Exploring Innovations in Manufacturing Processes
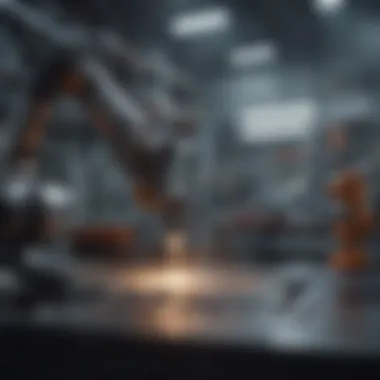

Intro
Manufacturing is a cornerstone of modern economies, fundamental to both developed and developing nations. Its evolution reflects advancements that transcend mere economic metrics, influencing social structures, technological capabilities, and environmental considerations. From its origins in artisanal craftsmanship to today's automated factories, manufacturing processes have undergone profound transformations. The integration of advanced technologies such as automation, artificial intelligence, and sustainable practices redefine how products are made and how businesses operate.
Research Overview
Summary of Key Findings
The manufacturing landscape is currently characterized by several key trends:
- Automation and Robotics: Increasing reliance on automated systems to streamline processes, reduce costs, and enhance efficiency.
- Sustainability: Growing emphasis on sustainable practices to minimize environmental impact and promote ethical sourcing of materials.
- Digital Integration: The adoption of digital tools and technologies, such as the Internet of Things (IoT) and data analytics, is transforming operational strategies.
- Up-skilling Workforce: As processes modernize, there is a critical need for skilled labor that can adapt to and manage these new technologies.
These findings illustrate not just the operational shift but also the changing educational and vocational landscapes as industries strive to keep pace with innovation.
Importance of the Research
Understanding modern manufacturing processes and innovations is vital for various stakeholders. For students and researchers, it provides insights into applied science and engineering principles. For educators, it informs course development, aligning curriculum with industry needs. For professionals, it offers a framework to navigate the challenges of a rapidly evolving field. In essence, manufacturing is not simply about production—it is about leveraging technology responsibly while fostering economic growth.
Methodology
Study Design
This exploration of manufacturing processes employs a mixed-methods approach. It integrates qualitative case studies from various sectors with quantitative data regarding productivity and employment impacts. This duality offers a holistic view of the industry.
Data Collection Techniques
Data was gathered through:
- Interviews with industry experts to provide context and expert opinions.
- Surveys distributed to manufacturing professionals to collect quantitative data on practices and outcomes.
- Literature review focused on recent publications, ensuring the findings are grounded in contemporary research and trends.
The combination of these methods provides a robust understanding of current and future challenges and opportunities within the manufacturing sector.
"The future of manufacturing lies in embracing technology while prioritizing sustainability, creating a balance that benefits all stakeholders."
Prelude to Manufacturing
Manufacturing is a core component of modern economies. It encompasses the transformation of raw materials into finished goods through systematic processes. Understanding the intricacies of manufacturing not only reveals how products come into existence but also highlights the economic, social, and environmental impacts of these activities. This section delves into the fundamental aspects of manufacturing, its significance, and its historical context to provide a comprehensive overview.
Definition and Importance
Manufacturing can be defined as the production of goods using labor, machines, tools, and chemical or biological processing. It plays a vital role in economic development by creating jobs and providing essential products for society. The sector contributes significantly to national GDP and influences trade balances.
Key points regarding its importance include:
- Job Creation: Manufacturing jobs often provide quality employment opportunities, especially in sectors such as automotive, electronics, and consumer goods.
- Technological Advancements: Innovations within the manufacturing sector foster research and development, leading to new technologies that enhance productivity.
- Global Trade: Manufacturing is integral to global supply chains. Products manufactured in one region may be sold in another, driving international commerce.
- Sustainability: With current emphasis on environmental responsibility, manufacturing processes are evolving to reduce waste and promote sustainable practices.
An Overview of Historical Evolution
The history of manufacturing is characterized by continuous evolution. From the early days of craftsmanship to today's advanced technologies, manufacturing has significantly changed.
- Pre-Industrial Era: Manufacturing began with artisans producing goods by hand. Craftsmanship was valued, but the scale of production was limited.
- Industrial Revolution: This marked a major turning point. The introduction of steam engines and mechanized production methods revolutionized how goods were produced. Factories became central to manufacturing, enabling mass production.
- Post-World War II: Economic expansion saw new manufacturing processes emerge, including lean manufacturing and Just-in-Time production strategies. These innovations improved efficiency and reduced costs.
- Digital Age: The current phase of manufacturing is shaped by digital technologies. Concepts such as Industry 4.0 integrate IoT, AI, and big data analytics into manufacturing processes, dramatically enhancing efficiency and adaptability.
As these stages illustrate, manufacturing is a dynamic field, continually adapting to shifts in technology and market demands. The importance of understanding its historical context cannot be overstated, as it provides insights into current practices and future innovations.
Types of Manufacturing Processes
Manufacturing processes are the backbone of production across various industries. Understanding the different types of manufacturing processes is crucial for optimizing efficiency, reducing costs, and fostering innovation. Each process type is tailored toward specific manufacturing needs, and they collectively enable businesses to meet market demands effectively. In this section, we explore three primary types of manufacturing: discrete manufacturing, process manufacturing, and additive manufacturing. Each approach offers unique advantages and considerations.
Discrete Manufacturing
Discrete manufacturing involves the production of distinct items that can be counted. This type is particularly common in industries such as electronics, automotive, and consumer goods. The items produced can often be disassembled and reassembled. For instance, automobile parts are individually created and then assembled into a complete vehicle.
Key characteristics of discrete manufacturing include:
- Counting Units: Each item is counted as a separate unit, facilitating clear inventory management.
- Customization: It allows for variations and customization in production, responding effectively to customer demands.
- Production Processes: Techniques like assembly line production and batch production are commonly utilized.
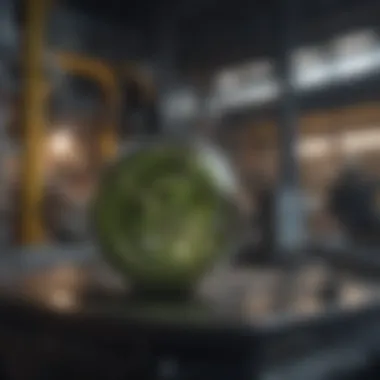

"Discrete manufacturing processes are crucial for industries where product variations are necessary to satisfy consumer preferences."
In this form of manufacturing, quality control is vital. Each unit produced must meet specified standards. Technologies such as computer-aided design and robotics play significant roles in ensuring precision and efficiency.
Process Manufacturing
Process manufacturing is used to produce goods that are typically in bulk and cannot be separated into individual units without losing their properties. This type is prevalent in industries like food production, chemicals, and pharmaceuticals. Products such as beverages, paints, and fuels are made using continuous or batch processes.
Significant features of process manufacturing are:
- Production Flow: Often involves a continuous production flow where materials are transformed into finished products through chemical, mechanical, or thermal processes.
- Homogeneity: The output is usually homogeneous, meaning that the end product has consistent quality and characteristics throughout.
- Efficiency: Economies of scale are more readily achieved, as large quantities are produced efficiently.
In terms of quality, process manufacturing must adhere strictly to industry standards to ensure safety and compliance. Technologies such as process control systems are employed to monitor production variables and guarantee optimal process conditions.
Additive Manufacturing
Additive manufacturing is a revolutionary approach that creates objects layer by layer. Often referred to as 3D printing, this method is transforming product development in industries such as aerospace, medicine, and custom manufacturing. With its ability to rapidly produce complex shapes, additive manufacturing has gained popularity for prototyping and end-use parts.
Important aspects of additive manufacturing include:
- Design Flexibility: It allows for intricate design possibilities that traditional methods cannot achieve.
- Material Efficiency: Material is used only where necessary, which minimizes waste and reduces costs.
- Rapid Prototyping: Shorter production times enable quicker iterations in product design and testing.
This technology is increasingly used for creating everything from medical implants to lightweight aerospace components. However, considerations around production speed and material limitations often need to be addressed.
Understanding these types of manufacturing processes helps businesses optimize their production strategies and align with modern market demands. Leveraging the strengths of each process can lead to significant advancements in product development and production efficiency.
Current Trends in Manufacturing
Manufacturing is experiencing a pivotal transformation, shaped by various trends that are redefining its landscape. This section aims to illuminate the prevailing forces in the industry, examining how they not only enhance productivity but also realign operational strategies. Understanding these current trends is essential for stakeholders at every level, from students and researchers to seasoned professionals in the field.
Impact of Automation
Automation has emerged as one of the most significant trends influencing manufacturing processes. It involves the use of technology to perform tasks with minimal human intervention. With the adoption of automation, companies can achieve higher production efficiency and consistency. Machines and robots can operate continuously, reducing downtime and increasing output.
The advantages of automation are multifaceted:
- Cost Reduction: By minimizing labor costs, businesses can allocate resources more strategically.
- Quality Improvement: Automated systems consistently deliver high-quality products with fewer defects.
- Safety Enhancements: Machines can take over hazardous tasks, reducing workplace injuries.
Despite these advantages, companies must consider the associated challenges, such as the initial investment in technology and the shift in workforce skill requirements. Training programs become crucial to equip employees with the skills needed to work alongside automated systems.
Sustainable Manufacturing Practices
Sustainability has become a core focus for modern manufacturing. As industries face growing regulatory pressures and consumer demands for environmentally friendly products, sustainable practices are now seen as integral to business strategy rather than an optional add-on.
Adopting sustainable manufacturing practices offers various benefits, including:
- Resource Efficiency: Reducing waste and optimizing resource use leads to cost savings.
- Market Advantage: Companies that emphasize sustainability can strengthen their brand reputation, appealing to environmentally conscious consumers.
- Regulatory Compliance: Staying ahead of environmental regulations helps avoid potential fines and disruptions.
Practices like recycling materials, reducing emissions, and utilizing renewable energy sources are becoming standard. Organizations must leverage these aspects to innovate and remain competitive.
Integration of Digital Technologies
Digital technologies are reshaping how manufacturers operate. The integration of tools like artificial intelligence, the Internet of Things (IoT), and advanced data analytics allows for improved decision-making and operational efficiency.
Key benefits of integrating digital technologies include:
- Real-Time Monitoring: IoT devices facilitate the tracking of operations in real-time, enabling faster responses to issues.
- Data-Driven Insights: Advanced data analytics provides valuable insights into production trends and areas for improvement.
- Enhanced Collaboration: Digital platforms bolster communication across teams and suppliers.
To successfully navigate this integration, businesses must foster a culture of adaptability and continuous learning. This approach helps organizations remain agile in a rapidly evolving market landscape.
"The future of manufacturing is not just about production; it's about using technology to improve every aspect of the process."
In summary, the trends in manufacturing highlight the industry's responsiveness to technological advancements and the increasing importance of sustainability. Embracing these changes will be vital for companies aiming to thrive in the modern economic environment.
Role of Quality Control
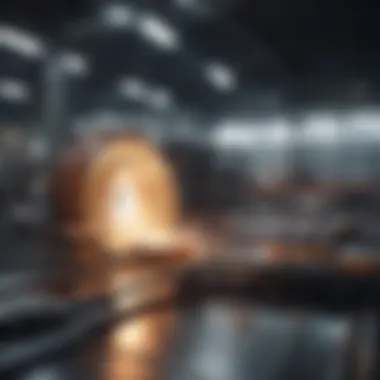

Quality control serves as a fundamental pillar in the manufacturing sector. Its primary objective is to ensure that products meet specific quality standards before they reach consumers. This is essential not only for customer satisfaction but also for maintaining a brand’s reputation in a competitive market. Effective quality control can lead to increased efficiency and reduced costs, which are critical factors in the success of any manufacturing operation. The quality assurance process encompasses various strategies aimed at minimizing defects, ensuring consistency, and enhancing the overall product lifecycle.
Importance of Quality Assurance
Quality assurance is paramount in any manufacturing process. It encompasses all planned and systematic actions necessary to provide adequate confidence that the product or service will meet given requirements for quality.
Key benefits of robust quality assurance include:
- Customer Satisfaction: Delivering products that meet or exceed expectations fosters trust and loyalty among customers.
- Cost Reduction: Identifying defects early in the production process minimizes waste and reduces costs associated with rework and returns.
- Compliance with Standards: Meeting international and industry standards can facilitate market access and enhance competitiveness.
Moreover, quality assurance helps in identifying process inefficiencies, leading to continuous improvement and innovation. By ensuring high-quality standards, companies also mitigate risks associated with recalls or legal liabilities.
Current Techniques in Quality Control
The manufacturing industry employs various techniques for quality control, reflecting the specific needs of different processes and products. Understanding these methods is essential for enhancing product quality and efficiency.
- Statistical Process Control (SPC): This method uses statistical methods to monitor and control a manufacturing process. By measuring outputs and determining their variability, companies can maintain control over production quality.
- Total Quality Management (TQM): TQM is a management approach centered on quality, based on the participation of all members of an organization. It aims for long-term success through customer satisfaction.
- Six Sigma: This is a data-driven approach aimed at reducing defects and improving processes. It involves various tools and techniques to analyze and improve operational efficiencies.
These current techniques integrate seamlessly into digital technologies, allowing for real-time data analysis, which is increasingly vital as manufacturing adapts to new demands.
"Quality means doing it right when no one is looking." – Henry Ford
Workforce Skill Enhancement
In the contemporary landscape of manufacturing, workforce skill enhancement has become essential. As technology and processes evolve, there is a pressing need for an adaptable workforce. Skilled workers are vital for maintaining quality, efficiency, and innovation. This section highlights the importance of workforce skill enhancement, discussing various aspects including training needs and the future of the workforce in manufacturing.
Training and Development Needs
Addressing training and development needs is crucial for sustaining progress in manufacturing. Companies must assess the current skill levels of their employees and identify gaps that impede productivity. Here are some key elements to consider:
- Skill Assessment: Regularly evaluate workforce competencies through assessments to tailor training programs.
- Diverse Learning Opportunities: Implement a mix of on-the-job training, workshops, and online courses. These should cater to different learning styles.
- Mentorship Programs: Pair experienced employees with newcomers to facilitate knowledge transfer and practical skills development.
- Industry Standards: Align training with industry standards and technological advancements. This ensures that the workforce is prepared for current challenges.
The Future of Workforce in Manufacturing
Looking ahead, the future of workforce in manufacturing is likely to be influenced by several factors. The integration of digital technologies will continue to reshape job roles. Workers will need to adapt to new tools and methodologies. Key considerations include:
- Automation Impact: While automation may replace some tasks, it will also create new roles that require advanced technical skills.
- Lifelong Learning: Emphasizing continuous education will become integral, as technology evolves rapidly. Employees must engage in lifelong learning to stay relevant.
- Collaborative Work Environments: Future workplaces will likely promote collaboration among teams utilizing digital platforms that enhance communication and project management.
"The skills that were relevant yesterday may not be relevant tomorrow." - A quote reflecting on the rapid changes in manufacturing.
In summary, workforce skill enhancement is a dynamic process that is fundamental to the success of manufacturing. Companies that prioritize training and development will not only improve operational efficiency but also build a more resilient workforce ready for future challenges.
Challenges Facing the Manufacturing Industry
Manufacturing is vital to economic growth and development. However, it faces numerous challenges that hinder its full potential. Understanding these challenges helps stakeholders navigate risks and seize opportunities. Key issues like supply chain disruptions and regulatory compliance significantly impact the industry. Addressing these challenges is crucial for sustaining innovation and efficiency in manufacturing processes.
Supply Chain Disruptions
Supply chain disruptions are a pressing issue for manufacturers. Global events, natural disasters, or unplanned incidents can interrupt the flow of materials and components. Such interruptions can lead to production delays and increased costs. The recent COVID-19 pandemic showcased how vulnerabilities in supply chains could hamper operations.
Factors contributing to supply chain disruptions include:
- Dependency on Global Suppliers: Many manufacturers rely on suppliers across the world. A disruption in one region can affect the entire chain.
- Transportation Challenges: Issues in shipping or logistics can also lead to delays. Whether due to weather, strikes, or port congestion, transport issues affect delivery.
- Demand Fluctuations: Sudden changes in consumer demand can strain supply chains. Businesses must adapt quickly to align production with market needs.
To mitigate these disruptions, manufacturers can adopt resilient strategies like:
- Building diversified supplier networks
- Investing in inventory management technologies
- Enhancing communication with suppliers and customers
In short, addressing supply chain disruptions is essential for maintaining smooth operations and ensuring production goals are met.
Regulatory and Compliance Issues
Regulatory and compliance issues are another significant challenge for the manufacturing sector. Frequent changes in regulations demand that manufacturers remain agile. Failure to comply can result in penalties, damaged reputations, and loss of market access.
Key areas of regulation include:
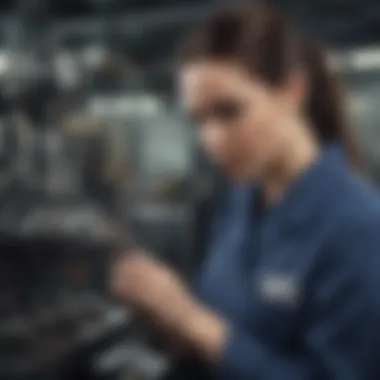

- Environmental Regulations: Manufacturers face strict compliance requirements related to pollution and waste management. Meeting these regulations often requires additional investments in technology and processes.
- Safety Standards: Workplace safety regulations are critical. Manufacturers must ensure compliance with health and safety guidelines to protect employees.
- Quality Control Regulations: Regulations concerning product quality vary by industry. Manufacturers must adhere to standards to satisfy customers and regulatory bodies.
For effective compliance, manufacturers can establish robust quality management systems and continuous monitoring of regulatory changes.
"The ability to adapt and respond to regulatory changes can provide a competitive edge in the manufacturing sector."
Overall, addressing regulatory and compliance issues is vital for sustainable and responsible manufacturing. Meeting these challenges can enhance credibility and customer trust.
Case Studies in Manufacturing Innovations
Case studies in manufacturing innovations provide significant insights into how theoretical concepts translate into practical applications. This segment examines real-world examples that highlight successful strategies and assist in understanding the cause-and-effect relationships in manufacturing. By analyzing diverse implementations, it becomes easier to discern patterns that lead to effectiveness and efficiency in manufacturing processes. These studies not only showcase the successes but also illuminate the pitfalls that companies face. This comparison is essential for industries aiming to innovate.
Successful Implementations
Successful implementations in manufacturing reflect the culmination of planning, execution, and ongoing evaluation. One notable case is Tesla's Gigafactory in Nevada. The Gigafactory employs advanced automation technologies that significantly enhance production rates while minimizing costs. The integration of robotics in assembly lines and energy-efficient manufacturing contribute to Tesla's competitive edge. Companies like Toyota also illustrate success through Just-In-Time (JIT) manufacturing, which optimizes inventory levels and reduces waste.
Key factors contributing to successful implementations include:
- Strategic Planning: Thorough market research and concept validation.
- Technology Adoption: Embracing cutting-edge technologies can enhance efficiency.
- Workforce Involvement: Engaging employees in the innovation process leads to better outcomes.
In a rapidly evolving industry, successful implementations serve as blueprints for others to follow, showcasing effective methods and practical solutions.
Lessons Learned from Failures
Learning from failures in manufacturing innovations is as crucial as celebrating successes. One striking example is the Boeing 787 Dreamliner project, which experienced significant delays and cost overruns due to poor supply chain management and lack of unified project oversight. This case illustrates the risks that can arise when innovation is prioritized over robust foundational systems.
Considerations learned from failures often include:
- Risk Management: Proactive measures to identify and mitigate potential issues.
- Clear Communication: Ensuring all stakeholders are aligned to avoid misinterpretations.
- Flexibility in Approach: Being ready to adapt as challenges emerge prevents further complications.
Such lessons offer valuable guidance, underscoring the significance of meticulous planning and execution in manufacturing innovations.
Future Directions in Manufacturing
Understanding the future directions in manufacturing is essential for comprehending how the industry will adapt to changing dynamics and pressures. The advancements in technology, the rise of sustainability demands, and the need for greater efficiency are setting the stage for profound transformations. The next several years will demand a pro-active stance, where organizations concentrate on the innovations not only to grow but to remain competitive.
The Role of Research and Development
Research and Development (R&D) stands at the forefront of moving manufacturing forward. Companies that invest wisely in R&D can unlock new processes and technologies that lead to higher efficiency and productivity. This discipline is vital, as it enables businesses to innovate and create competitive advantages.
The focus areas for R&D in manufacturing include:
- Material Science: New materials can lead to stronger, lighter, and more economical products.
- Process Improvement: Developing methods for lean manufacturing reduces waste and boosts profitability.
- Automation Tools: Creating next-gen automation solutions that optimize workflow and lessen human error.
Establishing partnerships with educational institutions or technology firms can catalyze innovation. As the market changes, R&D efforts must align closely with industry needs to maximize practical applications.
Potential Advances on the Horizon
The potential for future advancements in manufacturing is significant, driven by emerging technologies and sustainable practices. Some key trends expected to shape the landscape include:
- Advanced Automation: Robotics and AI will become more integrated into the manufacturing process, boosting efficiency and precision.
- Sustainable Practices: Circular manufacturing, which emphasizes reuse and recycling, will gain traction as companies aim to minimize environmental impact.
- Smart Manufacturing: The Internet of Things (IoT) will continue to enable machines to communicate and improve operations independently, creating a more responsive manufacturing environment.
- Data Analytics: Leveraging big data for predictive maintenance will reduce downtime and enhance productivity.
The evolution of manufacturing is not just about adopting new technologies; it involves redefining processes to meet current and future demands.
The importance of continuous innovation in manufacturing cannot be overstated. Companies that embrace R&D and adapt to technological advancements will thrive, while others risk being left behind.
Ending
The conclusion of this article serves not only as a summary but also as a crucial reflection on the importance of manufacturing processes and innovations in today's world. The manufacturing sector stands at the intersection of tradition and progress, requiring adaptation to continuously evolving technologies and methodologies.
Summarizing Key Points
In this exploration of manufacturing, several key points arise:
- Historical Evolution: Understanding the historical context helps shape current manufacturing practices. The transition from handcrafting to machinery transformed the industry.
- Types of Processes: Discrete, process, and additive manufacturing each have unique features and applications. Knowledge about these types aids in selecting the best suited to specific needs.
- Current Trends: Automation, sustainability, and digital technology integration reflect the industry's direction. These trends illustrate how manufacturing is responding to global changes.
- Quality Control: Emphasizing quality assurance and current techniques enhances product reliability. Manufacturers can reduce defects and improve customer satisfaction.
- Workforce Development: Training and skill enhancement are vital for future success. A well-equipped workforce adapts to changing technology and retains industry competitiveness.
- Challenges: Addressing supply chain disruptions and regulatory issues remains essential for stability and growth in manufacturing.
- Case Studies: Analyzing successful and failed innovations provides lessons to move forward wisely.
- Future Directions: Research and development, alongside potential advances, suggest a bright but challenging future for manufacturing.
These points synthesize the critical information necessary to understand the complexities of manufacturing.
The Importance of Continuous Innovation
Continuous innovation is vital for the vitality of the manufacturing sector. As new technologies emerge, manufacturers must integrate these advancements to remain competitive. Adopting innovative practices can lead to improved efficiency, reduced costs, and higher quality products.
Moreover, innovation can drive sustainability efforts, ensuring that manufacturing processes align with environmental goals without compromising productivity. Thus, embracing change is not just beneficial but necessary for the long-term health of the industry.