Mastering ABS Print Speed in 3D Printing
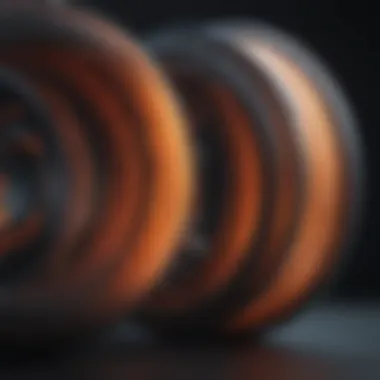
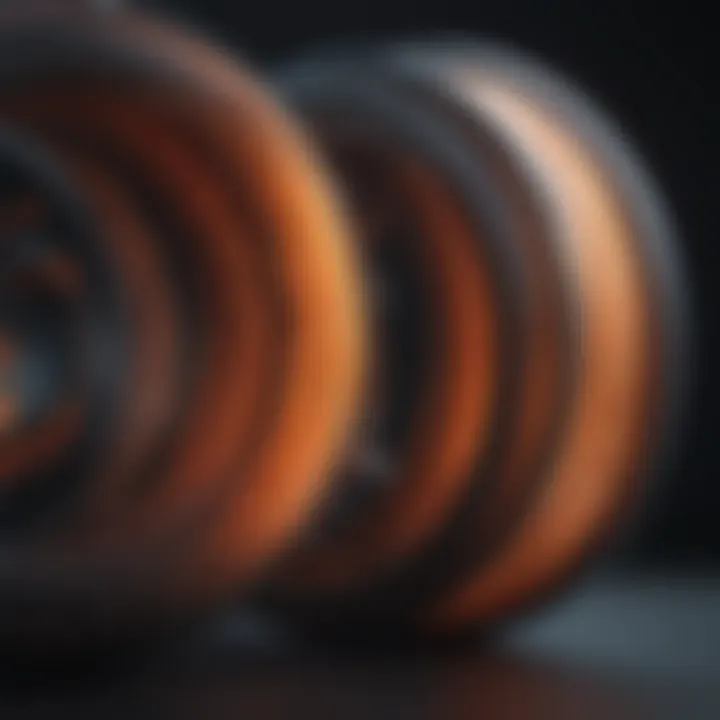
Intro
Additive manufacturing has evolved rapidly over the past few years, with various materials gaining prominence for different applications. Among these, Acrylonitrile Butadiene Styrene (ABS) stands out due to its unique properties and versatility. Understanding the print speed of ABS is crucial for optimizing the quality of prints and enhancing overall productivity. The nuances of ABS print speed impact everything from layer adhesion to the structural integrity of the final product. As such, grasping the intricacies of these factors is essential for both practitioners and enthusiasts in the 3D printing landscape.
In this exploration, we will examine the elements that govern ABS print speed. We will discuss settings that affect performance, compare ABS with other materials, and delve into the complexities of temperature management. Additionally, we will address the challenges practitioners face in achieving their desired output, providing practical insights alongside technical details. This comprehensive guide aims to enrich the reader's understanding and equip them with strategies for refining their 3D printing processes.
Prolusion to ABS Printing
The realm of 3D printing presents many materials, and Acrylonitrile Butadiene Styrene, commonly referred to as ABS, stands out for its unique properties and applications. Understanding how to efficiently utilize ABS in printing underscores the importance of grasping not just its characteristics, but also the nuances of its print speed.
With 3D printing becoming universal in various industries, the significance of mastering ABS printing cannot be overstated. Print speed emerges as a focal point in this process as it directly influences both the operational efficiency and the quality of the end product. So, why does the balance of speed and quality matter? Higher print speeds can reduce production time significantly, yet this must be tempered with the demands of layer adhesion and surface finish. This article serves as a comprehensive guide to navigate these complexities, establishing a strong foundation for both novices and seasoned practitioners.
What is ABS?
Acrylonitrile Butadiene Styrene is a thermoplastic polymer known for its robustness and versatility. Its combination of materials provides an optimal blend of strength, toughness, and flexibility. ABS is widely used in durable applications ranging from consumer products to industrial components. It is recognized for its ability to be shaped under heat, allowing it to be molded and milled with ease. This adaptability makes it a favored choice for 3D printing, particularly in prototyping and functional parts that require resilience.
Importance of Print Speed
Print speed is an essential variable in the 3D printing process, impacting both production efficiency and part integrity. It refers to the speed at which the printer's nozzle moves while depositing material. A faster print speed can lead to reduced print times, which is advantageous in production settings where efficiency is critical.
However, the relationship between print speed and quality is intricate.
- Quality Concerns: High speeds might lead to less accurate layer adhesion, resulting in weak parts.
- Surface Finish: The appearance of the final product can suffer if excess speed is not managed properly.
It is crucial to find an optimal print speed that aligns with the specific characteristics of ABS and the demands of the project. Striking this balance is what enables effective use of this versatile material, thus enhancing the overall performance of 3D printing tasks.
Fundamental Principles of Print Speed
Understanding print speed is essential for anyone involved in 3D printing, particularly when using Acrylonitrile Butadiene Styrene (ABS). The print speed impacts not just how quickly a model is built, but also the final quality of the object produced. In this section, we will define print speed and explore the various factors that influence it, providing a clearer understanding of how they interact and contribute to successful ABS printing.
Defining Print Speed
Print speed refers to the rate at which a 3D printer moves its extruder while laying down filament. Typically measured in millimeters per second (mm/s), it largely dictates the duration of a print job. However, it is not merely about moving faster; the quality of the final product is also influenced by how efficiently the printer operates at different speeds. Too high a speed can lead to problems such as poor adhesion, while too low can prolong the print time unnecessarily. The right balance needs to be found based on the model complexity and desired finish.
Factors Affecting Print Speed
Numerous factors can affect print speed, and understanding them is key to optimizing the printing process. Below are some critical elements to consider:
Extruder Speed
Extruder speed directly impacts how quickly material is melted and extruded. High extruder speeds increase the flow of filament, allowing for faster prints. However, excessive extruder speed can lead to stringing and oozing, which detracts from print quality. The typical range varies depending on the type of printer and material used. For ABS printing, a balanced extruder speed between 40 and 60 mm/s is often recommended to maintain quality while improving efficiency. Adjusting this speed carefully can lead to better layer adhesion.
Layer Height
Layer height plays a significant role in print speed and overall quality. Thinner layers yield higher resolution prints, but require more time to complete, as more passes are needed to achieve the desired height. Conversely, thicker layers speed up the printing process but may compromise detail. Generally, for ABS, a layer height of 0.2 mm represents a good compromise, offering decent detail while maintaining reasonable print times. It can be adjusted according to the complexity of the model and quality expectations.
Flow Rate
Flow rate determines how much filament is pushed through the extruder for each unit of distance covered. Adjusting the flow rate can ensure that the correct amount of material is deposited for the desired layer height and speed. Too high a flow rate might result in over-extrusion, leading to blobs, while too low can create gaps and under-extrusion. A typical flow rate setting for ABS is around 100%, although this can be fine-tuned based on specific printing conditions. Managing flow rate effectively contributes to smoother surfaces and better adhesion between layers.
By analyzing each of these elements, users can better appreciate their synergy and adjust settings accordingly. Navigating the complexities of ABS print speed requires a thorough understanding of these principles.
Optimal ABS Print Speed Settings
When discussing 3D printing, specifically with Acrylonitrile Butadiene Styrene (ABS), one cannot overlook the importance of print speed settings. The optimal settings are crucial not only for achieving the desired mechanical properties but also for the aesthetic quality of the final print. Proper configurations lead to smoother surfaces, better layer adhesion, and overall improved durability.
The benefits of identifying the right print speed are profound. Higher speeds can increase production rates, which is valuable for prototyping or mass production. However, pushing speeds too high may compromise quality, resulting in defects like stringing or poor layer bonding. Thus, balancing speed and quality becomes paramount in any printing project involving ABS.
Considerations for optimal print speed settings include:
- Printer specifications: Each machine has its own limitations and characteristics that influence maximum achievable speed.
- Model complexity: Intricate designs may require slower speeds to ensure details are not lost or distorted.
- Layer height: Using a lower layer height can improve detail but may necessitate slower speeds to maintain quality.
- Filament quality: Not all ABS filaments behave the same way. Some are engineered to withstand higher speeds, while others prefer more cautious handling.
By understanding these aspects, practitioners can effectively adjust their print speeds, ensuring that the final result is both functional and visually appealing.
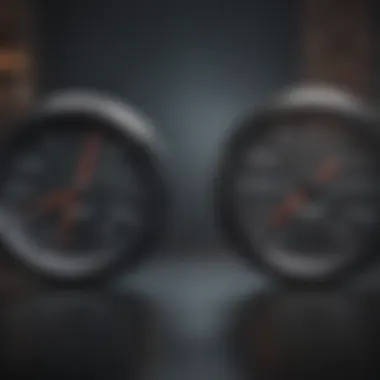
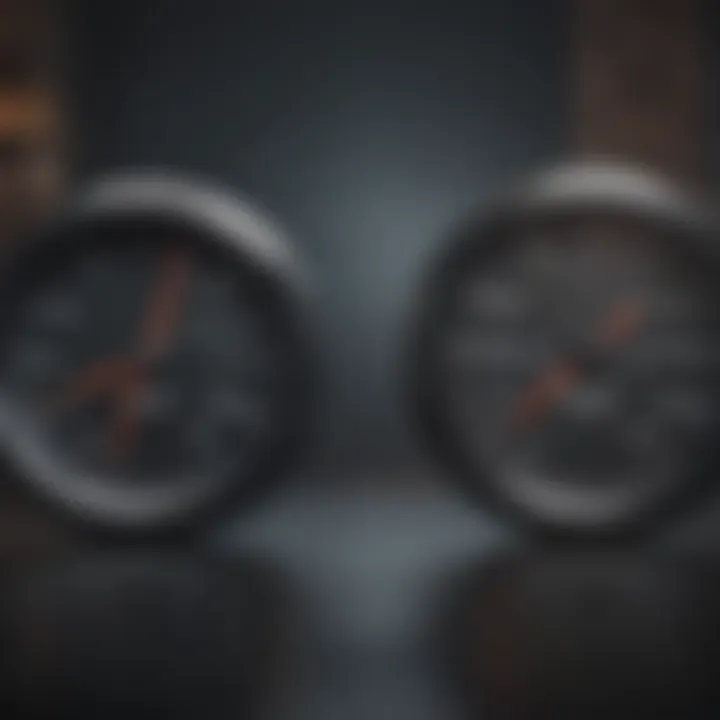
Recommended Speed Ranges
Determining the appropriate speed range for ABS printing can be influenced by several factors. Generally, a range of 40 mm/s to 100 mm/s serves as a solid baseline.
- Low Speed (40-60 mm/s): Ideal for intricate and detailed prints where quality takes precedence. Slow speeds allow for better layer adhesion and finer details.
- Medium Speed (60-80 mm/s): A balanced approach suitable for most general printing tasks. It offers a good compromise between speed and quality.
- High Speed (80-100 mm/s): Recommended for larger, less detailed prints. Caution is advised here. While reductions in print time are significant, quality may start to degrade.
Printing at the upper limits of speed can introduce issues:
- Decreased layer adhesion
- Increased likelihood of defects such as warping or stringing
Many users will find success by starting in the middle of these ranges and then making adjustments based on their specific printer, environment, and material properties.
Customizing Print Speed for Projects
Customization of print speed settings is essential when working with ABS due to its unique characteristics. Different projects demand different approaches, and tailoring settings can make a significant impact on the outcome.
Begin with defining project goals. If quicker turnaround times are critical, a higher speed setting can be considered. For parts subject to mechanical stress, a slow speed may yield better results. When customizing, consider using slicing software.
Here are aspects to modify:
- Infill and Shell Speed: Adjusting infill print speed separately from outer walls can yield stronger parts while maintaining good surface finish.
- Layer Height Adjustments: Combine layer height and print speed adjustments to optimize time vs quality.
- Acceleration and Jerk Settings: Knowing how fast the printer can change directions will help control vibrational issues that can occur with high-speed printing.
Ultimately, understanding ABS properties and having adaptable settings allows 3D printing to meet specific demands. Experimentation is encouraged. Tools such as reditt can offer community-experienced advice tailored to unique situations.
"Ultimately, the key to success in ABS printing lies in the balance of speed and quality, fine-tuning settings to match the specifics of each project."
By honing in on these elements, users can effectively yield prints that meet both their performance criteria and aesthetic desires.
Impact of Print Speed on Quality
The speed at which your ABS printer operates is crucial to achieving prints that meet your desired specifications. It is not merely about completing a project quickly; rather, it significantly affects the quality of the final output. Print speed influences essential characteristics like layer adhesion, surface finish, and detail preservation. Understanding these impacts is vital for both hobbyists and professionals striving for excellence in additive manufacturing.
Effects of Speed on Layer Adhesion
Layer adhesion is a fundamental aspect of successful 3D printing using ABS. When the printer operates at high speeds, the extruded filament may not bond adequately with the previous layer. This can lead to parts that are weak and prone to separation. On the other end, too slow a speed can cause the filament to overheat, resulting in excessive oozing and stringing. Therefore, finding an optimal speed range is critical.
Here are some factors relating to layer adhesion:
- Optimal Speed Range: Typically, ABS prints well within a speed range of 30 to 60 mm/s. Exceeding this range may compromise adhesion.
- Cooling: Fast speeds contribute to a lack of adequate cooling time for each layer, worsening adhesion. A balanced approach to speed and cooling can mitigate these issues.
- Flow Rate: Adjusting the flow rate in accordance with print speed can help maintain consistent extrusion, improving adhesion between layers.
Surface Finish and Detail Preservation
The surface quality of 3D printed ABS parts is largely determined by print speed. Higher speeds can lead to a rougher finish, with visible layer lines and imperfections impacting the aesthetic quality. Conversely, a slower, more deliberate print speed allows the filament to settle more evenly, creating a smoother surface.
Consider these aspects when examining surface finish and detail preservation:
- Fine Details: Faster speeds can erase intricate patterns or details in the model. Precision is sacrificed in favor of speed, which can be detrimental for detailed projects.
- Surface Texture: Variations in speed directly affect the surface texture. Optimal speeds can enhance the overall appearance, allowing for a polished look without significant post-processing.
- Experimentation: Users should be encouraged to test various speeds to see how it affects their specific designs. The results may vary depending on the complexity of the print and the desired outcome.
"Finding the right balance between print speed and output quality is essential for successful ABS printing. Each adjustment can lead to significant changes in the final product's characteristics."
By carefully adjusting print speed, one can significantly influence both the structural integrity of the printed object and its visual appeal. It remains important for users to consider these elements when setting up their printing processes.
Temperature's Role in ABS Printing
In the realm of 3D printing, particularly with ABS (Acrylonitrile Butadiene Styrene), temperature plays a vital role that directly influences the overall print quality and operational efficiency. Understanding how different temperature settings affect printing can help to mitigate common issues such as warping, poor adhesion, and surface defects. This section will explore the significance of nozzle temperature and heated bed considerations, providing insight into the ideal configurations for optimal results.
Influence of Nozzle Temperature
Nozzle temperature is a critical factor in successfully printing with ABS. Typically, ABS requires a nozzle temperature that ranges between 220°C to 260°C. This temperature range is essential for ensuring that the filament flows smoothly through the nozzle, preventing blockages and inconsistencies.
Key effects of nozzle temperature include:
- Melt Flow Rate: Higher temperatures increase the melt flow rate, which allows for better layer adhesion. However, excessively high temperatures may lead to overheating of the filament, causing degradation.
- Viscosity Control: Maintaining the appropriate nozzle temperature keeps the filament at a viscosity conducive to extrusion, leading to finer resolution and accuracy in printed models.
- Stringing and Oozing: If the nozzle temperature is too high, it can introduce issues like stringing and oozing, where excess material leaks from the nozzle, resulting in messy prints.
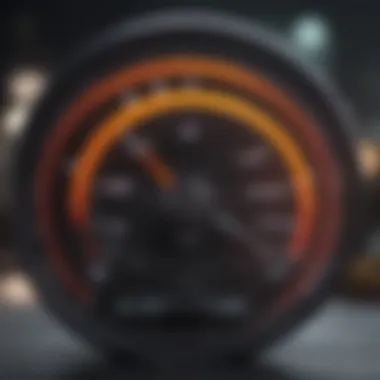
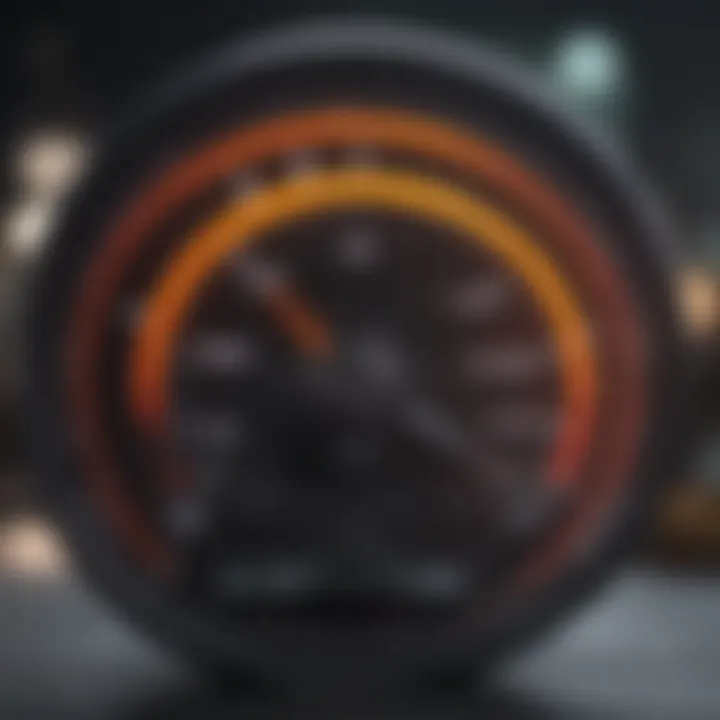
Finding the right nozzle temperature may require experimentation, as different brands of ABS filament can have slightly different recommended temperature settings. As a best practice, begin printing at a mid-range temperature and make adjustments based on the observed print quality.
Heated Bed Considerations
The heated bed is another integral component in ABS printing. It helps in maintaining the adhesion of the first layers to the print surface, crucial for reducing warping. The recommended surface temperature for the heated bed when working with ABS usually lies between 80°C to 110°C.
Important considerations regarding heated beds:
- Reduction of Warping: A heated bed minimizes the temperature gradient between the bottom and top layers of the model, significantly reducing the likelihood of warping as the material cools.
- Adhesion Improvement: The heated surface enhances the bond between the filament and the print bed. It promotes better adhesion, preventing the print from lifting or shifting during the printing process.
- Material Compatibility: Different materials may have different requirements for bed temperature. Therefore, it is advisable to verify compatibility with the specific brand of ABS being utilized.
When optimizing for ABS, a well-calibrated nozzle and heated bed can lead to more successful prints and a more enjoyable printing experience.
Ultimately, the precise control of nozzle and bed temperatures is a hallmark of proficient 3D printing with ABS. Understanding these elements not only aids in boosting print quality but also saves time and resources on future projects.
Comparative Analysis of Materials
In the field of 3D printing, understanding the characteristics of different materials is crucial. A Comparative Analysis of Materials signifies not just a surface-level evaluation but an in-depth examination of how each material performs under various conditions. When it comes to ABS, comparing it with alternative materials like PLA provides insights that are valuable for making informed choices in additive manufacturing. Each material has unique properties affecting strength, flexibility, and printability. By analyzing these properties, one can determine the best material choice depending on the project requirements.
ABS vs. PLA Print Speed Analysis
The comparison of ABS and PLA is significant due to their prevalent use in 3D printing. ABS (Acrylonitrile Butadiene Styrene) tends to exhibit faster print speeds compared to PLA (Polylactic Acid). The differences in chemical composition play a role here. ABS's higher melting temperature enables quicker layer adhesion when print settings are optimized. Conversely, PLA's lower melting point may require slower speeds to ensure layer quality without warping.
- Print Speed Differences:
- Layer Attachment:
- ABS is generally printed at speeds ranging from 60mm/s to 100mm/s, facilitating rapid production of models.
- PLA can be printed at similar speeds but often benefits from lower settings, around 30mm/s to 60mm/s.
- ABS tends to have superior layer bond strength at high speeds when compared to PLA, especially in tall, thin prints.
- PLA may struggle with adhesion when printed too quickly, leading to defects due to weak inter-layer bonding.
In summary, while ABS offers higher speed potential, PLA provides ease of use, particularly for beginners. Understanding these nuances helps users select the right material based on objectives and printing experience.
Performance of Other Thermoplastics
While ABS and PLA are widely recognized, other thermoplastics also possess noteworthy qualities affecting print speed and performance. Materials like PETG (Polyethylene Terephthalate Glycol), Nylon, and TPU (Thermoplastic Polyurethane) demonstrate unique traits that can influence project outcomes.
- PETG:
PETG combines the ease of use found in PLA with the strength of ABS. It is less prone to warping, allowing for a moderate printing speed between 50mm/s and 80mm/s. Its excellent layer adhesion makes it suitable for functional parts. - Nylon:
Known for its toughness and flexibility, Nylon requires careful temperature control. It typically prints slower due to its warp tendencies, with speeds around 30mm/s to 50mm/s often recommended. - TPU:
As a flexible material, TPU requires slow print speeds to ensure proper extrusion and layer adhesion – usually not exceeding 30mm/s. The elasticity of TPU challenges users to adjust settings progressively for quality outcomes.
Overall, considering different thermoplastics offers a holistic view that enhances decision-making in material selection for 3D printing. Each has trade-offs that can significantly affect the print quality, speed, and usability of finished products.
Troubleshooting Print Speed Issues
In the journey of mastering ABS printing, understanding how to troubleshoot print speed issues becomes essential. Problems linked to speed can severely impact the quality of the final product. Addressing these issues promptly leads to better print quality and reduces material waste. Analyzing the common problems and finding effective solutions helps both beginners and seasoned practitioners to enhance their printing experience, making troubleshooting an integral part of the printing process that cannot be overlooked.
Common Problems Linked to Print Speed
Stringing and Oozing
Stringing and oozing are frequent issues encountered during the 3D printing process. These problems occur when excess filament leaks from the nozzle during non-print moves, resulting in fine threads of plastic across the print. This occurs more often when the print speed is set too high, causing an imbalance when the nozzle moves from one area to another.
The key characteristic of this issue is the unwanted strands of filament that disrupt the clean lines of the print. Stringing can lead to poor aesthetic quality, making this an important factor to address. In the context of this article, understanding stringing clarifies how effective speed and movement settings contribute to clean prints.
Advantages of recognizing this issue include the ability to optimize travel speed, retraction settings, and temperature adjustments. A unique feature of stringing is that it can often be fixed with simple adjustments in slicing software. However, if not managed carefully, it can lead to frustrating results.
Layer Misalignment
Layer misalignment represents another significant print speed issue. This occurs when subsequent layers fail to lay down correctly, causing visible shifts in the print. One of the most common causes of layer misalignment is an excessively high print speed that moves the printer head too quickly for the material to adhere properly.
What makes layer misalignment a critical topic is its direct connection to the integrity of the print. When layers misalign, the structural strength of the object is compromised, which can defeat the purpose of printing in the first place. This can be especially detrimental in applications requiring precision.
The unique aspect of layer misalignment is that it can be influenced by several factors, such as mechanical issues within the printer, but print speed is a controllable element. Proper care must be taken to ensure that the speed settings allow for adequate time for layer bonding. The advantages of addressing layer misalignment include producing higher quality prints and reducing the chances of reprints due to errors.
Solutions and Adjustments
To tackle the issues of stringing, oozing, and layer misalignment effectively, several solutions can be employed.
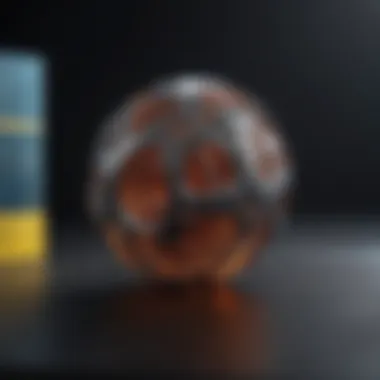
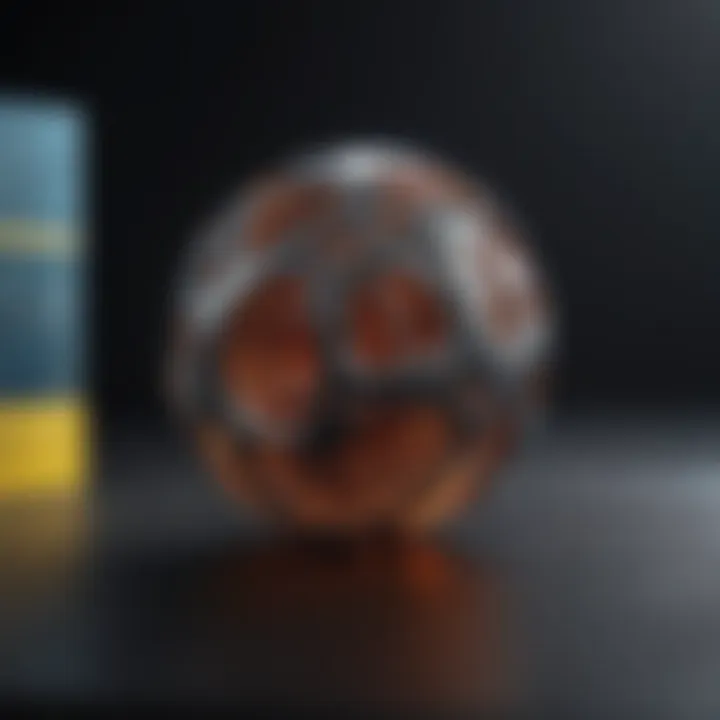
- Adjust Retraction Settings: Increasing the retraction distance can minimize stringing by pulling back filament before the nozzle moves.
- Change Print Speed: Slowing down the print speed can greatly benefit layer adhesion. Slower speeds can enhance the accuracy of layer placement.
- Modify Travel Speed: Reducing the speed at which the print head travels can also lower the chances of oozing.
- Temperature Control: Lowering the nozzle temperature can help in reducing stringing, while ensuring the material still flows adequately during the print.
By systematically diagnosing and adjusting these factors, one can achieve a notable improvement in print quality, making the troubleshooting of print speed issues a vital part of the additive manufacturing process.
Integration of Software in Print Speed Management
In the rapidly advancing field of additive manufacturing, managing ABS print speed has become increasingly reliant on sophisticated software tools. The significance of integrating software in print speed management cannot be overstated. It not only streamlines the printing process but also provides a platform for optimization tailored to individual projects. The right software can enhance precision, reduce material waste, and improve overall print quality.
Slicing Software Optimization
Slicing software plays a vital role in 3D printing. It converts 3D models into instructions that a printer can understand. The optimization of this software directly affects print speed. Key aspects include:
- Layer Height: Selecting an appropriate layer height can improve print time without compromising quality. Thinner layers produce finer details but take longer.
- Infill Density: Adjusting infill density allows users to find a balance between print speed and part strength. Lower densities decrease print time.
- Print Speed Settings: Software settings enable users to specify speed parameters. These include maximum speed, acceleration, and jerk settings, which collectively influence the flow of material during printing.
"The right settings can boost the efficiency of the printing process, reducing costs and enhancing output quality."
Finding the optimal settings requires a blend of understanding practical needs and utilizing the full capabilities of the slicing software. Experimentation with different configurations can yield significant improvements.
Impact of G-code Settings
G-code is the language that drives 3D printers. Generated by slicing software, it comprises a series of commands that dictate every movement and action of the printer. Adjusting G-code settings can have substantial effects on print speed and quality. Key considerations include:
- Movement Speed: This refers to how fast the print head moves while not extruding. Higher speed can lessen print time but might lead to loss of detail.
- Extrusion Speed: This dictates how quickly filament is pushed through the nozzle. The right balance ensures consistent material flow, crucial for print quality.
- Acceleration and Jerk: These parameters govern how quickly a printer can change direction. Calibrating these values can prevent issues like ghosting, where the print quality deteriorates due to excessive movement speeds.
By fine-tuning the G-code, practitioners can optimize print speed significantly. Increased knowledge of each parameter empowers users to achieve their desired outcomes without sacrificing quality.
Future Trends in ABS Printing
The realm of 3D printing, particularly with ABS materials, is continually evolving. Understanding the future trends in ABS printing is vital for anyone involved in the industry. Trends can significantly impact print quality, efficiency, and the overall usability of this versatile thermoplastic. It is crucial to explore emerging technologies and anticipated developments in print speed to grasp the direction of ABS printing.
Emerging Technologies
Innovations in technology play a pivotal role in shaping the future of ABS printing. Key advancements include:
- Improved Printer Designs: Manufacturers are exploring new designs for 3D printers, integrating better cooling systems and enhanced precision mechanisms. This directly affects the print speed and quality of ABS prints.
- Advanced Slicing Software: New algorithms in slicing software are under development to optimize how ABS material is processed. These software innovations streamline the printing process, enabling faster print times without sacrificing quality.
- AI and Machine Learning: The integration of AI can assist in automating print speed adjustments based on real-time analysis of printing conditions. This adaptive approach promises more reliable outcomes, especially in complex prints.
"Emerging technologies not only improve the speed but also enhance the quality of ABS prints, paving the way for greater innovation in the industry."
These new tools and technologies are set to revolutionize how ABS is printed, making it more accessible and efficient for users at all levels.
Anticipated Developments in Print Speed
Future developments in print speed for ABS materials will likely focus on several techniques and approaches:
- Higher Print Speeds: The push for faster printing is constant. Improvements in motor and extruder technology could enable manufacturers to safely increase print speeds without compromising structural integrity or layer adhesion.
- Enhanced Material Formulations: Researchers are likely to produce ABS variants that allow for quicker melting and layering. This may also include blends with other materials to support faster production.
- Automated Calibration Systems: New printers may feature automatic calibration systems that fine-tune settings for optimal print speed and quality, thus reducing the need for manual adjustments.
Incorporating these anticipated trends can significantly change the landscape of 3D printing with ABS materials. Keeping abreast of these innovations is essential for educators, students, researchers, and professionals to stay competitive and effective in the market.
Epilogue and Final Thoughts
In synthesizing the various topics explored within this article, the significance of understanding ABS print speed becomes abundantly clear. ABS, as a widely used thermoplastic in 3D printing, has unique attributes influenced by multiple factors, including print speed. Proper management of this factor not only enhances the mechanical properties of the printed object but also affects the overall aesthetic finish and production efficiency.
The insights gained emphasize several crucial elements. Firstly, one must recognize that print speed is not a one-size-fits-all metric. Each project may demand a tailored approach, influenced by the specific objectives, complex geometries, and desired surface quality. The recommendation of optimal speed ranges can serve as a starting point, but it is through customization that one can truly achieve excellence in printing. Understanding layer adhesion and its correlation with speed lays a foundation for producing reliable and precise prints.
Moreover, the interplay between temperature and print speed is one of the pivotal considerations. Adjusting nozzle temperatures and using a heated bed can mitigate the adverse effects of high speeds, such as warping and detachment. Hence, the relationship between these variables requires continuous evaluation and adjustment, demonstrating that proficiency in 3D printing is as much about the material knowledge as it is about the technical application.
"Through education and experimentation, practitioners can unlock the full potential of ABS printing, leading to innovative and high-quality outcomes."
Thus, the complexity of print speed management in ABS printing encourages deeper investigation and hands-on experimentation. The article's discussions provide actionable insights to assist you in this journey, fostering an environment of continuous learning and adaptation in the evolving landscape of additive manufacturing.
Recap of Key Insights
- Understanding print speed is crucial for optimizing the quality of ABS prints.
- Tailoring speed settings based on specific project needs can lead to better results.
- The importance of temperature management in relation to print speed cannot be overstated.
- Comparison with other materials, like PLA, can contextualize the performance of ABS.
Encouragement for Experimentation
In the spirit of advancement and innovation, practitioners are encouraged to actively engage in experimentation with their printing processes. Every printer behaves differently, and what works well in one setup may not yield the same results in another. Varying print speeds and temperatures based on your observations can greatly enhance the overall quality of your projects.
Take notes during your print sessions. Documenting parameters and outcomes can help identify the patterns that lead to success or failure. Share your findings with others in the community, perhaps through platforms like Reddit or Facebook. Learning from peers, engaging in discussions, or seeking feedback can foster growth and refinement in your approach.
Ultimately, the domain of 3D printing continuously evolves, and those willing to explore new possibilities will undoubtedly find themselves at the forefront of technology. Your dedication to understanding and improving print speed may well lead to innovation that contributes significantly to the field.