Corrosion Inhibitors and Their Role in Oil & Gas
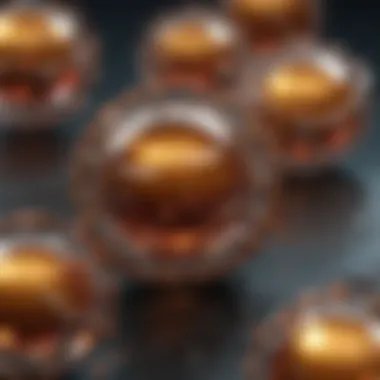
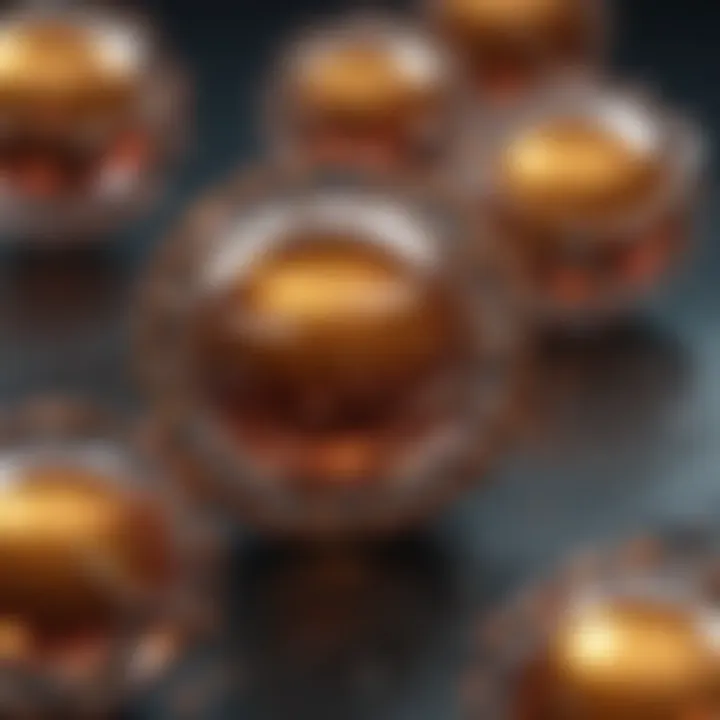
Intro
Corrosion inhibitors play a pivotal role in safeguarding the infrastructure within the oil and gas industry. These materials are formulated to slow down the natural process of corrosion, which can lead to significant operational hazards and financial losses. As pipelines, drilling rigs, and storage facilities remain exposed to harsh environments, the demand for effective corrosion management strategies has become crucial.
This section provides a researched overview concerning the impact and relevance of corrosion inhibitors. The insights drawn here will guide industry professionals, educators, and researchers in understanding both the mechanisms at play and the importance of implementing these protective measures.
Research Overview
Summary of Key Findings
Corrosion is responsible for a staggering amount of economic loss annually across many industries, particularly in oil and gas. Effective inhibitors can mitigate such losses by providing a protective barrier against corrosive agents in the environment. Key studies reveal that the application of corrosion inhibitors can reduce maintenance costs and prolong the lifespan of equipment significantly.
"The application of corrosion inhibitors often leads to a lower likelihood of equipment failure, which is particularly beneficial in the oil and gas sector where operational downtime can be extraordinarily costly."
Recent advancements in inhibitor technologies focus on:
- Bio-based inhibitors: Harnessing natural materials to provide non-toxic alternatives.
- Smart inhibitors: Employing nanotechnology for targeted corrosion prevention.
- Multi-functional inhibitors: Delivering additional benefits such as scale prevention or biocide properties.
Importance of the Research
The importance of this research cannot be overstated. Corrosion management directly influences operational efficiency, environmental safety, and economic viability. As oil and gas continue to be fundamental energy sources, understanding the tools available to reduce corrosion risks holds paramount importance for its sustainability. This research contributes to a deeper comprehension of corrosion inhibitors, thus paving the way for optimized use in the field.
Methodology
Study Design
The examination of corrosion inhibitors involves a multi-faceted approach that encompasses both laboratory experiments and field studies. This dual approach ensures comprehensive data that addresses varying conditions found in the oil and gas sector.
Data Collection Techniques
Data collection in corrosion research often involves:
- Field measurements: Assessing actual corrosion rates and inhibitor performance in real-world settings.
- Laboratory simulations: Creating controlled environments that mimic corrosive conditions to test different inhibitors.
- Surveys and case studies: Gathering qualitative data from industry practitioners about their experiences and challenges with corrosion inhibitors.
By synthesizing both quantitative and qualitative data, researchers can derive actionable insights for better corrosion management.
Prelude to Corrosion in Oil and Gas
Corrosion presents a significant challenge in the oil and gas industry. As pipelines, rigs, and storage facilities age, they encounter environmental factors that promote corrosion. This process can lead to catastrophic failures, environmental disasters, and considerable financial losses. Thus, understanding corrosion and appropriate management strategies focused on corrosion inhibitors is crucial.
In this article, we will examine the complexities of corrosion within this vital sector. Special emphasis will be placed on the role of corrosion inhibitors—compounds that mitigate degradation—and their mechanisms. Additionally, we will discuss the economic impacts of corrosion and how effective management strategies can enhance the longevity and safety of oil and gas operations.
What is Corrosion?
Corrosion is a natural process whereby metals deteriorate due to chemical reactions in their environment. It occurs when metal surfaces react with environmental elements like oxygen and moisture, leading to oxidation. In the oil and gas industry, corrosion is often accelerated by the presence of various chemicals, including acids and salts, which are inherent in crude oil and natural gas.
Common forms of corrosion that affect oil and gas operations include:
- Uniform Corrosion: Even deterioration over a large area.
- Pitting Corrosion: Localized, creating small pits on the metal surface.
- Stress Corrosion Cracking: Cracks forming under mechanical stress.
- Microbiologically Induced Corrosion: Caused by microorganisms that create corrosive byproducts.
Each type has distinct characteristics and may require tailored corrosion management strategies.
Importance of Managing Corrosion
Managing corrosion is not merely a technical requirement; it is vital for operational success and sustainability in the oil and gas industry. The expenses associated with corrosion are steep, potentially exceeding billions in repairs, lost production, and environmental remediation. According to various studies, the total cost of corrosion in North America alone amounts to over 300 billion dollars annually.
Effectively managing corrosion has several benefits:
- Enhanced Equipment Longevity: Reduces the frequency of repairs and replacements.
- Improved Safety: Minimizes risks of leaks and catastrophic failures.
- Environmental Protection: Mitigates the risk of spills and contamination.
- Cost Savings: Alleviates the financial burden of direct repairs and indirect costs from lost production.
Overall, a strategic approach to corrosion management, facilitated by corrosion inhibitors, is indispensable for businesses that operate in this sector. By understanding the nature of corrosion and applying the right inhibitors, companies can safeguard their assets and contribute responsibly to the energy industry.
Types of Corrosion in Oil and Gas Operations
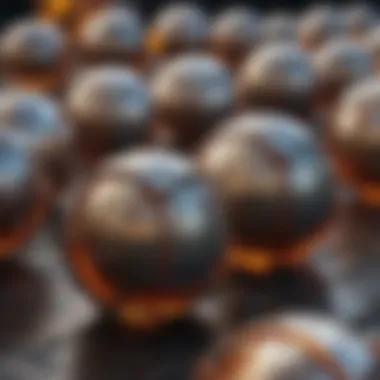
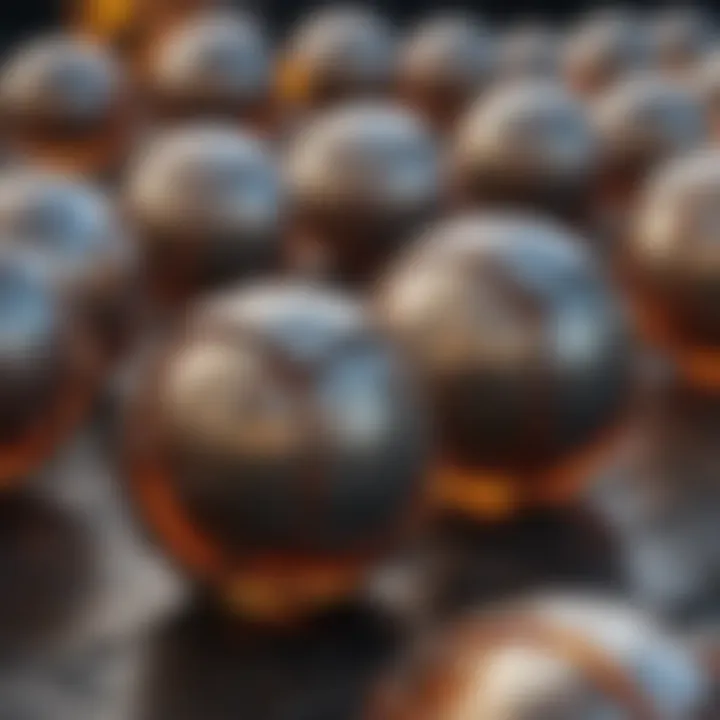
Understanding the different types of corrosion that occur in oil and gas operations is crucial for effective management and utilization of corrosion inhibitors. Each type presents unique challenges and risks that can significantly affect equipment lifespan, operational efficiency, and safety. Recognizing these corrosion types allows for targeted prevention and mitigation strategies, ultimately reducing costs associated with maintenance and failure. The types of corrosion prevalent in the oil and gas industry are varied, but four main forms are particularly significant: uniform corrosion, pitting corrosion, stress corrosion cracking, and microbiologically induced corrosion.
Uniform Corrosion
Uniform corrosion is considered one of the most straightforward types to understand and manage. This type occurs evenly across the surface of metals exposed to corrosive environments. Factors such as temperature, pH, and the presence of corrosive agents influence its rate. In oil and gas operations, uniform corrosion commonly affects carbon steel and can lead to significant material loss if not monitored. While it is sometimes easier to predict, its potential to cause widespread damage means that consistent monitoring and the application of corrosion inhibitors are necessary to extend material life.
Pitting Corrosion
Pitting corrosion is more localized and severe than uniform corrosion. It manifests as small holes or pits on the metal surface, which can lead to catastrophic failure if not addressed promptly. The complexity of pitting corrosion lies in its unpredictable nature; small pits can appear suddenly and grow rapidly. In oil and gas facilities, factors such as chloride ions significantly accelerate this type of corrosion. The localized attacks can compromise structural integrity in critical areas, thus highlighting the need for tailored corrosion inhibitors designed to combat this specific hazard.
Stress Corrosion Cracking
Stress corrosion cracking (SCC) is another critical type of corrosion that necessitates careful monitoring and management. SCC is influenced by tensile stress, which can be from the material itself or external sources. It occurs in particular environments and can be exacerbated by factors such as temperature and the presence of specific chemicals, particularly chlorides. In oil and gas operations, pipelines and pressure vessels are often vulnerable. Early detection and appropriate inhibitors are essential to mitigate risks associated with SCC. Ignoring this type of corrosion can lead to severe consequences, including leaks or ruptures.
Microbiologically Induced Corrosion
Microbiologically induced corrosion (MIC) involves the activity of microorganisms such as bacteria and fungi that produce corrosive byproducts. This type of corrosion is often found in wet environments, such as storage tanks or pipelines. The presence of microbes can accelerate traditional corrosion processes and create localized corrosion effects. The management of MIC is complex, requiring continuous monitoring and the application of biocides along with corrosion inhibitors. Companies must remain vigilant in identifying and controlling microbial growth to prevent significant infrastructure damage and maintain operational efficiency.
Understanding Corrosion Inhibitors
The topic of corrosion inhibitors is vital in addressing the ongoing challenges within the oil and gas industry. Corrosion can lead to significant operational failures, safety hazards, and economic losses. Hence, understanding corrosion inhibitors is not just a technical necessity but a strategic imperative. By employing these chemical agents, companies can extend the lifespan of equipment, decrease maintenance costs, and ensure safety compliance.
Definition and Function
Corrosion inhibitors are substances that, when added in small amounts to an environment, significantly reduce the rate of metal oxidation. This function serves as a protective barrier, preventing detrimental reactions with corrosive agents, which are often present in the oil and gas sector.
There are two main categories of corrosion inhibitors: active and passive.
- Active inhibitors react directly with metal surfaces to form a protective film.
- Passive inhibitors modify the chemical environment, reducing corrosion potential.
The importance of understanding the definition and function of these materials cannot be overstated. Without this knowledge, proper application and effectiveness measurement risk being compromised, leaving installations vulnerable to corrosion failures.
Mechanisms of Action
The effectiveness of corrosion inhibitors stems from various mechanisms that help mitigate corrosion. Here’s a deeper look into some of these mechanisms:
- Film Formation:
Many inhibitors function by adsorbing onto metal surfaces and creating a physical barrier. This barrier can significantly slow down corrosion reaction rates by acting as a shield against corrosive agents. - Surface Modification:
Certain inhibitors can alter the surface properties of metals, increasing their resistance to oxidation and reducing the rate of wear and tear. - Electrochemical Reduction:
Some inhibitors can participate in electrochemical reactions, favorably changing the reaction kinetics of metal oxidation processes. - Ion Exchange:
Inhibitors can also create a localized environment that is less conducive to corrosion through ion exchange mechanisms, further protecting the metal substrate.
Understanding these mechanisms equips professionals and researchers with the knowledge needed to select the right inhibitors for specific applications.
"A comprehensive understanding of the mechanisms of action behind corrosion inhibitors is crucial for optimizing their use in industry applications."
By grasping how these inhibitors work, stakeholders can make informed decisions that lead to better corrosion management strategies, ultimately increasing operational efficiency and safety.
Types of Corrosion Inhibitors
Understanding the types of corrosion inhibitors is essential for effectively managing corrosion in the oil and gas industry. Each type comes with its specific characteristics, benefits, and considerations. Selecting the right kind of inhibitor can greatly influence the operational efficiency and longevity of equipment. Corrosion inhibitors are categorized broadly into three main types: organic, inorganic, and volatile.
Organic Corrosion Inhibitors
Organic corrosion inhibitors consist of carbon-containing compounds. These compounds often create a film on metal surfaces, providing a protective barrier against corrosive agents. Their primary advantage is the ability to self-assemble on surfaces, enhancing their protective qualities. Common examples include amines, fatty acids, and esters.
The performance of organic inhibitors can be affected by several factors, including the pH level and temperature of the environment. They are generally effective in specific conditions, making careful evaluation necessary prior to their application. One key benefit is their low toxicity, which aligns well with environmental regulations.
However, it's important to be cautious, as some organic inhibitors can be soluble in the medium, which can reduce effectiveness over time. These inhibitors find applications in various oil and gas processes, such as refining and production, due to their effectiveness against uniform and pitting corrosion.
Inorganic Corrosion Inhibitors
Inorganic corrosion inhibitors, unlike their organic counterparts, do not contain carbon. They often include metal salts, phosphates, and silicates, each contributing different mechanisms of protection. For instance, zinc salts can impede the electrochemical process that leads to corrosion.
These inhibitors are typically more effective in high-temperature environments and can function well in acidic conditions. They also tend to be more stable and have a lower chance of being washed away. Their application can lead to significant cost savings, since they provide robust protection over extended periods.
Nevertheless, inorganic inhibitors may introduce complexities related to disposal and environmental safety. This necessitates adherence to safety standards and regulatory requirements. Overall, they serve as a compelling option for instances where resilience and longevity against corrosion are required.
Volatile Corrosion Inhibitors
Volatile corrosion inhibitors (VCIs) are unique in that they work by releasing vapor into the air surrounding the protected substrate. This vapor then condenses on the surface, forming a protective film. VCIs are particularly beneficial when dealing with enclosed spaces, where static air can aid the retention of the inhibitor.
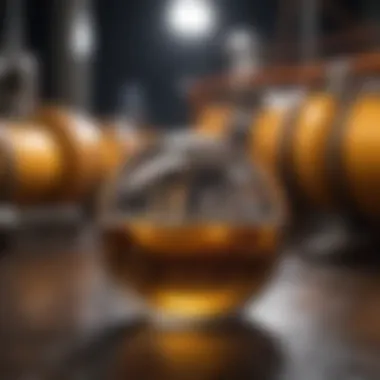
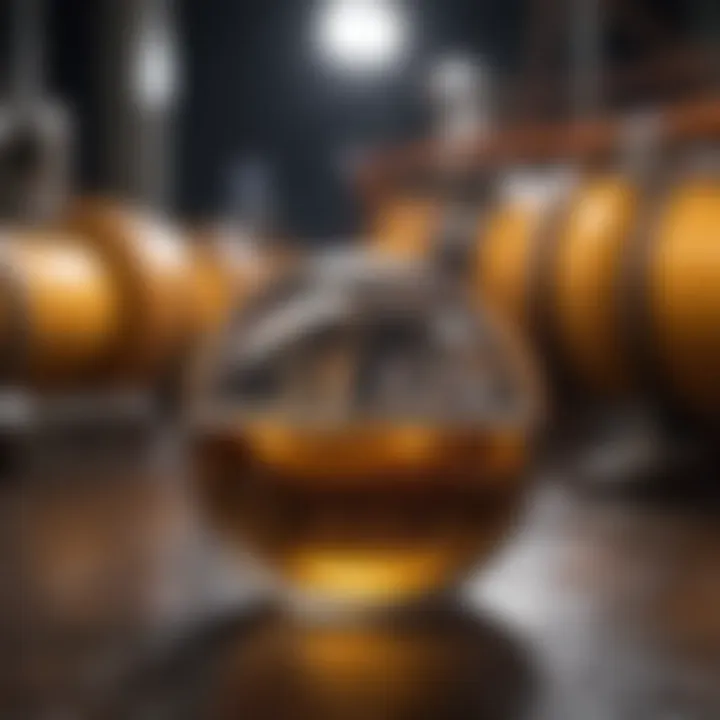
The primary advantage of VCIs is their ease of application and excellent long-term protection. They are often used in packaging and storage scenarios for components that may be exposed to moisture and air. Examples of VCIs include amines and certain aldehydes that are designed specifically for corrosion protection.
However, users should consider the potential health impacts and environmental issues related to VCIs. It's important to study the specific requirements and apply these inhibitors properly to maximize effectiveness. In the oil and gas sector, their application is primarily seen in storage units and in the transportation of equipment.
Ultimately, selecting the appropriate type of corrosion inhibitor can have direct implications on cost efficiency, equipment longevity, and operational safety. Knowledge about the different categories aids industry professionals in making informed choices that align with their specific operational requirements.
Application Methods for Corrosion Inhibitors
The application methods for corrosion inhibitors are essential to understand for effective corrosion management in the oil and gas industry. These methods dictate how inhibitors are applied, chosen based on the specific operational conditions and types of corrosion encountered. Knowing these methods allows for tailored solutions that optimize the protection afforded by corrosion inhibitors. Careful selection of the application method can lead to improved efficiency and reduced long-term costs.
Batch Treatment
Batch treatment involves the periodic addition of corrosion inhibitors to a system, often in large doses. This method can be particularly useful in scenarios where there are predictable operational cycles. For instance, during downtime in processing facilities or pipeline systems, operators can introduce a concentrated dose of the inhibitor to combat corrosion effectively.
The intermittent nature of batch treatment makes it easier to manage resources and minimizes the risk of overuse or underuse, thus optimizing chemical usage. However, this method requires careful timing, as improper scheduling might lead to less effective corrosion prevention. It is crucial that monitoring occurs to gauge the efficacy of the treatment over time. Moreover, the potential for system contamination must be considered, as the addition of external substances can affect the integrity of existing operational processes.
Continuous Injection
Continuous injection represents a more active approach in which corrosion inhibitors are gradually introduced into the system. This method is often preferred in environments with consistent flow, such as pipelines and storage tanks. Continuous injection ensures that there is a constant level of inhibitor present, which can be critical for maintaining operational integrity in high-risk corrosion areas.
The benefit of this application method lies in its ability to adapt to varying flow rates and conditions. Automated systems can regulate the amount of inhibitor injected based on real-time sensors monitoring the corrosive environment. However, continuous injection might require more upfront investment in equipment and monitoring systems to ensure precise dosing. There is also the need for regular calibration and maintenance to prevent issues that may arise from system wear or clogging.
Coatings and Linings
Coatings and linings are passive methods of corrosion prevention, relying on the application of protective layers on metal surfaces. These coatings can be comprised of various materials, including epoxy, polyurethane, or zinc-based formulas. They serve as a barrier that shields the base metal from corrosive agents and environmental stressors.
This method can be particularly effective for equipment in harsh environments. Regular maintenance is crucial to ensure the integrity of the coatings, as wear and tear can lead to compromised protection. Moreover, while coatings can greatly enhance outcomes, they do not entirely replace the need for inline inhibitors. Instead, they work in conjunction to offer a comprehensive approach to corrosion management.
In summary, understanding the various application methods for corrosion inhibitors is vital for optimizing corrosion management strategies in the oil and gas industry. Each method has its unique benefits and challenges, making it essential to choose the right approach based on specific operational needs.
Effectiveness of Corrosion Inhibitors
The effectiveness of corrosion inhibitors is a pivotal aspect within the oil and gas industry. It not only determines the longevity of pipelines, tanks, and equipment, but also has significant implications for safety and cost management. Understanding how these inhibitors work and their limitations allows for better operational decisions. Hence, assessing their effectiveness becomes essential for anyone involved in the production and distribution processes.
Corrosion inhibitors function to minimize the rate of corrosion on metal surfaces exposed to harsh environments. Beyond merely halting deterioration, they contribute to operating efficiency. Effective inhibitors can lower maintenance costs, prolong equipment life, and ultimately enhance profitability. However, the variable performance of different inhibitors necessitates a nuanced approach to their application.
===
Factors Influencing Effectiveness
Several factors influence the effectiveness of corrosion inhibitors in oil and gas operations. Understanding these elements helps in choosing the right product for specific conditions.
- Chemical Composition: The inherent properties of the inhibitor, including its polarity and solubility, dictate its ability to adhere to metal surfaces. Organic inhibitors may offer different performance characteristics than inorganic ones.
- Environmental Conditions: Factors such as temperature, pH level, and the presence of impurities can significantly influence inhibitor performance. A higher temperature might increase reaction rates, leading to either enhanced effectiveness or accelerated degradation of the inhibitor.
- Application Method: The method used to apply the inhibitor, whether batch treatment or continuous injection, affects its distribution and efficacy. An improper method may lead to localized corrosion, even when an inhibitor is used.
- Concentration: The concentration of the corrosion inhibitor is critical. Too little may be ineffective, while too much could lead to adverse chemical reactions or higher costs without proportional benefits.
- Duration of Exposure: The amount of time the inhibitor is allowed to act on the surface also plays a role. Short exposure may not give it time to form a protective barrier, whereas prolonged use might yield better results.
"Choosing the right corrosion inhibitor requires a comprehensive understanding of the operational environment and challenges."
Determining the optimal conditions for inhibitor effectiveness requires careful observation and adjustment.
===
Performance Measurement Techniques
To assess the effectiveness of corrosion inhibitors, performance measurement techniques must be employed. These techniques gauge how well inhibitors prevent corrosion over time under specific conditions.
- Weight Loss Measurements: This method involves measuring the weight change of test samples before and after exposure to corrosive environments. A lower weight loss indicates better performance of the inhibitor.
- Electrochemical Tests: Techniques such as linear polarization resistance (LPR) and electrochemical impedance spectroscopy (EIS) can provide real-time insights into corrosion rates. These methods help to determine the protective layers formed by inhibitors effectively.
- Visual Inspection and Ultrasonic Testing: Regular visual checks and ultrasonic thickness measurements can help identify any corrosion beneath protective coatings. This technique is essential for evaluating long-term performance.
- Laboratory Atmosphere Tests: Simulated environments in a lab can be used to test the effectiveness of inhibitors under controlled conditions. These tests help understand how inhibitors respond to various factors that may be present in the field.
- Field Trials: Actual application in a real-world environment can provide insight into the effectiveness of different inhibitors. Field trials offer data that can be more valid than laboratory tests since they consider varying conditions that might exist in operation.
Evaluating and measuring the performance of corrosion inhibitors is crucial for maintaining optimal conditions in oil and gas operations. Careful analysis allows firms to adjust applications instantly and improve overall corrosion management strategies.
Economic Implications of Corrosion Management
Corrosion is a widespread issue in the oil and gas industry. Understanding its economic implications is crucial for effective management. Organizations face direct costs related to equipment maintenance and replacement due to corrosion, but indirect costs often surpass these. When corrosion is not managed properly, it can lead to significant production delays, environmental damages, and increased operational hazards. This section examines these implications in detail, highlighting the benefits of effective corrosion management.
Cost of Corrosion in the Oil and Gas Industry
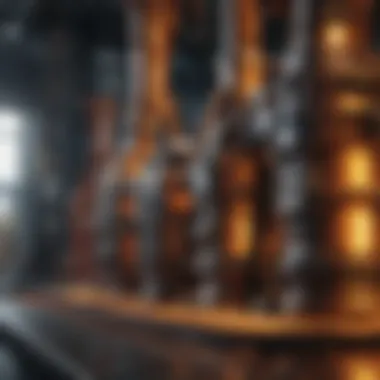
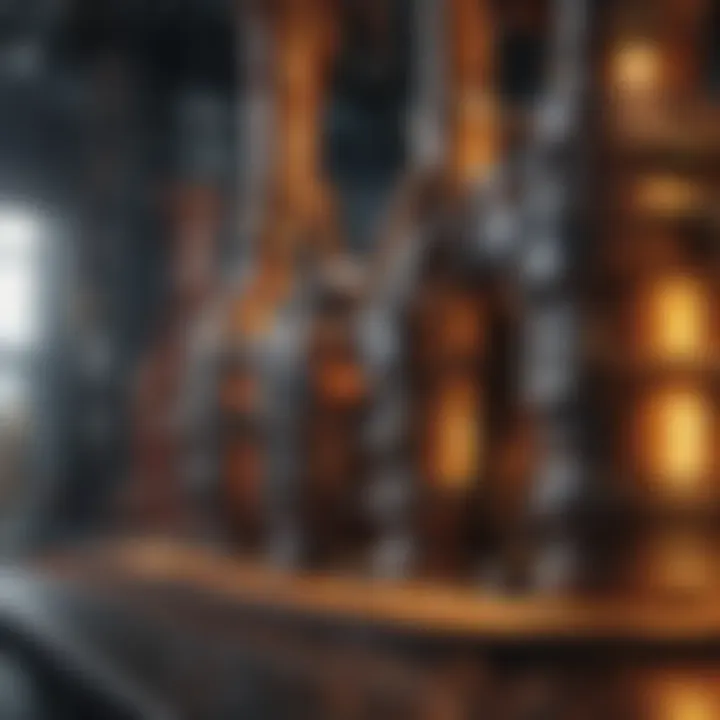
The cost of corrosion can be substantial. It includes:
- Maintenance Costs: Frequent repairs and replacements can drain budgets. Many operators may spend millions on maintenance each year due to the impact of corrosion.
- Production Losses: Unplanned outages from corrosion-related failures lead to reduced output. In a sector where every barrel counts, this can impact profits greatly.
- Environmental Penalties: Leaks caused by corrosion can result in environmental damage, leading to hefty fines and cleanup costs. Regulatory agencies enforce strict penalties, which put additional financial strain on companies.
According to research, the annual cost of corrosion in the oil and gas sector can reach upwards of 20% of the total maintenance budget. These figures show how vital it is for companies to invest in corrosion management strategies to mitigate these costs.
Return on Investment for Corrosion Inhibitors
Investing in corrosion inhibitors can yield significant returns. Effective use of these chemicals results in:
- Extended Equipment Lifespan: By preventing corrosion, these inhibitors extend the life of pipes and equipment, reducing the frequency of replacements and repairs.
- Reduced Downtime: Enhanced performance and fewer failures lead to increased operational efficiency. Less downtime translates to higher production rates and profitability.
- Compliance and Risk Management: Companies using corrosion inhibitors may face fewer regulatory issues related to breaches and environmental impact, lowering the risk of costly penalties.
Research indicates that the return on investment from corrosion inhibitors can be threefold over time. Although initial costs for inhibitors may seem high, the savings and improved operational performance often justify this investment. Organizations that prioritize corrosion management through these measures stand to gain both economically and operationally.
Regulatory Considerations
Environmental Regulations
Environmental regulations focus on minimizing the ecological impact of corrosion inhibitors. The oil and gas industry is under scrutiny due to its potential to harm the environment through spills and emissions. Regulations often dictate the types of chemicals that can be used, promoting greener alternatives.
For instance, the Environmental Protection Agency (EPA) in the United States mandates monitoring practices that assess the effects of chemical releases. Additionally, the REACH regulation in Europe requires businesses to register the chemicals they use, ensuring they are safe for human health and the environment.
Companies must adopt biodegradable corrosion inhibitors that align with these regulations. Such substances can reduce environmental harm while maintaining effectiveness. Moreover, regular training for workers about these regulations is essential to prevent compliance issues and associated penalties.
Safety Standards
Safety standards are another aspect of regulatory considerations that the oil and gas industry must navigate. These standards ensure that the use of corrosion inhibitors does not compromise the safety of personnel or the integrity of equipment. Organizations such as the Occupational Safety and Health Administration (OSHA) set regulations that guide safe handling and application practices.
Compliance with safety standards involves developing and implementing safety data sheets (SDS) for all corrosion inhibitors used in operations. These sheets provide crucial information on handling, storage, and emergency procedures in case of exposure or spills.
Additionally, conducting regular audits and training sessions ensures that workers are aware of best practices when using these chemicals. Equipment that may come into contact with corrosion inhibitors should also be routinely inspected to prevent leaks or spills that could compromise safety.
"Adhering to regulatory considerations protects both the environment and workers, thus ensuring sustainable oil and gas operations."
Overall, it is clear that navigating regulatory considerations is not merely a compliance issue; it is essential for responsible business practices in the oil and gas sector. Proper attention to both environmental regulations and safety standards fosters an industry environment that prioritizes sustainability and safety.
Emerging Trends in Corrosion Inhibitor Technology
Corrosion inhibitors must evolve due to the complex challenges in the oil and gas industry. Their effectiveness can greatly influence operational reliability and cost management. This section will discuss advancement made in corrosion inhibitor technology. Focus is on two key areas: nanotechnology and biodegradable options. These innovations offer significant benefits such as increased effectiveness, environmental sustainability, and adaptability to changing industry needs.
Nanotechnology in Corrosion Inhibition
Nanotechnology has emerged as a crucial player in corrosion inhibitor development. It involves the manipulation of materials at the nanoscale, which can dramatically improve performance. Nanoscale materials can form protective layers on metal surfaces with enhanced adherence and longevity.
- Improved Barrier Properties: Nanoparticles can create dense barriers that limit exposure to corrosive agents.
- Controlled Release Mechanisms: Inhibitors can be designed to release their active ingredients in a controlled manner, prolonging their protective effect.
- Enhanced Compatibility: Nanomaterials often show compatibility with various oil and gas environments, which increases their versatility.
The incorporation of nanotechnology is not without challenges. Concerns about potential toxicity and environmental impact need careful consideration. However, the potential benefits in effectiveness make this area promising for future exploration.
Biodegradable Corrosion Inhibitors
The focus on sustainability is increasingly important in the oil and gas sector. Biodegradable corrosion inhibitors represent a significant advancement in this context. These materials break down into non-toxic components, minimizing environmental impact.
- Sustainable Sourcing: Many biodegradable inhibitors are derived from renewable resources. This aligns with global efforts towards sustainability.
- Reduced Environmental Risk: Unlike traditional inhibitors, which may persist in the environment, biodegradable options reduce the risk of long-term contamination.
- Regulatory Compliance: As environmental regulations tighten, using biodegradable options can help companies comply with these new standards.
In summary, emerging trends in corrosion inhibitor technology are vital for addressing current and future challenges in the oil and gas industry. The ongoing research offers solutions that not only enhance operational efficiency but also contribute to environmental sustainability. Adoption of these technologies can lead to significant improvements in corrosion management practices.
Closure and Future Outlook
Corrosion inhibitors play an essential role in the oil and gas industry. Effective management of these substances can significantly reduce operational costs and equipment failures. The discussion surrounding corrosion inhibitors encompasses various aspects, including their application methods, effectiveness, and the economic benefits they confer. As the industry moves forward, understanding the challenges and pursuing innovative solutions remains crucial.
Summary of Current Challenges
The oil and gas sector faces several challenges related to corrosion and the use of inhibitors. Here are some key issues:
- Cost Considerations: The initial investment in corrosion inhibitors can be significant. Companies must weigh these costs against potential losses from corrosion damage.
- Selection of Inhibitors: With many options available, selecting the right corrosion inhibitor can be complex. Different environments require specific inhibitors for optimal protection.
- Regulatory Compliance: Adhering to strict environmental and safety regulations can limit the choice of corrosion inhibitors, affecting their effectiveness.
- Performance Measurement: Evaluating the effectiveness of corrosion inhibitors is often challenging, requiring sophisticated monitoring and analysis.
Future Directions for Research
Future research in corrosion inhibitors should focus on several key areas to enhance their effectiveness. Some suggested directions include:
- Nanotechnology Applications: Research into the use of nanomaterials may improve the performance of corrosion inhibitors, providing more robust protection in harsher environments.
- Biopolymers and Green Inhibitors: Developing biodegradable and environmentally friendly corrosion inhibitors is essential for aligning with global sustainability goals.
- Advanced Monitoring Techniques: Enhanced methods for measuring corrosion rates and inhibitor effectiveness will provide better feedback, allowing for timely adjustments.
- Data Analytics: Utilizing big data and machine learning to predict corrosion patterns can lead to more effective inhibition strategies, reducing downtime and costs.
Overall, addressing these challenges and pursuing innovative research will shape the future landscape of corrosion inhibition in the oil and gas sector.