Understanding Ferrosilicon: Composition and Impact
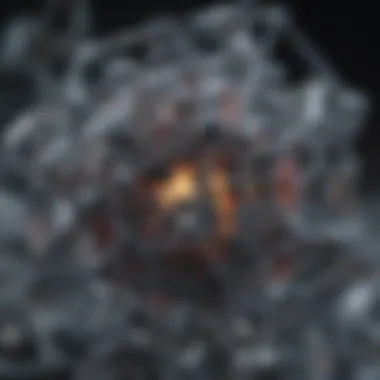
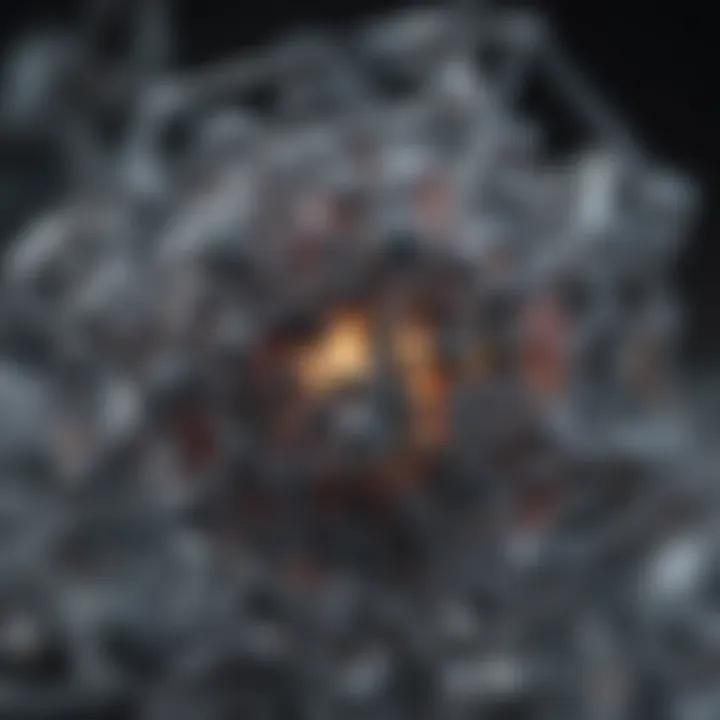
Intro
Ferrosilicon plays a significant role across multiple industries, particularly in metallurgy. As an iron-silicon alloy, it is integral to the production of steel and cast iron. Understanding its composition, applications, and environmental impacts is crucial for professionals engaging in materials science and engineering.
The physical and chemical properties of ferrosilicon determine its functionality in various processes. These properties include its melting point, density, and reaction behavior, factors that influence how it is utilized in different settings. The versatility of ferrosilicon makes it valuable in making high-quality steel, where it acts as a deoxidizer and an alloying agent.
This article aims to provide an in-depth analysis of ferrosilicon, taking a look at its vital role in the industrial sector and its implications for both users and the environment.
Prelims to Ferrosilicon
Ferrosilicon is a critical alloy that plays a significant role in various industrial applications. It is primarily composed of iron and silicon, with the percentages of these elements varying based on its intended use. Understanding ferrosilicon goes beyond just its composition; it involves exploring its properties, production methods, and applications across different sectors. In metallurgy, ferrosilicon is indispensable for improving the quality of iron and steel, thus enhancing overall material performance. Beyond metallurgy, ferrosilicon finds utility in welding, casting, and the production of silicon alloys.
In this article, we will provide a comprehensive overview of ferrosilicon. We will discuss its chemical composition, production methods, diverse applications, impacts on material properties, and environmental considerations. By examining these key aspects, we aim to offer insights valuable to students, researchers, educators, and professionals in the field of materials science and engineering.
Definition of Ferrosilicon
Ferrosilicon is an alloy made primarily of iron and silicon. It typically contains between 15% and 90% silicon. This variability allows it to be tailored for specific applications. The silicon content enhances the properties of steel and cast iron, improving strength and resistance to oxidation. Ferrosilicon also acts as a deoxidizer, removing impurities during the steelmaking process. It is marketed in several grades, with each grade designed for specific industrial purposes.
Historical Context
The history of ferrosilicon dates back to the late 19th century. Its production became more systematic with the advent of electric arc furnaces around the 1900s. Initially, it was seen merely as a byproduct of silicon production in the iron industry. However, as the demand for high-quality steel increased during the industrial revolution, ferrosilicon gained importance. Modern advancements in metallurgy and materials science have further elevated its role, leading to innovations in various production methods and applications. Today, ferrosilicon is a staple in the global metallurgical industry, contributing to improved material performance and durability.
Chemical Composition and Properties
The chemical composition and properties of ferrosilicon are vital in determining its utility across various industrial sectors. Understanding these elements allows professionals to tailor its application effectively, enhancing material performance, safety, and sustainability. This section delves into the elemental, physical, and chemical composition of ferrosilicon, spotlighting their significance to both production processes and end users.
Elemental Composition
Ferrosilicon is primarily composed of iron and silicon, with the silicon content typically varying from 15%-90% depending on the specific type. The rest of the composition is predominantly iron, with trace elements such as manganese, aluminum, and calcium often present. These additional elements can influence the overall performance of ferrosilicon in various applications. For instance, higher silicon contents can improve strength and resistance to oxidation, making ferrosilicon particularly useful in metallurgy.
"The balance of elements in ferrosilicon directly affects its performance in steelmaking and foundry applications."
In metallurgy, ferrosilicon serves as a reducing agent and a source of silicon, which is essential for improving the mechanical properties of the resulting alloys. The specific ratio of iron to silicon can also modify the melting points and fluidity during the casting processes, making it crucial for industries to choose the appropriate grade of ferrosilicon for their specific needs.
Physical Properties
The physical properties of ferrosilicon play a critical role in its applicability in various sectors. Noteworthy properties include:
- Density: Typically ranges between 6.5 and 7.5 g/cm³.
- Melting Point: Generally falls between 1200 and 1400 °C, depending on its specific grade.
- Solubility: In general, ferrosilicon is insoluble in water, which is essential for its stability in metalworking processes.
These physical characteristics make ferrosilicon a versatile material. Its density, for instance, allows it to settle effectively during smelting and refining processes, leading to a more homogeneous final product. The melting point is also significant, as it ensures that ferrosilicon can withstand high temperatures without degrading during the production of various alloys, particularly those used in the automotive and construction industries.
Chemical Properties
The chemical properties of ferrosilicon include its reactivity and interactions with other materials during metallurgical processes. Key chemical attributes are:
- Reducing Agent: Ferrosilicon acts as a strong reducing agent in the production of silicon metal and ferrosilicon alloys. This is crucial in several chemical reactions during metal processing.
- Oxidation Resistance: The presence of silicon in ferrosilicon enhances its oxidation resistance, thus prolonging the lifespan of both the material itself and the metals it interacts with.
- Compatibility: It is generally compatible with other alloying elements, such as manganese and nickel, allowing for the creation of specialized alloys with enhanced properties.
Understanding these chemical traits is essential for practitioners in metallurgy and materials science. It helps in optimizing processes and choosing the right alloys for specific applications, thus maximizing efficiency and performance in manufacturing scenarios.
Production Methods
The production methods of ferrosilicon are pivotal. They shape not only the quality of the alloy but also influence its applications across various industries. Understanding these methods helps in recognizing the intricacies involved in achieving a desired blend of iron and silicon. It involves selecting appropriate raw materials, detailed smelting processes, and maintaining stringent quality control measures. Each of these elements play a significant role in the overall efficiency of ferrosilicon production.
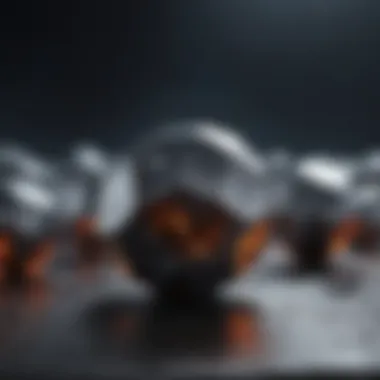

Raw Materials Required
To produce ferrosilicon, specific raw materials are essential. The primary materials needed include:
- Silica: This is a silicon dioxide, which is a crucial component in forming ferrosilicon. A high-quality silica boosts the efficiency of the smelting process and enhances the alloy properties.
- Iron Ore: The quality of iron ore affects the overall composition of ferrosilicon. It is vital to choose iron ore with low impurities to ensure a purer final product.
- Reducing Agents: Carbon, usually in the form of coke, serves as a important reducing agent. It reacts with silica and iron ore during the reduction phase, enabling the extraction of silicon.
The careful selection of these raw materials is critical. Each material contributes distinct properties to ferrosilicon and helps in gauging its suitability for various applications.
Smelting Process
The smelting process represents the heart of ferrosilicon production. Typically conducted in an electric arc furnace, this process involves several steps:
- Charging: Raw materials are mixed and loaded into the furnace. The ratio of materials impacts the silicon content in the final product.
- Electrode Insertion: Graphite electrodes are inserted into the furnace. Electricity flowing through these electrodes generates heat.
- Melting and Reduction: As the temperature increases, silica and iron ore melt. The carbon from the reducing agent reacts with the silica and reduces it to silicon.
- Formation: The molten material then solidifies into ferrosilicon, which can be further processed.
The quality of the smelting process is essential as it determines the purity levels of silicon and iron in the end product.
Quality Control Measures
Quality control in ferrosilicon production cannot be underestimated. It involves a series of measures to ensure that the alloy meets specific standards:
- Material Inspection: Before production, raw materials undergo thorough inspection to check for impurities. Any imperfections could lead to a substandard product.
- Process Monitoring: Continuous monitoring during the smelting process is crucial. It ensures that temperatures remain stable and materials are processed correctly.
- Testing Final Product: Once the ferrosilicon is produced, it is subjected to various tests. These may include physical and chemical tests to check composition and strength.
Implementing these quality measures ensures that the ferrosilicon produced is reliable, effective and meets industry standards. This is important for manufacturers who depend on ferrosilicon for various applications, ensuring customer satisfaction and regulatory compliance.
Applications of Ferrosilicon
The applications of ferrosilicon are crucial in various fields. It is extensively used in metallurgy, welding, and casting processes. This section highlights the importance of ferrosilicon's diverse roles in industrial applications and its contributions to material properties.
In Metallurgy
Ferrosilicon is an essential component in metallurgy. It is often added to iron and steel to enhance various properties. The silicon content in ferrosilicon acts as a deoxidizer. This helps to remove oxygen from molten metal, leading to improved quality in the final product.
Additionally, ferrosilicon contributes to the mechanical strength of steel. This is vital for applications where durability is paramount. High silicate levels can increase toughness. In many cases, ferrosilicon is also used in the production of cast iron, providing filtration abilities during the casting process, which results in smoother surfaces.
Some key points about ferrosilicon in metallurgy:
- Improves strength and toughness of steel.
- Acts as a deoxidizer for better quality iron and steel.
- Enhances casting processes to reduce defects.
Welding and Casting
Ferrosilicon plays an important role in welding and casting applications. In welding, it is used as an additive to improve the quality of the weld. The addition of ferrosilicon helps reduce the formation of cracks. It offers better arc stability, allowing smoother operations.
In casting, ferrosilicon is key as a nodulizing agent. It helps convert graphite flakes in cast iron to nodular shapes, which improves ductility. This modification leads to better performance in various applications. Also, ferrosilicon powders can be used in metal coatings to enhance wear resistance.
Benefits in welding and casting include:
- Improved weld quality with reduced cracking.
- Enhances ductility and performance in cast iron products.
- Increases wear resistance in coatings.
In the Production of Silicon Alloys
Ferrosilicon is instrumental in producing silicon alloys. These alloys have various applications in different industries. The primary use is in making aluminum-silicon alloys, which are critical in automotive and aeronautics. The presence of ferrosilicon significantly improves the alloy's mechanical properties and castability.
Moreover, ferrosilicon is used in the production of silicon carbide, a material known for its hardness. This is valuable in abrasives and cutting tools. The ability of ferrosilicon to influence the microstructure of alloys is vital as it allows tailored properties for specific applications.

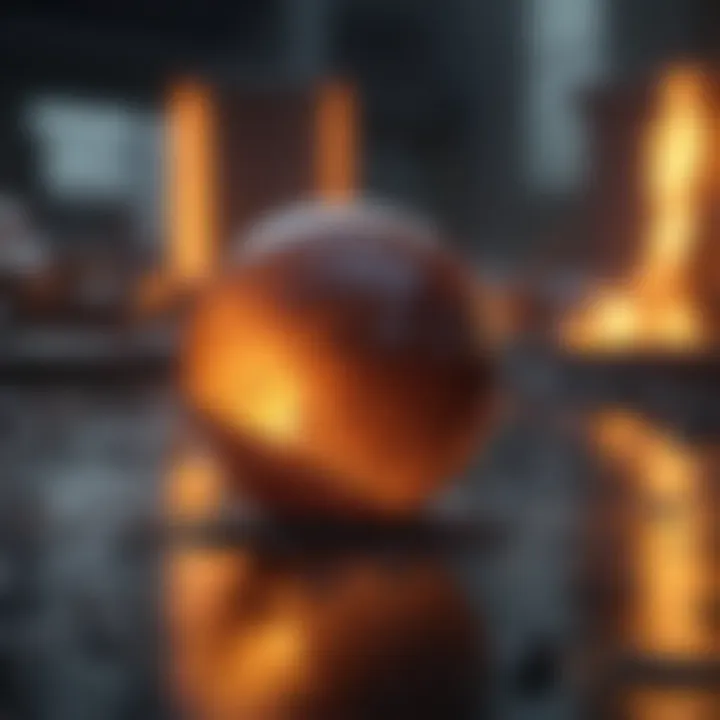
In summary, the role of ferrosilicon in silicon alloy production includes:
- Critical for making aluminum-silicon alloys.
- Enhances mechanical properties for specific uses.
- Key ingredient for silicon carbide used in cutting tools and abrasives.
This versatility makes ferrosilicon an indispensable material in modern manufacturing processes.
Impact on Material Properties
In the world of materials science, understanding the impact of elements like ferrosilicon on material properties is vital. Ferrosilicon not only serves as a crucial ingredient in metallurgy but also significantly alters the characteristics of the metals with which it is alloyed. This section will focus on three critical aspects: mechanical strength enhancement, corrosion resistance, and thermal conductivity. Each of these properties will reflect how ferrosilicon allows materials to perform better in various industrial applications.
Mechanical Strength Enhancement
Ferrosilicon is well-known for its role in enhancing the mechanical strength of iron and steel. When added to molten iron during casting, it modifies the microstructure of the metal. This modification improves tensile strength, yield strength, and hardness.
- Tensile Strength: Ferrosilicon increases the resistance of the metal to being pulled apart. This is because it refines the grain structure of the iron.
- Yield Strength: It helps the material withstand higher loads without deforming, crucial for construction and manufacturing.
- Hardness: The presence of silicon allows the alloy to resist deformation under pressure, making it suitable for tools and machinery.
The enhanced mechanical properties mean that parts made from ferrosilicon alloys can often be thinner yet stronger, leading to reduced material use and lower costs in manufacturing.
Corrosion Resistance
Another significant benefit of using ferrosilicon is its ability to improve corrosion resistance in treated metals. This is essential for products that will face harsh environments. Here are some key points:
- Formation of Protective Layers: Silicon contributes to the formation of protective oxide layers on metal surfaces, which prevents oxidation. This is particularly valuable in exposed outdoor applications.
- Reduced Rust Formation: The properties of ferrosilicon help in combating rust, allowing for greater longevity of metal structures.
- Chemical Stability: Ferrosilicon excels in various acidic and basic environments. Thus, it is widely used in industries like oil and gas.
By improving corrosion resistance, ferrosilicon aids manufacturers in producing longer-lasting products, which is a significant consideration for both economic and environmental factors.
Thermal Conductivity
The thermal conductivity of metals affects how they perform in high-temperature applications, and ferrosilicon plays a crucial role here as well. Materials with enhanced thermal conductivity can dissipate heat more effectively, leading to safer and more efficient operations. Significant points include:
- Improved Heat Dispersion: The alloy provides better heat distribution because silicon enhances the overall thermal conductivity of the metal.
- Safety in High-Temperature Applications: This is especially important in engines and machinery, where excess heat can lead to failures. Enhanced thermal conductivity lowers the risks.
- Efficient Thermal Management: Opportunities for better thermal management lead to improved performance in applications such as electric motors and transformers.
The addition of ferrosilicon to materials not only enhances their performance but also broadens the range of applications in industrial contexts, where reliability and efficiency are paramount.
"The careful selection of materials significantly influences the outcome of engineering projects, making ferrosilicon a key player in modern metallurgy."
Through its contributions in mechanical strength, corrosion resistance, and thermal conductivity, ferrosilicon proves to be indispensable in advancing material science.
Environmental Considerations
Environmental considerations are crucial to understanding ferrosilicon. As the production and utilization of ferrosilicon grow, it is paramount to assess its environmental impact. This section focuses on the production processes that influence the environment and explores recycling options, highlighting their importance toward sustainability.
Environmental Impact of Production
The production of ferrosilicon demands significant energy input, which can lead to high carbon emissions if fossil fuels are used. Pollutants released during smelting processes generally include particulate matter, sulfur dioxide, and various other greenhouse gases. This produces a ripple effect on air quality and contributes to global warming.
Several factors affect the environmental impact:
- Energy Source: Utilizing renewable energy sources can drastically reduce the carbon footprint during production.
- Waste Management: Effective waste management strategies can minimize the output of hazardous materials.
- Regulatory Compliance: Companies that adhere to environmental regulations and standards tend to have lesser impacts than those that don’t.
Effects of poor production practices can extend to biodiversity loss and contamination of local water streams. Therefore, a comprehensive approach to managing these factors is essential.
"The pathway to sustainable ferrosilicon production lies in improving processes and committing to environmental regulations."
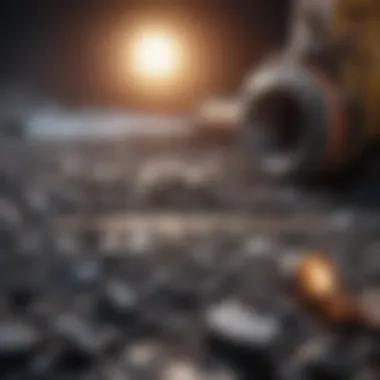
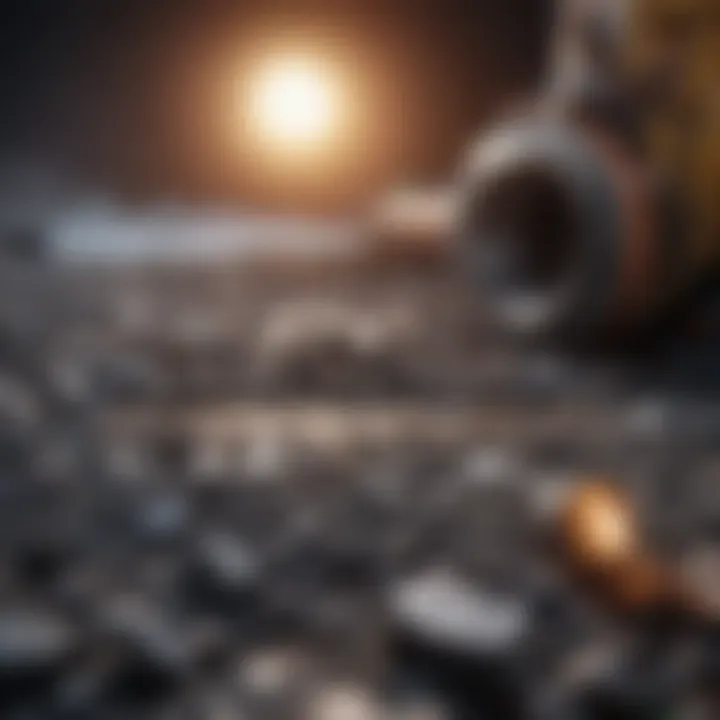
Recycling Ferrosilicon
Recycling ferrosilicon not only reduces waste but also conserves energy. The recycling process can recover ferrosilicon from scrap materials, thus decreasing the need for raw materials. This contributes to a circular economy where material reuse minimizes environmental degradation.
Benefits of recycling ferrosilicon include:
- Resource Conservation: Reduces dependence on mining activities, which can be destructive to the environment.
- Energy Savings: Recycling typically uses less energy than producing new ferrosilicon, making it more sustainable.
- Pollution Reduction: Fewer emissions result from recycling compared to new production processes.
Efforts to enhance recycling should focus on innovations in collection and processing technologies. Establishing a more robust infrastructure for recycling ferrosilicon can foster a greener industry.
In summary, understanding the environmental considerations surrounding ferrosilicon is essential. This includes evaluating production impacts and embracing recycling methodologies. Both avenues present opportunities for mitigating environmental harm while promoting sustainable practices.
Market Dynamics
Understanding the market dynamics of ferrosilicon is crucial for players in the metallurgy and material science fields. This section provides insight into global demand trends and identifies primary producers. Knowing the ebbs and flows of market dynamics enables stakeholders to adapt strategies, optimize production methods, and meet future challenges effectively.
Global Demand Trends
The demand for ferrosilicon has been strongly linked to several factors, including economic growth, particularly in developing countries. As industries expand, the need for high-quality steel increases, driving up the demand for ferrosilicon. The construction, automotive, and manufacturing sectors are the primary consumers.
- Steel Manufacturing: Ferrosilicon is vital in steel production, utilized as a deoxidizer and an alloying agent. The more steel is produced, the more ferrosilicon is required.
- Welding: As infrastructures develop globally, the demand in welding applications also rises. Ferrosilicon enhances the welding process, which again feeds back into industrial needs for ferrosilicon.
- Economic Indicators: Regional economic indicators such as GDP growth or infrastructure investment are predictive of ferrosilicon demand. Stronger economies often lead to increased consumption.
According to recent analyses, the compound annual growth rate (CAGR) for ferrosilicon is expected to be notable as the steel market continues to grow, especially in Asia.
Primary Producers
The landscape of ferrosilicon production reflects a few key players that dominate the market. These producers not only satisfy current demand but often drive innovation and pricing strategies.
- China: As the leading producer, China accounts for a significant portion of the global ferrosilicon production. Its advances in production technology and mass manufacturing capabilities provide competitive pricing.
- Brazil: The country stands out as a top producer, leveraging its abundant natural resources to maintain a strong position in ferrosilicon production. Brazil’s ferrosilicon is highly sought for its quality.
- Russia: With a focus on export markets, Russia's production also contributes significantly to global supply chains. Russian ferrosilicon is known for high purity, making it valuable in metallurgical applications.
- Norway: Known for sustainability practices, Norway utilizes hydroelectric power in its production, appealing to environmentally conscious buyers.
Overall, understanding the key producers and demand trends highlights the interconnectedness of various sectors and the importance of ferrosilicon in industrial applications. The global market for ferrosilicon reflects larger industrial trends, making it essential for stakeholders to closely monitor these dynamics.
Future Prospects
The future of ferrosilicon is set against a backdrop of evolving industrial demands and environmental considerations. With its crucial role in metallurgy and the production of iron and steel, understanding the prospects of this alloy involves looking at technological innovations and sustainability initiatives. These elements are not only important for the current industrial landscape but also for shaping a more responsible use of resources in the coming decades.
Technological Innovations
Technological advancements are transforming the way ferrosilicon is produced and utilized. Innovative smelting techniques have emerged to enhance efficiency and reduce emissions. For instance, the use of electric arc furnaces optimizes energy consumption and minimizes the carbon footprint associated with ferrosilicon production. The integration of automation and AI in manufacturing processes is another significant trend. These technologies facilitate better quality control and increase production rates while ensuring the consistency of the alloy's properties.
Recent developments also focus on producing high-purity ferrosilicon. This is particularly essential for specialized applications in electronics and advanced materials. Technologies that enable precision refining and alloy customization are likely to advance ferrosilicon's role in sectors demanding higher performance materials.
Sustainability Initiatives
As the global focus shifts towards sustainability, ferrosilicon production faces new challenges and opportunities. One significant area of sustainability initiatives involves improving the recycling processes. The recycling of ferrosilicon is vital in reducing waste and conserving raw materials. Continuous research is being done to explore effective ways to recycle ferrosilicon from obsolete electronic devices and from post-consumer steel products, thereby closing the loop on lifecycles.
Moreover, leading producers are adopting cleaner production methods, such as utilizing renewable energy sources. Shifting to solar or wind energy can drastically decrease the carbon emissions associated with traditional smelting processes. The emphasis on corporate social responsibility is pressuring companies to invest in greener technologies.
"The integration of sustainable practices in ferrosilicon production could reshape its market appeal and reputation in the coming years."
As manufacturers prioritize sustainability, collaboration across the supply chain will also increase. This includes sharing best practices, technologies, and innovations aimed to enhance the overall environmental footprint of ferrosilicon.
Epilogue
The conclusion of this article serves as a crucial element for summarizing the extensive discussions held regarding ferrosilicon. It brings together the various aspects explored, including its composition, applications, environmental implications, and future trends. Recognizing the multifaceted role of ferrosilicon is essential for students, researchers, educators, and industry professionals alike. It not only highlights the alloy's importance in metallurgy and production processes but also emphasizes the necessity for sustainable practices in its production and use.
Summary of Key Points
- Ferrosilicon is an alloy of iron and silicon, with key importance in metallurgy and associated industries.
- Its unique composition enhances mechanical properties, making it valuable for steel production and other applications.
- The production methods for ferrosilicon involve raw material acquisition, smelting, and strict quality control measures.
- Environmental considerations are paramount, as the production processes have significant impacts on ecosystems, prompting a need for recycling and sustainable practices.
- Technological innovations aim toward improving efficiency in production, while sustainability initiatives influence future trends in ferrosilicon usage.