Exploring Conductive Ink: Applications and Innovations
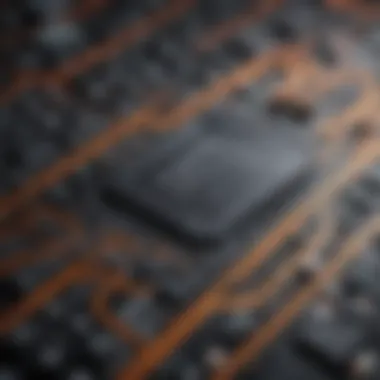
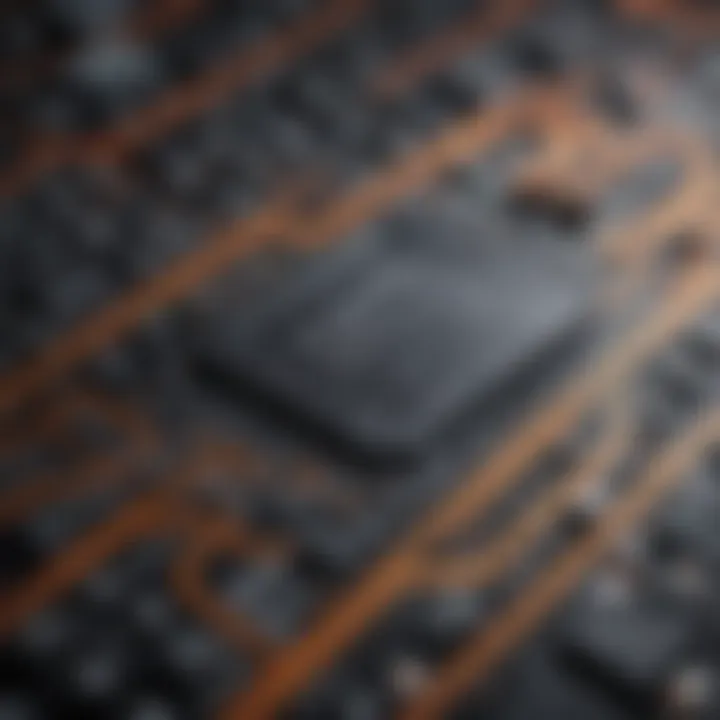
Intro
Conductive inks represent a significant advancement in modern material science, offering various applications within electronics and beyond. These inks consist of a blend of conductive materials, typically metal nanoparticles or carbon-based substances, mixed with a binder or solvent. This composition allows conductive inks to maintain liquid form while ultimately setting into a conductive layer upon drying.
The rapid growth of printed electronics has stimulated interest in conductive inks. These materials facilitate the creation of flexible, lightweight, and cost-effective electronic devices. They have diverse applications, ranging from capacitive touch sensors to antennas and circuitry on flexible substrates. Researchers, professionals, and hobbyists alike are drawn to the innovative potential of conductive inks.
In this exploration, we aim to uncover the many dimensions of conductive ink, examining key applications and innovative developments. The insights yielded through this inquiry offer valuable knowledge relevant to various stakeholders in technology and design.
Intro to Conductive Ink
Conductive ink is a revolutionary material that facilitates the production of electronic components on various substrates. As technology advances, there is a rising demand for lightweight, flexible, and cost-effective materials in electronics. This section aims to shed light on the significance of conductive ink and its ability to transform various industries. Understanding conductive ink is vital for researchers, engineers, and organizations seeking innovation in creating novel electronic devices.
Defining Conductive Ink
Conductive ink refers to a specialized ink that contains conductive materials, allowing it to conduct electricity. Typically, it incorporates materials like silver nanoparticles, carbon-based materials, or conductive polymers. These inks are engineered to be printed using various techniques, making them versatile for numerous applications. The primary purpose of conductive ink is to create electrical pathways on surfaces that may not traditionally support electronic circuits.
Historical Development and Research Background
The concept of conductive ink emerged from the idea of simplifying electronic design and manufacturing. Initial research began in the 20th century, driven by the need for more efficient and less costly means of creating circuits. Early developments primarily focused on the incorporation of metal particles in inks. Over decades, research expanded, leading to innovations in the formulation of inks and the methods of applying them.
Significant advancements were made in the late 1990s when inkjet printing technology became more accessible. This opened new avenues for producing highly intricate designs rapidly and affordably. The past decade has seen an explosive interest in conductive inks, particularly due to the rise of flexible electronics and the Internet of Things. Universities and research institutions are actively investigating new formulations and applications, pushing the boundaries of what conductive inks can achieve.
"Innovations in conductive inks could redefine how we manufacture electronic components and devices."
The journey of conductive inks from laboratory prototypes to real-world applications highlights their importance in modern technology. As industries recognize the potential for cost-saving and design flexibility, the development of conductive inks continues to unlock new possibilities.
Composition of Conductive Ink
The composition of conductive ink is fundamental to its functionality and application across various technologies. Understanding what these inks are made of allows one to appreciate their potential better. The core materials used in conductive inks serve specific roles, impacting their characteristics, performance, and suitability for different applications.
Materials Used in Conductive Inks
Silver Nanoparticles
Silver nanoparticles are a key component in conductive inks due to their excellent electrical conductivity. The miniaturized size of these particles provides a high surface area, maximizing their effectiveness in conducting electricity. This characteristic makes silver nanoparticles a popular choice for applications requiring high precision and reliability.
One unique feature of silver nanoparticles is their ability to form conductive pathways even at low concentrations. As a result, products can remain lightweight and flexible while maintaining conductive properties. However, there are drawbacks; silver is relatively expensive and can be subject to issues of oxidation and long-term durability in certain environments.
Carbon-Based Materials
Carbon-based materials like graphene and carbon nanotubes are gaining traction in the field of conductive inks. Their key characteristic lies in their flexibility and strength, which makes them suitable for a wide range of applications, especially in flexible electronics. Carbon-based materials are considered a beneficial choice due to their cost-effectiveness, exceptional conductivity, and abundant availability.
A unique feature of carbon is its versatility; it can be manipulated to enhance electrical properties or increase mechanical strength. However, their conductive properties may not reach the same level as silver, requiring careful formulation to achieve desired outcomes.
Conductive Polymers
Conductive polymers are another critical component when discussing the composition of conductive inks. These materials are valued for their lightweight nature and tunable conductivity, making them suitable for various applications in electronics. The key characteristic of conductive polymers is their ability to be processed in solution, allowing for complex patterns and designs that are essential in modern electronics.
The unique feature of conductive polymers lies in their environmental stability and mechanical flexibility. They can endure bending and stretching while maintaining their conductive properties. However, they may exhibit lower overall conductivity compared to metals, which poses challenges in applications where high conductivity is essential.
Chemical Properties and Conductivity Mechanisms
The chemical properties of conductive inks play a significant role in determining their effectiveness. Conductivity in these inks happens through various mechanisms, including hopping, tunneling, and percolation. Understanding these principles is essential for researchers and engineers aiming to innovate and optimize conductive ink formulations.
Conductive inks typically require specific conditions — such as temperature and humidity — which influence their performance. Furthermore, the choice of additives can enhance properties like adhesion and long-term stability.
In summary, the composition of conductive ink is a blend of advanced materials, each contributing unique benefits and challenges. Recognizing the significance of these components is crucial for driving advancements in technology and applications relevant to conductive inks.
Manufacturing Processes of Conductive Ink
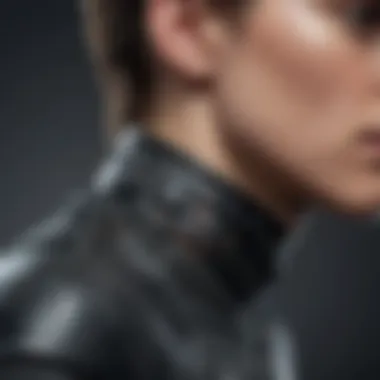
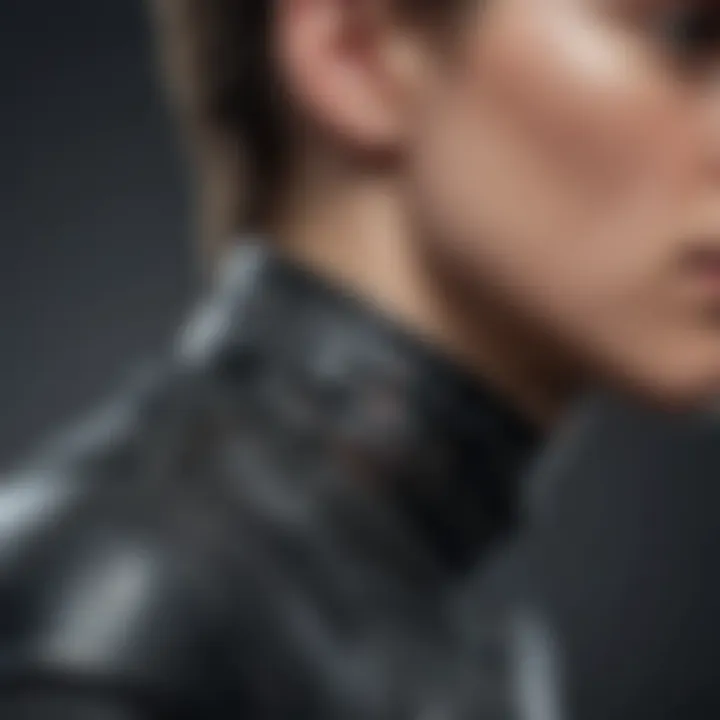
The manufacturing processes of conductive ink are crucial to the overall quality, functionality, and applicability of this innovative material. As the demand for advanced electronic solutions increases, the methods used to produce conductive ink can significantly influence its performance characteristics in various applications. By understanding these processes, stakeholders can make informed decisions about material choices, production techniques, and quality assurance practices.
Production Techniques for Conductive Ink
Screen Printing
Screen printing is a widely known method in the production of conductive ink, allowing for precise application on various substrates. One significant aspect of screen printing is its ability to create thick and continuous traces, which is essential for ensuring reliable electrical conductivity. The key characteristic of screen printing is the use of a mesh screen that transfers the ink onto the substrate through a stencil.
This method is beneficial because it supports large-scale manufacturing, making it a popular choice for high-volume production runs. The unique feature of screen printing lies in its flexibility with different inks and substrates, including textiles and plastics. However, one notable disadvantage is that it may not be suitable for highly intricate designs due to the limitations in resolution.
Inkjet Printing
Inkjet printing presents another fascinating approach to the production of conductive inks. This technique utilizes digital technology to eject tiny droplets of ink onto the substrate, which allows for the creation of complex patterns with high precision. The key characteristic of inkjet printing is its ability to selectively deposit the ink, reducing waste and making it suitable for prototypes and small batches.
Inkjet printing is particularly popular due to its capability to quickly adapt designs without the need for extensive setup. The unique feature of this method is its high-resolution output, enabling intricate designs that might be challenging for other techniques. On the flip side, the main disadvantage is the potential for lower conductivity if the ink’s composition isn’t optimized for this technology.
Roll-to-Roll Processing
Roll-to-roll processing has emerged as a highly efficient production technique, particularly for flexible substrates. This continuous method allows for high-speed production, suitable for large-scale applications. The key characteristic of roll-to-roll processing is that it enables mass production while maintaining uniformity across the product. This makes it a favorable choice for industries that require consistent quality, such as the production of large printed electronic circuits.
One unique feature of this technique is the ability to integrate multiple processes, such as printing, coating, and drying, into a single line. However, a minor disadvantage is the complexity involved in transitioning between different types of substrates, which may impact production speed and efficiency.
Quality Control in Conductive Ink Production
Quality control is an essential aspect of conductive ink production. Ensuring that the final product meets specific standards for conductivity, viscosity, and adhesion is critical to its reliability in applications. Various techniques for quality assurance may include testing for electrical properties and assessing the uniformity of the printed patterns. Quality control measures help in minimizing defects, enhancing product reliability, and ensuring that the conductive ink performs as intended in practical applications.
Quality control is an ongoing process that ensures the efficacy and reliability of conductive inks in their end applications.
In summary, the manufacturing processes of conductive ink encompass several production techniques, each with its own benefits and challenges. Understanding these methods can enhance their applications across fields, promoting further innovation and adaptation.
Applications of Conductive Ink
Conductive ink has transcended traditional boundaries, establishing itself in various sectors due to its versatility and functionality. Its applications are crucial for modern innovations, providing significant advantages in manufacturing and design processes. The significance of applications in conductive ink extends to numerous fields including electronics, textiles, and healthcare. Each application takes advantage of unique properties inherent to conductive inks, enabling solutions that were not possible before.
Flexible Electronics
Flexible electronics represent a transformative measure in technology and design. Conductive ink provides the means to produce circuits on flexible materials, which offers numerous benefits in usability. This flexibility supports the manufacturing of lighter and thinner electronic devices. Moreover, they enable the integration of electronics in unlikely places, expanding the potential for innovation.
Wearable Technology
Wearable technology has gained immense popularity due to its convenience and functionality. The integration of conductive ink allows for real-time data collection in devices like smartwatches and fitness trackers. A key characteristic is the lightweight and bendable nature of these devices, making them more user-friendly. Additionally, conductive inks can seamlessly adhere to textiles, providing a more comfortable experience for users.
However, one must consider durability. While conductive ink enhances wearables' functionality, it may face wear-and-tear issues over time.
Smart Textiles
Smart textiles are another field benefiting from conductive ink. These fabrics can monitor health parameters, providing valuable data without the need for traditional devices. A significant advantage of smart textiles is their ability to blend technology with fashion, making them appealing to a broader audience. The unique feature here is the capacity to integrate sensors directly into the fabric, creating garments that react to environmental stimuli.
Nevertheless, the scalability of smart textiles could be a challenge. While potential exists, the manufacturing processes remain complex and may deter widespread adoption.
Printed Circuit Boards
Printed Circuit Boards (PCBs) are fundamental components in virtually all electronic devices. Conductive inks facilitate the production of PCBs through methods like screen printing or inkjet printing. This method enables rapid prototyping and customization of circuit designs, which traditional methods cannot match. Conductive inks reduce costs significantly, allowing smaller firms to participate in PCB manufacturing.
Internet of Things Devices
The Internet of Things (IoT) relies heavily on the use of conductive inks, particularly in the production of smart sensors and other connected devices. The ability to print electronic components directly into various substrates expands the possibilities for IoT applications. As these devices become more prevalent, the demand for versatile and efficient manufacturing practices rises.
Sensors and Biosensors
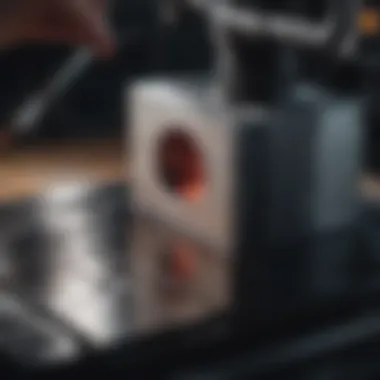
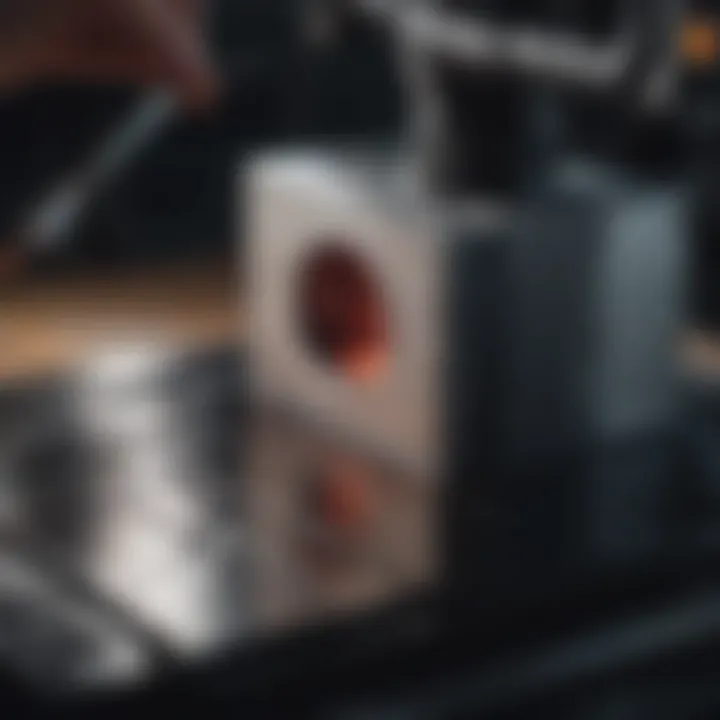
Sensors and biosensors are essential for numerous fields such as healthcare and environmental monitoring. Conductive ink can be employed to produce low-cost, sensitive sensors that can detect various parameters, including heart rate or pollutants. One of the main strengths is that they can be made lightweight and portable.
However, the challenge lies in ensuring the accuracy and reliability of these sensors in real-world applications.
"The potential applications of conductive ink are vast, touching facets of daily living that require innovation and adaptability."
In summary, the application of conductive ink spans several industries, each with its unique challenges and prospects. Understanding these applications provides insight into how conductive ink shapes future developments in technology.
Advantages of Conductive Ink
Conductive ink has emerged as a game changer in various fields, proving its importance across multiple industries. The advantages of using conductive ink are numerous and touch upon key elements such as cost-efficiency, flexibility, and environmental benefits. Understanding these advantages is crucial for professionals and researchers who seek to innovate and optimize processes in their respective fields.
Cost-Efficiency Compared to Traditional Methods
One major benefit of conductive ink lies in its cost-effectiveness compared to traditional conductive materials. For instance, silver paste is often used in conventional electronics. While effective, it can also be quite pricey due to the cost of raw materials and the complexity involved in its application. Conductive ink, on the other hand, leverages cheaper materials like carbon and polymers. This allows manufacturers to achieve similar conductivity levels while significantly reducing production costs.
Moreover, the ability to print conductive patterns using methods such as inkjet printing eliminates several steps in the manufacturing process, leading to lower labor costs and fewer waste materials. This streamlined approach not only cuts down the cost but also the time necessary for production. As a result, businesses can scale operations while maintaining profit margins.
Flexibility and Customizability
The flexibility of conductive ink is another significant advantage. Unlike traditional circuitry, which often relies on rigid substrates, conductive ink can be printed on various materials, including plastic, paper, and textiles. This characteristic enables the development of flexible electronics that can conform to a variety of shapes. For instance, smart wearable devices that monitor health metrics leverage this flexibility, providing comfort without compromising functionality.
Customization is another dimension where conductive ink excels. Manufacturers can easily modify the ink's composition or printing patterns to meet specific design or functional requirements. Custom circuits can be created for unique applications without the need for costly molds or dies. Thus, industries like automotive and healthcare benefit from quicker iterations and tailored solutions.
Environmental Benefits
Beyond financial and practical advantages, conductive ink offers notable environmental benefits. As industries increasingly focus on sustainability, the use of conductive inks aligns well with green practices. They often require fewer hazardous materials than traditional conductive substances, making them safer for both the environment and the people who work with them.
The ability to use less energy during the manufacturing process is an additional perk. Such inks often cure at lower temperatures. This results in lower energy consumption and minimized emissions, addressing ecological concerns. Through recycling and the utilization of bio-based materials, conductive ink can also contribute to a reduced carbon footprint.
"Utilizing conductive ink not only pushes the boundaries of technology but also represents a sustainable approach to industrial practices."
Embracing conductive ink technology can lead to innovations that not only enhance functionality and reduce costs but also address pressing environmental challenges. These advantages play a critical role in positioning conductive ink as an important player in modern and future applications.
Limitations and Challenges
Conductive ink stands at the intersection of innovation and practicality. However, it is essential to acknowledge the limitations and challenges that come with its use. Understanding these factors is crucial for maximizing the utility of conductive inks in various applications. While their advantages are notable, potential users must navigate through issues like durability, production scalability, and material availability to implement these technologies effectively.
Durability and Stability Issues
One of the primary concerns regarding conductive ink is its durability. Unlike traditional conductive materials, such as copper or aluminum, conductive inks often exhibit less robustness. They can be susceptible to environmental conditions, such as humidity and temperature fluctuations. This can lead to degradation over time, affecting performance. In applications where long-term reliability is critical, such as in wearable technology, the ink must maintain conductivity under stress.
There are various strategies to enhance durability. For example, researchers are exploring composite materials that combine conductive inks with protective coatings. This approach aims to improve resistance to wear and tear. Another potential solution is the development of inks with inherent elastic properties, allowing them to withstand bending and stretching without losing conductive capabilities.
Scalability of Production
The scalability of conductive ink production remains a significant challenge. While processes like screen printing and inkjet printing facilitate small-scale manufacture, scaling up presents logistical and technical difficulties. The consistency of quality in larger batches can vary, leading to performance discrepancies in the final product. Meeting the demands of mass production while ensuring that the conductive properties remain intact is often complicated.
Emerging technologies, such as automated printing technologies, are being researched to tackle these issues. These advancements promise to streamline production processes while maintaining stringent quality control measures. Additionally, better understanding the rheology of inks can help improve their application in high-throughput production environments.
Material Costs and Availability
Material costs play a critical role in the adoption of conductive inks. Many conductive inks use precious metals like silver, which can make them expensive compared to traditional methods of producing conductive pathways. The price fluctuation of these materials can pose a challenge as well. Moreover, sourcing high-quality materials consistently can be difficult due to market demand and geopolitical factors.
Strategies to mitigate these challenges involve researching alternative materials. Carbon-based materials, for example, are part of ongoing investigations. These materials are not only more abundant but also potentially cheaper than traditional ingredients. By focusing on developing inks that utilize these alternative resources, researchers can help reduce costs significantly.
Innovations and Future Trends
The field of conductive ink is experiencing rapid evolution. This section addresses the critical innovations and future trends shaping the world of conductive inks. Understanding these trends is vital for industry professionals, researchers, and educators who wish to stay abreast of developments that could redefine production methods and product functionalities.
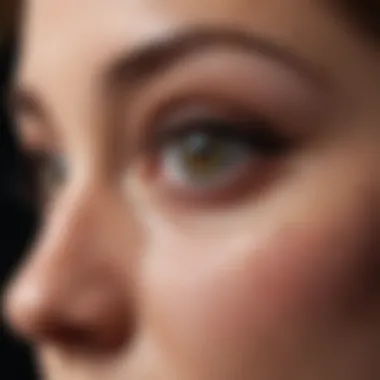
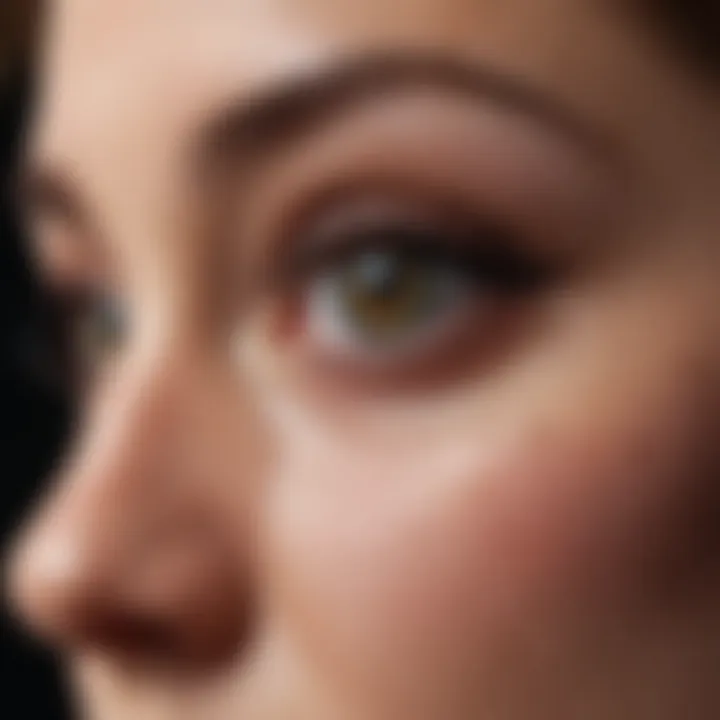
Emerging Technologies in Conductive Ink Development
Recent advancements in technology are continuously enhancing the performance of conductive inks. Techniques such as nanotechnology and advanced synthesis methods are paving the way for inks that offer improved conductivity and flexibility. For instance, the incorporation of graphene and carbon nanotubes in conductive inks has shown a significant increase in electrical performance.
Furthermore, research is focusing on developing inks that can function under extreme conditions, such as high temperatures or varying humidity levels. These innovations not only enhance the usability of conductive materials in diverse applications but also offer potential for new industries to adopt these technologies. Enhanced performance can be crucial for applications in sectors like healthcare and aerospace, where reliability is non-negotiable.
Integration with Advanced Manufacturing Techniques
As the demand for efficiency in production rises, the integration of conductive inks with advanced manufacturing techniques becomes essential. Techniques like additive manufacturing and 3D printing are successfully incorporating conductive inks, leading to novel manufacturing methods. This integration allows for the production of intricate designs and structures with reduced waste.
In essence, additive manufacturing enables the creation of complex electronic devices that can be tailored to specific functions, often within a single print. This can expand the application of conductive inks in areas like custom electronics and personalized devices. The convergence of these technologies creates opportunities for innovations that were previously unimaginable.
Future Market Prospects and Growth Opportunities
The market for conductive inks is projected to grow significantly in the coming years. Demands are driven by advancements in consumer electronics, wearable technologies, and the increasing trend of IoT. The potential for conductive inks to contribute to lighter, more efficient products fuels this growth.
Investors and companies are recognizing the importance of sustainability in production processes. Future trends show a preference for environmentally friendly materials, which could expand the range of conductive inks available in the market. As industries seek to reduce their carbon footprint, this shift could lead to novel formulations of conductive inks made from sustainable sources.
"The intersection of technology, sustainability, and functionality will define the future of conductive inks."
Implications for Society
The implications of conductive ink reach far beyond its technical aspects; they resonate through various sectors of society, altering how industries function and how products are conceived. These implications highlight the transformative potential of conductive ink in electronic design, textile innovation, and health care technology. The societal impact is significant when considering the path forward in terms of sustainability, usability, and economic influence. Conductive ink provides a bridge between traditional manufacturing practices and modern needs, emphasizing efficiency and adaptability in production.
Impact on Industries
Electronics
Conductive ink plays a crucial role in the electronics industry, offering unique advantages that enhance both product design and manufacturing processes. Its flexibility allows for the creation of stretchable circuits that can conform to various shapes and sizes, ideal for wearable technology. The key characteristic of conductive ink in this industry is its capability to reduce the overall size and weight of electronic devices. This is particularly beneficial in applications requiring compactness without compromising functionality.
A unique feature of conductive ink is its application in printed circuit boards. It enables the production of circuits that are lightweight and capable of being printed on flexible substrates. The primary advantage here is the potential for innovation in designing smaller and more integrated devices. However, issues around durability persist, raising questions about long-term reliability under varying environmental conditions.
Textiles
In the textiles sector, conductive ink has ignited a new wave of innovation that combines fabric with electronic capabilities. The integration of conductive materials into textiles has led to the development of smart clothing, enabling functionalities such as monitoring vital signs or providing heating through embedded sensors. The key characteristic making conductive ink favorable for textiles is its compatibility with existing fabric manufacturing processes, which allows for seamless integration.
Textiles imbued with conductive ink highlight a unique feature: the potential for washing and enduring wear without compromising electronic functionality. This resilience is an advantage, but it is imperative to consider washing conditions that may affect conductivity over time. Moreover, the aesthetics of smart textiles pose a challenge, as achieving an appealing look while maintaining functionality is crucial for widespread acceptance.
Healthcare
The healthcare industry benefits from conductive ink through the development of advanced biosensors and wearable medical devices. Conductive ink enables real-time monitoring of physiological parameters such as heart rate and temperature. This aspect of healthcare innovation is compelling, as it promotes preventive care and allows for remote patient monitoring.
A key characteristic of conductive ink in this field is its ability to produce low-cost medical devices that are vital for broader access to healthcare solutions. The unique feature of these devices is their potential for integration with mobile health applications, enhancing user engagement and data collection. However, the challenges include ensuring reliability and accuracy in critical health monitoring scenarios, where errors can have serious implications.
Potential for Sustainable Solutions
In summary, conductive ink stands as a pivotal technology with implications that stretch across multiple sectors. Its contributions to industries such as electronics, textiles, and healthcare illustrate a shift towards more integrated, efficient, and innovative practices. Furthermore, the continuous evolution and optimization of conductive ink may stimulate advancements in sustainable solutions, influencing future developments that align with environmental goals and societal needs.
"The intersection of technology and society is where transformative ideas arise, and conductive ink exemplifies this interplay in modern innovation."
The role of conductive ink not only shapes products but also fosters a new understanding of how these innovations can lead to more sustainable practices in traditional and emerging industries.
Culmination
The exploration of conductive ink culminates in understanding its profound implications and future potential. Conductive ink is a transformative material that broadens the horizons for technical innovation. Its development has led to new applications across various sectors, enhancing manufacturing processes and facilitating the demand for lighter, more flexible electronics. The versatility of conductive ink is not only revolutionizing product design, but it also addresses several critical needs in modern society.
Summary of Key Points
- Variety of Applications: Conductive inks are finding uses in wearable technology, smart textiles, and printed circuit boards, among others. Each application highlights its ability to merge functionality with design.
- Material Composition: Understanding the materials involved, like silver nanoparticles and conductive polymers, provides insight into how conductivity is achieved and tailored for specific needs.
- Advantages Over Traditional Methods: This ink offers notable benefits, such as cost efficiency and environmental friendliness, presenting itself as a favorable alternative in various manufacturing processes.
- Challenges: Despite its numerous advantages, conductive ink faces challenges. Issues like durability, stability, and production scalability remain key considerations for future development.
- Innovations: Emerging technologies promise to enhance the capabilities of conductive inks, fuel growth opportunities, and integrate with advanced manufacturing techniques.
Future Directions for Research
Future research in conductive ink is poised to tackle the ongoing challenges faced in the field. Increasing durability through material design is crucial, allowing conductive inks to withstand harsher conditions without losing functionality. Additionally, further innovation in the synthesis of conductive materials could improve cost efficiency and effectiveness.
Exploring sustainable materials for conductive ink presents a notable direction, promoting environmental responsibility. The impact of nanotechnology in the development of conductive inks is another frontier worth investigating, as it can lead to the enhancement of conductivity and application versatility. Finally, integrating conductive ink with digital fabrication techniques may open avenues for rapid prototyping and custom designs in electronics.