher battery lifespans and efficiencies, which are vital for competing in the evolving market.
Automation and Industry 4. in Manufacturing
The ongoing integration of Industry 4.0 principles in battery electrode manufacturing is revolutionizing the sector. Automation not only enhances operational efficiency but also improves product quality and consistency.
Key elements of this trend include:
- Robotic Process Automation (RPA): Streamlining repetitive tasks and reducing human error.
- Data Analytics: Facilitating real-time process monitoring, allowing manufacturers to adjust parameters instantaneously and optimize outcomes.
- IoT Technologies: Enabling connected devices to gather data across the production line, assisting in predictive maintenance and improving overall line efficiency.
"Automation and real-time data analytics will shape the future of battery manufacturing, addressing challenges of scalability and sustainability head-on."
As the industry moves forward, melding automation with advanced materials will be crucial. This will not only meet the rising energy demands but will also drive down costs and environmental impact associated with battery production.
In summary, the innovations highlighted here signify a clear direction towards more efficient, sustainable, and high-performance battery electrode manufacturing. Keeping abreast of these trends is essential for stakeholders aiming for relevancy in a fast-evolving energy sector.
Culmination: The Path Forward in Battery Electrode Manufacturing
In today's rapidly evolving energy landscape, the battery electrode manufacturing process stands as a pivotal component in the development of efficient and sustainable energy storage systems. This conclusion synthesizes important elements discussed in previous sections, emphasizing their collective impact on the future of battery technology.
One significant aspect is the increasing importance of materials used in electrode production. Advanced materials such as silicon-based anodes and high-capacity cathodes are becoming more prevalent. Their integration not only enhances performance but also supports sustainability goals by encouraging the use of abundant resources. Moreover, ongoing research in nanomaterials is pushing the boundaries of energy density, adaptability, and cycle life in batteries.
Additionally, innovations in manufacturing techniques, like automated slurry preparation and improved coating processes, are instrumental in enhancing production efficiency. Automation is streamlining operations, reducing waste, and ensuring consistent quality. These advancements contribute to lowering manufacturing costs, thereby making electric vehicles and renewable energy storage technologies more accessible to the general public.
Quality control has also emerged as a key focus area, ensuring that batteries meet stringent safety and performance standards. As production scales up, adopting robust monitoring and testing methodologies will be crucial. This ongoing commitment to quality assurance will build trust in battery technologies, which is essential for widespread adoption.
The environmental implications of battery electrode manufacturing cannot be overstated. Striking a balance between industrial growth and sustainable practices is critical. Companies are increasingly being held accountable for their environmental footprint. This drives innovation not just in materials and processes, but also in end-of-life considerations, such as recycling and repurposing battery components.