Boosting 3D Print Strength: Key Techniques
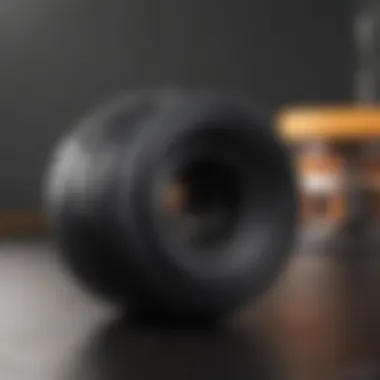
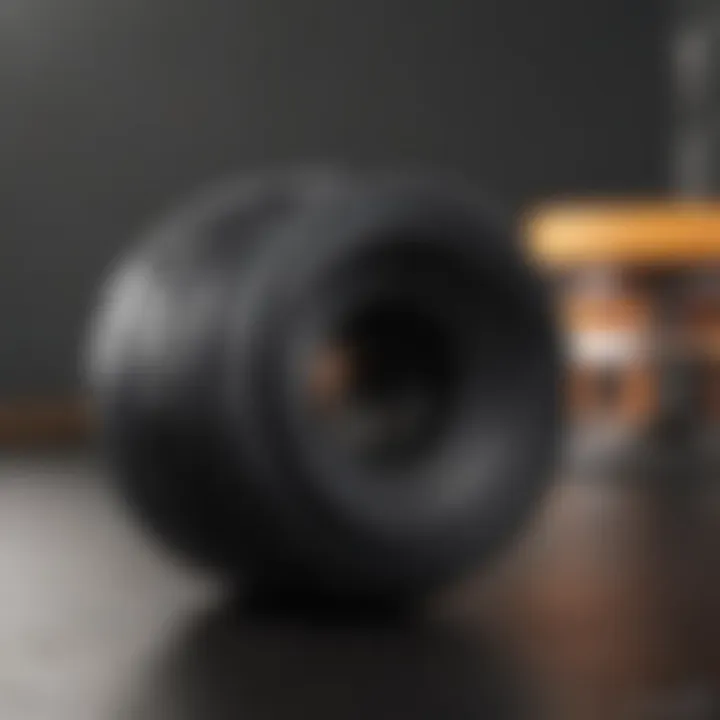
Intro
In the ever-evolving landscape of manufacturing, 3D printing has emerged as a cornerstone technology, redefining how objects are made. Its allure lies not just in the speed of production, but in the sheer creativity it enables. However, there's a catch—durability challenges can rear their ugly heads, particularly in functional applications where strength is paramount. Reliable 3D printed parts don’t just emerge; they require careful consideration and strategy to ensure they withstand the test of time.
This article dives deep into the nitty-gritty of enhancing durability in 3D printing, addressing essential factors that influence the longevity and reliability of printed items. We will traverse through material selection, design intricacies, print settings, and post-processing methods—all potent tools in the arsenal of anyone aiming to amplify their prints' resilience. Through a blend of scientific principles and practical know-how, each point presented here aims to arm both veterans and newcomers in the field with actionable insights.
Research Overview
Summary of Key Findings
Recent studies reveal a multitude of strategies that can be employed to bolster the durability of 3D printed objects. From exploring innovative materials like carbon fiber-infused filaments to tweaking print settings such as layer height and infill density, improvements can be made at various stages of the 3D printing process. Key takeaways include:
- Material Selection: Choosing the right filament is critical; materials such as PETG or Nylon often outperform standard PLA in terms of durability.
- Design Considerations: Architecture matters. Adding ribs or modifying wall thickness can greatly enhance strength.
- Print Settings: Parameters like extrusion temperature and speed play significant roles in the final product's durability.
- Post Processing: Techniques such as annealing or coating can provide an extra layer of protection.
Importance of the Research
Understanding the durability of 3D printed objects is not merely academic—it's a pressing need for those who rely on these technologies in sectors ranging from aerospace to healthcare. The stakes are particularly high when the failure of a printed part can lead to significant safety risks or economic losses. Thus, enhancing durability isn't just a nice-to-have; it's a must.
By synthesizing these findings, users can navigate the intricate world of 3D printing with informed confidence, ensuring that their creations are not just innovative, but also robust enough for everyday use.
Understanding the Importance of Strength in 3D Printing
The demand for durable components in various applications has skyrocketed in recent years, making strength a crucial factor in 3D printing. The integrity of a printed object determines its performance, longevity, and suitability for specific purposes. For 3D printed items that serve functional roles, strength is not just a feature; it's a necessity. This section dives into why understanding strength is pivotal for anyone operating within the realm of 3D printing.
The Role of Strength in Functional Parts
In practical terms, the strength of a functional part can dictate how well it withstands stress, load, and environmental factors. Take, for instance, automotive components - a gear or bracket that fails under load can spell disaster, leading to safety concerns and financial losses. The design and materials must align perfectly to ensure that such parts not only fulfill their intended function but do so reliably.
Key factors include:
- Material Composition: Different materials offer varying levels of tensile and compressive strength. Knowledge of these properties is essential.
- Geometric Design: The shape and configuration of parts affect how forces are distributed. Efficient designs can considerably enhance strength.
- Post-Processing: Techniques such as annealing or coating can improve durability.
Ultimately, the robustness of functional parts plays a pivotal role in their performance, emphasizing the need for careful consideration and optimization during the design and manufacturing stages.
Common Applications Requiring Enhanced Strength
Certain sectors have notably high demands for enhanced strength in 3D printed components. Examples include:
- Aerospace: With components facing immense pressures and varying temperatures, strength is essential for safety and reliability.
- Medical Devices: Implants and prosthetics require not only precision but also the ability to withstand stresses within the human body.
- Architecture: Structural models and components must support significant loads while maintaining aesthetic appeal.
"In every field where 3D printing finds its application, the strength of printed objects stands at the forefront, shaping the future of innovation and safety."
Materials Selection for Stronger Prints
When it comes to constructing 3D printed objects, the materials you choose can make all the difference. Material selection holds a crucial role in ensuring that the final product not only meets its intended purpose but also can withstand the rigors of use. What constitutes a robust structure? Typically, it boils down to a combination of factors, including the intrinsic properties of the material, its compatibility with the design, and how well it aligns with the user’s specific needs. The right material choice can enhance strength, increase durability, and provide functionality that may seem like a stretch at first.
Overview of Popular 3D Printing Materials
3D printing has seen a plethora of materials coming to the forefront for different applications. Here are some commonly utilized materials and what makes them tick:
- PLA (Polylactic Acid): A favorite among beginners, PLA is derived from renewable resources like corn starch. It’s easy to print with and provides decent detail. However, it's not the best for functional parts due to its brittleness.
- ABS (Acrylonitrile Butadiene Styrene): Known for its toughness, ABS is widely used in industrial applications. It can withstand higher temperatures than PLA, making it more suitable for functional prototypes.
- PETG (Polyethylene Terephthalate Glycol): This material strikes a balance between PLA and ABS, offering durability with less odor during printing. It is also resistant to moisture, which increases its application scope.
- Nylon: Well-regarded for its flexibility and resilience, Nylon is ideal for mechanical parts but can be challenging to print due to its warping tendency.
- TPU (Thermoplastic Polyurethane): This is a flexible material that is perfect for making rubber-like parts, providing excellent durability.
Choosing among these materials largely depends on the specific project requirements, environmental factors, and mechanical properties desired.
Impact of Material Properties on Strength
Material properties fundamentally shape the strength and durability of the finished print. These elements work hand in hand with how the material performs under various conditions. Below are some key properties to consider:
Density and Composition
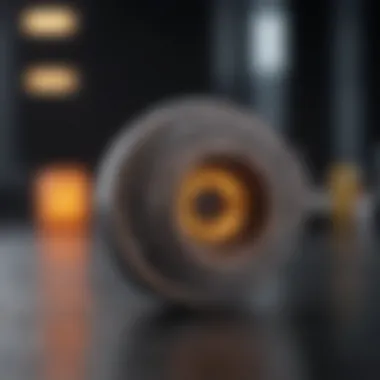
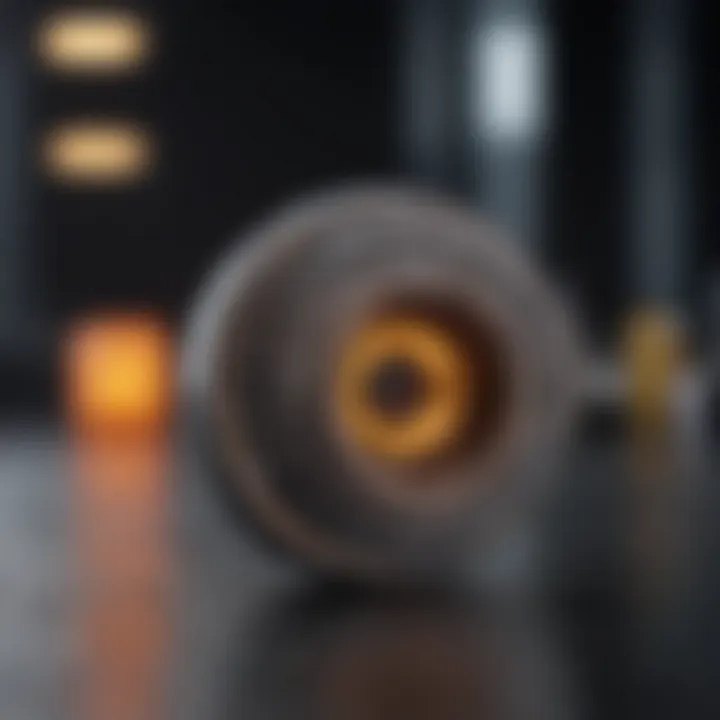
Density and composition of a material influence its load-bearing capacity. Higher density materials often correlate with increased strength but at the cost of weight. For instance, a material like Nylon has a higher density which allows for better tensile strength. On the flip side, using materials with lower density, such as PLA, may lead to lighter prints but compromises strength.
In applications like automotive parts, where weight matters but strength cannot be compromised, selecting a denser material can be advantageous.
Thermal Resistance
Thermal resistance might not be the first property that comes to mind when talking about strength, but it plays a key role. Materials with high thermal resistance are critical for parts exposed to heat, ensuring they maintain structural integrity under elevated temperatures. ABS, for example, has great thermal stability, allowing it to retain its form even in environments where heat can warp lesser materials.
However, the downside is that some of these heat-resistant materials can be harder to print with, which can complicate the production process.
Flexural and Tensile Strength
Flexural strength refers to a material’s ability to withstand bending, while tensile strength relates to how well it can endure being pulled apart. These two characteristics are crucial, especially in applications where parts experience both bending and tension. For example, a component used in robotics might need to flex but still maintain rigidity under load.
Materials like PETG strike a good balance between both flexural and tensile strengths, making them robust options for a range of applications. However, achieving a higher tensile strength often requires dealing with more complex printing conditions and possibly post-processing methods.
In summary: Material selection should not be approached lightly. A strategic choice based on understanding the specific requirements of the end-use can greatly enhance the efficacy and life of 3D printed parts.
Ultimately, the essence of creating more durable, functional 3D prints lies within thoughtful consideration of not just material types but their intrinsic properties as well.
Design Principles for Stronger 3D Models
The realm of 3D printing is not just about loading a file and hitting print. The very foundation of a resilient print lies in thoughtful design principles. Understanding how these principles function can lead to more robust and reliable models that serve their intended purpose efficiently. For designers and engineers, the choices made in the modeling phase can spell the difference between a mere prototype and a functional, durable part.
Key design principles encompass a variety of geometric and structural considerations. These include, but are not limited to, weight distribution, ribbing, and the incorporation of unique structural features. Each of these elements plays a vital role in enhancing the overall strength and longevity of a printed object. Ultimately, smart design choices can significantly reduce the likelihood of failure during use, ensuring that the final output meets or exceeds expectations.
Geometric Considerations in Design
Weight Distribution
When crafting a model, weight distribution is a crucial aspect to keep in mind. Properly segmenting the mass of a print can greatly affect how it behaves under stress. Ideally, a well-distributed design reduces the risk of breakage by allowing for even stress absorption during use. This means that when forces are applied to a component, they aren't concentrated in a particular area, which might otherwise lead to cracks or complete failure.
One of the main characteristics of effective weight distribution is evenness. A design that includes thick and thin sections can create weaknesses at junction points. By distributing weight equally, the likelihood of stress points forming diminishes. However, an important note here is that weight distribution can also add complexity to a design. It challenges the designer to think spatially and understand how changes affect the entire model.
Ribbing and Reinforcements
Ribbing and reinforcements serve as intrinsic support to a print's structure. By adding ribs or braces in key areas, you can bolster specific sections of a part that might be prone to flexing or bending. The primary characteristic of ribbing is its functionality—it not only increases strength but can also maintain the overall weight of the object.
Implementing this design feature is advantageous because it enhances the load-bearing capacity without adding significant mass. However, an increased amount of ribbing can, at times, complicate the printing process due to additional material requirements and potential issues with layer adhesion. Thus, it's essential to find a balance when using these reinforcements; too little may not suffice, while too much may hinder other aspects of printing.
Incorporating Structural Features
Curvature vs. Flat Surfaces
In 3D modeling, the debate of curvature versus flat surfaces ends up being critical in strength optimization. Curved surfaces can distribute stress more naturally compared to flat ones. When forces apply, a curved shape tends to redirect them, minimizing potential points of failure. Flat surfaces, though easier to model, can concentrate stress, especially in corners and junctions.
Curved designs are often a popular choice for models requiring strength. However, they may pose challenges in printing, especially regarding the initial layers, which may struggle to adhere. This means that while curvature can enhance durability, designers must also consider the capabilities and settings of their printers.
Undercuts and Overhangs
The use of undercuts and overhangs can significantly impact the strength of a design. While these features allow for more complex shapes, they can also introduce vulnerabilities. Overhangs, for instance, might suffer sagging if the print settings aren't optimized for the material being used. Such settings might entail adjusting the cooling rate, extrusion parameters, and support structures.
An intriguing characteristic of undetected elements is their aesthetic and functional potential. However, if not managed properly, they may lead to weaknesses in the final part. That being said, successful incorporation of these features often requires a balance of creativity and engineering knowledge, to forge designs that are not only visually appealing but also rugged.
Understanding and applying these design principles can revolutionize the way 3D printing is approached. By intentionally considering the geometry and structure of a model, designers can create strong, reliable prints that withstand the test of time and use.
Optimizing Print Settings for Durability
When it comes to producing durable 3D prints, optimizing the settings during the printing process plays an essential role. The right print configurations can significantly affect the strength and longevity of the final product, making this aspect critical for users who depend on the functional application of their prints. Parameters like layer height, print speed, infill density, patterns, and temperature need careful consideration to ensure the highest level of durability. By understanding the nuances of these settings, all kinds of practitioners can optimize their operations and create items that stand the test of time.
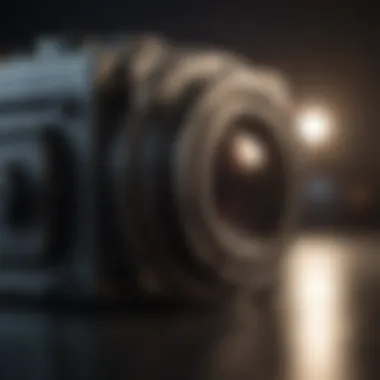
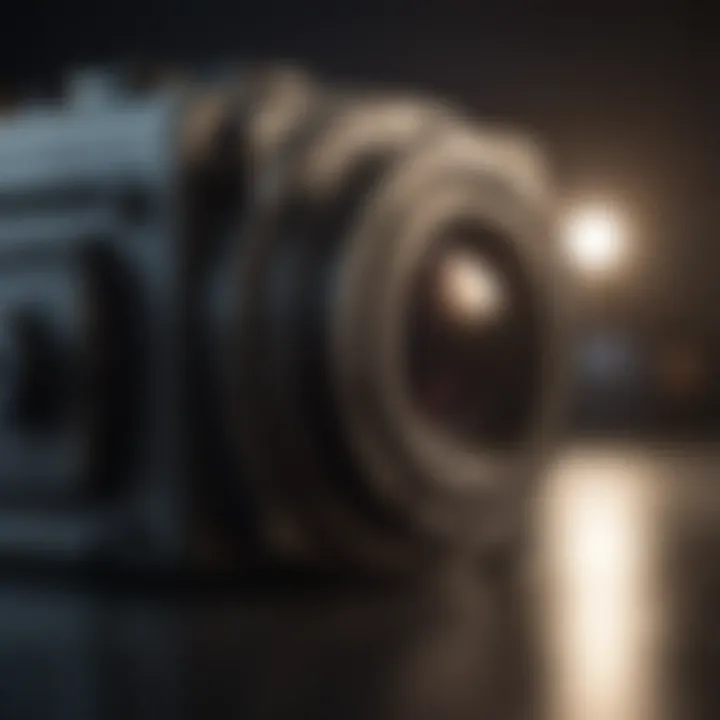
Layer Height and Print Speed
Layer height is a fundamental setting influencing structural integrity. A smaller layer height typically yields finer details, but it also adds time to the printing process. On the contrary, larger layer heights can expedite production but may sacrifice some strength. This balance can be trickier than choosing a brand of coffee; you want that delectable latte art, but also to get out the door on time. Generally, adjusting the layer height to somewhere in the middle often serves well, as it combines reasonable strength with decent print speed.
Print speed, on the other hand, is no less important. A slower printer speed allows for better adhesion between layers, reducing the risk of structural weaknesses. Conversely, moving too quickly can create gaps or uneven layering which diminishes the potential durability. It’s akin to trying to write neatly while rushing: a lot can go wrong in the process.
Infill Density and Patterns
Infill density and its patterns have profound effects on durability.
Standard vs. Custom Infill
When discussing standard versus custom infill, it’s essential to recognize that both options serve different needs. Standard infill structures—like grid or honeycomb—are often user-friendly and provide a good balance of support and material usage. However, custom infill can tailor strength right to the user's specification. Think of it like being able to price-tag your favorite pizza: you choose every topping according to your flavor.
Standard infill is usually preferred for ease of use. It’s quick to set up and doesn’t require elaborate adjustments, making it a popular choice for those who may not wish to dive deep into settings. Custom infill, while requiring a bit of trial and error, offers increased flexibility. However, the downside? It can be more time-consuming and sometimes results in over-complicated settings, which could confuse the average user.
Choosing the Right Pattern
Choosing the right infill pattern is another vital factor in enhancing strength. Each type of pattern, whether it be triangular or concentric, has unique attributes that contribute to load distribution and overall resilience. A pattern like the cubic infill, for instance, is enviable for achieving a good balance of weight and structural integrity—like a well-crafted bridge.
The key characteristic of choosing the right pattern is understanding the specific requirements of the part you are printing. For instance, if you are creating a functional component that is expected to endure stress, a denser pattern might be advisable. This choice can complicate the print process, yet the result is often appreciated for its robustness.
Temperature Control During Printing
Temperature control during printing is another crucial aspect that should not be overlooked. The extrusion and platform temperature can significantly influence the overall durability of the final product.
Extrusion Temperature
Extrusion temperature has a direct impact on adhesion between layers. If the temperature is too low, the filament may not meld properly, resulting in a weak bond; too high, and risks include warping or stringing—neither of which is desirable for a strong product. Ideal temperature settings often depend on the specific filament type being used; for example, PLA generally requires less heat than ABS.
Finding the sweet spot for extrusion temperature is critical—it can make or break the print’s durability. Fine-tuning this aspect aids in achieving a homogenous structure crucial for load-bearing.
Platform Temperature
Platform temperature serves a similar function but in a different context. A heated bed helps in maintaining adhesion while preventing warping in the print itself. The platform temperature creates an initial stability that forms the foundation of a print, actively reducing the chance of failures due to shrinking or lifting at corners. Opting for the right temperature ensures that prints not only complete successfully but are also resilient once finished.
In summary, optimizing print settings for durability involves a careful melding of various factors, ensuring that both layer height and speed, as well as infill and temperature settings, are all aligned to produce that reliably strong print. By addressing these considerations thoroughly, users can push the boundaries of what their 3D printing endeavors can achieve.
Post-Processing Techniques to Enhance Strength
In the quest for robust 3D printed objects, post-processing techniques emerge as vital allies. These methods, while perhaps tedious, open avenues to significantly bolster the durability of printed items. They can bridge the gap between a print that's just good and one that's seriously usable in demanding conditions. It’s crucial to examine how various post-processing techniques can alter the printed item’s physical properties, fostering stronger, more reliable outputs.
Heat Treatment Methods
Heat treatment stands out as a prominent method used to enhance the strength of 3D prints. This process involves heating the printed component to a specific temperature and then allowing it to cool at a controlled rate. Often employed in metals and some polymers, heat treatment can greatly improve the mechanical properties of the material.
One pivotal point is that heat treatment can relieve internal stresses that occur during the printing process. When materials cool, they often contract, leading to warping or internal tension, which weakens the part overall. By applying heat, the material’s molecular structure can be rearranged and stabilized, enhancing both toughness and strength.
Chemical Strengthening Techniques
Epoxy Coatings
Epoxy coatings serve as a powerful ally in strengthening 3D prints. Their key characteristic lies in their adhesive properties and ability to form a rigid, stable layer over the printed object. Using epoxy adds a protective barrier that not only enhances the surface finish but also offers increased impact resistance, making it ideal for functional parts subjected to stress.
A unique feature of epoxy coatings is their versatility; they can adapt to a variety of prints, regardless of size or shape. Despite their numerous advantages, there are some considerations. Allowing time for proper curing is essential; rushing this process can result in compromised strength. Additionally, it may increase the weight of the print, a factor to consider depending on the application.
Vapor Smoothing
Vapor smoothing is another technique garnering attention for its role in enhancing 3D print strength. This method uses a solvent vapor to slightly melt the outer layer of the printed part, effectively smoothing out the surface. This not only improves aesthetics but can also enhance strength by eliminating microscopic flaws that might exist on the surface.
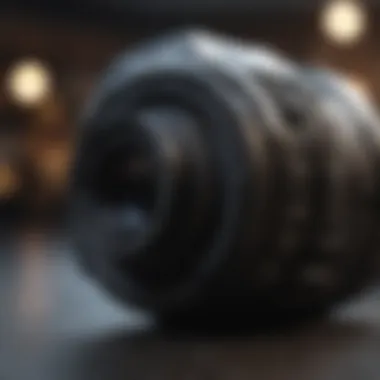
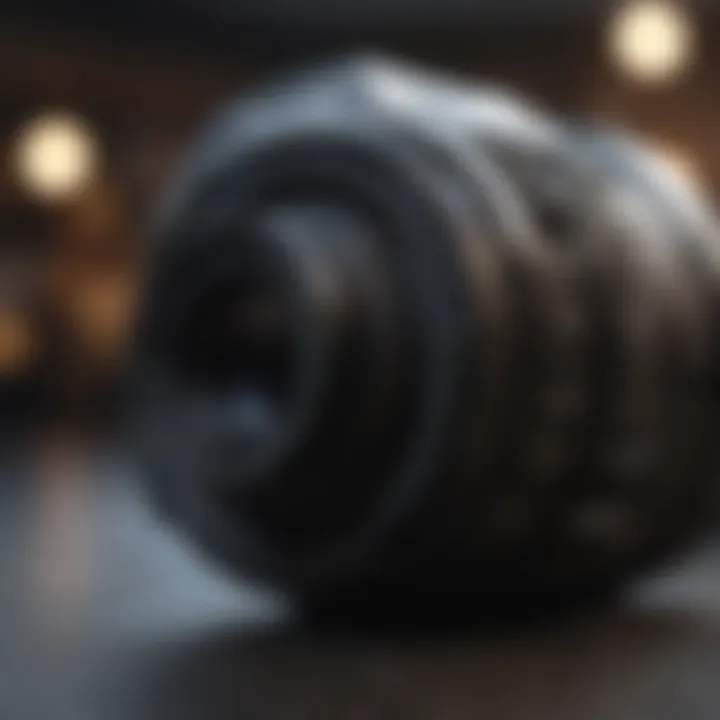
Key to vapor smoothing is its gentle approach; unlike mechanical sanding, it doesn’t remove material but rather smooths out imperfections. One notable advantage is that it can improve layer adhesion by fusing the layers together more effectively. Nevertheless, caution is needed with this technique. Overexposure might lead to warping or undesirable changes in dimensions, which could negate some of its benefits.
Mechanical Reinforcements
Screws and Fasteners
Mechanical reinforcements like screws and fasteners effectively address structural integrity issues in 3D printed parts. They provide an easy method of joining different components while improving the overall strength of the assembly. The primary characteristic of screws is their simplicity and ease of use—adding these fasteners can transform a print from a single piece into a much sturdier unit.
Screws offer unique features like adjustable tightness, allowing users to fine-tune the assembly's integrity based on load requirements. However, it’s worth noting that the practicality of using screws importantly hinges on the design of the part itself. If not designed with reinforcements in mind, the part might still be vulnerable to failure.
Joining Techniques
Joining techniques encapsulate a variety of methods to unify multiple 3D printed parts into one integral component. Techniques such as adhesive bonding or mechanical interlocking can provide significant benefits. A key feature of these methods is their ability to overcome some of the limitations of 3D printing, where certain geometries might lack inherent strength.
The benefit of employing joining techniques lies in the flexibility they offer—multiple parts can be combined to create an object that meets specific performance criteria or dimensional constraints. However, attention must be paid to ensure that the interfaces between joined parts are properly designed and executed. Poor joins can become weak points, ultimately leading to failure under load.
"Choosing the right post-processing technique can mean the difference between a fragile object and a dependable functional part. The method involves understanding your material, the intended use, and making clever adjustments to improve the printed outcome."
The Role of Experimentation in Developing Stronger Prints
In the journey of 3D printing, experimentation stands out as a linchpin in achieving stronger, more durable prints. It’s not just what you start with – the materials and the design – but also how you test and tweak those variables that can lead to breakthroughs in efficacy and strength. A methodical approach to experimentation enables practitioners to harness the full potential of their 3D printing capabilities. This focus can lead to considerable benefits, not only in the quality of the finished products but also in understanding the interplay between design and material properties.
Conducting Material Tests
When it comes to producing robust parts, the choice of material is absolutely crucial. Conducting material tests allows for a hands-on evaluation of various compositions, blends, or treatments that can enhance the strength of a print. For instance, materials like PLA might seem versatile initially, but they might not withstand high temperatures compared to ASA or polycarbonate, which boast better thermal resistance. Testing should involve:
- Tensile Testing: This assesses how materials respond under stretching forces; essential for applications where tension is a key concern.
- Impact Resistance Tests: Measures how well a material can absorb energy and resist breaking upon impact.
- Thermal Stability: Understands how materials perform when exposed to extreme heats – vital for functional parts that might be used in demanding environments.
Making use of both seasoned testing tools and simple DIY setups can yield significant insights. Even something as straightforward as bending an extruded sample can reveal weak points that might hinder a part's overall durability.
"Experimentation is the mother of innovation. Without testing, we remain in the dark regarding the true capabilities of our materials and designs."
Iterative Design and Prototyping
Once material tests illuminate the strengths and weaknesses of your selections, iterative design becomes the next logical step. This phase involves creating prototypes, analyzing how they hold up in real-world applications, and refining the designs based on observed results. The cycle of designing, printing, and testing should not be seen merely as a chore but as the heart of the optimization process. Here are some key facets of this approach:
- Feedback Integration: Every prototype brings with it a wealth of insights. By documenting failures and successes alike, designers can pinpoint what works and what doesn’t, turning every setback into a setup for future success.
- Adjusting Design Features: Sometimes, tweaking a parameter like wall thickness or adding ribs can dramatically change the strength profile of a print. For instance, refining infill patterns based on prototype performance may yield stronger yet lighter final products.
- Rapid Prototyping Techniques: Embracing techniques such as SLA or DLP can expedite the testing phase, letting creators quickly iterate on their designs without an extensive wait for materials to cure or harden.
Future Directions in Strength Optimization for 3D Printing
As the realm of 3D printing continues to rapidly evolve, exploring the future directions of strength optimization is imperative. This area holds a significant weight, not merely as a theoretical endeavor but as a practical necessity for those who depend on 3D-printed objects in demanding applications. The advancements in this field promise not just improvements in material properties but also introduce smart technologies that can revolutionize how we approach 3D printing.
The benefits of delving into these future strategies are manifold. Not only can they lead to enhanced durability and functionality of printed parts, but they will also allow for greater efficiencies in printing processes. Users, whether they are hobbyists or industry veterans, must stay attuned to these advancements to ensure they can leverage the best available options in their projects.
Moreover, with ongoing developments in related fields, like machine learning and material science, there is an increased potential to discover novel materials and printing techniques, making the optimization process more intuitive and effective than before. This section aims to shed light on two critical components shaping the future of strength optimization in 3D printing.
Advancements in Material Science
Material science sits at the heart of innovations in strength optimization. The exploration of new materials often leads to staggering improvements in printed part performance. For instance, research into composite materials, which blend the properties of different polymers, can lead to significant increases in strength and durability. By combining, say, carbon fiber with PLA, one can achieve a lightweight material that possesses superior tensile strength compared to either component on its own.
Key trends in material advancements include:
- Biodegradable materials: As sustainability becomes a buzzword, developing materials that maintain strength while being environmentally friendly is essential. These alternatives can effectively reduce the ecological footprint of 3D printing.
- Smart materials: Materials that respond to environmental changes, such as those that change shape based on temperature or light exposure, provide exciting potential, making parts more adaptive.
- Metals and alloys: Advancements in metal 3D printing allow for more complex geometries and designs that were previously unattainable, providing robust solutions for industrial applications.
The collaboration between researchers and manufacturers is crucial in pushing the boundaries of what materials can achieve, ensuring stronger and more reliable 3D prints for various uses.
Integration of AI in Print Optimization
Artificial Intelligence (AI) is rapidly changing numerous industries, and 3D printing is no exception. The integration of AI in print optimization opens up a new frontier in enhancing the durability of printed objects. With AI, the capacity to analyze vast amounts of data allows for smarter printing strategies that adapt in real-time.
Imagine a printing process where AI continually assesses the printed layers for any discrepancies and adjusts the parameters accordingly. This could lead to reductions in material waste and improvements in overall part quality.
Benefits of AI in this context include:
- Predictive analytics: Utilizing historical data to foresee potential failures or weaknesses in the print, thus enhancing design robustness before the printing even begins.
- Optimized print settings: AI can analyze different material behaviors and environmental factors, suggesting optimal print speeds, layer heights, and infill patterns to improve the final product's resilience.
- Automation of quality control: By implementing machine learning algorithms that monitor the printing process, any anomalies can be detected immediately, significantly boosting quality assurance protocols.