The Role of Carbon Fiber in 3D Printing Innovation
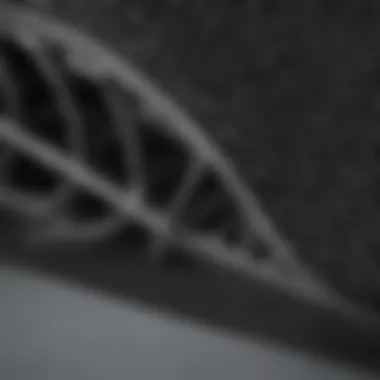
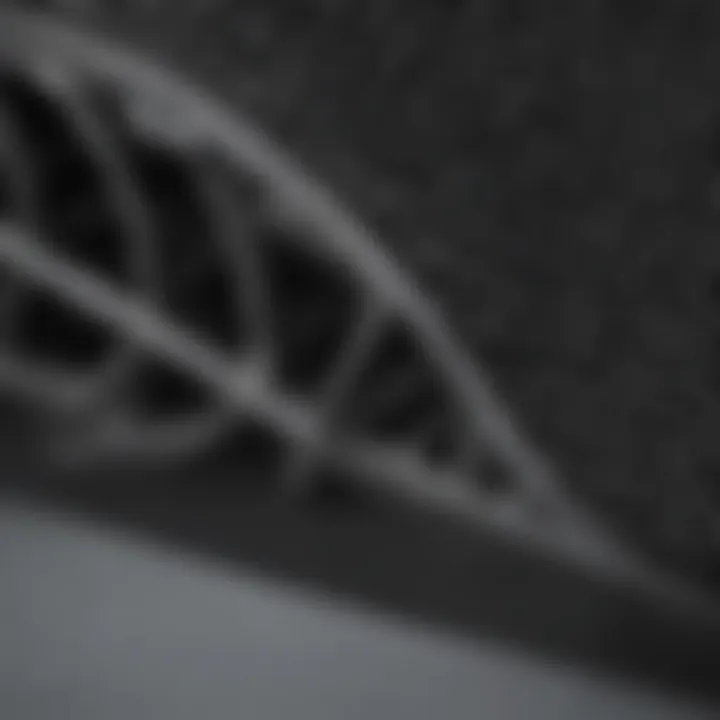
Intro
As industries continue to evolve, the quest for materials that blend strength, durability, and lightness has become a pivotal focus. One material gaining traction is carbon fiber. Best known for its high-performance characteristics, carbon fiber has found its way into various sectors, from aerospace to automotive. With the surge in 3D printing, it’s essential to understand how this material is influencing the landscape of additive manufacturing. This journey through the realm of carbon fiber as a 3D printing material will uncover its unique properties, diverse applications, and potential to reshape traditional manufacturing methodologies.
Research Overview
Summary of Key Findings
The examination of carbon fiber reveals several compelling traits:
- High Strength-to-Weight Ratio: Carbon fiber is lighter than steel yet significantly stronger, making it ideal for weight-sensitive applications.
- Durability and Longevity: This material exhibits excellent resistance to fatigue and provides impressive longevity under harsh conditions.
- Versatile Compatibility: When combined with thermoplastics or thermoset resins, carbon fiber enhances the performance of 3D printed parts.
- Customization Potential: The compound nature of 3D printing allows for complex geometries, which can be particularly beneficial for carbon fiber applications.
These findings suggest that carbon fiber not only complements existing manufacturing processes but also presents opportunities for innovation in product design and functionality.
Importance of the Research
Research into carbon fiber's role in 3D printing is crucial for several reasons. It provides valuable insights into:
- Cost Efficiency: As production processes evolve, exploring how carbon fiber can reduce material waste and lower costs is vital for businesses.
- Sustainability: The push for more sustainable manufacturing practices highlights the importance of materials like carbon fiber, which can be reused or recycled more effectively than traditional materials.
- Future Trends: Understanding current advances facilitates predicting new applications and technologies that may emerge, ensuring that businesses remain competitive.
Methodology
Study Design
To thoroughly investigate the effectiveness of carbon fiber in 3D printing, a mixed-method approach combining quantitative and qualitative analysis is utilized. This design allows for a comprehensive understanding of both the material properties and user experiences across different industries.
Data Collection Techniques
Data is gathered through:
- Surveys and Interviews: Engaging industry professionals and researchers offers first-hand perspectives on practical applications and challenges.
- Market Analysis: Studying market trends and adoption rates of carbon fiber in various sectors helps illuminate its impact.
- Experimental Testing: Conducting trials with different carbon fiber composites under various printing conditions yields critical performance data.
The synthesis of these methodologies enriches the understanding of how carbon fiber can influence the future of 3D printing.
This exploration into carbon fiber sheds light on both its practical advantages and its challenges within the manufacturing process. As technology advances, understanding the implications of using carbon fiber in 3D printing is not only timely but necessary.
Foreword to Carbon Fiber in 3D Printing
Carbon fiber has been capturing attention as a remarkable material in the world of 3D printing, and for good reason. Its unique interplay of strength and weight lets engineers and designers push boundaries in ways that other materials simply cannot. As industries evolve, they enthusiastically look to carbon fiber as a game changer in additive manufacturing, optimizing performance and productivity.
One of the major selling points of carbon fiber is its high strength-to-weight ratio. This quality means that parts made from this material can be both incredibly strong and significantly lighter than those made from traditional materials, like metals or even standard plastics. For example, in the aerospace sector, where every ounce matters, the utilization of carbon fiber can lead to impressive reductions in overall weight and, consequently, fuel consumption.
Additionally, the thermal stability associated with carbon fiber makes it a preferred choice for applications that experience significant temperature fluctuations. Think of automotive components that withstand under-hood conditions; carbon fiber not only endures heat but retains structural integrity, providing a real advantage.
"The introduction of carbon fiber into the 3D printing world is akin to finding a high-performance engine for a vehicle that previously relied on simple motors. It opens doors to new possibilities."
However, it’s worth noting that while carbon fiber shines in many areas, it also brings with it a set of specific challenges and considerations. The cost of carbon fiber materials can be prohibitively high compared to other options, making it less accessible for small-scale projects. Printability can also be a concern—the materials may require specialized equipment that not every 3D printing setup can handle.
In summary, understanding carbon fiber and its role in 3D printing is crucial for professionals looking to leverage additive manufacturing in contemporary industries. The right balance between performance and practicality is essential, and this is exactly where carbon fiber sits—promising unprecedented capabilities while demanding careful consideration.
The Nature of Carbon Fiber
Understanding carbon fiber is pivotal in so many discussions about modern manufacturing. As one of the frontrunners in composite materials, it showcases a unique concoction of characteristics that make it exceptionally suited for 3D printing. The fascination with carbon fiber is not simply about its cool factor. Its adoption in additive manufacturing stems from properties that significantly enhance performance in various applications. From the automotive industry whipping up lighter parts to drones that need to maintain precision in flight, carbon fiber is carving its niche.
Composition and Structure
At the core of carbon fiber's appeal lies its intricate composition. Essentially, carbon fiber is made up of long, thin strands of carbon atoms. These strands are typically around 5-10 micrometers in diameter, which is equivalent to about a seventh of a human hair. When these fibers are woven together, they form a structure known as a towp, giving rise to the exceptional material properties. The arrangement of carbon atoms leads to a crystal structure, enhancing stiffness and strength.
"The unique arrangement and bonding of carbon atoms are the backbone of what makes carbon fiber a heavyweight in the lightweight category.”
This structural prowess is crucial because it allows carbon fiber to maintain high performance under stress. This means manufacturers can create components that are not only strong but can also withstand various environmental factors, another advantage note in the realm of 3D printing.
Properties of Carbon Fiber
The properties that stem from the composition of carbon fiber truly set it apart in the field of 3D printing. Examining these characteristics can shine a light on why this material continues to gain traction in various sectors.
Strength and Stiffness
When discussing strength and stiffness, carbon fiber stands tall. It's one of those materials known for its impressive ability to endure loads without deformation. This makes it an excellent choice when creating components that require precision and reliability. For instance, in industries like aerospace, the necessity for lightweight yet robust materials is paramount. Carbon fiber provides that allure, allowing for constructions that do not compromise on strength.
One key characteristic here is the tensile strength, which refers to a material's resistance to being pulled apart. Carbon fiber possesses significantly higher tensile strength compared to metals such as aluminum. This leads to not just lighter designs, but also creates opportunities for innovative applications previously thought impossible. However, one must tread carefully, as it does have its downsides. If mishandled, carbon fiber can be brittle, leading to a higher likelihood of breakage under extreme conditions.
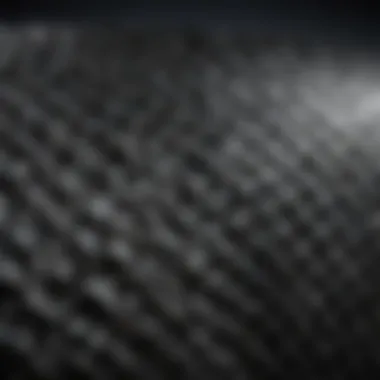
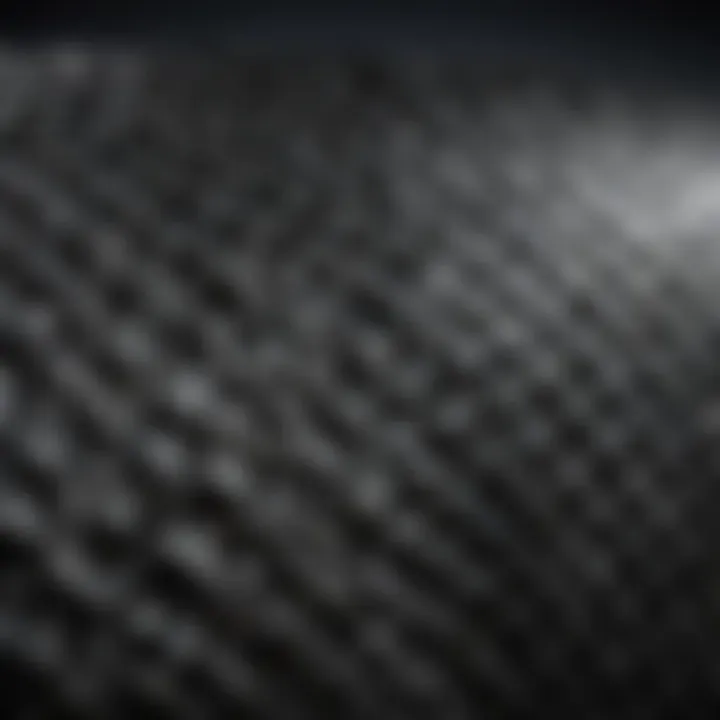
Weight-to-Strength Ratio
When people talk about the weight-to-strength ratio, carbon fiber often catches the eye due to its remarkable performance in this arena. This ratio is a key factor in determining how materials behave under weighty conditions. Carbon fiber’s ability to provide high strength while maintaining a low weight is crucial in applications ranging from sporting equipment to automotive components.
One unique feature of carbon fiber is its functionality in high-stress environments—where minimizing mass without sacrificing integrity is required. Take, for example, the aviation sector, where every gram counts toward fuel efficiency. The lightweight nature grants aircraft superior fuel performance while still being robust enough to endure the rigors of flight. Still, a critical point to highlight is its cost. While its advantages are clear, the price tag attached can make it less accessible compared to traditional materials, posing a barrier for some manufacturers.
Thermal Stability
Thermal stability is yet another feather in carbon fiber’s cap. The ability to maintain its properties across a wide temperature range is an attractive feature for many applications, most notably in high-performance engines and race cars. This property informs the decision to use carbon fiber in places subjected to intense changes in temperature, ensuring that performance stays consistent regardless of external conditions.
One of the highlights of this characteristic is its resistance to thermal expansion. Unlike metals that can warp under heat, carbon fiber retains its shape, which is a substantial asset for precision engineering. However, the downside is that carbon fiber can become challenging to process when subjected to thermal extremes during the print process itself. This means that while the finished product is stable, the printing requires careful considerations.
The distinctive nature of carbon fiber brings forth a significant dialogue about its role in additive manufacturing. Although there are hurdles to overcome regarding costs and print quality, the composite’s inherent characteristics present opportunities that have sparked interests across industries. As we delve deeper, we can explore how these properties translate into practical benefits and challenges when employed in 3D printing.
Additive Manufacturing Overview
The world of manufacturing has been shifting gears with the emergence of additive manufacturing, commonly known as 3D printing. This technology enables the creation of complex structures layer by layer, showcasing a flexibility that traditional manufacturing methods simply can't match. Especially when it comes to materials like carbon fiber, understanding additive manufacturing becomes crucial. Not only does it underscore the significance of 3D printing in modern applications, but it also reveals the multifaceted benefits and considerations involved.
Understanding 3D Printing
Techniques Used in 3D Printing
3D printing isn't a monolithic process; it’s an umbrella under which various techniques operate. Fused Deposition Modeling (FDM), for example, is widely recognized for its simplicity and affordability. This method involves extruding thermoplastic filament to build objects layer by layer. One key characteristic of FDM is its versatility; it's suitable for prototyping as well as small production runs, making it a popular choice in numerous sectors including aerospace and automotive.
However, FDM does have its quirks. The finish quality often leaves something to be desired, especially when compared to more intricate techniques like Stereolithography (SLA), which uses a laser to cure resin, yielding smoother surfaces. Yet, the trade-off generally revolves around cost and material options.
Another technique worthy of mention is Selective Laser Sintering (SLS). This method uses a laser to fuse powdered materials, providing exceptional strength and design freedom. Notably, SLS allows for intricate geometries that would be nearly impossible with traditional methods. However, the associated costs can be a barrier for smaller businesses or hobbyists.
Materials for 3D Printing
When it comes to materials for 3D printing, the choice is vast and varies depending on the application. Thermoplastics such as PLA and ABS are commonly utilized due to their ease of use and availability. They offer a favorable balance of strength and flexibility, yet some might argue they don’t measure up in demanding environments.
Here enters carbon fiber, which elevates the conversation. It’s not just about printing; it's about enhancing performance. Carbon fiber composites showcase not only high strength but also a low weight which is vital in industries where every gram counts, such as in aerospace. However, the unique feature of carbon fiber lies in its rigidity, ideal for parts that endure high levels of stress.
Yet, there’s a flip side; carbon fiber’s tendency to be more expensive and its poor impact resistance can pose challenges. Not to mention the printability aspects—sourcing quality carbon fiber composite filaments often requires navigating a complicated web of suppliers and specifications.
Market Growth and Innovations
The landscape of additive manufacturing is not stagnant. In fact, it's growing at an impressive rate. As industries continue to explore the capabilities of 3D printing, more players are entering the fray, leading to a surge in innovations. New techniques and materials are emerging, aiding in everything from the prototyping of consumer products to the creation of robust components for industrial machines.
The global push towards sustainability is also influencing this growth. Companies are feeling the pressure to adopt more environmentally friendly practices, and additive manufacturing can aid in this regard by minimizing waste and allowing for more efficient use of materials. Furthermore, specialized software and development tools are evolving, making the design and production process even more intuitive and accessible for engineers and designers alike.
"The shift towards additive manufacturing represents both a challenge and an opportunity within the industry, particularly with the integration of innovative materials like carbon fiber."
Overall, the overview of additive manufacturing reveals a dynamic interplay of techniques and materials, with carbon fiber standing out as a formidable candidate for optimal performance in a diverse range of applications.
Benefits of Carbon Fiber in 3D Printing
In the realm of 3D printing, the use of carbon fiber marks a significant advancement. This material brings a plethora of benefits that not only streamline production processes but also enhance the characteristics of the final product. Carbon fiber in additive manufacturing is compelling because it optimally combines strength with lightness, making it a valuable resource in various sectors. Some key advantages worth dissecting include enhanced performance related to structural integrity, cost-efficiency over traditional manufacturing methods, and remarkable versatility in its applications.
Enhanced Performance Characteristics
Carbon fiber reinforces the performance characteristics of 3D-printed items. Its strength rivals that of metals while weighing considerably less. When you craft components using carbon fiber, the result is a final product that can endure greater stress with minimal deformation. This remarkable feature of carbon fiber provides a cushion against failure in demanding environments. For instance, machinery parts made from carbon fiber composites exhibit superior longevity under repetitive loads, which is crucial in industries where reliability is non-negotiable.
Cost and Time Efficiency
Employing carbon fiber in 3D printing also translates to cost and time savings. While the material can demand a higher upfront investment, its durability leads to reduced maintenance costs over time. Additionally, the creation of components through additive manufacturing significantly cuts down on production time. Unlike traditional methods that often involve lengthy and elaborate processes, 3D printing can produce complex shapes in a single build, leading to shorter lead times for prototypes or final products. Thus, the initial expense can quickly be offset by the operational savings provided throughout the lifecycle of the product.
Versatility in Applications
The versatility of carbon fiber in 3D printing catalyzes its adoption across various sectors, allowing businesses to innovate and meet unique demands. This customization potential means that industries can create tailored solutions that align perfectly with their needs. Three noteworthy applications include:
Prototyping
When it comes to developing new products, prototyping with carbon fiber allows for rapid iteration with optimal resilience. The unique characteristics of carbon fiber, particularly its lightweight nature, facilitate the production of prototypes that can be tested rigorously without burdening them excessively. This property makes it a popular choice for engineers and designers seeking effective physical representations of their ideas on a budget. However, while carbon fiber remains a favorable choice, its cost may be a barrier for small-scale projects, demanding careful planning to harness its full potential.
Aerospace Industry
In aviation, carbon fiber 3D printing is revolutionizing component design and fabrication. The key characteristic here is the material's ability to withstand extreme conditions. Parts that are both lightweight and strong improve fuel efficiency and performance, which is a major advantage for manufacturers looking to optimize aircraft operations. Nonetheless, stringent safety standards and regulatory compliance can pose challenges, as every material used must pass rigorous testing protocols before it can be implemented in aircraft.
Automotive Sector
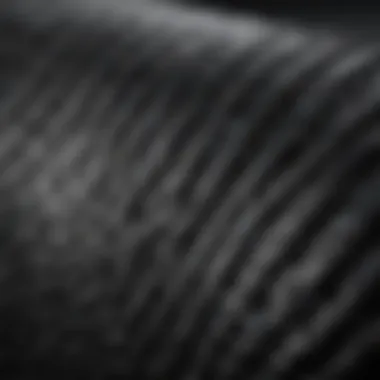
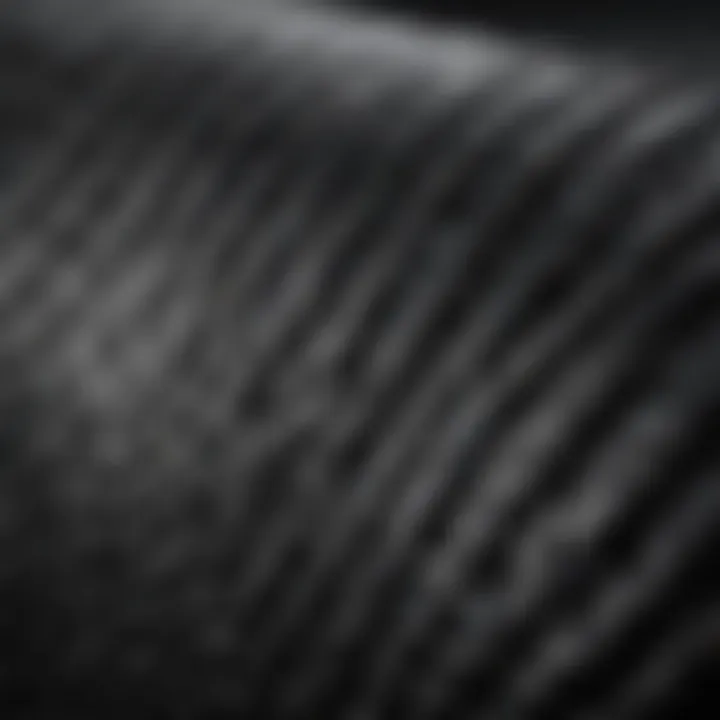
The automotive industry is benefiting significantly from incorporating carbon fiber into 3D printing processes. This sector values the lightweight and strong facets of the material, allowing for the creation of parts that enhance vehicle speed and fuel efficiency. Here, carbon fiber components can cut down on vehicular weights thereby improving overall performance on the road. The challenge, however, lies in balancing cost and performance, as carbon fiber can be more expensive than traditional materials, making it a premium choice for high-end models or performance vehicles.
“With the right balance of cost and performance, carbon fiber paves a new path for innovation across multiple industries.”
Challenges of Using Carbon Fiber in 3D Printing
While the significance of carbon fiber in 3D printing is clear, it comes with a set of challenges that cannot be ignored. These hurdles, ranging from material limitations to environmental concerns, play a crucial role in determining how effectively carbon fiber can be utilized within the realm of additive manufacturing. Not only do these challenges influence the perception of carbon fiber as a material, they also shape decisions made by designers and engineers when selecting it for specific applications. Understanding these challenges is essential for a holistic view of carbon fiber in this context.
Material Limitations
Cost Concerns
One of the more noticeable drawbacks of carbon fiber is its cost. Compared to other 3D printing materials like PLA or ABS, carbon fiber tends to carry a higher price tag due to the complex process involved in its production. The key characteristic here is the price per kilogram, which can cause a tight squeeze on budgets, especially for small businesses or hobbyists trying to enter the field.
This cost factor plays an essential part in limiting its broader adoption. While carbon fiber offers superior performance, its financial barrier can deter many from leveraging its benefits.
Interestingly, industries like aerospace and automotive, where performance takes precedence over cost, still heavily invest in carbon fiber. Its unique feature of incredible strength-to-weight ratio makes it a valuable asset, often outweighing those cost concerns. However, for general consumer-level applications, this elevated cost may be perceived as a disadvantage, reducing its appeal.
Printability Issues
The second hurdle that comes along with carbon fiber is associated with its printability. Not every printer is equipped to handle the intricacies of carbon fiber filaments. The notorious abrasiveness of carbon fibers can lead to wear and tear on print heads, particularly if they are not specifically designed for such materials.
This key characteristic of reduced compatibility means that those interested in using carbon fiber face the trouble of ensuring their existing equipment is up to the task, causing potential upgrade expenses and other logistical headaches.
In terms of unique features, one notable aspect of carbon fiber printability is the requirement for higher temperatures, which can complicate the printing process. Not only does this affect the quality of the final product, but it also heightens the risk of material warping during the process. Thus, while carbon fiber offers compelling advantages, these printability issues can prove frustrating to users and could limit its use in certain applications within the additive manufacturing spectrum.
Environmental Impact
An often overlooked aspect of carbon fiber usage in 3D printing pertains to its environmental sustainability. The manufacturing process for carbon fiber, notably its energy-intensive nature, tends to raise eyebrows among environmentally-conscious users. It’s not merely about the material itself but the broader implications associated with its production and waste.
The production of carbon fiber consumes significant energy, which contributes to higher carbon emissions when not sourced from renewable energy. Moreover, once carbon fiber products reach the end of their life cycle, the recycling options remain limited. Many users find themselves at a crossroads when considering both performance metrics and environmental responsibility.
While advancements in recycling technologies are underway, current methods often lead to challenges in reusing carbon fiber materials. Thus, as we continue to explore the application of carbon fiber in 3D printing, addressing these environmental concerns must be part of the deeper conversation.
"For all its advantages, integrating carbon fiber into 3D printing demands a careful assessment of cost, printability, and environmental impact to ensure a balanced approach."
Technological Advancements in Carbon Fiber 3D Printing
The realm of carbon fiber in 3D printing is not just a passing fad; it represents a significant leap forward in manufacturing capabilities. Technological advancements in this area are pivotal, as they enhance both the performance and versatility of carbon fiber as a printing material. With ongoing innovations, the potential applications and efficiency gains increase, making carbon fiber a serious contender in various markets.
Innovative Printing Techniques
With the integration of carbon fiber into additive manufacturing, new printing techniques have emerged. These methods do not merely replicate traditional approaches but have evolved to cater to the unique properties of carbon fiber. One notable innovation is the use of continuous fiber reinforcement. This method allows for the embedding of carbon fiber strands into the print layers, significantly improving mechanical properties without adding excessive weight.
Moreover, hybrid techniques combining various printing processes offer flexibility that was previously unattainable. For instance, combining Fused Deposition Modeling (FDM) with resin printing results in a composite material that takes advantage of both techniques to yield stronger and more resilient parts.
Benefits of these advancements include:
- Improved Performance: Parts created using these new techniques can withstand higher stresses and strains than those printed from traditional materials.
- Customization: With sophisticated software, users are able to fine-tune the placement of carbon fiber layers to suit specific applications.
- Rapid Prototyping: New methods enable quicker iterations in product design, which is crucial in industries like automotive and aerospace where precision and speed are paramount.
Post-Processing Methods
Once the printing phase is complete, the nature of carbon fiber necessitates specific post-processing methods that enhance the final product's properties. Traditional 3D-printed items often require little to no finishing, but carbon fiber components might need additional steps to unlock their full potential.
Common post-processing techniques include:
- Surface Smoothing: Carbon fiber objects can undergo sanding or chemical treatment to achieve a finer surface finish, which is especially important for aesthetic applications such as consumer products.
- Thermal Treatments: These techniques are intended to relieve internal stresses within the printed material and can improve the overall strength and stability. The right temperature and time duration must be carefully calculated, as overexposure can lead to degradation of properties.
- Coating: Applying protective coatings not only enhances appearance but also provides resistance against elements like corrosion or temperature changes.
Post-processing can sometimes be the difference between a good part and an exceptional one, allowing designers to really push the limits of what can be achieved with carbon fiber in 3D printing.
"Carbon fiber is not just about strength; it's about enabling new possibilities and applications that were previously outside our reach."
In summary, the advancements in printing techniques and post-processing methods significantly support the broader application of carbon fiber in 3D printing. As technology evolves, it offers new horizons for innovation and efficiency in manufacturing processes.
Comparative Analysis with Other Materials
In the fast-evolving world of additive manufacturing, understanding how carbon fiber stacks up against other commonly used materials is crucial. The comparative analysis of carbon fiber, especially against materials like PLA and ABS, sheds light on its unique benefits and considerations. This section aims to explore the key differences, helping students, researchers, and professionals make informed choices depending on their project requirements.
Carbon Fiber vs. PLA
When we line up carbon fiber against polylactic acid, or PLA, it's like comparing apples to oranges. While PLA is well known for its ease of use and environmentally friendly profile, carbon fiber brings a party that is all about toughness and durability.
- Strength and Stiffness: Carbon fiber boasts exceptional tensile strength. It can withstand significant forces without deforming, making it suitable for structural components. On the other hand, PLA, while strong, cannot hold a candle to carbon fiber’s load-bearing capacities. This makes carbon fiber preferable for applications that demand rigidness, such as parts for drones or automotive components.
- Ease of Printing: PLA is often celebrated for its user-friendliness; it prints at lower temperatures and adheres well to the build surface. Carbon fiber's abrasive nature poses challenges—special nozzles are typically required to avoid wear and tear on standard equipment, complicating its use a tad for beginners.
- Environmental Factors: PLA is derived from renewable sources like corn starch, which gives it a green badge. In contrast, carbon fiber is not as sustainable by frosty comparisons; it requires more energy to produce and poses recycling hurdles.
In summary, if one is crafting prototypes or parts where ease of use and environmental impact matters, PLA may be the pick. However, when the chips are down, and performance is critical, carbon fiber takes the cake.
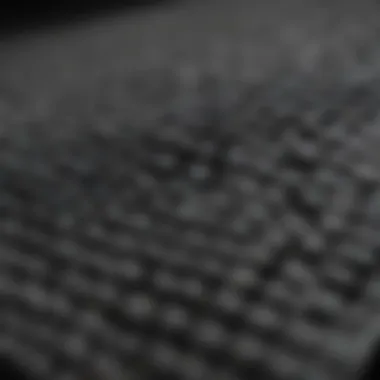
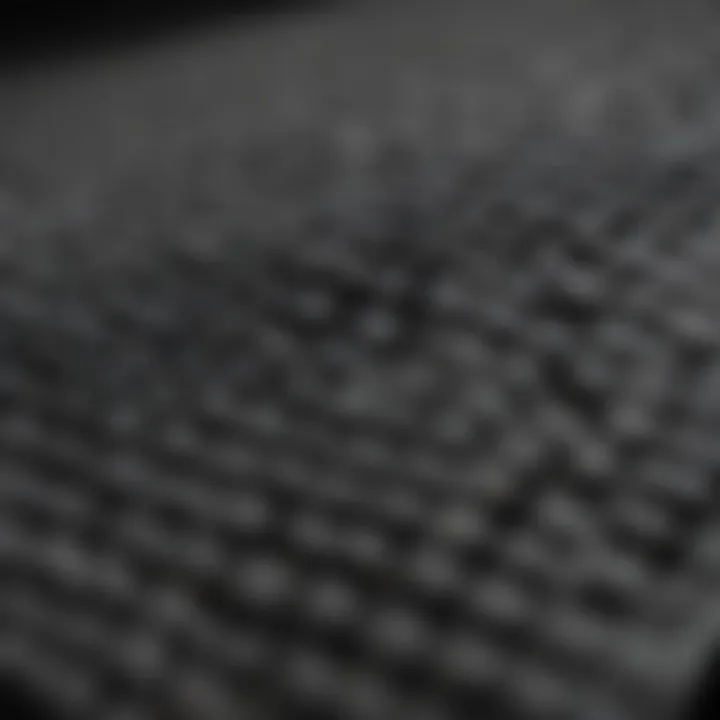
Carbon Fiber vs. ABS
Next up, let's pit carbon fiber against acrylonitrile butadiene styrene, or ABS. ABS is often crucial in the world of 3D printing due to its strong impact resistance and ability to be polished or acetone smoothed to a shiny finish. Yet, here too, carbon fiber holds its own in different ways.
- Mechanical Properties: Carbon fiber stands tall with superior strength-to-weight ratios compared to ABS, meaning it can deliver better performance while being lighter. This is a key factor in fields like aerospace where every gram counts.
- Heat Resistance: ABS holds up pretty well against heat, but carbon fiber’s thermal properties often surpass those of ABS in high-temperature applications. This can be pivotal for industrial uses where temperature fluctuations are common.
- Cost Factors: ABS, often more accessible and cheaper, may initially seem attractive for larger batch productions. However, its longevity is often overshadowed by carbon fiber in demanding applications, making carbon fiber a more cost-effective long-term option in specialized sectors.
"Understanding the unique attributes of carbon fiber compared to other materials provides a roadmap for its effective implementation in various applications."
Through this comparative lens, it's evident that selecting the right material hinges on the specific needs, production scales, and performance expectations of the project at hand. By taking the time to analyze these aspects, users can ensure they’re not just filling a quota but achieving their design goals with precision.
Real-World Applications of Carbon Fiber 3D Printing
Carbon fiber 3D printing is making waves across multiple sectors, a trend that's worth some serious attention. This material is not just for high-end racing cars or aerospace but is gradually weaving itself into everyday products. Understanding these real-world applications sheds light on the material's significance alongside its advantages.
From prototypes that mold the future of consumer goods to components used in heavy industries, carbon fiber offers an enticing blend of properties that are tough and lightweight, making it a go-to choice for various stakeholders. The implications of this can be seen not just in performance but in sustainability and efficiency as well.
Consumer Products
The consumer product market is where carbon fiber really stretches its legs. Imagine a bicycle frame crafted from this strong yet lightweight material. It's not just about being cool; it's about improved performance. Cyclists looking for speed and agility are especially drawn to these high-end bikes.
- Durability: Products made from carbon fiber endure rigorous use without losing integrity. Consider luggage, for instance. Carbon fiber suitcases withstand the rough and tumble of travel while remaining lightweight.
- Aesthetic Appeal: The sleek, modern look of carbon fiber is an attractive selling point. Products like smartphone cases or wearable tech benefit not just from functionality but also from the high-tech vibe that carbon fiber brings.
A deeper dive into the real-world applications reveals:
- High-performance sports gear, such as carbon fiber tennis rackets and golf clubs, improving athletes' performance.
- Personal items like custom headphones or eyewear frames that mix style with utility.
In the consumer sphere, 3D printing allows for customization that was previously unimaginable. Think about the growing trend of bespoke products. Potential customers can now order items tailored to their own preferences, incorporating different designs and personal touches. This customization wave is all set to transform how products reach consumers.
"Carbon fiber not only delivers strength but also has a thermal performance edge that enhances functionality in consumer products."
Industrial Components
When we shift gears to the industrial side of things, carbon fiber 3D printing is revolutionizing how components are made. The manufacturing process in sectors like aerospace or automotive is typically labeled as meticulous. Traditional manufacturing methods often struggle with intricate designs. However, the introduction of carbon fiber in 3D printing lends itself to intricate geometries while maintaining performance characteristics.
Key considerations include:
- Cost-Effective Solutions: Despite the initial investment in carbon fiber materials, the long-term savings in durability and maintenance catch the eye of industry leaders. These components often last longer, leading to reduced replacement costs.
- Rapid Prototyping: Engineers can create prototypes fast and efficiently, shortening the cycle from concept to production. With carbon fiber's robust nature, prototypes can be tested vigorously before any final design is chosen, aiding in refining their projects more effectively.
Some prominent examples of application in the industrial sector are:
- Aircraft parts that demand low weight but high strength, such as brackets and fuselage components. These are often subjected to rigorous stress, and carbon fiber products have repeatedly proven their mettle.
- Automotive components, particularly in high-performance cars that benefit from weight-saving features without facing a drop in safety and reliability.
As this technology continues to evolve, it’s clear that carbon fiber could reshape not only products but entire industries. Understanding how it fits into the ecosystem of manufacturing highlights its potential for growth.
Future Prospects of Carbon Fiber in Additive Manufacturing
The landscape of additive manufacturing is continuously evolving, and carbon fiber stands out as a noteworthy player in this arena. Its unique characteristics—chief among them, exceptional strength, light weight, and durability—position it as a material of choice for future advancements in 3D printing. Understanding the prospects of carbon fiber is pivotal, especially as the technology and its applications enhance across various sectors.
Emerging Trends
Several trends are bubbling to the surface in the world of carbon fiber and 3D printing. These include:
- Increased Automation: As the demand for carbon fiber components rises, automation in the production process is becoming essential. This shift is particularly relevant in industries like aerospace and automotive, where precision and efficiency are crucial. Automated systems can reliably output high-quality components while reducing waste.
- Integration with Smart Technologies: The intersection of carbon fiber 3D printing and smart technology is creating opportunities for innovative materials that adapt and respond to environmental factors. Consider materials that change color or structure based on temperature or stress; such advancements could revolutionize both aesthetics and functionality in products.
- Sustainability Focus: With a growing emphasis on reducing environmental impact, manufacturers are looking toward biobased resins or recycling processes for carbon fiber. Using eco-friendly feedstocks in the production of carbon fiber composites can mitigate some ecological concerns traditionally associated with the material.
In these rapidly changing times, the ability to stay ahead of trends could very well define the success of businesses utilizing carbon fiber.
Potential for Wider Adoption
Much like throwing a pebble into a pond, the ripples created by carbon fiber in 3D printing extend beyond immediate applications. The potential for wider adoption is clear, and several factors contribute to this:
- Cost Reduction: As production techniques improve and technology matures, the cost of carbon fiber materials is expected to decrease, making them accessible to smaller businesses and hobbyists alike. In an economy that often craves innovation without breaking the bank, affordability stands to fuel broader usage.
- Customization Opportunities: Consumers increasingly desire tailored solutions. Carbon fiber's versatility allows for customization in design and functionality, which is a big draw for industries ranging from aerospace to healthcare. Manufacturers can create lightweight, strong, and unique parts tailored to specific needs, tapping into a market that's hungry for bespoke offerings.
- Educational Outreach: More education and awareness about carbon fiber manufacturing techniques among students and professionals alike can drive interest. As educational institutions and vocational centers introduce relevant programs, a new generation of makers could choose carbon fiber as their go-to material, fostering skilled labor in this domain.
"The advances in carbon fiber 3D printing will not only change how products are made but also what those products might become entirely."
The future is bright for carbon fiber in additive manufacturing, with a host of exciting developments just on the horizon. As businesses and industries adapt, the integration of this material could very well reshape manufacturing processes, leading to more innovative and efficient ways to produce a wide array of products.
Finale
In wrapping up our exploration of carbon fiber as a 3D printing material, it's clear this subject holds significant weight in both current practices and future avenues of manufacturing.
One cannot overlook the multifaceted benefits carbon fiber brings to the table. Its unique combination of strength and lightweight properties makes it an attractive choice for industries that prioritize performance without the bulk. Consider aerospace, for instance, where maximizing fuel efficiency is paramount. The ability to create parts that are both robust and feather-like can transform how aircraft operate.
Moreover, the versatility of carbon fiber finds its place not just in high-tech industries but also in everyday consumer products. Whether it be sports equipment or automotive components, the implications are vast. Here are some key takeaways regarding the importance of carbon fiber in 3D printing:
- Enhanced Strength without Extra Weight: Carbon fiber's lightweight nature paired with its impressive strength enhances product longevity and functionality.
- Economic Feasibility in Prototyping: The cost efficiencies realized in the prototyping phase allow businesses to test designs without burning a hole in their pocket.
- Innovation Potential: As technology progresses, innovations in carbon fiber processing and application pave new paths, encouraging wider adoption across different fields.
Still, challenges linger; issues such as printability and environmental impacts can't be brushed aside. These considerations are crucial for stakeholders. The need for continuous dialogue on sustainability and improving the material's adaptability is a conversation worth having. As researchers and industries alike explore new frontiers, carbon fiber’s journey in additive manufacturing isn’t just a fleeting trend; it’s shaping the landscape of how we approach production at large.
In summary, the prospects for carbon fiber in 3D printing are encouraging. By bridging material science with innovative printing techniques, we can anticipate a future where carbon fiber isn’t just an option, but a staple in countless applications. As we look ahead, both enthusiasm and caution must guide our explorations—balancing innovation with responsibility.