Understanding 3D Printing Failures: Causes and Solutions

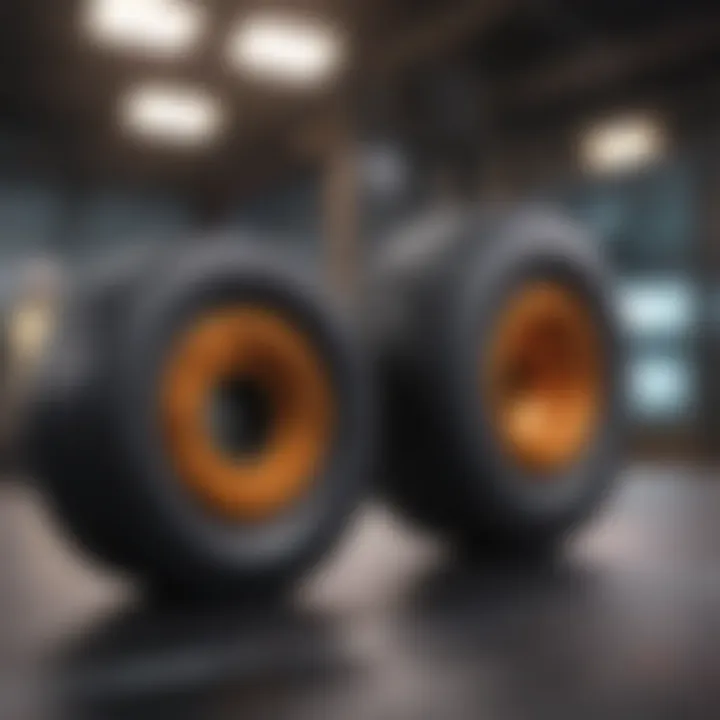
Intro
3D printing has revolutionized the way we approach manufacturing, prototyping, and design. Despite its many advantages, practitioners in this field frequently encounter failures that can derail projects. Understanding these failures becomes crucial for enhancement and innovation. Each hiccup in the printing process not only consumes time and resources but can also diminish the trust in an otherwise promising technology. As the interest in 3D printing grows across various industries, it is vital to dissect the underlying causes of these setbacks, along with appropriate solutions.
In this article, we will analyze why 3D printing failures happen and what can be done to resolve them. We will cover aspects such as technical errors, material issues, and environmental factors that can lead to unsuccessful prints. Furthermore, the exploration of practical methodologies will aid in mitigating these challenges and improving print quality overall.
The following sections will provide a structured approach, allowing readers to not only recognize the symptoms of failure but also grasp effective strategies for resolution.
Foreword to 3D Printing
3D printing has gained prominence as a revolutionary technology, boasting diverse applications across various industries. Understanding this technology helps us grasp its significance in creating complex structures and rapid prototyping. The ability to convert digital designs into tangible objects offers countless possibilities, significantly influencing manufacturing and design processes.
This article emphasizes the importance of grasping fundamental concepts of 3D printing, laying the groundwork for exploring its inherent challenges. Failures in 3D printing processes are not merely inconveniences; they can lead to increased costs, wasted materials, and delays in project timelines. Thus, comprehending how these failures can occur is critical for improvement.
As we delve into the various aspects of 3D printing, we will identify common points of failure, analyze potential causes, and propose effective solutions. We aim to equip readers with detailed knowledge that will bolster their ability to produce successful prints, leading to enhanced overall efficiency.
The Evolution of 3D Printing
3D printing, or additive manufacturing, traces its history to the early 1980s, when Chuck Hull invented stereolithography. This process was one of the first methods to create three-dimensional objects layer by layer using ultraviolet light to cure liquid resin. As the years progressed, several other techniques emerged, including selective laser sintering and fused deposition modeling. These advancements significantly enhanced the capabilities of the technology.
As materials and processes developed, 3D printing evolved from slow, experimental rapid prototyping to a versatile technology with applications in diverse fields. Today, industries including aerospace, healthcare, automotive, and consumer products utilize 3D printing for various purposes. The technology has reached a stage where custom, intricate designs can be efficiently produced and mass-manufactured, creating a competitive edge for businesses.
Current Applications of 3D Printing
Today, the applications of 3D printing are extensive, impacting many sectors. Some of the key areas include:
- Aerospace: Lightweight components are crafted to improve fuel efficiency and reduce costs.
- Healthcare: Customized implants and prosthetics can be produced for tailored fit and functionality.
- Automotive: Prototyping and production of parts allow for quicker and more economical design cycles.
- Architecture: Models can be created to visualize projects before construction begins.
In addition, several innovative uses in education and research fields demonstrate the adaptability of 3D printing. Schools and universities are increasingly using this technology to foster creativity and hands-on learning among students.
In summary, 3D printing has transitioned from a niche technology to a mainstream manufacturing approach. Understanding its evolution and applications is essential as we delve deeper into the nuances, challenges, and solutions that arise in this fascinating domain.
Defining 3D Printing Failures
Defining 3D printing failures is essential to comprehending the complexities within the field of additive manufacturing. In the 3D printing world, understanding the specific types and characteristics of failures helps in identifying the underlying problems and finding solutions. When a print fails, it can lead to wasted time, resources, and effort. Therefore, having a clear framework for defining these failures brings several benefits, including efficient troubleshooting and enhanced print quality.
Types of 3D Printing Failures
Partial Prints
Partial prints refer to situations where a 3D print does not complete fully, leading to models that are either unfinished or missing sections. This failure type contributes significantly to the overall goal of understanding the printing process. One key characteristic of partial prints is the abrupt halt, often triggered by mechanical issues or filament abnormalities. A notable aspect of this failure is its prevalence. Partial prints are common enough to warrant serious consideration in troubleshooting methods. While they may seem merely inconvenient, their occurrence signals deeper issues within the printer setup or operation. Partial prints can waste materials and create cumbersome cleanup challenges. Therefore, addressing them through careful inspection and proactive measures is crucial.
Layer Misalignment
Layer misalignment occurs when the layers of a print do not stack correctly, causing visible gaps or shifts in the printed model. This issue affects the structural integrity and aesthetics of the final piece. The primary factor of layer misalignment connects directly to printer calibration. Calibration ensures that every component works harmoniously. This failure type is popular in discussions surrounding quality control, as misalignment can lead to subpar results. Furthermore, misalignment can obscure the intended design, making it a critical concern. Its unique feature lies in its association with both hardware and software settings, underlining the importance of a holistic approach to 3D printing. Layer misalignment can lead to dissatisfaction and increased print times, making it a vital aspect to understand.
Under-extrusion
Under-extrusion signifies a scenario where insufficient filament flows through the extruder, resulting in gaps and weak spots in printed objects. This failure type can drastically affect the quality and strength of a print. The critical characteristic of under-extrusion is its clear impact on the final product. Prints often appear stringy or incomplete due to this condition, drawing attention to the importance of maintaining filament supply. Under-extrusion often stems from several causes, including clogged nozzles or improper temperature settings. Its implications can range from minor surface imperfections to complete model failure, highlighting the need for awareness of extruder dynamics. Thus, it serves as a crucial point of discussion for efficient print management.
Impact of Failures on the Process
The effects of printing failures extend beyond the frustration they cause. The overall process suffers in terms of time and resource wastage. Every failure incurs additional cost in material and machine wear, requiring additional labor and planning to address effectively. Moreover, frequent failures can instill a lack of confidence in the 3D printing system, affecting user perceptions and future project ambitions. Understanding failures promotes a proactive approach, shifting the focus toward prevention and rectification. Recognizing failure categories allows users to adopt specific strategies tailored to their needs, ultimately enhancing the efficacy of the 3D printing process.
Common Causes of 3D Printing Failures
The importance of understanding common causes of 3D printing failures resides in the significant impact these failures can have on the overall productivity and effectiveness of the printing process. Identifying the exact reasons behind failures can help in rectifying them swiftly, thereby improving print quality and reliability. This section delves into specific issues that routinely emerge during 3D printing processes, including mechanical issues, filament problems, environmental factors, and software errors. Knowing these causes not only assists in remedying current issues but also aids in preventing future occurrences.
Mechanical Issues
Printer Calibration
Printer calibration ensures that the printer operates within its optimal parameters. It specifically involves adjusting the printerโs axes to ensure accurate movement during prints. Proper calibration contributes significantly to print quality. It reduces the risk of misalignment and other discrepancies that might lead to failed prints. With regular calibration, one can expect improved dimensional accuracy and better overall performance. However, it does require time and understanding of the printer's mechanics.
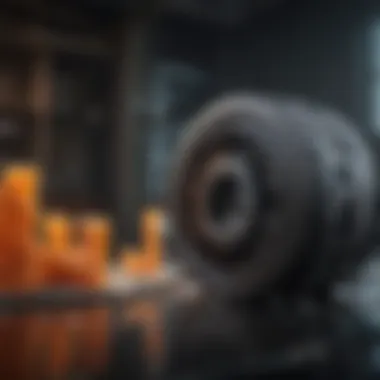
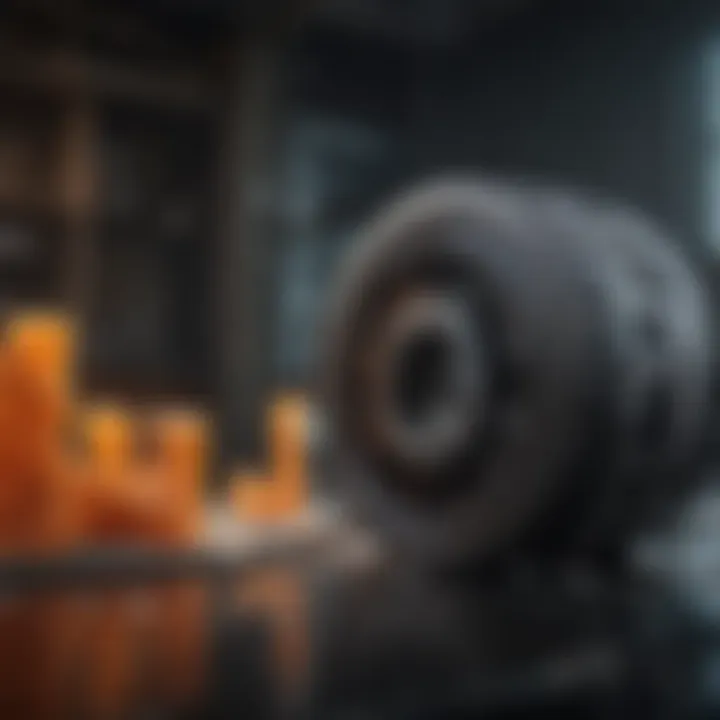
Component Wear and Tear
All printers face component wear and tear over time. This aspect relates to the deterioration of parts such as nozzles, belts, and drive gears. Regular checks on these components are essential to maintain consistent print quality. A worn-out component can cause issues like uneven extrusion and layer inconsistencies, leading to failed prints. It's vital to monitor the condition of these parts to avoid unexpected disruptions in the printing process.
Bed Leveling Errors
Bed leveling errors indicate that the print bed is not positioned correctly in relation to the print head. This condition often leads to poor adhesion of the first layer, which is crucial for print success. Ensuring proper bed leveling frequently prevents multiple printing failures caused by the printing surface being too high or low. Bed leveling is an essential step that should not be overlooked; it significantly enhances the stability of the print job.
Filament Problems
Moisture Absorption
Moisture absorption is a common concern. Many filaments, especially those made of PLA or Nylon, can absorb moisture from the environment. This absorption compromises the filament's strength and can result in poor prints. Understanding the impact of moisture on filament performance is vital. Proper storage solutions, such as desiccants or sealed containers, can mitigate these issues.
Filament Diameter Variations
Filament diameter variations can lead to inconsistent extrusion. Most printers are calibrated for a specific filament diameter, often 1.75mm or 2.85mm. Variations in diameter beyond the tolerances specified by the manufacturer can cause under-extrusion or over-extrusion. Ensuring the correct diameter can improve print outcome and reduce waste during the printing process.
Quality of Filament
Quality of filament is another crucial factor affecting print success. A high-quality filament offers better consistency during printing, while low-quality filament can lead to issues like clogging or inconsistent extrusion. By investing in quality filaments, users can significantly enhance the reliability of their prints and decrease the likelihood of failures.
Environmental Factors
Temperature Variance
Temperature variance affects the printing process significantly. If the ambient temperature varies too much, it can lead to warping and cracking in prints. Maintaining a stable temperature in the printing environment helps to ensure proper adhesion and layer bonding. Any abrupt temperature change can adversely affect print fidelity.
Humidity Levels
Humidity levels play a critical role in print quality, especially for hygroscopic materials. Excessive humidity can degrade filament properties, leading to moisture-related issues in printing. Monitoring humidity and maintaining it within specified limits is essential for keeping filament in optimal conditions for printing.
Air Flow
Air flow can influence the cooling process of prints. For certain materials, excessive airflow can lead to cooling too quickly, which can cause warping. On the other hand, inadequate airflow can result in prolonged cooling times, leading to poor layer adhesion. Finding a balance in airflow around the printer can contribute to improved print results.
Software and Slicing Errors
Incorrect Slicing Settings
Incorrect slicing settings can have a devastating effect on print quality. Factors such as layer height, printing speed, and infill density directly change the way a model is printed. Understanding these settings and configuring them correctly based on the model and material used can significantly reduce the chances of print failure.
Model Design Flaws
Model design flaws often stem from the design software used to create the 3D model. Errors in models such as non-manifold edges or overlapping geometry can cause slicing software to produce ineffective paths for the print head. Thorough checks and repairs can prevent potential print failures arising from these underlying design flaws.
Firmware Issues
Firmware issues may arise when the printer's software does not operate correctly. This can lead to miscommunication between the model and the printer itself. Regular updates and checks of the firmware help maintain printing efficiency. Ensuring the firmware is current can prevent many unexpected printing errors.
Analyzing Failed Prints
The capacity to analyze failed prints is crucial for advancing the efficacy of 3D printing technology. Failure analysis helps identify specific issues that can affect the final outcome. Effectively diagnosing these problems enables the user to avoid repeating mistakes and refine their printing techniques. It not only enhances print quality but also saves time and resources in the long run.
There are two primary methods to analyze failed prints. Visual inspections and data collection through data loggers are fundamental approaches that equip users with insights into what went wrong. Both techniques serve as complementary tools in the overall quality control process.
Visual Inspection Techniques
Visual inspection is often the first line of defense when troubleshooting failed prints. This method offers immediate insights into the nature of the problem. Whether it's an under-extruded print or a model that has not adhered properly to the print bed, physical examination allows an operator to assess various aspects:
- Surface Quality: Check for imperfections, such as blobbing or stringing, on the surface of the print.
- Dimensional Accuracy: Ensure that the dimensions of the printed object match the intended design. Deviations can point to calibration issues.
- Layer Adhesion: Look for signs of separation between layers, which might indicate issues with extrusion settings or material quality.
- Bed Adhesion: Evaluate how well the print adhered to the bed. Poor adhesion can cause warping or detachment during printing.
While visual inspections provide essential information, they often require a trained eye to recognize subtle defects.
Using Data Loggers for Analysis
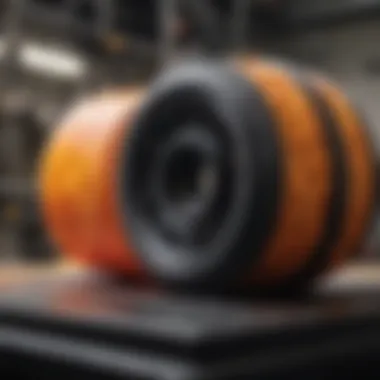

Data loggers serve as an advanced tool for understanding the dynamics of 3D printing failures. By collecting real-time data from various components of the printing process, these devices can unveil underlying issues that may not be apparent through visual inspection alone.
Data loggers can monitor multiple parameters such as:
- Temperature Variations: Tracking the extruder and bed temperatures helps identify inconsistencies that might lead to poor adhesion or material flow issues.
- Movement Accuracy: Monitoring the stepper motors allows operators to see if the printer is executing movements accurately according to the G-code.
- Extrusion Rates: Measuring the filament feed rate ensures that the printer is dispensing the correct amount of material during the print.
Integrating data logger information with visual inspections creates a comprehensive analysis of failed prints. This multifaceted approach allows for a more precise diagnosis and can guide further troubleshooting.
Successful analysis of failed prints leads to innovation and improved printing strategies, reducing costs and increasing efficiency in the long term.
Applying both visual inspection techniques and data loggers can decisively clarify the causes behind 3D printing failures, laying the groundwork for effective solutions and enhanced print quality.
Rectifying Printing Failures
Understanding how to rectify 3D printing failures is crucial for anyone working with this technology. The importance of this topic lies in its ability to improve print quality and efficiency. By addressing issues effectively, a user can save time and resources while maximizing the potential of 3D printing. Rectifying failures not only enhances the output's reliability but also elevates the overall experience for operators and users alike.
Printer Maintenance Protocols
Regular Calibration
Regular calibration is vital for maintaining accurate prints. This involves adjusting the printer's settings to ensure precision in the layering process. A well-calibrated printer provides consistent and high-quality results, reducing the likelihood of failures. Regular calibration contributes significantly to a printer's longevity and performance.
The key characteristic of this practice is that it directly influences print accuracy. It is a beneficial choice for those seeking to improve their print outcome. Ensuring calibration can mitigate common issues like misalignment and poor adhesion.
A unique feature of regular calibration is its requirement for a systematic approach. Users must frequently check alignment and adjust settings as needed. While it is time-consuming, the advantages of reduced errors outweigh the disadvantages, as it leads to a more reliable printing process.
Component Replacement Tips
Component replacement tips focus on the necessity to replace worn or faulty parts. Understanding when and how to replace components can significantly enhance the printer's performance. Regular assessment of the printer's physical condition means that common issues can be addressed promptly, aiding in successful printing.
The key characteristic of component replacement is its impact on the final results. By maintaining the integrity of components, users can expect improved durability and functionality. This practice is beneficial as it helps prevent breakdowns during crucial printing jobs.
Unique to this approach is the understanding of each component's lifespan. The user can prioritize which parts need replacing based on usage frequency. Although replacing components can involve additional costs, the benefits of maintaining optimal machine performance can justify the investment.
Improving Material Handling
Storage Solutions
Effective storage solutions are essential for preserving filament quality. Proper storage prevents issues related to moisture absorption or degradation, which can lead to printing failures. Using airtight containers or desiccants can prolong the lifespan of materials.
The key characteristic of this practice is the prevention of filament damage. This approach offers significant benefits, especially for high-value materials that require specific conditions. Ensuring that filament is stored correctly enhances the likelihood of successful prints.
A unique feature is the need for a controlled environment. Users must consider factors like temperature and humidity. While the initial setup may require effort, the long-term advantages include cost savings and consistent print quality.
Pre-drying Techniques
Pre-drying techniques involve methods to remove moisture from filament before printing. This is especially relevant for materials known to absorb humidity, like nylon or PLA. Pre-drying enhances adhesion and reduces the risk of defects during the print process.
The key characteristic lies in its preemptive nature. Implementing this technique can drastically improve print outcomes. It is a practical solution often favored for high-performance prints.
The unique feature of pre-drying is the various methods available, such as using specialized dryers or ovens. Although it requires additional equipment, the benefits of enhanced print fidelity make it a worthwhile consideration.
Optimizing Environmental Conditions
Controlling Temperature
Controlling temperature is vital for successful 3D printing. Fluctuations can impact filament behavior, leading to warping or delamination. A stabilized temperature helps maintain ideal conditions throughout the print cycle.
The key characteristic of this practice is its direct effect on the printing process. Users who focus on temperature management often encounter fewer issues such as layer separation. This is a beneficial practice that can drastically improve results.
A unique feature is the use of enclosures or heated beds to maintain warmth. While initial setups might require investment, the consistent outcomes justify these measures.
Humidity Regulation
Humidity regulation is just as important as temperature control. High humidity can lead to filament degradation, adversely affecting print quality. Managing humidity ensures that material properties remain stable and that prints are reliable.
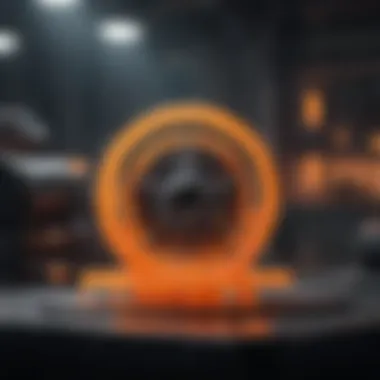
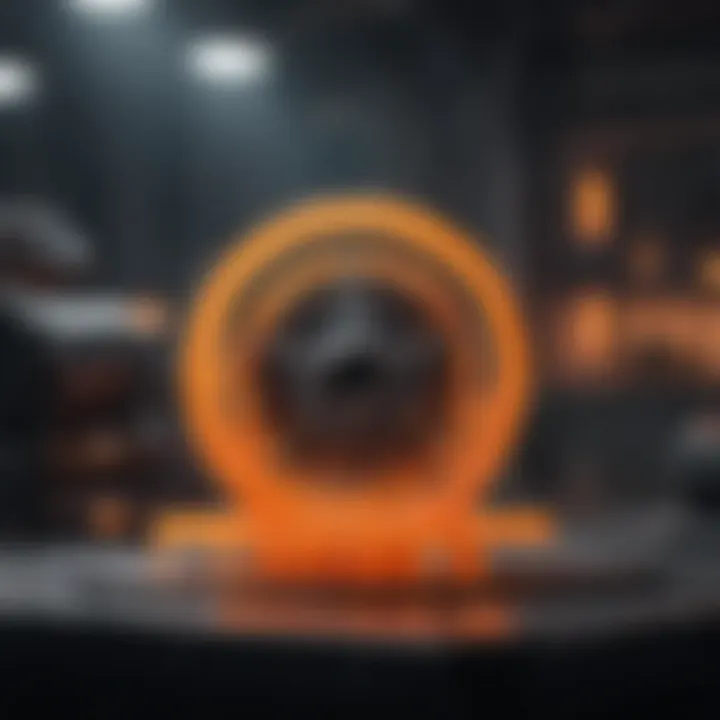
The key characteristic here is efficiency. Regulating humidity can prevent failures caused by improper material conditions. This method is popular for those in regions with fluctuating climates.
A notable feature is the introduction of hygrometers to monitor conditions. Though they may require additional attention, the advantages of reliably high-quality prints are substantial.
Software Solutions
Selecting the Right Slicing Software
Selecting the right slicing software is essential for achieving desired printing results. The choice of software directly affects how models are translated into instructions for the printer. Different programs have unique features that can either mitigate or exacerbate issues.
The key characteristic of this aspect is its direct influence on print accuracy. Choosing compatible software is beneficial, as it can optimize settings for various materials and printers. Users can expect fewer failures with the right program.
A unique feature is the adaptability of slicing software. Options range from beginner-friendly interfaces to advanced settings for experts. Understanding how to navigate these features can greatly enhance a user's printing capabilities.
Model Repair and Preparation Tools
Model repair and preparation tools are critical for ensuring files are ready for printing. These tools identify and fix issues that may cause failures during the printing process. Correctly preparing models can prevent many common printing errors.
The key characteristic of these tools is their preventive nature. Users can analyze models before printing to identify potential flaws. This is beneficial as it saves time and resources by avoiding failed prints.
A unique feature is the variety of tools available, each suited for specific issues like geometry errors or non-manifold edges. While learning to use these tools can take time, the resultant decrease in print failures makes them valuable tools in any 3D printing workflow.
Case Studies of 3D Printing Failures
Case studies provide valuable insights into 3D printing failures by examining real-world situations where issues have arisen. These examples highlight specific challenges faced in the field and demonstrate the complexity of the 3D printing process. Understanding these failures in various contexts enhances the ability to prevent similar issues in the future. It allows individuals in industry and academia to glean lessons learned, improve procedures, and benefit from the failures of others. Moreover, case studies encourage a systemic approach to troubleshooting, focusing on not only the issues but also the solutions that were developed in response to those challenges.
Industrial Applications
In industrial settings, 3D printing is often applied in production lines and prototyping, emphasizing the need for reliability. Failures in this context can lead to significant financial losses and delays in product delivery.
For instance, consider a case from Boeing that illustrates how material inconsistencies led to failed parts in aircraft manufacturing. Despite rigorous testing procedures, some parts did not meet quality standards due to flaws that were not detected during the printing process. The solution involved a comprehensive review of the printing process and material selection, prompted a shift towards more stringent quality checks before production, ultimately saving time and resources.
Another example is from automotive company Ford who faced issues related to layer adhesion in prototypes. The team used insights from the failure to redesign their printer settings and improve the drying and storage processes of their filament. As a result, they saw an increase in print quality and a decrease in failures, showcasing how analyzing failures can lead to immediate and beneficial changes.
Academic Projects
Academic projects frequently rely on 3D printing for research and experimentation. Failures in this setting can be costly, both in terms of wasted materials and time. One notable case is that of a university research group that aimed to create a bio-printed organ model. They encountered issues with the precision of the layers, causing their models to be structurally weak. After investigating the causes, the team discovered that their slicing software settings were misconfigured; thus, they adjusted the print thickness and speed parameters, which dramatically improved print integrity.
Another university project explored 3D printing technology in art. Artists attempting to use this technology faced challenges with detail accuracy. A failure in one project led the group to develop a new method of integrating traditional artistic practices with 3D print methods, enhancing the final outcomes of their work. This cross-disciplinary approach demonstrated how failures can serve as pivot points for innovation and creativity.
Both industrial and academic examples emphasize how understanding failures is not merely about rectifying mistakes. It is about cultivating a proactive mindset that transforms setbacks into opportunities for learning and development.
Future of 3D Printing and Failure Prevention
The future of 3D printing holds significant potential, particularly in combating failures that hinder efficiency and quality. Understanding how emerging trends and technologies can reshape the landscape is crucial. As 3D printing continues to evolve, attention to preventive strategies is essential. By fostering innovative solutions and adopting proactive measures, stakeholders can enhance the reliability of 3D printing processes. This section will address key components that contribute to the effective prevention of printing failures.
Emerging Technologies
Emerging technologies are at the forefront of addressing 3D printing failures. One noteworthy example is the integration of artificial intelligence in the design and manufacturing processes. AI can analyze data from previous prints, identifying failure patterns and suggesting adjustments. This predictive capability can drastically reduce the likelihood of similar errors occurring in future prints.
Another seminal technology is the advancement of multi-material printers. These printers enable the use of different types of filaments in a single project, which can produced complex geometries with varying properties. This flexibility allows for better optimization of material properties during the printing process, thus improving overall durability and print quality.
3D scanning technology also plays a critical role. By scanning printed objects for defects or inaccuracies during the printing process, adjustments can be made in real time. This diminishes wasted time and resource that otherwise occur when a print fails and has to be restarted.
Finally, automation is making strides in increasing the consistency of prints. Automated calibration systems can modify printer settings to adapt to environmental changes, ensuring that each print remains within the ideal parameters. The overall reliability of 3D printing will improve as these technologies develop.
Trends in Material Science
Material science has a direct impact on 3D printing effectiveness and longevity. The following trends are critical:
- Biocompatible Materials: In medical applications, there is a rising trend towards biocompatible materials that can function safely within the human body. These materials need to be reliable over time, ensuring less chances for failure in implantation.
- Recyclable Filaments: Sustainability is taking precedence in materials development. Filaments that can be recycled help reduce costs while minimizing waste. Innovations in these areas can promote the availability of high-quality materials at reduced prices.
- Enhanced Composite Materials: Creating composite materials with improved strength-to-weight ratios opens possibilities for various industries, from aerospace to automotive.
- Smart Materials: Materials that adapt to environmental stimuli are gaining traction. These smart materials can change properties during or after printing, which may lead to improved functionality.
Understanding these trends allows 3D printing users to make informed choices about the materials they use, potentially reducing failures.
Epilogue
In summarizing the complexities of 3D printing failures, it becomes evident that understanding these issues is crucial for anyone working in this realm. The article provides a comprehensive exploration of various factors that contribute to failures. Recognizing the distinctions between mechanical issues, filament problems, environmental factors, and software errors serves as a foundation for developing effective strategies to mitigate these setbacks.
An important element to highlight is the value of preventive measures. By implementing regular maintenance protocols and improving material handling, practitioners can significantly lower the risk of encountering failures. Not only does this save resources and time, but it also enhances the overall quality of prints. Furthermore, an awareness of how environmental conditions, like humidity and temperature fluctuations, impacts printing outcomes is equally vital.
It is also beneficial to consider the importance of education and awareness in this field. Users, whether students or professionals, need to be well-versed in troubleshooting and rectifying failures. This article presents a synthesis of practical tips and methodologies, ensuring that readers gain not just knowledge, but also actionable insights.