Understanding Physical Vapour Deposition Techniques
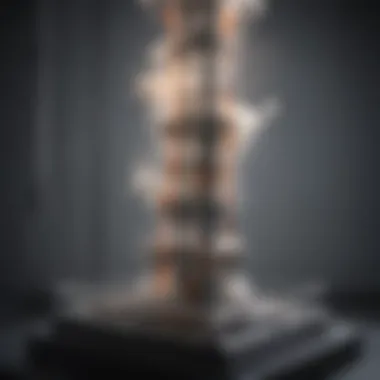
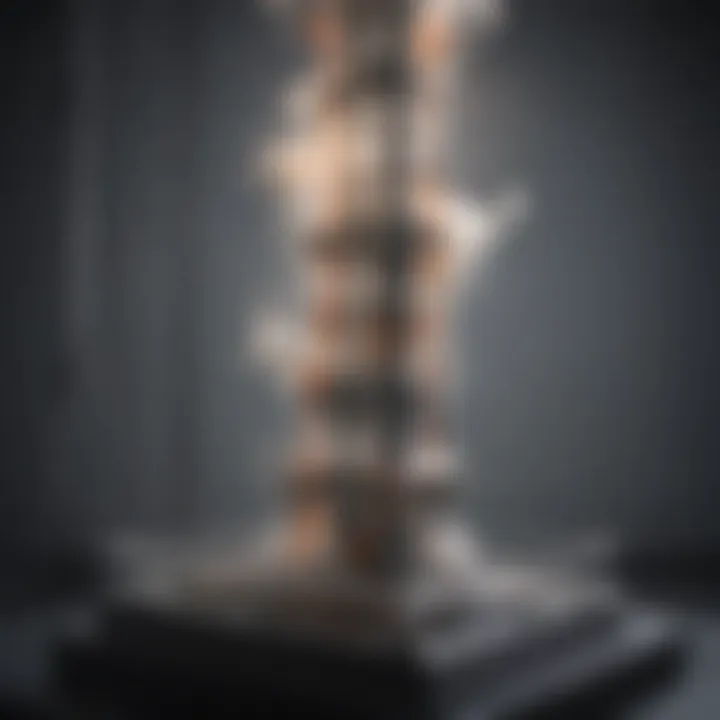
Research Overview
Physical Vapour Deposition (PVD) is a sophisticated method for producing thin films, crucial in various fields such as electronics, optics, and materials science. The technology is based on the physical transfer of material from a condensed phase onto a substrate. This section outlines the key aspects of PVD, emphasizing its mechanisms, significance, and recent advancements in the domain.
Summary of Key Findings
- Mechanisms of PVD: The process of PVD involves three primary steps: evaporation or sputtering of the target material, transport of the vapour through a vacuum or inert gas, and deposition onto the substrate surface. The interaction between vapour species and the substrate significantly influences the film's properties.
- Techniques: Various methods such as thermal evaporation, electron-beam evaporation, and sputter deposition are employed under PVD. Each technique offers distinct advantages and parameters which determine the quality of the deposited layers.
- Applications: The applicability of PVD spans diverse industries. It is crucial in the production of semiconductors, mirror coatings, and decorative finishings. Industries leverage PVD for its ability to enhance properties such as wear resistance, corrosion resistance, and aesthetic appeal.
Importance of the Research
The relevance of exploring PVD extends beyond mere technical knowledge. PVD serves as a gateway to developing advanced materials and coating techniques that meet the evolving demands of technology. The ability to tailor material properties through PVD promotes innovation in manufacturing processes, contributing to the advancement of sustainable practices and energy-efficient technologies. As industries strive for superior materials, understanding PVD becomes integral for researchers and professionals alike.
PVD is not just a method; it is a catalyst for innovation, pushing the boundaries of what materials can achieve in various practical applications.
Methodology
To effectively engage with the topic of Physical Vapour Deposition, a structured approach is utilized in this investigation.
Study Design
A qualitative approach is adopted to explore the nuances of PVD. This involves a comprehensive review of literature, including academic papers, industry reports, and technological analyses. This design aids in examining both theoretical frameworks and empirical outcomes related to PVD.
Data Collection Techniques
Data is collected from multiple sources to ensure a well-rounded perspective. These include:
- Peer-reviewed journals and conference proceedings concerning PVD technologies.
- Case studies from leading manufacturers and research institutions focusing on PVD applications.
- Interviews with experts in material science and coatings.
This multifaceted approach enables a nuanced understanding of PVD, highlighting the potential it holds in shaping future advancements in materials technology.
Prologue to Physical Vapour Deposition
Physical Vapour Deposition (PVD) is a pervasive and critical technology in the field of materials science, particularly in the area of thin-film deposition. This introduction serves as a foundation for understanding how PVD plays an essential role in various industrial applications and technologies.
PVD encompasses processes that allow for the deposition of thin films on a wide range of substrates. The benefits of this process are numerous, including the ability to create highly controlled coatings with exceptional quality and performance characteristics. The significance of PVD cannot be overstated, as it contributes to advancements in industries such as electronics, optics, and even aerospace.
In this section, we will define PVD and provide an overview of its mechanisms and historical context. A clear understanding of the definition will set the stage for a deeper exploration of the procedures and techniques involved in PVD. By assessing the historical context, readers can appreciate how PVD has evolved over the years and its current relevance in modern technology.
Definition and Overview
Physical Vapour Deposition is a set of vacuum deposition techniques that produce thin films by thermally evaporating materials. These vapors then condense on a substrate to form a solid film. Generally, PVD techniques are applied to enhance the properties of surfaces, such as increased durability, improved optical characteristics, and better electrical conductivity.
Common types of PVD methods include evaporation and sputtering, which will be discussed in detail in subsequent sections. The precision of PVD results in thin films that range from a few nanometers to several micrometers in thickness. This precision is a key reason PVD is widely adopted across various applications, including semiconductor manufacturing and optical coatings.
Historical Context
The origins of Physical Vapour Deposition can be traced back to the late 19th century. Early experiments with vacuum deposition began with scientists like Michael Faraday. He explored the principles of vapor deposition as he conducted research on electric discharge in gases.
In the 1960s and 1970s, PVD technologies advanced significantly with the introduction of modern vacuum systems and the development of sputtering techniques. This period marked a pivotal change as industries began utilizing PVD for producing high-quality thin films in electronics and optics. As technology progressed, new advancements emerged—better control over the coating process pioneered techniques such as ion beam deposition and reactive sputtering.
Today, PVD is an established technique utilized across a variety of industries, indicating its essential role in modern manufacturing processes. Its ongoing development reflects the continuous need for innovative material solutions, particularly in advanced technology sectors.
"PVD has impacted various fields, allowing for custom-tailored surface properties that enhance the durability and performance of materials."
In summary, understanding the fundamentals of PVD and its historical developments provides an essential perspective on its implications. As we proceed further in this article, the mechanisms and applications of Physical Vapour Deposition will be investigated in detail to highlight its significance in today’s technological landscape.
Key Mechanisms of PVD
Understanding the key mechanisms of Physical Vapour Deposition (PVD) is crucial for grasping how this technology achieves its purpose of thin-film deposition. The two principal methods—evaporation and sputtering—represent the underlying techniques employed in PVD processes. Each method has its unique characteristics, offering distinct advantages and challenges that significantly impact film quality, properties, and applications.
Evaporation
Evaporation is one of the oldest and most straightforward techniques utilized in PVD. This method involves transforming solid or liquid materials into vapor, which then condenses on a cooler substrate to form thin films. The fundamental principle is relatively simple, yet the nuances of evaporation can lead to significant variations in film characteristics.
Advantages of Evaporation:
- Simple Setup: The evaporation process generally requires less complicated equipment compared to other PVD methods, making it accessible for various applications.
- High Purity: Deposited films often exhibit superior purity since the source material evaporates in a vacuum, minimizing contamination from environmental sources.
- Control Over Thickness: By adjusting the evaporation rate and time, precise control of film thickness can be achieved.
However, it’s important to note that this technique has its limitations. For instance, the directional nature of the vapor can lead to non-uniformities in film deposition, especially for large or complex substrates. Additionally, some materials may not vaporize efficiently, which can affect deposition rates.
Sputtering
Sputtering, distinct from evaporation, involves bombarding a target material with energetic ions. This process ejects material from the target, which then deposits onto the substrate. Sputtering is known for producing films with excellent adhesion and uniformity, making it a preferred choice in many advanced applications.
Key Benefits of Sputtering:
- Versatile: This method can be used for a wide range of materials, including metals, oxides, and nitrides.
- Uniform Thickness: The plasma-induced sputtering generates a more uniform deposition across the surface, even for complex geometries.
- Energy Transfer: The energetic nature of sputtering allows for better control over film properties, leading to enhanced performance in applications such as semiconductors and optics.
Despite its benefits, sputtering requires more complex equipment and can have higher operational costs due to the need for maintaining a plasma environment. Additionally, the process can generate excess heat, which may affect sensitive substrates if not managed properly.
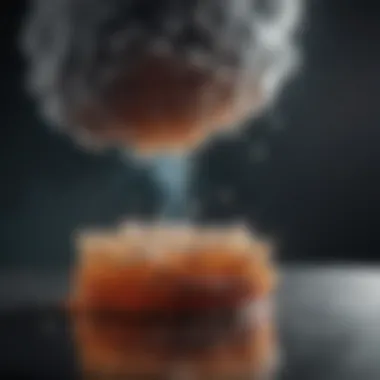
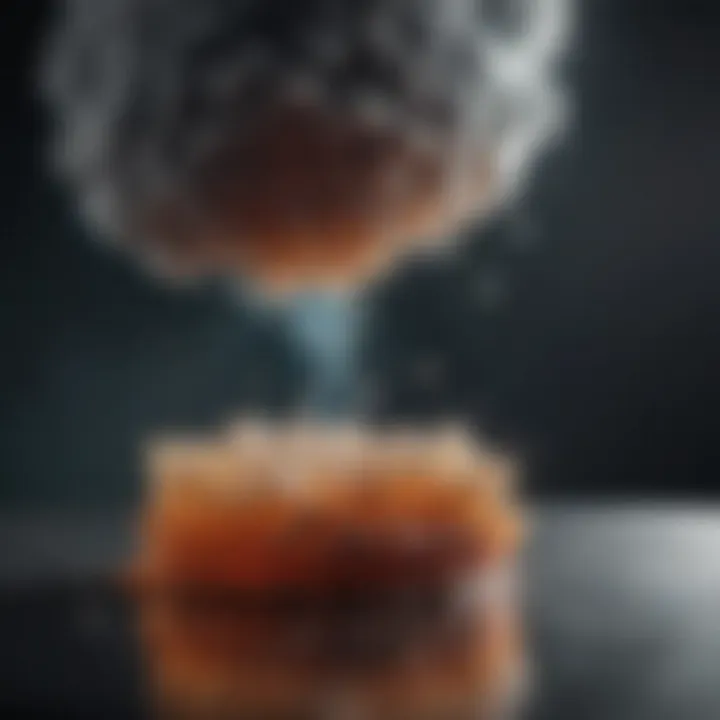
"The choice between evaporation and sputtering is often dictated by the specific application requirements, film properties desired, and cost considerations. Understanding these mechanisms allows for better selection of techniques to achieve optimal results."
In summary, both evaporation and sputtering are critical components of the PVD landscape. Their unique characteristics provide a complementary palette for the engineering of thin films in various technological domains.
Techniques of Physical Vapour Deposition
The Techniques of Physical Vapour Deposition (PVD) are fundamental for achieving precise thin-film coatings with specific properties. These techniques play a significant role in various industries, including semiconductor manufacturing, optics, and materials science. Different methods are chosen based on the required characteristics of the deposited film, such as thickness, purity, and adherence to the substrate.
Thermal Evaporation
Thermal evaporation is among the most commonly used methods in PVD. It involves heating a material in a vacuum chamber until it vaporizes. The vapor then condenses on the cooler substrate, forming a thin film. This method is relatively straightforward and cost-effective. However, it necessitates a robust vacuum system to minimize contamination and ensure even thickness.
Key Features of Thermal Evaporation:
- Material can be metal, polymer, or other compounds.
- High purity due to the vacuum environment.
- Suitable for a range of substrates, including glass and silicon wafers.
One notable advantage of thermal evaporation is the ability to achieve thin films varying from nanometers to several micrometers. Yet, it has limitations, such as lower deposition rates compared to other techniques.
Electron Beam Evaporation
Electron beam evaporation enhances thermal evaporation by utilizing a focused electron beam to heat the source material. This method allows for increased control over the deposition process, leading to better quality thin films. It is particularly effective for materials with high melting points. The process occurs under high vacuum conditions, which reduces impurities in the film.
Benefits of Electron Beam Evaporation include:
- Higher deposition rates compared to standard thermal evaporation.
- Enhanced film uniformity and atomic alignment.
- Focused energy can precisely target specific areas on the substrate.
The trade-off with electron beam evaporation includes the complexity of the equipment and potential for uneven deposition if not monitored closely.
Magnetron Sputtering
Magnetron sputtering is a widely employed technique in PVD, especially in the semiconductor and optical industries. This method involves using a magnetron to create a plasma that bombards a target material. The kinetic energy from the ions ejects atoms from the target, which then deposit onto a substrate. This technique provides superior control over film properties.
Advantages of Magnetron Sputtering:
- Ability to deposit a wide range of materials, including metals, oxides, and nitrides.
- High-quality films with good adhesion and durability.
- Lower substrate damage due to the process's lower thermal load.
In addition, magnetron sputtering often results in improved step coverage on complex geometries compared to other methods. However, the initial capital investment can be significant.
"By choosing the appropriate PVD technique, industries can optimize performance and achieve specific material properties essential for advanced applications."
Materials Used in PVD
The selection of materials in Physical Vapour Deposition (PVD) is crucial due to its direct impact on the quality of the deposited film and the overall performance of the end product. The materials chosen not only influence the mechanical properties, such as hardness and adhesion, but also impact the electrical and optical characteristics of the resulting coatings. This section examines the three main categories of materials used in PVD: metals, oxides, and nitrides. Each category offers unique advantages and challenges that contribute to their application across various industries.
Metals
Metals are among the most common materials used in PVD processes. Their excellent conductivity and thermal properties make them suitable for various applications, particularly in the semiconductor industry. Common metals used include titanium, aluminum, and copper.
- Titanium: Often used for its superb strength-to-weight ratio and corrosion resistance. Titanium films enhance durability in harsh environments.
- Aluminum: Its low melting point and high conductivity make it ideal for electronic components. Aluminum is widely used in chip fabrication.
- Copper: Known for its high electrical conductivity, copper is extensively used in interconnects and circuit boards.
Choosing appropriate metals can significantly enhance the performance of coatings. However, the challenge lies in controlling the deposition process to achieve desired thickness and uniformity, which is critical for effective performance.
Oxides
Oxides are another vital category of materials in PVD. Metal oxides, such as titanium dioxide and zinc oxide, are notable for their chemical stability and optical properties. They are commonly employed in applications requiring transparency and durability.
- Titanium Dioxide (TiO2): Widely used for its photocatalytic properties and applications in self-cleaning surfaces. It has also found use in anti-fogging coatings.
- Zinc Oxide (ZnO): Utilized in photonic devices and transparent conductive films. Its wide bandgap feature makes it suitable for UV light applications.
These materials can enhance the optical properties of coatings. The challenge with oxides is maintaining stability during the deposition process and ensuring the correct stoichiometry in the resulting films.
Nitrides
Nitrides, particularly titanium nitride and silicon nitride, represent a unique section of materials used in PVD. These compounds offer exceptional hardness and thermal stability. They are extensively applied in cutting tools and protective coatings.
- Titanium Nitride (TiN): Known for its gold-like appearance, TiN is frequently used to enhance the wear resistance of tools and provide decorative finishes on various household and industrial items.
- Silicon Nitride (Si3N4): Valued for its high toughness and thermal stability, it is commonly used in ceramics and electronic applications.
Overall, selecting the right nitrides for a specific application is vital for achieving optimal performance and longevity. The main concern is ensuring precise control over the deposition parameters to achieve the desired properties.
"The choice of materials in PVD directly influences the performance characteristics of the final product. A careful selection between metals, oxides, and nitrides is necessary to meet specific application requirements."
In summary, the materials used in PVD play a fundamental role in determining the quality and performance of the deposited films. Understanding their unique properties and applications allows researchers and engineers to make informed decisions, ensuring successful and effective outcomes in their respective fields.
Applications of Physical Vapour Deposition
The applications of Physical Vapour Deposition (PVD) are vast and diverse, significantly impacting multiple sectors. This technique is pivotal in enhancing material properties and extending the functionality of various products. Understanding these applications is crucial for researchers, engineers, and industry professionals looking to leverage PVD technology in their respective fields.
Semiconductor Industry
The semiconductor industry relies heavily on PVD processes for fabricating microelectronic devices. PVD techniques such as sputtering and evaporation are notably used for creating thin films of materials like silicon and metal, essential for circuit components. The precision offered by PVD allows for the development of intricate structures with nanoscale dimensions.
Key benefits of using PVD in this industry include:
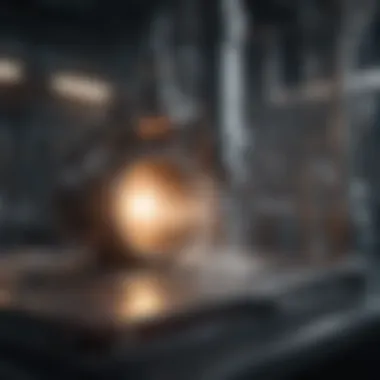
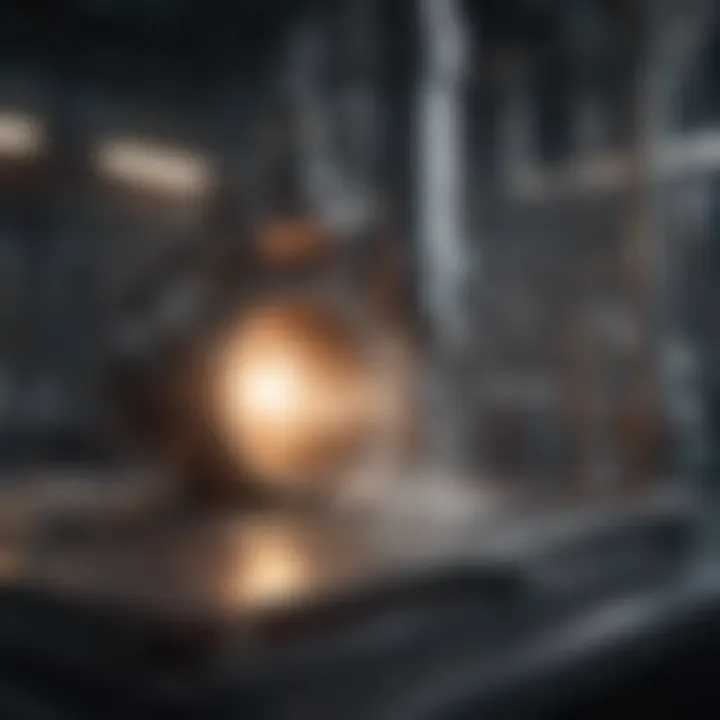
- High purity: The films produced show minimal contamination, which is critical for semiconductor performance.
- Control over thickness: PVD enables accurate film thickness control, ensuring the reliability of devices.
- Scalability: It can be scaled for both small and large production volumes, making it versatile for different manufacturing needs.
The ongoing advancements in PVD technology continue to support the evolution of microelectronics, meeting the demands of faster and more efficient devices.
Optical Coatings
Another significant application of PVD technology is in the field of optical coatings. These coatings enhance the performance of optical components such as lenses and mirrors. The deposition of thin films can improve reflectivity, transmission, and anti-reflection properties. Utilizing materials like titanium dioxide and silica, manufacturers can create coatings tailored for specific wavelengths of light.
Optical coatings produced by PVD offer several advantages:
- Enhanced durability: PVD coatings are typically more robust compared to traditional coatings.
- Design flexibility: Various materials can be combined to achieve desired optical characteristics.
- Reduced cost: In many cases, PVD is more cost-effective than competing coating technologies, especially for large runs.
The versatility of PVD in optical applications underscores its importance in improving product performance and driving innovation in vision technologies.
Protective Coatings
Protective coatings produced through PVD play a vital role in extending the life of products in harsh environments. Industries such as aerospace, automotive, and manufacturing use these coatings to combat wear, corrosion, and thermal degradation.
Some materials often applied include titanium nitride and chromium nitride, which provide a hard surface finish. Key benefits include:
- Corrosion resistance: PVD coatings significantly improve the resistance of components against various chemicals and moisture.
- Wear resistance: This is crucial for tools and parts subject to friction and abrasion.
- Aesthetic enhancements: PVD allows for various finishes that can improve the visual appeal of products without sacrificing functionality.
In summary, the applications of Physical Vapour Deposition highlight its transformative role across various industries, making it indispensable for modern technology and manufacturing processes.
"PVD technology is a cornerstone in advancing the capabilities of materials, allowing for innovations that push industry boundaries."
The exploration of its applications reveals not only the technical advantages but also the potential for future developments in various sectors.
Advantages of PVD Techniques
Physical Vapour Deposition (PVD) offers several notable advantages that make it a preferred choice in various industries. These advantages are influential in not only the performance of the films produced but also in the efficiency and effectiveness of the overall deposition process. Understanding these benefits can provide insights into why PVD is a critical technology in material science.
High Purity Films
One of the primary advantages of PVD techniques is the ability to produce films of exceptionally high purity. The process involves vaporizing solid materials in a vacuum, which minimizes contamination from other sources. The primary deposition material can be deposited without introducing impurities, which is vital in many applications.
High purity is essential in sectors such as semiconductors, where even minute levels of impurities can disrupt electronic properties. This characteristic ensures that the final products meet stringent quality standards, leading to improved performance and reliability.
Uniform Coating
PVD techniques also excel in achieving uniform coating across various substrates. Uniformity in thickness is crucial, particularly in applications involving optical coatings or protective layers. Inconsistent thickness can lead to defects in electronic devices or optical performance issues in lenses.
Techniques like magnetron sputtering offer improved control over film thickness. This allows for uniform distributions even over complex geometries. Consequently, manufacturers can achieve higher performance and longer-lasting products, reducing waste and increasing efficiency.
Versatility
The versatility of PVD is another compelling advantage. PVD can be applied to a wide range of substrates, including metals, ceramics, and plastics, making it suitable for diverse applications. This adaptability is critical in modern manufacturing environments that require different materials for various applications.
Moreover, PVD techniques can deposit various materials, from metals to nitrides and oxides, on a single substrate. This opens avenues for innovative designs and combinations of materials that would not be possible with other deposition methods. The ability to customize coatings based on specific requirements enhances its appeal in industries including aerospace, automotive, and healthcare.
"The versatility of PVD techniques offers unprecedented opportunities for innovation in material engineering."
In summary, the advantages of PVD techniques—high purity films, uniform coating, and versatility—make them indispensable in modern technology and industrial applications. These benefits significantly influence the material characteristics and performance, paving the way for advancements in various fields.
Challenges Associated with PVD
Understanding the challenges associated with Physical Vapour Deposition (PVD) is crucial for its optimization and application. While PVD presents numerous advantages, it is not without its limitations. These challenges impact the efficiency, cost, and feasibility of using PVD in various industrial contexts. Acknowledging these issues helps researchers and industry professionals to find solutions and improve processes, thereby enhancing the technology as a whole.
Cost Effectiveness
Cost-effectiveness represents a significant concern in the application of PVD technologies. The initial investment for PVD equipment can be quite substantial. High-quality vacuum systems, advanced sources for material vaporization, and sophisticated substrate handling apparatus are among the expensive components. Moreover, operational costs, including maintenance, materials, and labor, can accumulate rapidly. As a result, smaller companies may find it difficult to justify the expense of PVD when compared to other coating methods that may be less expensive upfront.
Another aspect to consider is the return on investment (ROI). It is vital for companies to assess whether the benefits of PVD, such as high quality and uniformity of films, justify the higher costs. Businesses focusing on specialized applications that require superior coatings may be more inclined to invest in PVD, despite its cost, as the end products can lead to greater customer satisfaction and market competitiveness.
Film Thickness Control
Precise control of film thickness is essential in PVD processes. Variability in thickness can adversely affect the performance and properties of the deposited films. If the film is too thin, it may not provide adequate protection or functional characteristics; if too thick, it can lead to issues like cracking or delamination.
Achieving uniform thickness can be challenging, especially for complex geometries or large substrates. Some PVD techniques, such as sputtering, may produce films with non-uniform thickness across large areas. This can be problematic in industries where tight tolerances are crucial, such as in electronics or optics. Collaboration and constant monitoring through advanced tools are necessary to ensure the film thickness remains within acceptable limits during the deposition process.
Substrate Compatibility
The compatibility of the substrate with PVD processes poses another challenge. Different materials respond uniquely to the high energy environment of PVD operations. Some substrates can endure the conditions without adverse effects, while others may experience degradation or warping.
Additionally, the adhesion of the deposited layer depends significantly on the substrate material and its surface characteristics. If the substrate cannot support the applied film, issues can arise, leading to poor coating performance and compromised durability. It becomes imperative for researchers and manufacturers to select appropriate substrates that can withstand the PVD process while ensuring effective adhesion and overall performance.
"Adequate knowledge about substrate properties is vital for achieving successful PVD outcomes."
Innovations in PVD Technology
Innovations in Physical Vapour Deposition (PVD) technology are essential to enhance the efficiency, capabilities, and applications of this vital process in material science. As industries demand higher performance from materials, advancements in PVD methods meet these needs by allowing for better film quality, improved uniformity, and the ability to work with various substrates. In this section, we will delve into some of the latest innovations that are shaping the field of PVD.
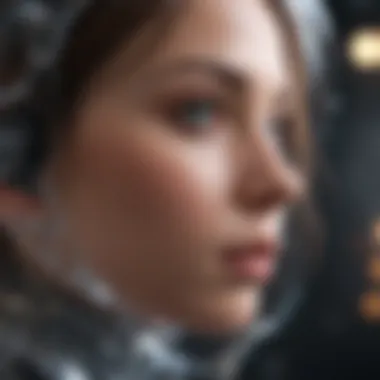
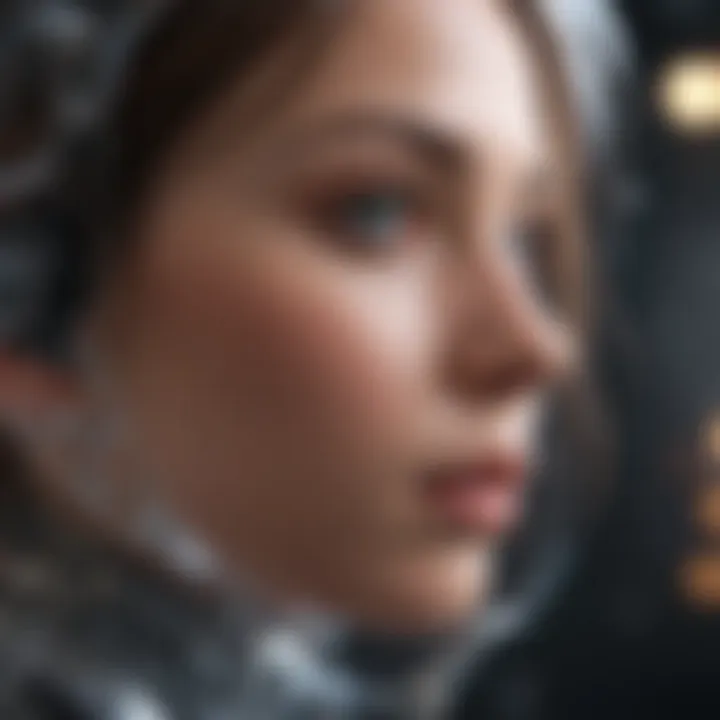
Advanced Sputtering Techniques
Advanced sputtering techniques represent significant progress in the PVD process. Traditional sputtering can be slow and may not provide the desired film quality. Recent developments have introduced methods such as high-power impulse magnetron sputtering (HiPIMS). HiPIMS enhances the ionization of the vaporized material, leading to a denser and more uniform thin film.
Another notable method is pulsed DC sputtering. This approach allows for better control over the deposition process. It can adapt to different substrates and materials, enabling the use of complex coatings that were previously challenging to achieve. As a result, the application scope expands from electronics to medical devices, improving both functionality and durability.
Plasma Enhanced PVD
Plasma enhanced PVD is another area where innovations have emerged. This technique uses plasma to assist the deposition process, increasing the rate of film growth and improving adhesion to substrates. The use of plasma can modify the properties of the films deposited, resulting in better mechanical characteristics.
Plasma takes advantage of various gases, such as nitrogen or argon, to create different film compositions. This flexibility opens doors for creating tailored materials for specific applications, from optical coatings to hard protective layers. The growing interest in eco-friendly practices makes plasma enhanced PVD attractive since it often uses fewer harmful chemicals compared to other deposition techniques.
Integration with Other Techniques
The integration of PVD with other coating techniques is a vital trend in this field. For instance, combining PVD with chemical vapor deposition (CVD) enhances the properties of the coatings while offering more versatility. Such integration allows for the development of multilayer coatings, which can significantly enhance performance in demanding environments.
Using hybrid approaches can lead to exceptional results, especially in areas like semiconductor manufacturing or optical applications. These methods provide unique solutions to complex challenges encountered in modern applications, such as the need for more robust materials or innovative designs.
"Innovative PVD technologies are pivotal in addressing the needs of today's high-performance materials, making them more adaptable and efficient across various industries."
Innovations within the PVD landscape are essential for maintaining the relevance of the technology in an ever-changing industrial ecosystem. Each advancement not only improves the quality and efficiency of the deposition process but also ensures that PVD continues to play an integral role in future materials science developments.
Environmental Considerations in PVD
In recent years, environmental considerations in Physical Vapour Deposition (PVD) have gained notable attention among researchers and industry professionals. As PVD is widely applied in various fields, the impact of PVD processes on the environment is crucial to understand. This section will elaborate on the essential aspects surrounding sustainability and waste management in the context of PVD, emphasizing the need for a balanced approach to ensure ecological integrity while exploiting its advantages.
Sustainability Challenges
Sustainability challenges in PVD primarily involve the energy consumption associated with deposition processes. Many PVD techniques require significant power inputs, which can lead to high carbon emissions if the energy sources are not renewable. Moreover, the materials used during the deposition can contribute to resource depletion if not sourced responsibly. In addition to energy use, several chemicals and materials are involved in the processes, potentially exacerbating environmental harm if not managed adequately.
PVD often utilizes noble gases, such as argon, in sputtering techniques. These gases, while necessary for the processes, are non-renewable. Their extraction and transportation carry environmental costs. Thus, a transition toward more sustainable gas management practices could provide benefits.
Waste Management
Efficient waste management is critical in minimizing the environmental impact of PVD operations. Waste generated during the PVD processes can include unutilized target materials, contaminated substrates, and process gases. The challenge lies in ensuring that these materials are properly handled, recycled, or disposed of in a way that does not harm the environment.
Innovative methods, such as recycling both target materials and used substrates, are essential in achieving waste management goals. Developments in closed-loop systems can help recover materials instead of discarding them. This not only reduces waste but also decreases costs associated with raw material procurement.
Furthermore, emissions control technologies need to be integrated into PVD systems to capture and neutralize hazardous gases. Such measures can significantly reduce the release of harmful substances into the atmosphere.
"Implementing sustainable practices in PVD is not just beneficial for the environment; it also creates a competitive edge in a market that increasingly values ecological integrity."
End
The environmental considerations surrounding PVD cannot be overlooked in today's industrial landscape. Addressing sustainability challenges and improving waste management will lead to more responsible deposition practices, aligning industry objectives with ecological principles. As research and innovation in this field advance, ongoing efforts must focus on striking the right balance between technological advancement and environmental stewardship.
Future Directions in PVD Research
Physical Vapour Deposition (PVD) continues to play an essential role in material science and engineering. To keep pace with evolving technology and demands, ongoing research is vital. This section focuses on the future directions in PVD research that promise to enhance capabilities and applications.
Emerging Materials
The exploration of emerging materials in PVD is a major focus for researchers. New materials can significantly improve the properties of coatings. For instance, novel alloys and compounds can enhance hardness and corrosion resistance. The introduction of two-dimensional materials also presents new opportunities. Graphene and transition metal dichalcogenides are examples. These materials may offer unique electronic and thermal properties, making them promising candidates for next-generation devices.
The demand for environmentally friendly materials is also growing. Research into non-toxic alternatives to traditional materials like cadmium or chromium is critical. Using biodegradable materials for specific applications can lead to more sustainable practices in the industry.
In summary:
- Novel alloys can enhance durability.
- Two-dimensional materials provide unique properties.
- Eco-friendly options are in demand for sustainability.
Enhanced Process Control
Another significant area of future research is enhanced process control during PVD. Achieving precise control over the deposition parameters is crucial for obtaining uniform coatings. Factors such as temperature, pressure, and time need meticulous adjustment. Advanced techniques for real-time monitoring can lead to better outcomes.
Automated systems utilizing artificial intelligence can optimize these parameters dynamically. They can analyze the deposition process continuously and make on-the-fly adjustments. This level of control is critical, especially in industries like semiconductor manufacturing. It ensures the high purity of films, reducing defects that could compromise the performance of electronic components.
There is also a focus on integrating simulation and modeling tools. These tools can predict the outcomes of different process parameters before actual deposition. This reduces trial and error, saving time and resources. Some benefits of enhanced process control include:
- Increased film quality
- Reduced material waste
- Improved manufacturing efficiency
"As technology evolves, the ability to control deposition processes with precision can change the landscape of PVD applications."
Finale
The concluding section of this article plays a crucial role in encapsulating the significance of Physical Vapour Deposition (PVD) technology within the realm of material science and engineering. It serves to summarize the performance, advantages, and intricate mechanisms that have been explored throughout the narrative. PVD is not just a method of film deposition; it is a vital technology shaping various industries, from semiconductors to optics.
One of the key insights is the ability of PVD to produce high-purity thin films. This attribute is critical for applications that demand exact specifications and superior quality. The techniques discussed, such as thermal evaporation and magnetron sputtering, highlight the versatility and adaptability of PVD in addressing different material deposition needs. Furthermore, the understanding of the materials involved — including metals, oxides, and nitrides — provides a foundation for innovation and application evolution.
Summary of Key Insights
- High Purity and Quality: PVD techniques yield thin films with exceptional purity, crucial for high-tech applications.
- Diverse Techniques: Methods like thermal evaporation and magnetron sputtering demonstrate the flexibility of PVD in varying manufacturing environments.
- Wide Range of Materials: The capability to coat metals, oxides, and nitrides allows for tailored solutions across multiple sectors.
- Technological Advances: Recent innovations, such as plasma enhanced PVD, indicate ongoing improvements and a shift toward more sustainable processes.
- Global Applications: PVD is integral in semiconductor manufacturing, optical coatings for electronics, and protective coatings in various hardware, underlining its industrial relevance.
Implications for Future Studies
Research in PVD remains an active domain, and future studies will likely focus on several key areas. Emerging materials, such as novel alloys and hybrid compounds, may redefine application boundaries and foster improved performance standards. Enhanced process control mechanisms will be paramount. They can lead to achievements in film thickness control and substrate compatibility, which are current challenges in PVD.
Considerations surrounding sustainability will also steer future research. There is a pressing need to develop PVD processes that minimize waste and energy consumption. As industries increasingly prioritize environmental impacts, PVD research must adapt to these requirements.