Essential Strategies for Aluminum Corrosion Protection

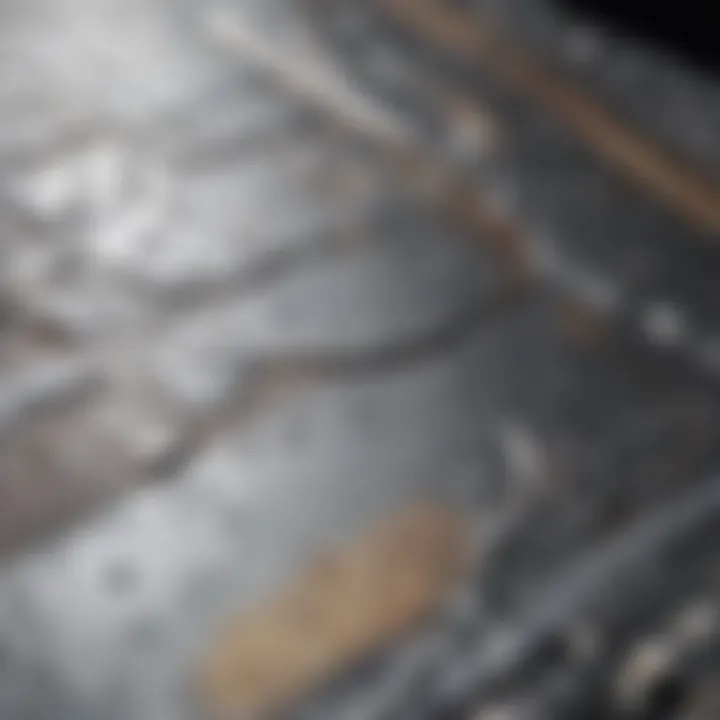
Intro
Aluminum is widely used in many industries due to its desirable properties. Its lightweight nature makes it a popular choice in aerospace, automotive, and construction applications. However, aluminum is not immune to corrosion. Understanding corrosion mechanisms and protection strategies is essential for maintaining the integrity of aluminum components. This guide will explore the different types of aluminum corrosion and the importance of protective measures.
Research Overview
Summary of Key Findings
Recent studies reveal that aluminum corrosion may arise from various environmental factors. Basic oxidation, pitting, galvanic corrosion, and stress corrosion cracking are key mechanisms identified. Each of these corrosion types can significantly affect the durability of aluminum.
"Aluminum can form a protective oxide layer, though certain environments can compromise this layer. Understanding these environments is crucial."
Importance of the Research
Addressing aluminum corrosion is vital not just for longevity of materials but also for safety and cost efficiency. With a growing emphasis on sustainability, innovative protective technologies can reduce waste and energy consumption. This study shows that implementing protective strategies can lead to significant long-term savings.
Methodology
Study Design
The research employed a mixed-methods approach. Quantitative data regarding corrosion rates were collected from various fields, while qualitative interviews with industry experts provided insights into practical experiences with aluminum protection.
Data Collection Techniques
Data collection involved various techniques, including:
- Laboratory experiments to test corrosion resistance under controlled conditions.
- Field studies to assess real-world performance of protective coatings.
- Surveys and interviews with professionals to gather anecdotal evidence on successful applications of protective measures.
These methods help form a comprehensive view of aluminum protection against corrosion. Understanding both empirical data and real-world practices fosters better strategies for protecting aluminum materials.
Prelude to Aluminum and Corrosion
Corrosion is a critical concern for materials, especially for aluminum, which is celebrated for its lightweight and strong properties. This section elucidates the significance of understanding how aluminum interacts with its environment. The onset of corrosion can lead to structural integrity issues and economic burdens, making it essential for students, researchers, and professionals to grasp these dynamics.
Basic Properties of Aluminum
Aluminum is a non-ferrous metal that is known for its remarkable properties. It has a low density, which makes it an ideal choice in various applications, from aerospace to construction. Aluminum is also malleable and ductile, allowing it to be easily shaped without breaking. The metal is not as susceptible to corrosion in ordinary environments due to its natural oxide layer, which thinly coats its surface and acts as a barrier.
However, this oxide layer does not provide immunity against all types of corrosive conditions. Factors such as pH levels, salt exposure, and humidity can lead to the degradation of aluminum over time.
Aluminum alloys, although providing enhanced mechanical properties, can exhibit different corrosion behavior compared to pure aluminum. It is critical to comprehend both pure aluminum's properties and those of its alloys to choose the right material for specific applications.
Importance of Corrosion Resistance
Corrosion resistance is paramount for extending the lifespan of aluminum products. The deterioration of aluminum structures and components can lead to catastrophic failures. Understanding corrosion resistance not only increases product durability but also enhances safety. Industries such as aviation and automotive prioritize corrosion resistance because any structural compromise can result in severe safety risks.
Moreover, from an economic standpoint, the cost of maintenance and repairs arising from corrosion can be significant. Choosing aluminum with high corrosion resistance can mitigate these costs effectively.
Knowledge of how aluminum behaves in various environments is essential for effective material selection and design decisions.
Understanding Corrosion
Understanding corrosion is crucial for protecting aluminum effectively. Corrosion can lead to structural failure, increased maintenance costs, and reduced longevity of metal products. For aluminum, a material often chosen for its lightweight and corrosion-resistant nature, recognizing how corrosion can still occur under the wrong conditions is essential. Analyzing the specifics of corrosion helps identify the most effective preventative measures. Thus, when knowledge of corrosion mechanisms is integrated into the design and application processes, it can greatly enhance the material's performance and durability over time.
Definition and Types of Corrosion
Corrosion refers to the gradual degradation of materials, typically metals, due to environmental factors. For aluminum, it tends to undergo oxidation processes. There are several types of corrosion that affect aluminum, including:
- Uniform Corrosion: This occurs evenly across a surface, leading to a general thinning of the material. It is usually the least harmful but can still compromise integrity over time.
- Pitting Corrosion: This localized form of corrosion leads to the formation of small pits or holes in the metal surface. Pitting is particularly insidious as it can progress silently.
- Galvanic Corrosion: This happens when aluminum comes into contact with a more noble metal in the presence of an electrolyte, leading to rapid degradation of aluminum.
- Crevice Corrosion: This occurs in shielded areas, like joints or overlaps, where stagnant water can accumulate, leading to localized attack.
- Stress Corrosion Cracking: This critical issue arises when tensile stress and a corrosive environment interact, resulting in cracks that can lead to catastrophic failure.
Understanding these types enables a focused approach to corrosion prevention.
Physical and Chemical Causes
Corrosion in aluminum can result from physical and chemical factors. Key contributors include:
- Moisture and Electrolytes: Water, especially when mixed with salts, can facilitate corrosion. It serves as a medium for electrolytic reactions that corrode aluminum.
- Oxygen Exposure: Aluminum naturally reacts with oxygen to form aluminum oxide, which is protective in small amounts. However, excessive exposure can lead to pitting and other corrosion types.
- Temperature Variations: Extreme temperatures can accelerate corrosion processes. For example, elevated temperatures may increase the rate of reactions that lead to material breakdown.
- Chemical Attack: Certain chemicals, such as acids and alkalis, are detrimental to aluminum. Knowing the environment in which aluminum will be used helps avoid exposure to harmful agents.
Through a clear understanding of the factors influencing corrosion, one can employ strategies to effectively safeguard aluminum.
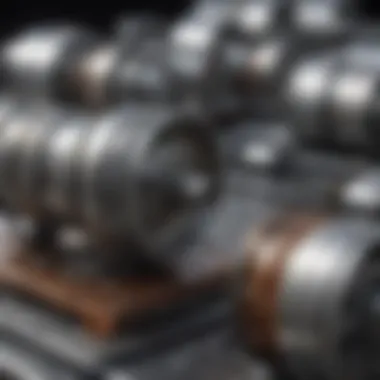
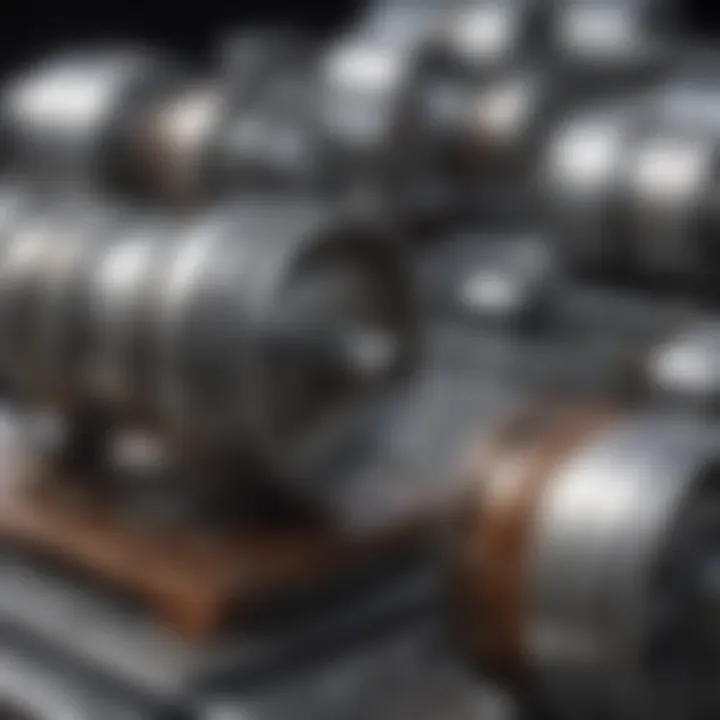
Specific Forms of Aluminum Corrosion
Understanding the specific forms of aluminum corrosion is critical to developing effective protection strategies. Different mechanisms can lead to various types of corrosion, impacting the performance and safety of aluminum products in many applications. Knowledge of these forms helps professionals select suitable materials and coatings, design features, and maintenance protocols to minimize risks.
Pitting Corrosion
Pitting corrosion is often regarded as one of the most aggressive forms of aluminum corrosion. It occurs when localized breakdown of the protective oxide layer takes place, leading to the formation of small, deep pits. This type of corrosion can be particularly concerning because it can advance without significant loss of overall material thickness, making it hard to detect until severe damage has occurred.
Some factors contributing to pitting corrosion include:
- Chloride ions: Common in many environments, chloride ions can aggressively attack the protective oxide layer of aluminum.
- Stagnant water conditions: Areas where water does not flow effectively can harbor corrosive substances, increasing pitting risk.
Protection against pitting can be enhanced through the use of alloy compositions that show improved resistance, as well as applying suitable protective coatings that fortify the oxide film.
Galvanic Corrosion
Galvanic corrosion occurs when two different metals come into electrical contact while in a corrosive environment. In this scenario, one metal acts as an anode and the other as a cathode, leading to accelerated corrosion of the anodic metal. When aluminum connects with certain metals, such as copper or steel, it can suffer galvanic corrosion, particularly in electrolytic solutions.
Some key elements to consider regarding galvanic corrosion include:
- Electrochemical potential: Understanding the relative potentials of the metals involved can help predict corrosion behavior.
- Environmental conditions: High humidity or saltwater environments can exacerbate galvanic effects.
To prevent galvanic corrosion, insulating barriers such as insulation tapes or coatings can be employed to separate metals. Proper alloy selection can also minimize risks.
Crevice Corrosion
Crevice corrosion is a type of localized corrosion typically occurring in confined spaces where the oxygen concentration is different. This usually happens in joints, seams, or under gaskets where moisture may become trapped. The environments in these areas often become more acidic, which fosters rapid corrosion of aluminum.
Important factors influencing crevice corrosion include:
- Geometric design: Factors such as tight joints or poor drainage can promote the formation of crevices.
- Presence of contaminants: Biological materials or decaying organic matter can accelerate corrosion in these areas.
Mitigating crevice corrosion often involves careful design to eliminate areas where crevices can form. Regular inspection and maintenance can also help detect early signs of this corrosion type.
Stress Corrosion Cracking
Stress corrosion cracking (SCC) is an insidious form of corrosion that occurs when the metal is under tensile stress and exposed to a corrosive environment. For aluminum alloys, SCC can lead to catastrophic failure. This form of corrosion initiates at specific sites and can grow rapidly, making it critical to detect and prevent.
Factors that contribute to SCC include:
- Stress levels: Both residual and applied stresses can increase susceptibility.
- Corrosive agents: Environments containing chlorides can significantly enhance SCC rates.
Effective strategies to combat SCC include stress-relieving processes during manufacturing and using more resistant alloy compositions. It’s also crucial to monitor components for signs of cracking, especially in high-stress applications.
Proactive measures for detecting and mitigating specific forms of aluminum corrosion are essential in ensuring the longevity and performance of aluminum products.
Understanding these forms of corrosion allows for informed decisions regarding material selection and preventive strategies, ultimately leading to improved durability and reduced maintenance costs.
Protective Coatings for Aluminum
Protective coatings play a crucial role in extending the life and functionality of aluminum in various applications. These coatings act as barriers that prevent corrosive substances from reaching the bare metal of the aluminum. The choice of coating depends on the specific needs of the application, such as the exposure conditions, mechanical demands, and aesthetic requirements. By understanding the different types of protective coatings, their benefits, and considerations, users can make informed decisions to enhance the durability of aluminum structures.
Anodizing Process
Anodizing is an electrochemical process that transforms the surface of aluminum into a durable, corrosion-resistant layer. This process involves immersing the aluminum in an electrolyte solution and passing an electric current through it. During this process, aluminum oxide forms on the surface, providing enhanced protection against corrosion.
The anodized layer can vary in thickness, which influences both the corrosion resistance and appearance of the aluminum. A thicker anodized layer generally provides better protection but may require more processing time. Anodized aluminum is not only resistant to corrosion but also offers improved wear resistance and can be colored for aesthetic enhancements. Moreover, anodizing is environmentally friendly, as it generates minimal waste and does not use hazardous chemicals.
Paints and Sealants
Using paints and sealants is another popular method for protecting aluminum surfaces. These coatings create a physical barrier between the aluminum and the environment, preventing moisture and chemicals from causing corrosion. Paints come in various formulations, including epoxy, polyurethane, and acrylic, each suited for different conditions.
- Epoxy paints provide excellent adhesion and chemical resistance, making them ideal for harsh environments.
- Polyurethane paints are known for their flexibility and UV resistance, suitable for outdoor applications.
- Acrylic paints offer good weathering properties and are easy to apply.
Sealants, on the other hand, are often used in conjunction with paints to provide additional protection against corrosion. They seal gaps and joints, keeping moisture and contaminants from reaching the metal underneath. Both paints and sealants can be customized to meet aesthetic preferences, allowing for a combination of protection and visual appeal.
Thermal Spraying
Thermal spraying is an advanced technique used to apply protective coatings to aluminum surfaces. In this process, molten or semi-molten materials are sprayed onto the surface through a nozzle. The process creates a dense and adherent coating that bestows excellent corrosion resistance.
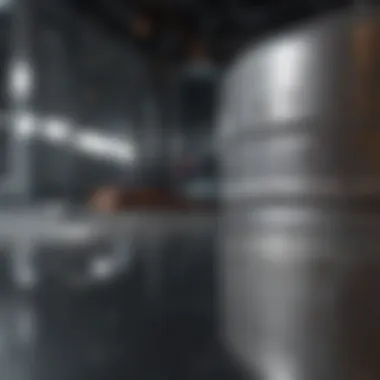
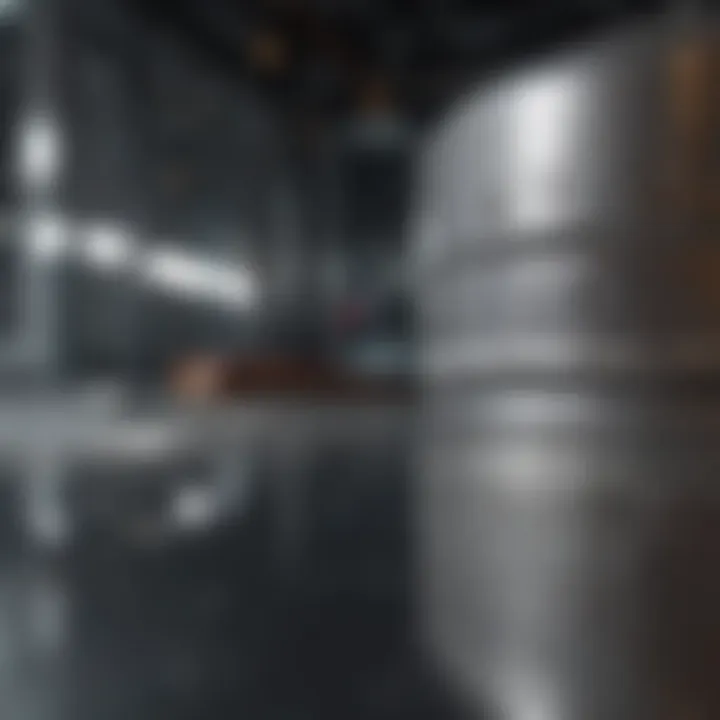
There are several types of thermal spraying methods, including:
- Flame spraying: Utilizes a flame to melt the coating material before it is projected onto the surface.
- Plasma spraying: Involves creating a plasma arc to melt the particles, resulting in a denser coating.
- HVOF (High-Velocity Oxygen Fuel) spraying: In which a fuel mixture is burned, producing high-velocity particles that impact and bond to the surface.
Thermal spraying offers significant advantages, including excellent adhesion, good hardness, and the ability to apply various materials, such as ceramics and metals. Additionally, this technique is particularly useful for large components or structures where traditional coating methods may be impractical.
"Choosing the right protective coating can significantly enhance the lifespan of aluminum components, making them more reliable in their respective applications."
Corrosion Inhibitors
Corrosion inhibitors play a crucial role in protecting aluminum from deterioration. Their significance lies in providing an additional line of defense against the corrosive attacks that materials may face in various environments. Since aluminum is appreciated for its lightweight and corrosion-resistant properties, it is still vulnerable under specific conditions. This section explores the types and mechanisms of action of corrosion inhibitors, which are key components in corrosion management strategies.
Types of Corrosion Inhibitors
Corrosion inhibitors can be classified into several categories based on their chemical composition and function. The most common types include:
- Anodic Inhibitors: These reduce the anodic reaction in metal corrosion, often by forming a protective oxide layer on the metal surface.
- Cathodic Inhibitors: They decrease the rate of cathodic reactions without affecting the anodic processes. These inhibitors can help mitigate galvanic corrosion particularly.
- Mixed Inhibitors: These affect both anodic and cathodic reactions, providing a more comprehensive approach to minimizing corrosion rates.
- Volatile Corrosion Inhibitors (VCIs): These are used in sealed environments, releasing vapors that protect aluminum components from corrosion.
The selection of an appropriate inhibitor depends on various factors such as the nature of the environment and the type of aluminum alloy being protected.
Mechanism of Action
The effectiveness of corrosion inhibitors hinges on their mechanism of action. Each type has a unique way to reduce corrosion, which can sometimes overlap.
- Film Formation: Anodic inhibitors often work by forming a protective film on the metal surface. This film acts as a barrier, preventing direct contact between the metal and corrosive agents.
- Ion Exchange: Many inhibitors function through ion exchange mechanisms. They interact with metal surfaces and modify the electrochemical environment, making it less conducive to corrosion.
- pH Alteration: Some inhibitors can change the pH level of the environment, making it less favorable for corrosive reactions to occur.
- Adsorption: Corrosion inhibitors can adsorb onto the metal surface, creating a protective layer that impedes ion movement and slows down the corrosion process.
Understanding how these inhibitors work is essential for selecting the right product and method for aluminum protection. This knowledge allows for targeted approaches that enhance the lifespan of aluminum structures, especially in challenging environments.
"Choosing the appropriate corrosion inhibitor is vital for effective aluminum protection, as each provides unique benefits and operates through distinct mechanisms."
In summary, corrosion inhibitors are indispensable in the fight against corrosion in aluminum materials. Their correct application can lead to significant cost savings, longer service lives for components, and reduced environmental impact by minimizing the need for frequent replacements.
Material Selection and Design Considerations
Selecting the right materials and designing components to reduce corrosion is pivotal in ensuring aluminum retains its desirable properties. Corrosion can significantly undermine not only the material integrity but also the overall functionality of the product. Understanding the nuances of material selection and design can lead to enhanced longevity and performance in applications ranging from aerospace to construction.
Alloy Selection
Choosing the appropriate aluminum alloy is fundamental in combating corrosion. Different alloys carry varying resistance levels based on their elemental composition. For instance, aluminum 6061 exhibits good resistance to corrosion, while 7075 might not fare as well due to its higher zinc content. The latter, while strong, is prone to stress corrosion cracking under certain conditions.
Factors to consider include:
- Hydration Properties: Alloys such as 5083 are suited for marine applications due to their excellent resistance to saltwater corrosion.
- Heat Treatment: Some alloys respond to heat treatment, influencing their mechanical and corrosion resistance properties. For instance, heat-treated 2024 displays superior strength but decreased corrosion resistance compared to its non-heat-treated counterpart.
- Environmental Factors: Consider the environment where the aluminum will be used. Aggressive environments might demand specific alloys designed to withstand challenging conditions.
Selecting an alloy does not solely pertain to its strength but requires a holistic assessment of performance metrics, environmental conditions, and potential exposure to corrosive agents.
Design Factors to Minimize Corrosion
Design plays an essential role in promoting corrosion resistance alongside material selection. Key design considerations include:
- Surface Area Exposure: Increasing surface area can accelerate corrosion. Designing components to limit unfavourable exposure to aggressive environments is vital.
- Joints and Crevices: Joints can trap moisture, leading to crevice corrosion. Engineers should plan joints to ensure good drainage and avoid tight gaps, which may compound corrosion risks.
- Orientation: Proper orientation during the installation of aluminum structures can aid in maintaining surface drainage, reducing pooling of moisture.
- Coating and Finishing: The choice of finish can influence how aluminum interacts with environmental elements. A properly applied anodizing layer or other protective coatings can serve as a barrier against corrosive substances.
"Effective design strategies are not only about aesthetics but also about structural integrity and longevity across varying conditions."
In summary, the careful selection of aluminum alloys and thoughtful design choices can significantly diminish the risks associated with corrosion. With a proactive approach, professionals can ensure the sustained utility and reliability of aluminum components across their intended applications.
Testing and Monitoring Corrosion
Corrosion can gradually undermine the integrity of aluminum structures, thus understanding how to test and monitor this process is essential. Testing and monitoring are critical components in maintaining the functionality and longevity of aluminum materials. Effective corrosion testing helps identify vulnerabilities and informs how to best protect against degradation. Similarly, monitoring technologies provide ongoing assessments that can prevent significant damage or component failure before they happen.
In practical terms, testing can reveal the extent of corrosion, the specific type, and thereby allows for the formulation of the most appropriate remediation strategies. Monitoring, on the other hand, provides real-time data about the condition of aluminum, allowing for timely interventions. This approach emphasizes not just immediate protection, but also ensures a sustainable outlook for aluminum use across applications.
Corrosion Testing Methods
Various methods exist for testing aluminum corrosion, each selected based on the specific context and requirements. Generally, these can be categorized into non-destructive and destructive testing methods:
- Visual Inspection: This is often the first line of defense. Trained personnel evaluate the physical condition of aluminum for signs of surface deterioration.
- Electrochemical Testing: Techniques like EIS (Electrochemical Impedance Spectroscopy) provide insights into the corrosion processes at the material's surface.
- Weight Loss Method: This method involves exposing aluminum samples to corrosive environments and measuring the weight loss over time. It quantifies overall corrosion rates but is destructive.
- Salt Spray Testing: Commonly used, this method simulates corrosive environments by exposing aluminum to saline mist for a specific duration.
Each method has its advantages and limitations. For instance, while visual inspections are easy and quick, they might not reveal issues beneath the surface. In contrast, electrochemical techniques can provide deeper insights but may require specialized equipment and expertise.
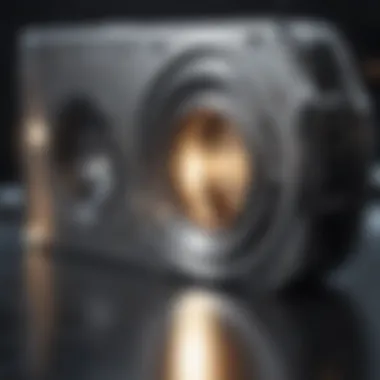
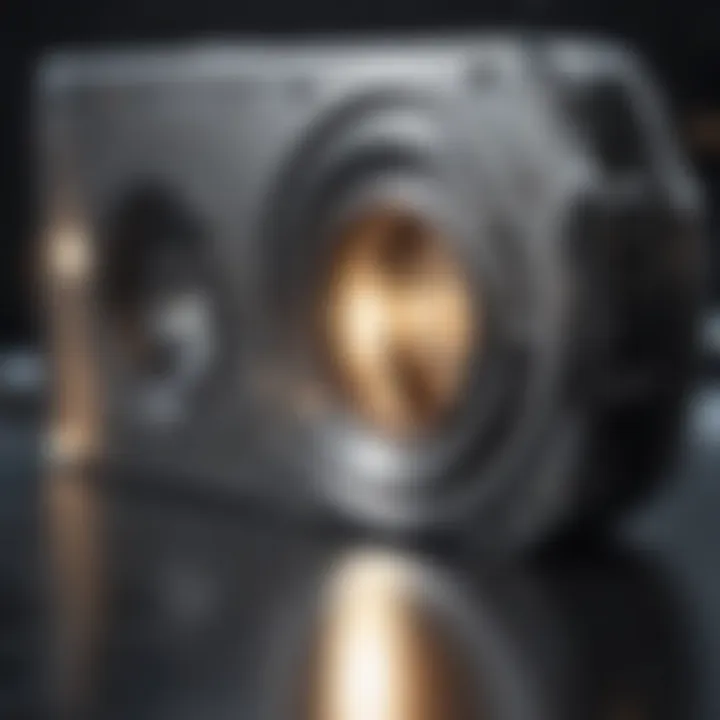
Monitoring Technologies
Effective monitoring technologies play a pivotal role in assessing aluminum's corrosion status. Here are some approaches:
- Corrosion Sensors: These devices are installed on aluminum components and measure corrosion rates in real-time. They can alert operators to critical changes immediately.
- Ultrasonic Testing: Employing sound waves to detect changes in thickness, ultrasonic testing can identify corrosion in inaccessible areas without having to dismantle structures.
- Remote Sensing Technologies: These systems can provide continuous data by using integrated sensors that relay information about the environmental conditions surrounding the aluminum.
Combining these techniques with routine maintenance enhances the resilience of aluminum structures. Therefore, investing in both corrosion testing and monitoring systems is prudent not only to safeguard investments but also to uphold safety and performance standards in various applications.
Economic and Environmental Implications
Consideration of the economic aspects includes the initial investment in corrosion protection strategies, such as coatings, inhibitors, and design adjustments. While the upfront costs may seem high, the long-term savings on maintenance and replacement parts can outweigh these costs. A well-executed corrosion protection plan can extend the lifespan of aluminum structures and components, resulting in reduced spending in the long run.
Additionally, aluminum corrosion can disrupt production processes, leading to unanticipated downtimes, which may further impact profitability. Analyzing the cost-benefit ratio of protective measures allows stakeholders to make informed decisions about investing in effective solutions.
"The long-term benefits of investing in corrosion prevention greatly exceed the initial costs involved."
Environmental considerations are equally significant. The production and disposal of aluminum, along with its corrosion-related issues, can have a considerable impact on the environment. By minimizing corrosion, industries can reduce waste and lower the carbon footprint associated with the manufacturing of new aluminum products. Choosing sustainable corrosion protection methods can lead to better resource utilization and overall ecological benefits.
Cost-Benefit Analysis of Protection Strategies
A cost-benefit analysis serves as a powerful tool for evaluating the viability of various corrosion protection strategies. By assessing both costs and expected benefits, organizations can make choices that align with their economic goals while safeguarding their aluminum assets.
Key points to consider in this analysis include:
- Initial Investment: The upfront costs required for protective coatings, inhibitors, or design changes.
- Maintenance Costs: Ongoing expenses associated with monitoring and maintaining protective measures.
- Replacement Costs: The financial implications of having to replace corroded aluminum components.
- Operational Downtime: Calculating potential productivity losses due to corrosion-related failures.
Implementing a thorough cost-benefit analysis allows stakeholders to identify which strategies result in significant savings over time, ensuring that they spend resources wisely.
Sustainability in Corrosion Protection
Sustainability is becoming increasingly important in corrosion protection strategies for aluminum. This shift arises from growing awareness of environmental concerns and the need for efficient resource management. By adopting sustainable practices, industries can not only protect their aluminum assets but also contribute positively to the environment.
Using eco-friendly materials for coatings and inhibitors helps to minimize harmful emissions and waste. Considerations for sustainability might include:
- Biodegradable Coatings: Choosing coatings that break down naturally over time reduces environmental harm.
- Recycling: Implementing recycling schemes for aluminum products can help mitigate waste.
- Life Cycle Assessment: Evaluating the entire life cycle of aluminum products ensures that decisions made are environmentally sound.
Future Directions in Corrosion Protection
The study of aluminum corrosion prevention is evolving rapidly, with innovations emerging to enhance the durability and lifespan of aluminum products. As industries continue to adopt aluminum due to its lightweight and strength, understanding future directions in corrosion protection is essential. This section explores key aspects that are shaping the future of aluminum protection strategies.
Emerging Technologies
Emerging technologies are at the forefront of enhancing corrosion protection for aluminum. These advancements aim to increase the effectiveness and efficiency of protective methods. Some notable technologies include:
- Nanocoatings: These coatings provide a protective layer at the nanoscale. They improve corrosion resistance and reduce surface roughness while maintaining the aluminum's lightness.
- Self-healing Coatings: Projects in this area focus on coatings that can autonomously repair scratches or damage. This capability significantly extends the protective life of aluminum surfaces.
- Smart Coatings: These intelligent systems can detect environmental changes and initiate protective actions, improving corrosion resistance proactively.
These technologies not only enhance performance but also may lead to reduced maintenance costs and increased safety for aluminum applications across different sectors.
Research Trends and Challenges
The field of corrosion protection is dynamic. Researchers are investigating various avenues to overcome challenges associated with aluminum materials. Some ongoing trends are:
- Biodegradable Inhibitors: There is a growing interest in developing environmentally friendly corrosion inhibitors derived from natural sources. These offer the possibility of reducing the ecological footprint of traditional chemical inhibitors.
- Advanced Computational Methods: Simulation and modeling aid in understanding corrosion processes better. These tools can predict material performance more accurately, leading to innovative designs that are less prone to corrosion.
However, challenges remain. The complexity of corrosion mechanisms and the need for interdisciplinary collaboration makes research intricate. Accelerating discoveries while addressing environmental concerns will demand focus and resource allocation in coming years.
"The future of aluminum corrosion protection lies in cooperation among academia, industry, and regulatory bodies to foster sustainable and innovative solutions."
Ending
The topic of corrosion protection for aluminum is vital in various sectors, including construction, automotive, and aerospace. As industries increasingly rely on aluminum for its lightweight and strength, understanding and implementing effective protection strategies becomes crucial.
Summary of Key Takeaways
To summarize, several key points emerge from this discussion:
- Understanding Corrosion: Recognizing how different types of corrosion affect aluminum is essential for proper management.
- Protective Measures: Coatings such as anodizing and the use of corrosion inhibitors can significantly enhance the longevity of aluminum components.
- Economic Benefits: Investing in corrosion protection not only prolongs the lifespan of products but also contributes to substantial cost savings over time.
- Environmental Considerations: In exploring sustainable methods, the industry is becoming increasingly cautious about the environmental impact, aligning technology advances with eco-friendly practices.
Importance of Ongoing Research
Continuous research in corrosion protection technologies is critical. Further innovations in materials and coatings could lead to better performance and sustainability. Researchers are looking for ways to:
- Enhance Existing Technologies: Improving current methods like anodizing, or developing new types of coatings that provide longer-lasting protection.
- Address Emerging Challenges: As aluminum applications expand, new forms of corrosion could become prevalent, requiring innovative solutions.
- Investigate Eco-Friendly Options: The movement toward sustainability is prompting research into methods that are less harmful to the environment while still effective against corrosion.
Overall, corrosion protection for aluminum is not just about making products last longer; it encompasses economic savings, environmental responsibility, and the advancement of technology.