Exploring Vibrating Conveyors: Innovations and Applications
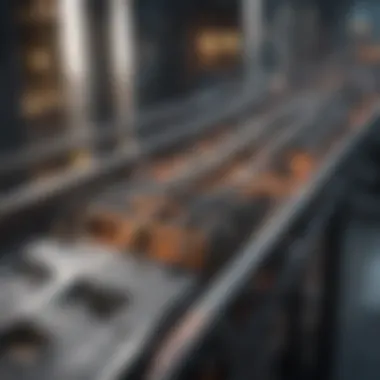
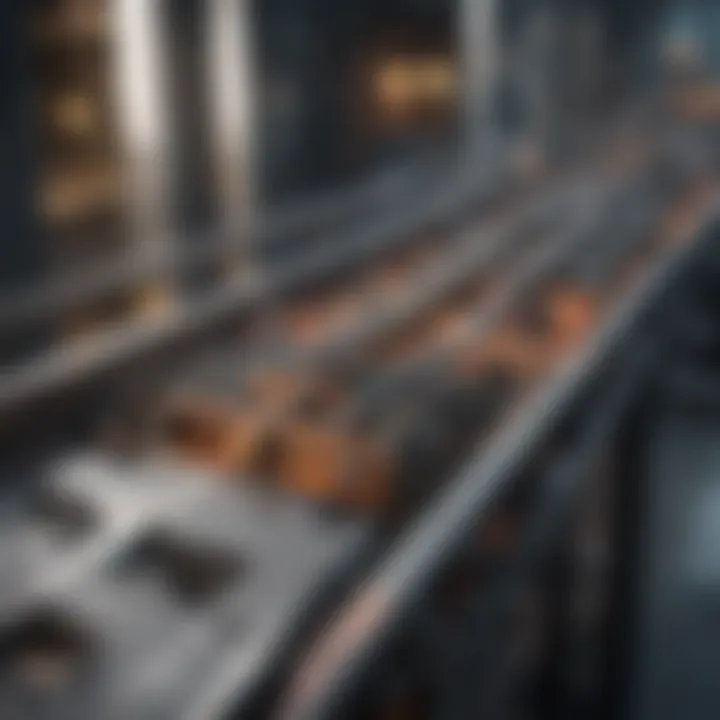
Intro
Vibrating conveyors are essential equipment in various industries. They transport materials efficiently, making them crucial for optimizing workflow and productivity. Understanding how these conveyors function helps industries improve their operations. In this article, we will explore the mechanisms behind vibrating conveyors, their diverse applications, and the latest innovations in the field.
Research Overview
Summary of Key Findings
The operational principles of vibrating conveyors revolve around the creation of vibration energy, which enables precise movement of materials. Key findings include:
- Vibrating conveyors operate based on controlled vibrations that ensure smooth material flow.
- They are widely used in industries such as mining, food processing, and waste management.
- Recent innovations have focused on improving energy efficiency, reducing maintenance, and increasing processing speed.
Importance of the Research
This research is significant for several reasons. First, it highlights the vital role of vibrating conveyors in optimizing industrial processes. Second, it reveals how advancements in technology can lead to enhanced operational capabilities. Understanding these aspects can help professionals make informed decisions regarding equipment selection and application in their respective fields.
Mechanisms of Operation
Vibrating conveyors function through the principles of vibration, utilizing mechanical oscillation to move materials along a defined path. The design typically incorporates a trough, where the material is loaded, and an oscillating mechanism that generates vibrations. The movement facilitates the transportation of materials over varying distances and inclines, thus adapting to specific operational needs.
The vibration frequency, amplitude, and angle of inclination can be adjusted to cater to different types of materials, such as bulk solids or packaged items. Consequently, the flexibility in design renders vibrating conveyors suitable for a broad range of applications.
Applications in Industry
Vibrating conveyors find applications in many sectors. Here are some common uses:
- Mining: Transporting ores and minerals from extraction points to processing facilities.
- Food Processing: Moving raw materials, intermediate products, and packaged goods within production lines.
- Waste Management: Sorting and processing recyclable materials efficiently.
Each application requires an understanding of the specific material characteristics and processing requirements to optimize the conveyor setup.
Innovations in Vibrating Conveyors
Technological advancements continue to enhance the functionality of vibrating conveyors. Recent innovations include:
- Smart monitoring systems that use sensors to track conveyor performance, ensuring timely maintenance.
- Energy-efficient motors designed to reduce energy consumption while maximizing output.
- Modular designs that allow easy modification and customization based on specific needs.
These innovations not only increase efficiency but also improve reliability and reduce operational costs.
End
In summary, vibrating conveyors offer a crucial solution for material transport in many industries. Their operational mechanics, extensive applications, and recent innovations reflect significant contributions to industrial efficiency. Understanding these aspects can enhance decision-making for professionals engaged in material handling and processing.
Prelude to Vibrating Conveyors
Vibrating conveyors have become pivotal in numerous industrial processes. They facilitate the movement of goods efficiently and effectively, impacting productivity and operational fluidity. Understanding how these conveyors work helps one appreciate their significance across various sectors, including mining, food processing, and recycling.
Definition and Basic Functionality
A vibrating conveyor is a piece of equipment designed to transport bulk material from one point to another using vibratory motion. The basic functionality relies on controlled vibrations, which create a shaking movement to move materials along a trough or a tube. This simple yet innovative approach enables handling various materials, such as powders, granules, and larger items, effectively.
The mechanism typically consists of a trough, which holds the material, and an oscillator. The oscillator produces vibrations that push the material forward as it rests in the trough. The design can vary, but the fundamental principle remains the same. These conveyors allow precise control over the flow of materials, making them suitable for delicate items in food processing or heavy loads in mining.
Historical Development
The history of vibrating conveyors dates back decades, tied closely to advancements in mechanical engineering. Early iterations were often basic, relying on simple mechanisms to create vibration. These conveyors were primarily used in the mining industry for transport of ores.
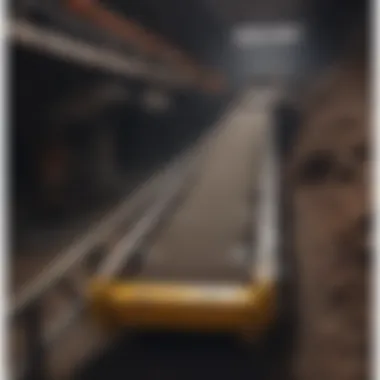
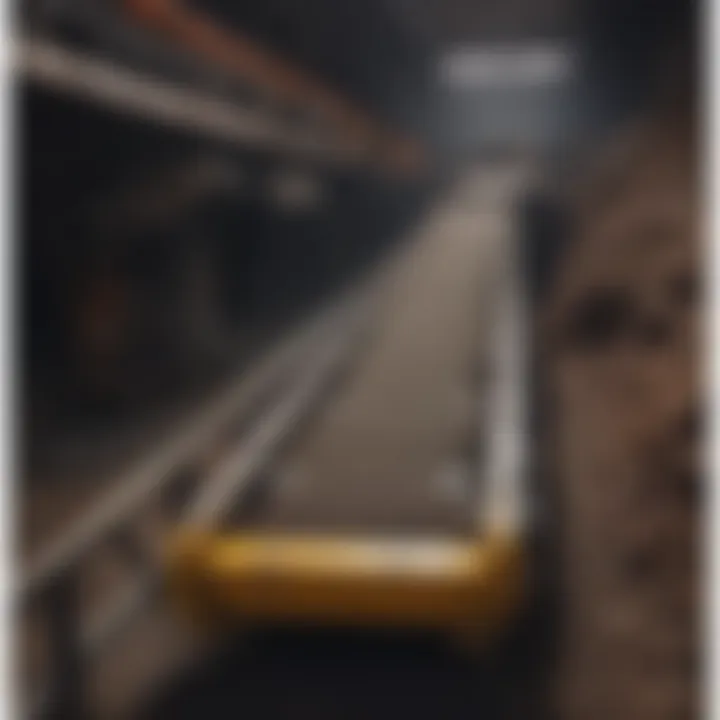
With time, new technologies emerged, improving the efficiency and effectiveness of vibrating conveyors. The introduction of electromagnetic systems revolutionized the field, replacing older mechanical-driven models. Further studies and innovations led to diverse designs tailored for specific applications and materials. This evolution has positioned vibrating conveyors as a standard solution in many industrial domains today.
Mechanisms of Vibrating Conveyors
Vibrating conveyors play a crucial role in industrial processes by transferring materials efficiently and effectively. Understanding their mechanisms is vital for optimizing performance in various applications. This involves recognizing the principles of vibration, knowing the different types available, and considering the key design elements.
Principles of Vibration
The principles that govern vibration in conveyor systems are fundamental to their operation. Vibration is generally produced by an external force, causing an oscillatory motion. This motion allows materials to move along the conveyor, driven by the dynamic forces acting on them. Properly tuned systems ensure that materials are carried smoothly while minimizing issues like backflow and blockages. The synchronization of motor forces and conveyor design also significantly affects efficiency. A correct balance in frequency and amplitude makes the system more productive.
Types of Vibrating Conveyors
Vibrating conveyors come in various forms, each suited for specific situations. Recognizing these types helps in selecting the right conveyor for a particular application.
Electromagnetic Vibrating Conveyors
Electromagnetic vibrating conveyors are driven by electromagnetic forces. This mechanism allows for a precise control over vibration frequency and amplitude, making it suitable for handling delicate materials. One key characteristic is its ability to adjust the speed of the conveyor by changing the power supply. This feature provides flexibility in operation, which can be beneficial in many processes. However, the dependence on electrical components can lead to higher maintenance requirements compared to other types.
Mechanical Vibrating Conveyors
Mechanical vibrating conveyors utilize mechanical forces, like springs, to generate vibration. This type is robust and has a long lifespan, making it a popular choice for heavy-duty applications. A distinguishing feature is its ability to transport larger volumes of materials effectively. However, the energy consumption can be higher, and it may require more initial investment compared to electromagnetic systems.
Gravity-Driven Vibrating Conveyors
Gravity-driven vibrating conveyors rely on gravitational forces to facilitate material movement. They are often simpler and more cost-effective, as they require fewer mechanical components. The key characteristic is that they can handle a wide range of materials, from bulk solids to powders. Their unique advantage lies in lower operating costs. However, they may not be suitable for all types of materials, particularly those that need a controlled speed.
Design Considerations
Designing an effective vibrating conveyor involves various considerations to make it suitable for operations. Attention to detail in these areas can lead to improved operational efficiencies and effectiveness.
Material Selection
Choosing the right materials for the construction of vibrating conveyors is fundamental to ensure durability and functionality. The key characteristic here is the capability of the materials to withstand wear and environmental factors. Selecting high-quality materials can reduce maintenance costs and extend the life of the conveyor. On the downside, premium materials can increase initial expenses, but the long-term savings can justify this choice.
Dimensioning and Layout
Dimensioning and layout are critical in determining the capacity and efficiency of the conveyor. A well-designed layout maximizes space and minimizes material handling issues. The key characteristic here is the ability of the layout to accommodate various process requirements. An effective dimensioning can optimize flow and increase throughput. However, improper layout might lead to bottlenecks and operational inefficiencies.
Energy Efficiency
Energy efficiency in vibrating conveyors is a significant consideration in modern industries. Efficient systems reduce operational costs and have a lower environmental impact. The key characteristic of energy-efficient designs is lower power consumption while maintaining high performance. Designing for energy efficiency can lead to substantial savings over time. Yet, these systems may require advanced technologies, which can elevate initial costs.
Understanding the mechanisms behind vibrating conveyors is essential for effective material handling. It allows for better decision-making and implementation of systems in various industrial contexts.
Applications of Vibrating Conveyors
Vibrating conveyors are pivotal in many industries due to their unique ability to transport various materials efficiently. Their applications span across multiple sectors, facilitating processes that demand precision and flexibility. In this section, we will explore the diverse applications of vibrating conveyors, focusing on their significance, benefits, and the specific contexts in which they excel.
Material Handling Processes
In the realm of material handling, vibrating conveyors play a crucial role in ensuring a smooth and continuous flow of bulk materials. They are often used to move ores, aggregates, and recycled materials. One major advantage is their ability to handle a wide variety of materials, regardless of size, shape, or weight. The gentle movement minimizes material degradation, maintaining product integrity.
Factors to consider in material handling with vibrating conveyors include:
- Capacity: Vibrating conveyors can be engineered to meet specific throughput needs.
- Durability: Many are constructed with materials that can withstand heavy use and harsh conditions.
- Scalability: Systems can be designed to expand or adapt as operational needs change.
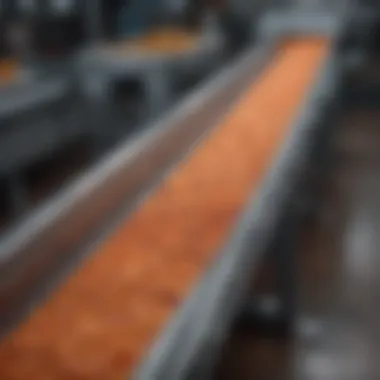
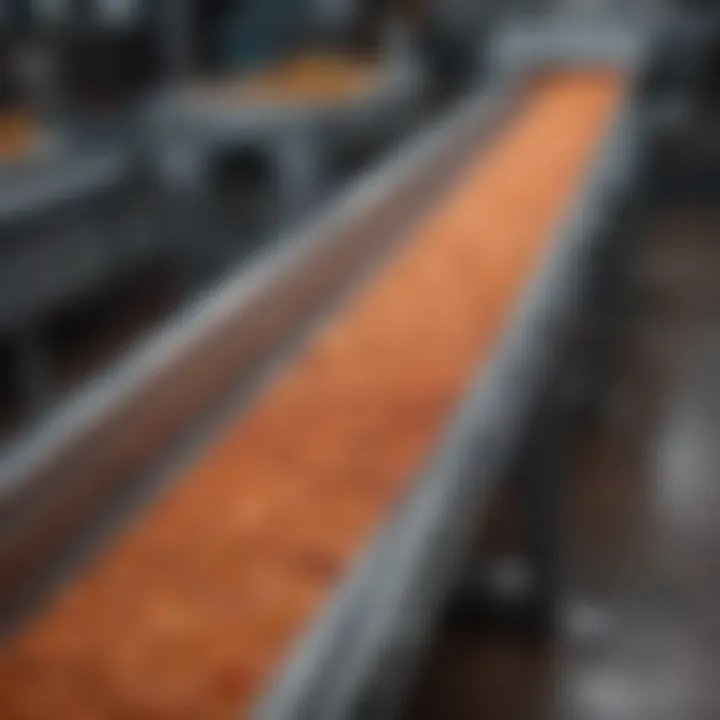
Mining and Mineral Processing
The mining and mineral processing industry relies heavily on vibrating conveyors for transporting mined materials from extraction points to processing facilities. These conveyors efficiently manage large amounts of heavy and abrasive materials. They are designed to endure the tough conditions found in mining environments.
Key points in their application in this sector include:
- Efficiency: They provide a continuous flow, reducing delays in operations.
- Versatility: From conveying coal to ore, they adapt to various material types.
- Safety: Their design often incorporates features that reduce the risk of accidents during transport.
Food Processing Industry
In the food processing sector, vibrating conveyors ensure the safe and effective movement of food products. They are crucial in transporting ingredients, finished products, and waste materials. Hygiene and cleanliness are primary considerations in this industry, which is where vibrating conveyors excel due to their design that minimizes contamination risk.
Essential aspects include:
- Compliance: Many vibrating conveyors are designed to meet food safety regulations.
- Gentle Handling: They transport delicate food items without causing damage.
- Customization: Various belt materials and design configurations allow for specific food applications.
Recycling Applications
Vibrating conveyors are increasingly essential in recycling facilities. They facilitate the separation and transportation of different materials such as glass, plastics, and metals. Their ability to minimize contamination and ensure the accurate sorting of materials is vital in recycling processes.
Important benefits in recycling applications are:
- Efficiency in Sorting: They help in maximizing recovery rates of recyclable materials.
- Reduced Labor Costs: Automating the transport reduces the need for manual sorting.
- Environmental Impact: By enhancing recycling processes, they contribute to sustainability efforts.
"Vibrating conveyors are not just tools of transport; they are integral to the efficiency and effectiveness of processes across various industries."
Innovations in Vibrating Conveyor Technology
Innovations in vibrating conveyor technology are pivotal in modern industrial processes. As industries aim for greater efficiency and productivity, the development of advanced technologies is crucial. These innovations not only enhance the performance of vibrating conveyors but also adapt them to meet evolving operational demands. The importance of this topic lies in understanding how cutting-edge technologies improve material handling, reduce downtime, and optimize resource use. This section will explore three specific areas of innovation: automation and smart technology integration, material innovations, and sustainability considerations.
Automation and Smart Technology Integration
Automation plays a significant role in optimizing the operation of vibrating conveyors. Smart technology integration facilitates real-time monitoring and control of the conveyor systems. Sensors and IoT devices gather data on various parameters, such as load weight and vibration frequency. This data empowers operators to make informed decisions, leading to improved efficiency and reduced maintenance costs. Additionally, automation minimizes human error, allowing for consistent operation.
The benefits of implementing automation include:
- Increased throughput: Automation enables faster processing of materials.
- Predictive maintenance: Advanced monitoring can predict potential failures, reducing unexpected downtimes.
- Improved operator safety: With automation, the risk of personnel injury is significantly decreased.
Material Innovations
The choice of materials used in the construction of vibrating conveyors has evolved significantly. Innovations in material science lead to the development of lighter, stronger, and more resilient materials. For instance, the use of advanced composite materials enhances durability while reducing overall weight. This, in turn, allows for easier installation and maintenance.
Additionally, materials that offer better resilience against wear and corrosion extend the lifespan of vibrating conveyors. Selecting the right material can also optimize energy efficiency, as lighter materials require less energy to transport the same load. Key considerations in material innovations include:
- Cost-effectiveness: New materials may have higher initial costs but reduce long-term maintenance expenses.
- Environmental impact: Sustainable materials can contribute to greener industrial practices.
Sustainability Considerations
In an era of increasing environmental consciousness, sustainability in vibrating conveyor technology cannot be overlooked. The innovation landscape has seen a rise in sustainable practices, addressing energy consumption and waste management. Technologies such as energy-efficient motors and regenerative drives reduce the energy footprint of conveyor systems.
Moreover, companies are exploring options to recycle materials used in conveyor construction, thus minimizing waste. Sustainability initiatives not only appeal to environmentally conscious consumers but also comply with regulatory requirements. Benefits of focusing on sustainability include:
- Cost savings: Reduced energy use translates to lower operating costs.
- Positive brand image: Companies perceived as environmentally responsible can attract more clients.
Innovations in vibrating conveyor technology are not just advancements; they represent a fundamental shift towards optimizing industrial practices and enhancing sustainability across various sectors.
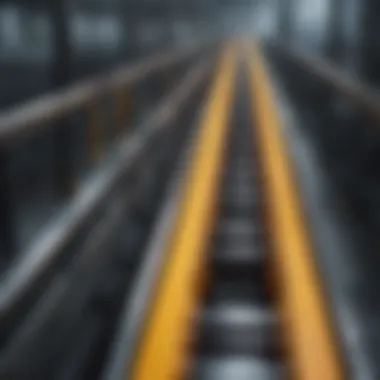
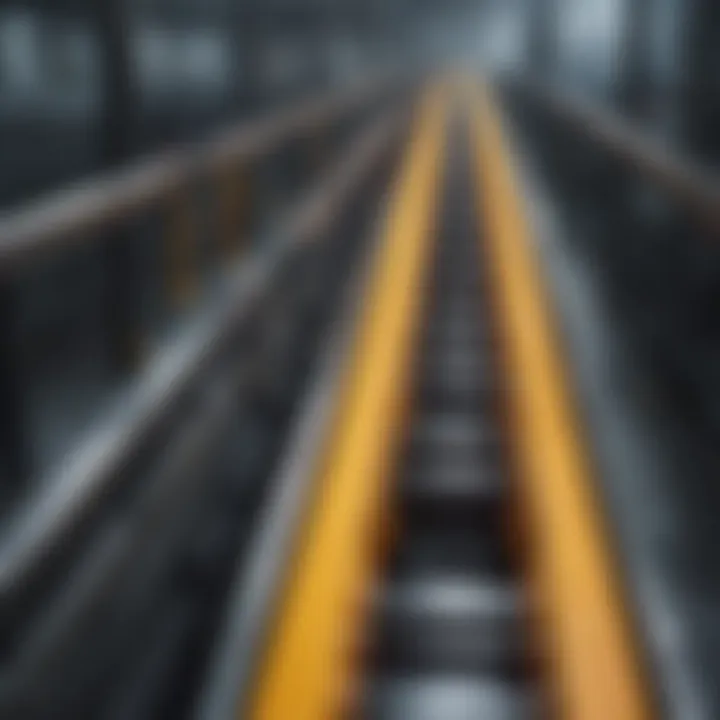
In summary, innovations in vibrating conveyor technology are vital for continued advancement in various industries. Automation, material developments, and sustainability efforts are key aspects driving this field forward. As these technologies evolve, they offer a clearer path toward achieving greater operational efficiency and environmental responsibility.
Challenges and Limitations
In the discourse surrounding vibrating conveyors, it is essential to acknowledge the challenges and limitations these systems encounter throughout their operational life. This section serves to outline the significant issues that impact the efficiency and effectiveness of vibrating conveyors in diverse applications. Understanding these challenges not only helps in designing better systems but also in optimizing their performance.
Wear and Tear
One of the most pressing challenges with vibrating conveyors is wear and tear due to continuous operation. The constant vibration applied to the materials can lead to gradual degradation of components, including springs, frames, and troughs. The amplitude and frequency of vibrations play critical roles in this aspect. If vibrations are excessively high, they can accelerate wear on the mechanical parts.
Regular maintenance schedules are vital to mitigate this issue. Examining components for signs of fatigue or damage can prevent unexpected breakdowns. Moreover, utilizing high-quality materials in the construction of vibrating conveyors can prolong their service life. It is also prudent to implement vibration monitoring systems that can provide real-time feedback on the health of key components.
Material Limitations
Vibrating conveyors must be designed to handle a wide range of materials, each with unique properties. However, certain materials might present difficulties due to their weight, size, or fragility. For instance, very fine or abrasive materials might wear down the conveyor's surfaces more rapidly. In contrast, heavy materials can exert significant stress on the conveyor systems, requiring careful consideration in design and operational parameters.
Additionally, the choice of components must match the properties of the materials being handled. If the conveyor is not suited for specific material characteristics, issues like blockages or improper flow can occur. Designers and operators must remain informed about the materials used to ensure they select appropriate vibrating conveyor configurations that accommodate these factors effectively.
Operational Constraints
Operational constraints can impose severe limitations on the performance of vibrating conveyors. These constraints may arise from environmental conditions, system integration, or operational schedules. For example, extreme temperatures or humidity levels can affect both the materials being processed and the functionality of the conveyor systems.
Furthermore, if a vibrating conveyor is part of a larger process, any delays or inefficiencies within the system can result in bottlenecks. Companies must consider these interconnected aspects when implementing vibrating conveyor solutions. Planning for flexible operation and integration can help in minimizing downtime and maximizing throughput in various settings.
โThe success of a vibrating conveyor system is contingent upon a comprehensive understanding of both its challenges and limitations.โ
Future Prospects of Vibrating Conveyors
The future prospects of vibrating conveyors present significant opportunities for advancement in various industries and applications. With the growing demand for efficient material handling and automation, vibrating conveyors are poised to evolve. Their fundamental importance lies not only in their current applications but also in their potential to meet the changing needs of industries. Several factors contribute to this evolution, including technological innovations, sustainability pressures, and the increasing complexity of supply chains. Understanding these elements can help stakeholders make informed decisions about investing in vibrating conveyor technology.
Market Trends and Projections
Recent data shows a steady increase in the adoption of vibrating conveyors across sectors such as food processing, mining, and recycling. Market research predicts that the global vibrating conveyors market will grow substantially in the coming years. This growth can be attributed to several trends, including:
- Increased Automation: Industries are embracing automation to enhance operational efficiency. Vibrating conveyors integrated with smart sensors and AI technology are becoming common, allowing for real-time monitoring and optimization.
- Demand for Flexibility: As production needs change, companies require adaptable systems. Vibrating conveyors offer the versatility necessary to handle various materials and changing operational demands.
- Growth in Recycling Initiatives: The ongoing focus on sustainability has led to more investments in recycling technologies. Vibrating conveyors play a crucial role in sorting and handling materials in recycling facilities.
Such trends indicate a positive trajectory for the market, suggesting that professionals should keep the latest developments in vibrating conveyors on their radar.
Research and Development Directions
Ongoing research and development in the realm of vibrating conveyors is crucial. Several key directions are taking shape:
- Material Science Advancements: Innovations in material science are leading to the development of lighter, more durable, and energy-efficient conveyor materials. This can help in reducing operational costs and enhancing lifespan.
- Enhanced Control Systems: Future research focuses on improving control mechanisms. More sophisticated algorithms can optimize vibration patterns, leading to better material flow and reduced wear.
- Sustainability Innovations: There is a growing emphasis on creating environmentally friendly vibrating conveyors. This includes using recyclable materials and developing energy-efficient operating systems.
Closure
The conclusion of this article plays a critical role in synthesizing the extensive information presented regarding vibrating conveyors. It serves as a pivotal summary of insights, revealing the essential nature of these devices in various industry applications. Emphasizing their mechanisms, functionality, and continuous innovations is crucial for readers to grasp their significance in modern logistics and material handling solutions.
Summarizing Key Insights
Vibrating conveyors are indispensable tools in numerous sectors. They effectively manage material handling, contributing to efficiency and productivity. Here are the key insights encapsulated in the article:
- Diverse Applications: From the food processing industry to mining, vibrating conveyors are utilized for transporting a wide range of materials. Their versatility is a significant advantage.
- Innovative Mechanisms: Understanding the underlying principles of vibration helps in appreciating how these conveyors function optimally. Different types, like electromagnetic and mechanical conveyors, cater to distinct needs.
- Future Trends: With ongoing technological innovations, including automation and smart technology, vibrating conveyors are evolving. Sustainability considerations also play an important role in the future of these devices and their applications.
The mentioned insights underline the vital role vibrating conveyors have in enhancing operational efficiencies across various industries.
Final Thoughts
The understanding gained from this article is applicable not just for professionals engaged in operations but also for researchers looking for future directions in material handling technology.
Vibrating conveyors are more than mere tools; they are the backbone of efficient material transport systems across countless industries.