Understanding Nickel-Free Alloys and Their Applications
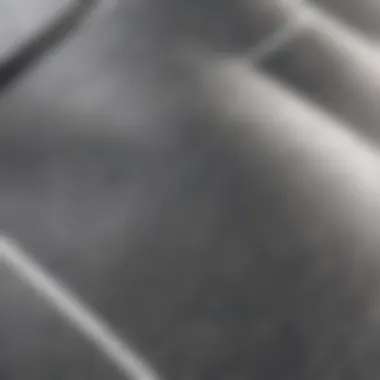
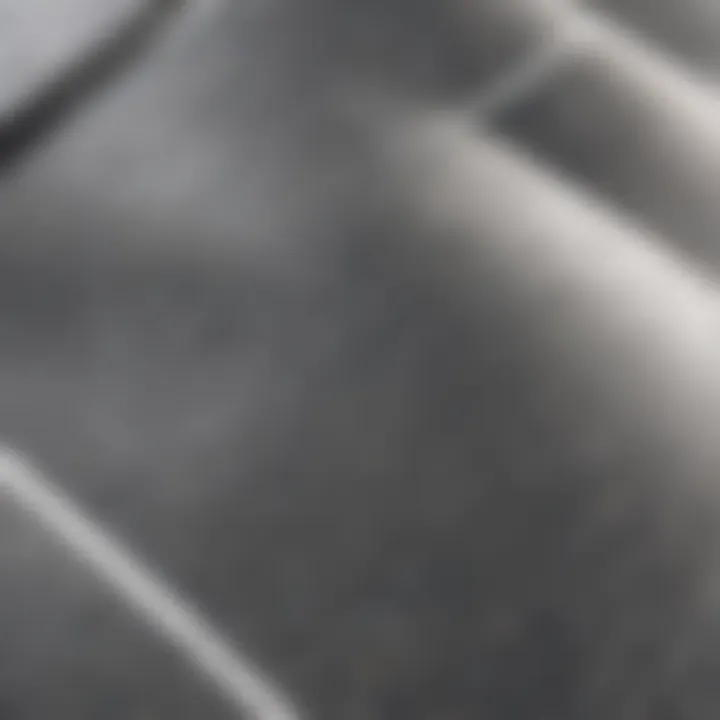
Intro
Nickel has long been a metal of choice in various industries due to its durability and resistance to corrosion. However, growing concerns over its health implications have spurred interest in alternatives. Nickel can cause allergic reactions in some individuals, leading to discomfort and health issues. Consequently, nickel-free alloys are emerging as a favorable option across multiple sectors. This trend signifies a broader shift towards safety and sustainability in manufacturing.
Understanding nickel-free alloys requires examining their properties, advantages, and applications. Research indicates that these materials offer comparable performance without the health risks associated with nickel. This article aims to provide thorough insights into nickel-free alloys and highlight their relevance in today’s technological landscape.
Research Overview
Summary of Key Findings
Nickel-free alloys usually consist of elements that offer similar mechanical properties. Their resistance to oxidation and corrosion can match or even exceed that of nickel-containing alloys. The main findings from various studies suggest that alloys such as titanium, zirconium, and certain steel compositions exhibit favorable characteristics in specific applications. Notably, these alternatives often show enhanced compatibility in medical implants, reducing allergic responses among patients.
Importance of the Research
The significance of researching nickel-free alloys lies in their potential to improve both human health and environmental sustainability. As industries pivot towards safer materials, understanding these alternatives becomes timely. Knowledge of nickel-free alloys can drive innovation, encouraging the development of products that are both functional and safe.
As the landscape of materials science evolves, the importance of incorporating nickel-free options cannot be understated. Their role in advancing health safety and contributing to ecological balance makes them a focal point for future studies and applications.
Preamble to Nickel-Free Alloys
Nickel-free alloys represent a growing segment of materials in various industrial applications. Their importance lies mainly in health, performance, and sustainability properties. Traditionally, nickel has been a common component in metal alloys, enhancing their strength and corrosion resistance. However, increased awareness of nickel allergy and its potential health risks has led to a shift toward nickel-free alternatives. In this article, we will discuss how these alloys are crafted, their applications, and the implications of using them.
Definition of Nickel-Free Alloys
Nickel-free alloys are metals that do not contain nickel as part of their composition. This characteristic makes them suitable for individuals who have sensitivities or allergies to nickel, which affects a significant portion of the global population. These alloys often incorporate other metals like iron, cobalt, and titanium to achieve the desired mechanical properties while still ensuring that there is no nickel present. The absence of nickel has become a major selling point for products ranging from jewelry to medical instruments, as manufacturers seek to meet the needs of allergic consumers and regulatory standards.
Overview of Nickel in Metal Alloys
Nickel plays a crucial role in enhancing mechanical and chemical properties of alloys. Historically, it has contributed strength and improved durability when added to steel, brass, and various other metal combinations. Nickel also enhances corrosion resistance, making it an ideal choice for many applications, including kitchenware and construction materials. However, nickel is known to cause allergic reactions in some individuals. As awareness of these allergies increases, industries are exploring alternatives. The focus is now shifting to designing alloys that provide similar or superior qualities without the adverse health effects associated with nickel exposure.
The transition to nickel-free alloys supports health awareness and environmental sustainability while maintaining industrial performance.
In summary, the shift towards nickel-free alloys is not just a trend but a significant response to evolve towards safer and more sustainable manufacturing practices.
The Health Considerations of Nickel Exposure
Nickel exposure is a significant topic of concern, particularly for individuals who work in industries where nickel alloys are prevalent. Nickel is widely used in various manufacturing processes, leading to increased likelihood of exposure. This section will examine the health implications of nickel, particularly focusing on allergies and long-term effects associated with nickel exposure. Understanding these health considerations is essential, providing insight into why many industries are transitioning to nickel-free alternatives.
Nickel Allergies and Sensitivities
Nickel allergies are among the most common metal allergies. Many individuals experience skin reactions upon contact with nickel-containing products. These reactions can vary in severity, ranging from mild irritation to significant dermatitis. Symptoms may include itching, redness, and swelling, particularly in areas where the metal contacts the skin, such as in jewelry or clothing fasteners.
The rise in awareness regarding nickel allergies has led to a growing demand for nickel-free products, especially in the cosmetic and jewelry industries. Some common items known to provoke reactions include earrings, watchbands, and belt buckles. Avoiding nickel can significantly improve quality of life for those affected. In some cases, individuals may require medical intervention, such as topical corticosteroids, to alleviate symptoms.
To address concerns about nickel exposure, manufacturers are increasingly choosing alternatives. This shift not only benefits consumers with allergies but also reflects a broader commitment to health considerations in product design.
Long-Term Health Effects of Nickel Exposure
Long-term exposure to nickel has raised public health concerns. Studies suggest that continuous exposure may lead to respiratory issues, including asthma and lung disease. Nickel particles, when inhaled, can be particularly harmful to workers in manufacturing environments. For instance, those in the mining, refining, or welding industries are at higher risk.
Moreover, nickel is classified as a carcinogen by various health authorities. Chronic exposure has been linked to an increased risk of lung and nasal cancers. This potential danger highlights the importance of regulating nickel exposure in the workplace and developing safer materials, like nickel-free alloys.
Characteristics of Nickel-Free Alloys
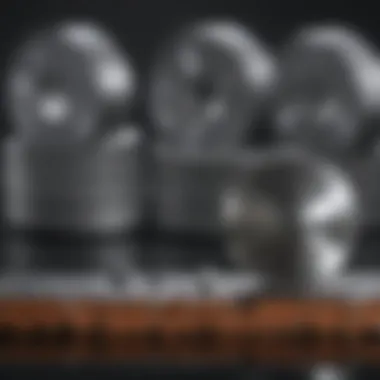
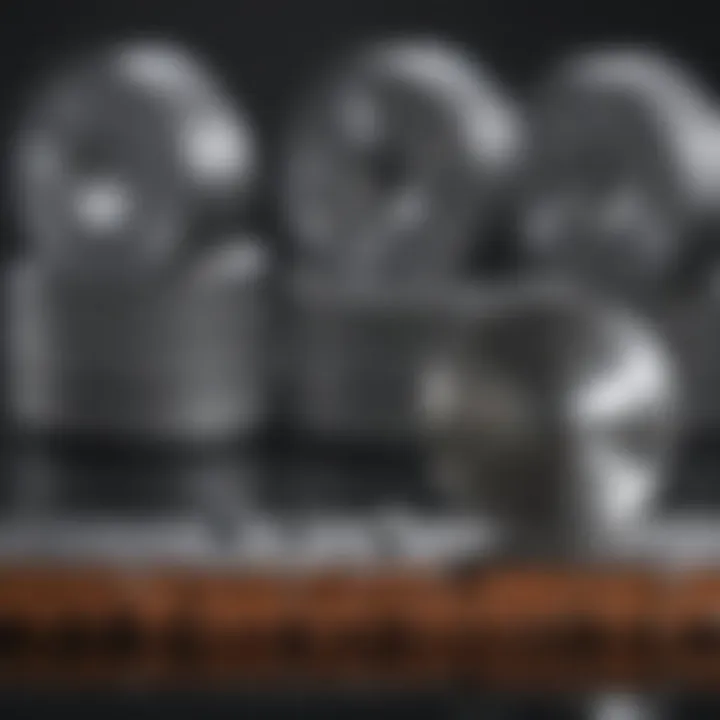
Nickel-free alloys present unique characteristics that justify their rising prominence in various fields of manufacturing and technology. Understanding these properties is crucial for making informed choices about materials in a wide range of applications. These characteristics often lead to enhanced performance, reduced health risks, and better alignment with environmental goals. There are three main areas within which the distinctive attributes of nickel-free alloys are illustrated: mechanical properties, corrosion resistance, and thermal stability.
Mechanical Properties
The mechanical properties of nickel-free alloys vary significantly depending on their specific composition. These alloys often exhibit good strength levels, which can be comparable to that of nickel-containing alternatives. Typical mechanical characteristics include yield strength, elongation, and hardness. Some nickel-free alloys use elements like titanium or cobalt, which can contribute to excellent tensile strength. For example, titanium-based alloys are known for their high strength-to-weight ratio.
Strong mechanical properties make nickel-free alloys suitable for a wide range of demanding applications, from aerospace components to medical devices.
Moreover, nickel-free alloys may show improved ductility in certain environments. This ductility, or the ability to deform under stress, is critical in applications that require complex shapes or substantial impact resistance. It is essential to assess these mechanical properties based on the specific needs of the application, as they can vary widely across different nickel-free materials.
Corrosion Resistance
Corrosion resistance is a vital characteristic of nickel-free alloys, especially in industries where exposure to harsh environments is commonplace. The absence of nickel does not inherently lead to lower resistance to corrosion. Instead, other alloying elements often enhance this property. For instance, cobalt and molybdenum can be added to improve the corrosion-resistant features significantly.
A significant advantage here is that nickel-free alloys do not undergo pitting corrosion, a common issue with materials that contain nickel. This scenario is particularly beneficial in marine and chemical processing applications, where exposure to corrosive agents poses a constant threat.
It is essential to carefully consider the specific exposure conditions and the local environment to identify the right nickel-free alloy that meets the required corrosion resistance standards. Under the right circumstances, these alloys can outperform traditional nickel-based alloys in specific applications.
Thermal Stability
Thermal stability is another key aspect that plays a critical role in the performance of nickel-free alloys. These materials often withstand high temperatures without significant degradation. Alloys such as certain titanium and cobalt blends maintain their structural integrity and performance under thermal stress, making them suitable for high-temperature applications.
This thermal stability can be particularly advantageous in settings where thermal cycling occurs frequently. For instance, in aerospace engineering, materials are subjected to fluctuating temperatures during flight, requiring that the alloys maintain their performance without losing any mechanical or structural properties.
Common Alternatives to Nickel in Alloys
Nickel is widely used in metal alloys for its strong properties, but the growing awareness of health and environmental concerns has led to increased interest in nickel-free alternatives. These alternatives are not only capable of providing similar or even superior properties, but they also offer significant benefits such as decreased risk of allergic reactions and improved sustainability. Understanding these alternatives becomes essential for industries aiming to enhance both the safety and performance of their materials.
Cobalt-Based Alloys
Cobalt-based alloys are increasingly favored as a substitute for nickel in various applications. They exhibit many advantageous characteristics, including excellent corrosion resistance and exceptional wear properties. These alloys are particularly useful in high-temperature environments, making them ideal for aerospace and automotive industries.
Cobalt-based alloys can be engineered to achieve specific mechanical properties. This means they can be tailored to suit different applications efficiently. Additionally, they are often used in medical instruments due to their biocompatibility. However, sourcing cobalt raises some ethical and environmental considerations, as its mining can pose local hazards.
Iron-Based Alloys
Iron-based alloys, frequently referred to as stainless steels, are commonly used as nickel substitutes. These alloys benefit from lower costs and are widely available. Iron-based alloys can achieve good mechanical properties and a high degree of corrosion resistance through various alloying elements like chromium and molybdenum.
These alloys find application primarily in construction, automotive, and household goods. However, it is essential to note that, depending on the specific composition, some iron-based alloys may not achieve the same level of corrosion resistance as their nickel-containing counterparts. Thus, the application must be carefully considered when choosing these materials.
Titanium and its Alloys
Titanium and its alloys present another promising alternative to nickel. Titanium boasts excellent strength-to-weight ratios and is highly resistant to corrosion. These properties make titanium-based materials suitable for a wide range of applications in industries such as aerospace, medical, and chemical processing.
The biocompatibility of titanium makes it a popular choice for implantable medical devices. However, titanium is generally more expensive than other alternatives. Its higher costs can be a limiting factor for some applications. Nevertheless, ongoing research aims to lower production costs and improve its availability, making titanium a more viable option in the future.
"Exploring alternatives to nickel alloys reveals pathways to safer and sustainable production without compromising on performance."
Selecting the appropriate nickel alternative requires a comprehensive understanding of each alloy's properties. Careful consideration of performance requirements, cost implications, and environmental impact is crucial. This analysis contributes to more informed decisions in material selection, paving the way for innovative applications.
Applications of Nickel-Free Alloys
Nickel-free alloys have become increasingly relevant in various industries due to their unique properties and health benefits. The applications of these alloys touch on several key sectors, offering advantages that address both performance and safety considerations. The significance of nickel-free alloys lies not only in their reduced allergenic properties but also in their potential for enhancing the sustainability of manufacturing processes. Adopting these materials can yield lower costs, reduce health risks, and improve product quality.
Medical Instruments and Implants
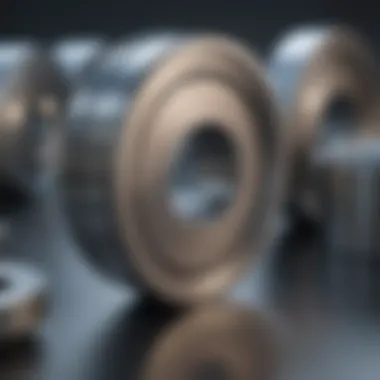
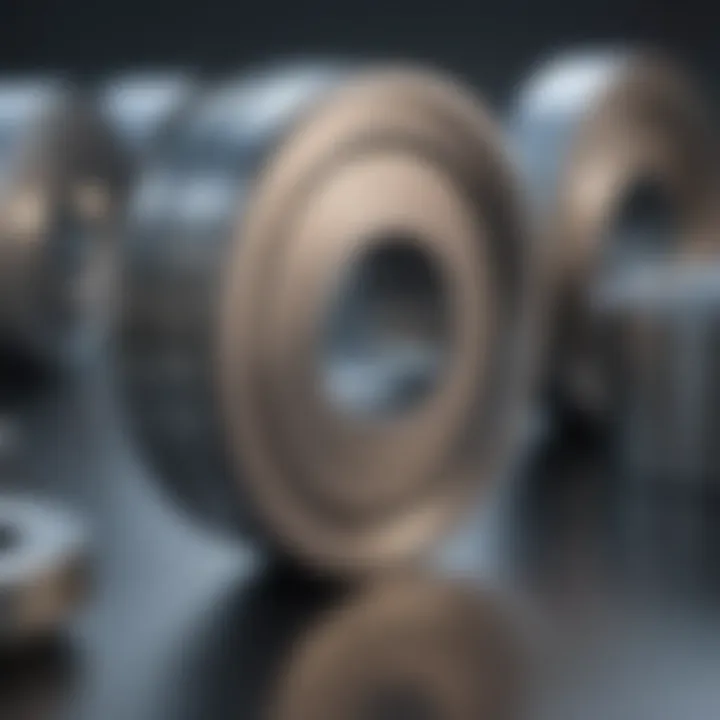
In the medical field, nickel-free alloys are crucial due to the high prevalence of nickel allergies among patients. Instruments like surgical tools and implants made from nickel-free materials significantly reduce the risk of allergic reactions. For example, titanium and cobalt-based alloys are often chosen for orthopedic implants because they are less likely to cause irritation. These materials are biocompatible, which means they do not produce adverse effects in the body.
Furthermore, nickel-free alloys possess excellent corrosion resistance, an essential property for any medical device that faces bodily fluids. Reliable performance in both surgical and long-term applications is vital. A study published in the Journal of Biomedical Materials Research discusses how titanium alloys exhibit better mechanical properties compared to nickel-containing options, solidifying their presence in modern medical technology.
Aerospace Engineering
The aerospace sector also benefits significantly from the adoption of nickel-free alloys. Components used in aircraft must endure extreme conditions, including high stress, temperature variations, and corrosive environments. Nickel-free alloys, particularly those based on titanium and aluminum, demonstrate strength and durability needed for such applications.
The lightweight characteristics of these materials contribute directly to fuel efficiency. For example, using titanium alloys in structural components can lead to weight savings without compromising strength. Many aerospace manufacturers are actively exploring nickel-free solutions due to stringent regulations on material safety and environmental impact.
Automotive Industry
The automotive industry represents another area where nickel-free alloys play a vital role. Components that require high performance and resistance to wear, like gears and bearings, can utilize these advanced materials to enhance longevity and reliability. With growing awareness around the environmental footprint of manufacturing, automakers are increasingly seeking materials that are both sustainable and effective.
Nickel-free alloys can contribute to lighter vehicle designs, aiding in fuel economy while ensuring safety and performance. Additionally, as consumers demand more environmentally friendly alternatives, nickel-free materials can give companies a competitive edge in the market. The shift towards nickel-free solutions in automotive manufacturing reflects broader trends in sustainability and health considerations, positioning the industry favorably for future growth.
"Transitioning to nickel-free alloys supports both health and performance in key industries".
Economic Impacts of Nickel-Free Production
The shift towards nickel-free alloys presents not only a health and environmental improvement but also significant economic implications. Understanding these impacts is crucial for various industries as they navigate the landscape of material options. Companies often face rising costs associated with nickel due to its fluctuating market price and environmental regulations regarding its extraction and processing. Nickel-free alternatives can offer more stable pricing and lower production costs in the long run.
Cost Analysis Compared to Nickel-Based Alloys
When analyzing costs, nickel-free alloys often emerge as competitive options. The initial investment in nickel-free production may seem higher due to research and development expenses or specialized equipment. However, companies must consider the following points:
- Raw Material Prices: Nickel can be subject to price instability influenced by global supply and demand. Nickel-free alloys usually rely on materials like iron or titanium, which may not face the same volatility.
- Production Processes: Nickel extraction and processing can be resource-intensive, incurring further costs. Nickel-free alternatives often require different manufacturing processes that can be more efficient and eco-friendly, thereby reducing operational costs.
- Maintenance and Durability: Nickel-free alloys may have better corrosion resistance, leading to longer product lifespans. This can reduce costs associated with repairs and replacements over time.
Ultimately, while the upfront costs might differ, the total cost of ownership can favor nickel-free materials in many situations.
Market Trends and Demand
Market trends illustrate a growing demand for nickel-free alloys across various sectors. Factors contributing to this trend include:
- Health Awareness: Increased consumer knowledge about nickel allergies and sensitivities is driving the demand for safer, nickel-free products.
- Sustainability Focus: Companies are increasingly prioritizing sustainable practices. Nickel-free alloys often align better with this goal, appealing to consumers who value environmentally conscious brands.
- Innovations in Materials: Ongoing research is producing advanced nickel-free alloys that maintain or even exceed the performance metrics of traditional nickel-based alloys. Industries are becoming more willing to adopt these alternatives as innovations continue to emerge.
In summary, the economic impact of transitioning to nickel-free production is profound. By closely examining costs and market dynamics, industries can make informed choices that benefit not only their bottom line but also the health of consumers and the environment.
Environmental Considerations
The focus on environmental considerations within the context of nickel-free alloys is essential as global manufacturing practices evolve. The shift towards sustainability in various industries is crucial for reducing environmental footprints. Nickel mining and processing pose significant ecological challenges. These include habitat destruction, water pollution, and high energy consumption. Thus, adopting nickel-free materials contributes to a more sustainable approach in manufacturing.
Sustainability of Nickel-Free Materials
Nickel-free alloys are increasingly recognized for their sustainable properties. These materials often utilize abundant and less harmful raw materials. For instance, alloys such as cobalt-based or titanium-based substitutes present fewer environmental issues in terms of extraction and processing. Moreover, nickel-free alloys tend to have a longer service life. They can withstand corrosive environments, resulting in reduced waste over time.
- Lower Emissions: The production processes for nickel-free alloys generally produce lower carbon emissions compared to traditional nickel-containing alloys.
- Resource Efficiency: Many nickel-free alloys allow for recycling and reuse, ensuring resource efficiency. This minimizes the demand for virgin materials which, in turn, alleviates environmental burden.
- Regulatory Compliance: Many manufacturers are subject to increasing regulations that favor or mandate the use of sustainable materials. Nickel-free alloys align well with these regulations, ensuring compliance and reducing potential liabilities.
Lifecycle Analysis of Nickel-Free Alloys
Conducting a lifecycle analysis provides insights into the environmental impact of nickel-free alloys from production to disposal. This analysis assesses the total environmental costs incurred throughout various stages.
- Raw Material Extraction: Many nickel-free alloys are derived from materials that require less intensive extraction methods, leading to less soil degradation and reduced energy usage.
- Production Stage: The manufacturing of these alloys can demand lower energy inputs and consequently lower greenhouse gas emissions. Many methods used for nickel-free alloys also focus on reducing waste.
- Service Life: The durability and corrosion resistance of nickel-free alloys mean a longer lifecycle before being retired from service. This reduces the frequency of replacements and the overall demand for additional resources.
- End-of-Life Management: With better recycling capabilities, nickel-free alloys can reduce the burden on landfills. Their constituents are often more compatible with current recycling technologies, enhancing circular economy practices.
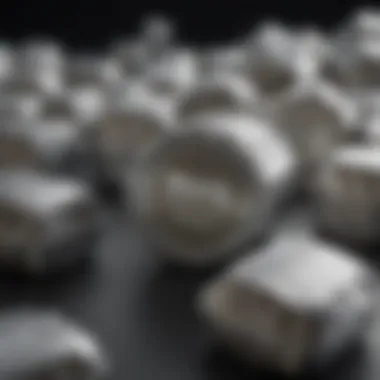
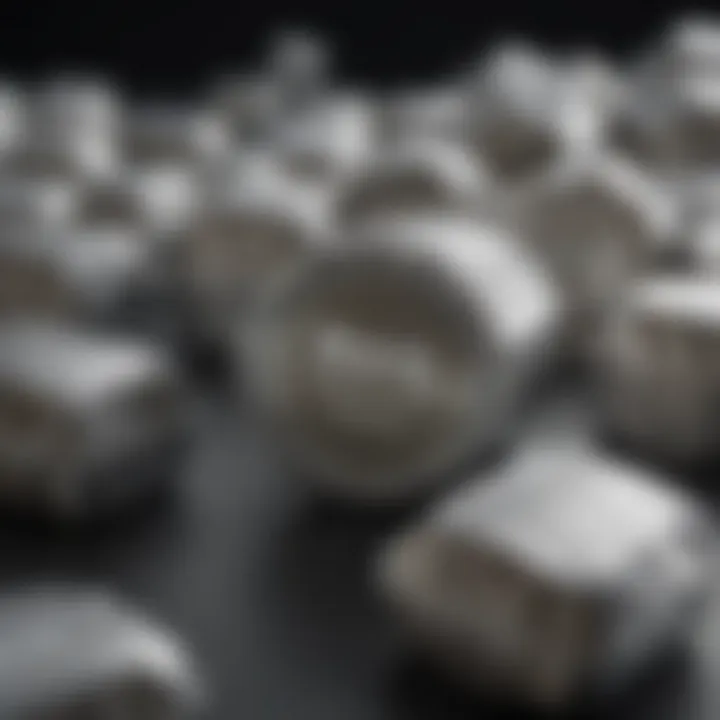
A lifecycle analysis highlights that switching to nickel-free alloys can significantly mitigate environmental impacts when compared to traditional nickel-containing alternatives.
Challenges in Adopting Nickel-Free Alloys
The adoption of nickel-free alloys in various industries presents several challenges that merit careful consideration. Understanding these challenges helps to illuminate the broader implications of transitioning away from nickel-containing materials. The hurdles range from technical issues in manufacturing to limitations in performance when compared to traditional nickel-based alloys.
Manufacturing Processes
The manufacturing of nickel-free alloys involves unique processes that can differ significantly from those employed for nickel-based counterparts. One primary challenge is the need for specialized equipment and techniques. Many nickel-free alloys require precise control of temperature and atmosphere during production. This enhances the integrity and performance of the alloys but may lead to increased costs and time delays. Additionally, existing facilities often need upgrades or modifications to handle these new materials effectively.
These adjustments are not trivial. For example, facilities that primarily use stainless steels with nickel may have limited experience with cobalt or titanium-based alloys. This might result in a steep learning curve, requiring training and adjustments in workflow. Furthermore, sourcing raw materials for nickel-free alloys can sometimes present difficulties. Not all suppliers may carry these materials, and logistics can become tricky.
Performance Limitations
While nickel-free alloys come with many benefits, they also exhibit performance limitations that industries must address. For instance, many alternatives, such as cobalt or titanium-based alloys, can display different mechanical properties compared to traditional nickel alloys. This can affect their suitability for some applications where specific strength or ductility is necessary.
Users may find that while nickel-free alloys offer enhanced corrosion resistance, they could fall short in other areas, such as high-temperature stability. Research indicates that, in extreme environments, some nickel-free materials may not perform as well as their nickel-containing counterparts. As a result, careful evaluation is necessary to ensure that these materials meet the demands of the intended application.
Future Directions in Alloy Development
The development of nickel-free alloys is an evolving field. The growing demand for safer materials that do not trigger health issues has pushed researchers to focus on innovative solutions. These advancements aim to improve the performance and functionality of alloys in various applications.
Innovations in Nickel-Free Technology
Recent innovations in nickel-free technology demonstrate promising improvements in material properties. One such area is the enhancement of corrosion resistance. Researchers are exploring coatings and surface treatments that can prolong the life of nickel-free alloys in harsh environments.
Another significant innovation is in the area of additive manufacturing. 3D printing technology allows for more complex designs and can enable the production of lightweight components using nickel-free materials. This is particularly beneficial in aerospace and automotive sectors where weight reduction is crucial.
Moreover, the introduction of new alloy compositions is a vital area of focus. For example, advancements in cobalt and titanium-based alloys have shown potential for high-temperature applications while maintaining structural integrity. These new formulations could provide alternatives that meet or exceed the performance characteristics of traditional nickel-based alloys.
Research Opportunities
The exploration of nickel-free alloys opens up various research avenues for scholars and industry professionals. There is a need for studies aimed at optimizing the properties of these materials through experimental and computational methods.
Research can also investigate the long-term durability of nickel-free alloys in real-world applications. Understanding how environmental factors affect their performance will be crucial for adoption in critical sectors such as medical implants. The lifecycle analysis of these materials could lead to the identification of more sustainable practices throughout the manufacturing process.
Furthermore, collaborative efforts between academia and industry can lead to breakthroughs in understanding the limitations of existing nickel-free alloys. Areas like alloy fatigue, wear resistance, and thermal stability warrant in-depth examination to drive further advancements.
Engaging in cross-disciplinary research that incorporates materials science, chemistry, and engineering principles is essential. This collaborative approach will enhance innovation, ultimately leading to the development of next-generation nickel-free alloys that can be integrated into a broad range of applications.
"The future of nickel-free alloys lies in the willingness to innovate and collaborate across disciplines, harnessing the combined expertise to revolutionize the materials landscape."
In summary, the future directions in alloy development are promising. Through innovations in technology and a proactive research approach, nickel-free alloys could reshape industries and provide benefits that extend well beyond health considerations.
Closure
The importance of this topic cannot be understated. As industries move towards safer and more sustainable practices, nickel-free alloys provide a compelling alternative. The benefits include not only enhanced safety for individuals sensitive to nickel but also an improvement in environmental outcomes. Nickel-free alloys are less likely to leach harmful substances and can offer media-friendly properties that are crucial in sensitive applications such as medicine and aerospace.
Summary of Key Points
- Health Benefits: Nickel-free alloys minimize allergic reactions, making them suitable for medical devices and personal jewelry.
- Sustainability: They contribute to lower environmental impact through decreased mining and processing of nickel.
- Versatile Applications: These materials find use in various fields such as automotive, electronics, and medical industries.
- Alternatives: Cobalt-based and titanium alloys serve as strong substitutes, showcasing comparable or superior properties in many cases.
- Economic Considerations: While there may be initial higher costs, long-term savings and compliance with health regulations often justify the transition.
Implications for Future Research and Industry
The shift towards nickel-free alloys has significant implications for both research and industry. Firstly, continued research into new nickel-free formulations could yield materials that outperform traditional alloys. Areas such as nanotechnology and biocompatibility are ripe for exploration. The demand for nickel-free options will likely continue to grow, driven by rising awareness of health impacts and environmental sustainability.
Additionally, as manufacturers adapt to these changes, they may need to rethink existing processes to optimize for nickel-free production. This transition could lead to innovations in manufacturing techniques that enhance efficiency and reduce waste.
"As industries evolve, embracing nickel-free alternatives is not just a preference; it is becoming a necessity for health, safety, and environmental responsibility."
In summary, the potential for nickel-free alloys spans across many domains. It speaks to a broader trend toward sustainable manufacturing practices and highlights the importance of innovation in meeting future demands.