Understanding Piezoelectric Actuators: Principles and Applications
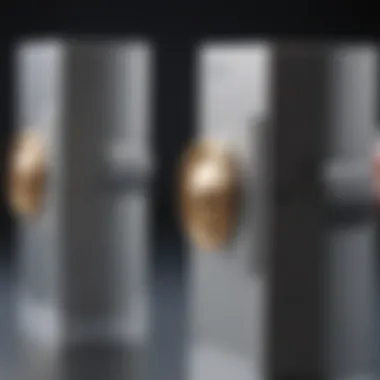
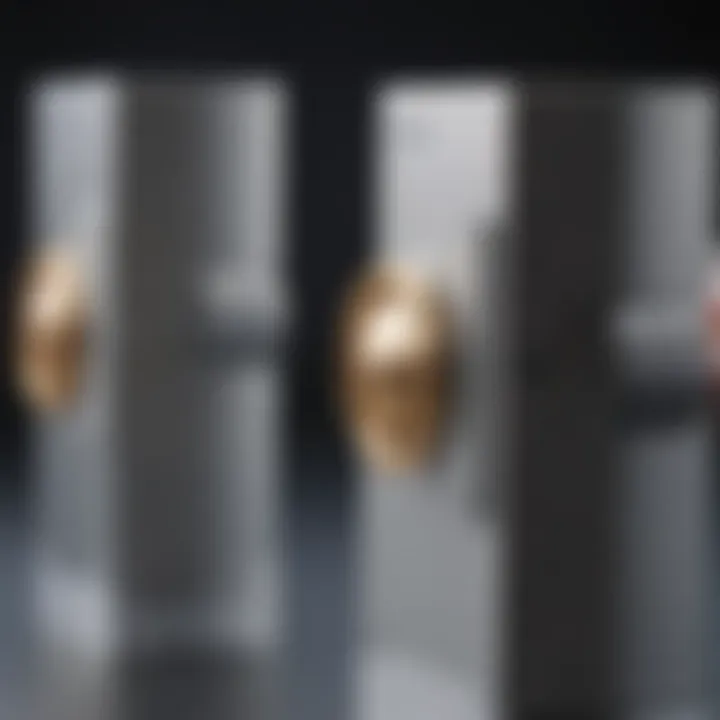
Intro
Piezoelectric actuators represent a unique category of devices utilizing the piezoelectric effect to convert electrical energy into mechanical motion. Their significance in various fields, such as robotics, aerospace, and medical devices, cannot be overstated. This article aims to provide a comprehensive overview of piezoelectric actuators, delving into their principles, underlying mechanics, and widespread applications. By illuminating the latest advancements in technology, this discussion seeks to cater to an audience that ranges from students and researchers to industry professionals.
Research Overview
The exploration of piezoelectric actuators has unveiled numerous key findings that highlight their importance in industrial applications. Below is a summary of these findings:
Summary of Key Findings
- Mechanics of Action: The primary operation principle of piezoelectric actuators is based on the piezoelectric effect, where certain materials deform when subjected to an electric field.
- Types of Actuators: Diverse actuator types include stack actuators, bimorphs, and ultrasonic transducers. Each type has distinct characteristics suited for specific applications.
- Advantages: These devices typically exhibit precise control, rapid response times, and high efficiency, making them appealing for engineers.
- Applications: Key sectors include robotics, optical systems, and medical devices such as surgical instruments. Their ability to achieve micro-level positioning and controlled movement is noteworthy.
Importance of the Research
Understanding piezoelectric actuators is crucial for advancing technologies in several domains. Their applications can enhance precision in manufacturing and improve safety and efficacy in medical devices. Moreover, ongoing research fosters innovation in actuator design, material selection, and integration techniques, which can lead to performance improvements and cost reductions.
Important Variables
When studying or implementing piezoelectric actuators, several factors deserve attention:
- Material Selection: The choice of piezoelectric materials, such as lead zirconate titanate (PZT) and polyvinylidene fluoride (PVDF), profoundly affects performance characteristics.
- Performance Parameters: Key metrics include displacement sensitivity, bandwidth, and hysteresis.
- Integration Techniques: Understanding how to integrate actuators with control systems is critical for achieving desired performance outcomes.
- Market Trends: Awareness of current market trends can guide future research and development efforts, including potential opportunities for new innovations in actuator technology.
"Piezoelectric actuators stand at the intersection of electrical engineering and materials science, embodying a rich field of study and application."
This overview serves as the foundation for a deeper exploration into the principles and applications of piezoelectric systems, setting the stage for more detailed examination of their mechanics and significance in technology.
Prologue to Piezoelectric Actuators
Piezoelectric actuators are essential devices in modern technology that harness the unique properties of certain materials to convert electrical energy into mechanical motion. Their ability to produce precise movements with high accuracy makes them invaluable in various applications such as robotics and medical devices. Understanding the principles underlying piezoelectric actuators is crucial for engineers and researchers, as it opens up avenues for innovation and improvement in several fields.
Definition and Basic Concepts
A piezoelectric actuator operates on the principle of piezoelectricity, which is the ability of certain materials to generate an electric charge in response to applied mechanical stress. Conversely, these materials can change shape when an electric field is applied. This bidirectional behavior is what makes piezoelectric actuators a key component in precision control systems. The mechanism relies on specific materials like piezoelectric ceramics, polymers, and crystals that possess this unique property. These actuators are typically classified into various types, each with distinct functionalities and uses. The basic concept centers around the conversion of electrical signals into mechanical displacement or motion, allowing for exact positioning in applications ranging from scientific instruments to industrial automation.
Historical Development
The journey of piezoelectric actuators began in the early 20th century, notably around 1880, when Pierre and Jacques Curie discovered the piezoelectric effect. This foundational work laid the groundwork for further exploration. Over the decades, advancements in material science and fabrication techniques have significantly enhanced the performance and reliability of piezoelectric devices. In the 1950s, the introduction of synthetic piezoelectric ceramics such as lead zirconate titanate (PZT) revolutionized the field. These materials exhibited superior properties compared to naturally occurring ones, enabling more practical and efficient actuator designs. Since then, piezoelectric technology has evolved to support a wide array of sophisticated applications.
"The development of piezoelectric actuators has transformed industries by enabling unprecedented levels of control and precision."
Today, piezoelectric actuators are not just a niche technology but a crucial element in sectors such as manufacturing, healthcare, and aerospace. As innovations continue, the potential applications expand further, making it imperative to understand both their fundamental principles and their practical implementations.
Principles of Piezoelectricity
The principles of piezoelectricity are foundational to understanding how piezoelectric actuators function and their applications. This section delves into the underlying mechanisms and the materials involved, both of which are crucial for harnessing the piezoelectric effect. By comprehending these principles, one can appreciate how various materials convert mechanical stress into electrical energy and vice versa. This knowledge is indispensable for fields such as robotics, medical devices, and precision positioning systems, where precise movement control is essential.
Fundamental Mechanisms
At its core, the piezoelectric effect arises from the unique arrangement of atoms within certain materials. When external mechanical stress is applied to these materials, the internal charge distribution shifts, leading to a generation of electric charge. Conversely, when an electric field is applied, it deforms the material, causing it to change shape. This duality is what makes piezoelectric materials particularly useful for actuators. The efficiency and response time of these mechanisms are critical for applications requiring high precision.
Materials and Their Properties
The choice of material plays a vital role in the performance of piezoelectric actuators. Various materials exhibit different piezoelectric properties, making some more suitable for specific applications than others.
Piezoelectric Ceramics
Piezoelectric ceramics are among the most commonly used materials. They are known for their high piezoelectric coefficients, which translate to efficient energy conversion. A significant characteristic of piezoelectric ceramics is their robustness against environmental influences, such as temperature and humidity. This property makes them suitable for use in critical applications where durability is essential. However, they can be brittle, which may limit their use in certain dynamic environments.
Polymeric Materials
Polymeric materials, like polyvinylidene fluoride (PVDF), are another class of piezoelectric substances. These materials offer flexibility, which can be advantageous in applications requiring conformability or lightweight components. A key characteristic is their ability to maintain piezoelectric properties over a wide temperature range. Nonetheless, their lower piezoelectric constants compared to ceramics may limit their effectiveness in high-performance applications. They are often selected for applications where mechanical flexibility is needed.
Single-Crystal Materials
Single-crystal materials provide high efficiency and excellent performance due to their uniform atomic structure. This uniformity allows for optimized piezoelectric responses. A defining characteristic of single-crystal materials is the ability to tailor their properties through growth techniques, which enables the production of highly specific devices. While they offer superior performance, the challenge lies in the higher manufacturing costs and complexities associated with their production. Despite this, their unique advantages make them a popular choice in cutting-edge applications, such as aerospace and advanced medical devices.
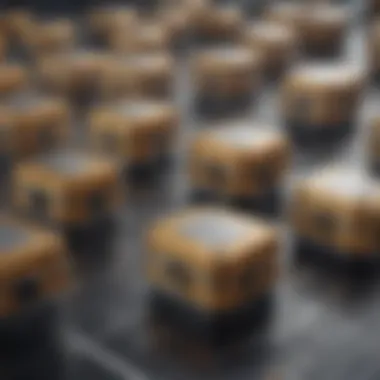
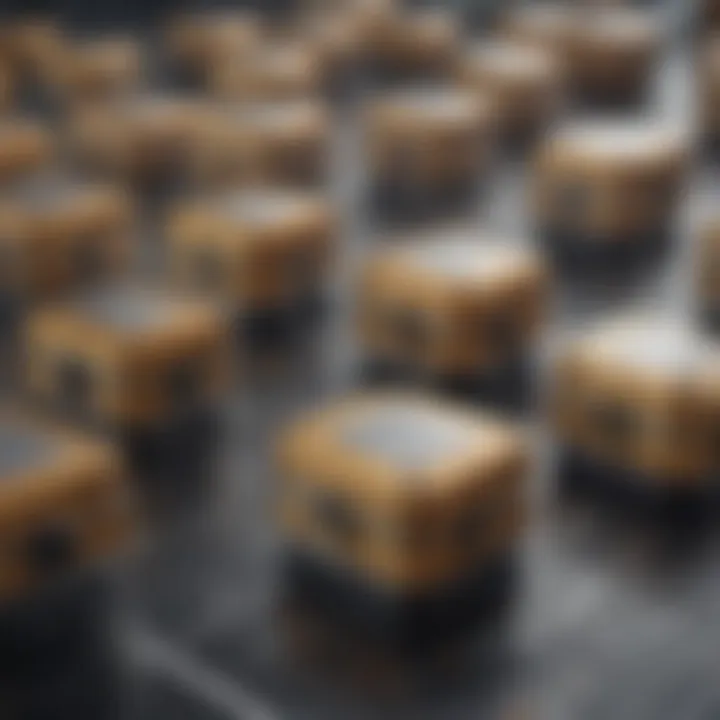
Types of Piezoelectric Actuators
Understanding the various types of piezoelectric actuators is essential for grasping their application across different fields. Each type has unique characteristics, advantages, and specific use cases. These actuators leverage the piezoelectric effect to convert electrical energy into mechanical motion. The choice of actuator often depends on application requirements such as displacement, force, frequency response, and design constraints. This section will detail the three main types: stack actuators, bender actuators, and shear mode actuators.
Stack Actuators
Stack actuators are composed of several piezoelectric layers stacked on top of one another. This configuration amplifies the total displacement and force output. The collective movement is achieved through the principle of adding the displacements of each layer. Stack actuators offer high precision and can produce significant thrust, making them suitable for applications that require fine movements and high forces.
This type is commonly used in precision positioning applications, such as optical systems, where minute adjustments are critical. Another benefit is their compactness, allowing them to fit into restricted spaces without sacrificing performance. However, their complexity in design and material stress at high loads can be potential drawbacks that engineers need to manage carefully.
Bender Actuators
Bender actuators function through a different mechanism. These actuators bend when an electrical voltage is applied across them. This bending motion enables them to convert electrical signals into physical displacement efficiently. Bender actuators are valued for their simplicity and versatility, making them popular in applications ranging from audio devices to micro-positioning systems.
Their design typically prioritizes low-profile configurations. One of the notable characteristics of bender actuators is their capability to operate in a variety of environments, including those with vibration or thermal changes. However, the displacement generated by a single bender is often lower compared to stack actuators, which necessitates their use in applications where lower forces are sufficient.
Shear Mode Actuators
Shear mode actuators operate differently from stack and bender types. By applying the electric field parallel to the electrodes, these actuators generate motion through shear deformation. This mechanism tends to provide a more stable output with lower hysteresis, which can be advantageous for applications that require consistent performance.
Shear mode actuators find their use in devices where precision is key, such as in sensors and advanced robotics. They can produce longer strokes at lower voltages, thus improving energy efficiency. Yet again, these actuators may not deliver the same power output as stack actuators, so choosing the right actuator depends on the specific requirements of the project.
"The selection of a piezoelectric actuator should consider the detailed requirements of the application, including desired performance characteristics and environmental conditions."
In summary, understanding these types aids in choosing the right actuator for various applications in modern technology. Each type brings its strengths and weaknesses, and their application contexts often dictate the best selection.
Performance Characteristics
Performance characteristics of piezoelectric actuators are essential to understand their capabilities and limitations. These characteristics determine how well the actuators can perform their intended functions across various applications. Key elements include displacement and force output, frequency response, efficiency, and linearity. By evaluating these factors, engineers can select suitable actuators for specific use-cases, thereby enhancing system reliability and performance.
Displacement and Force Output
Displacement in piezoelectric actuators refers to the movement produced when an electric field is applied. It is often measured in micrometers, showcasing how much the actuator can extend or contract. The force output is the amount of force the actuator can generate while performing work. Both displacement and force output are crucial in applications where precise movements are necessary, such as in robotics and medical devices.
- Factors affecting displacement include:
- Max force output relates directly to:
- The material composition of the actuator
- The design configuration, such as stack or bender actuators
- The actuator's mechanical design
- The electric field strength applied
This relationship indicates the balance needed when selecting an actuator; too much focus on displacement may compromise force output, and vice versa.
Frequency Response
Frequency response defines how quickly an actuator can respond to an input signal. In piezoelectric systems, this characteristic is vital because it influences the actuator's ability to operate at high speeds or in dynamic environments. The response is typically measured in Hertz (Hz), indicating the number of cycles per second the actuator can execute.
- High-frequency operation enables:
- Considerations include:
- Precision control in applications like optical positioning
- Rapid actuation in electronic components
- Damping effects, which can lessen responsiveness
- Resonance in the actuator, which can affect performance
A good frequency response ensures the actuator can meet industry demands for speed and accuracy.
Efficiency and Linearity
Efficiency refers to how effectively a piezoelectric actuator converts electrical energy into mechanical energy. High efficiency implies that a larger portion of the input energy results in usable work rather than losses due to heat or vibration. This characteristic directly affects the overall energy requirements for driving the actuator.
- Factors influencing efficiency:
- Type of materials used
- Design configuration and constraints
Linearity is the degree to which the displacement produced corresponds directly to the input voltage. A linear actuator will have predictable behavior throughout its operational range. Nonlinear behavior can lead to unforeseen challenges in precise applications.
- Importance of linearity:
- Enables accurate modeling in control systems
- Provides predictability in positioning tasks
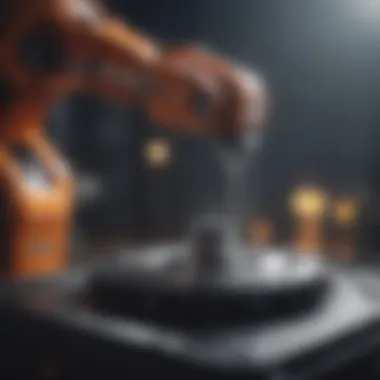
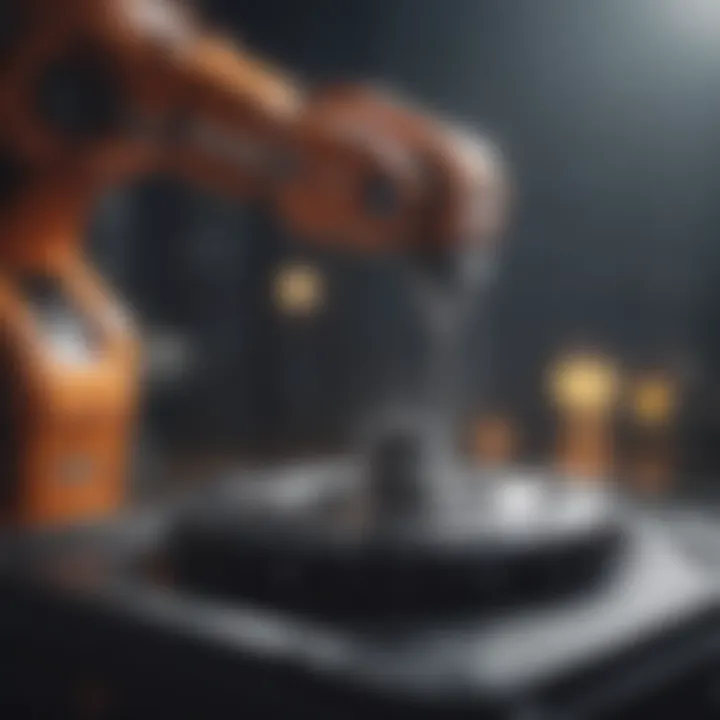
In summary, the performance characteristics of piezoelectric actuators — displacement and force output, frequency response, and efficiency and linearity — are vital considerations. They not only impact the actuator's operational capabilities but also determine its suitability for various applications. By understanding these properties, engineers can optimize systems for enhanced performance.
Applications of Piezoelectric Actuators
The applications of piezoelectric actuators are vast and have transformative effects across various sectors. These unique devices harness the piezoelectric effect, where materials generate mechanical strain when subjected to an electric field. This feature offers precision control, making piezoelectric actuators essential in numerous advanced applications. Their role in enhancing performance, efficiency, and technological innovation cannot be overstated. This section elaborates on some prominent application areas.
Robotics and Automation
In the realm of robotics and automation, piezoelectric actuators are crucial for enabling precise movement and control. These actuators can achieve rapid response times and high resolution, making them suitable for fine manipulation tasks. For instance, robotic arms used in assembly lines often integrate piezoelectric elements to provide quick adjustments and precise positioning.
Advantages of using piezoelectric actuators in robotics include:
- Compact size: They tend to be smaller than conventional motors, which makes them ideal for compact robots.
- Low power consumption: Their efficiency often leads to reduced energy requirements, allowing for longer operational times.
- High reliability: With fewer moving parts, piezoelectric actuators tend to require less maintenance.
Medical Devices
Medical devices significantly benefit from the precision that piezoelectric actuators offer. In surgical tools, for example, their ability to deliver fast and accurate movements makes procedures safer and more efficient. Devices such as needle injectors and ultrasound equipment use these actuators to achieve remarkable precision and control.
Key applications in healthcare include:
- Ultrasonic imaging systems, where piezoelectric transducers generate and receive sound waves for imaging purposes.
- Drug delivery systems, utilizing piezoelectric actuation to control the release of medication accurately.
- Surgical robotics, where the ability to perform fine operations with minimal invasiveness is essential.
Precision Positioning Systems
Precision positioning is critical in sectors require accurate movements, such as semiconductor manufacturing and optical alignment processes. Piezoelectric actuators provide the necessary precision with a high degree of repeatability. They can position components to the nanometer scale, which is vital in applications like fiber optic alignment or laser beam steering.
The benefits include:
- Sub-nanometer resolution: They can achieve extremely fine adjustments that are essential for various scientific instruments.
- Fast response rates: This allows for rapid repositioning, which is beneficial in dynamic environments.
- Stable positioning: They maintain high stability over time, ensuring reliability in long-term applications.
Energy Harvesting Devices
Energy harvesting is an emerging field where piezoelectric actuators play a significant role. These devices convert mechanical energy from various sources, such as vibrations or movements, into electrical energy. This technology is particularly valuable in scenarios where power sources are limited or where sustainability is a priority.
Notable applications include:
- Wearable technology, where piezoelectric elements can harvest energy from human motion to power small electronic devices.
- Structural health monitoring systems, using piezoelectric sensors to generate electrical signals from vibrations in infrastructure.
- Remote sensors, which can operate without external power sources, increasing energy efficiency and longevity.
The versatility of piezoelectric actuators across multiple industries highlights their importance in driving technological advancements and improving efficiency.
Integration Techniques
The topic of integration techniques is paramount when discussing piezoelectric actuators, as it involves aligning these devices into broader systems effectively. The performance of piezoelectric actuators often relies not just on their inherent properties but also on how they are integrated within mechanisms. Proper integration ensures that the actuators fulfill their roles in a precise and efficient manner.
For example, control strategies and mechanical designs must be carefully considered. When piezoelectric actuators are paired with suitable control systems, they can deliver enhanced responsiveness and precision. Control strategies directly impact how signals are processed and translated into movement, which is crucial for applications ranging from robotics to medical devices.
Mechanical design considerations also play an essential role in integration. The physical arrangement of the actuator within a system affects its efficiency. When designing a device that employs piezoelectric actuators, designers must think of how to minimize mechanical loads while optimizing the actuator’s performance.
Proper integration is essential to maximize the capabilities of piezoelectric actuators, ensuring optimal functionality in diverse applications.
Key elements in integration of piezoelectric actuators include:
- System Compatibility: The actuator must be compatible with existing mechanical and electrical systems.
- Actuator Positioning: Placement affects the application’s response time and precision.
- Control Algorithms: Algorithms should be finely tuned to translate input signals into precise actuator movement.
- Feedback Mechanisms: Sensors can provide data to adjust performance in real-time, enhancing accuracy.
Benefits of effective integration:
- Improved performance in applications where precision is crucial.
- Increased reliability and lifespan by reducing stress on the actuators.
- Enhanced overall system efficiency through better response times and behaviors.
In summary, understanding integration techniques is critical for leveraging the full potential of piezoelectric actuators. This not only involves designing effective control strategies but also entails thoughtful mechanical arrangements that cater to the specificities of each application.
Control Strategies
Control strategies for piezoelectric actuators are designed to regulate their movement accurately. A well-implemented control strategy employs feedback systems to adjust the actuator's position in real time. This may involve using PID (Proportional, Integral, Derivative) controllers, which are common in automatic control systems.
PID controllers allow for a balance between responsiveness and stability, making them suitable for applications where precision is vital. Additional strategies may include model predictive control or fuzzy logic controllers, which can handle non-linearities in system behavior more effectively. Understanding how to optimize these strategies not only enhances actuator performance but also expands their applications in fields such as robotics and aerospace.
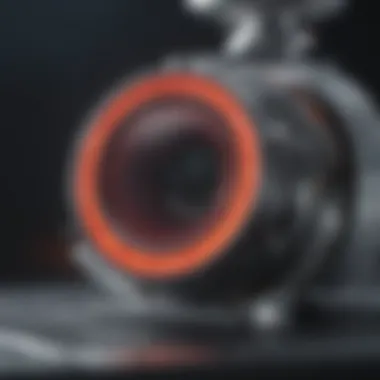
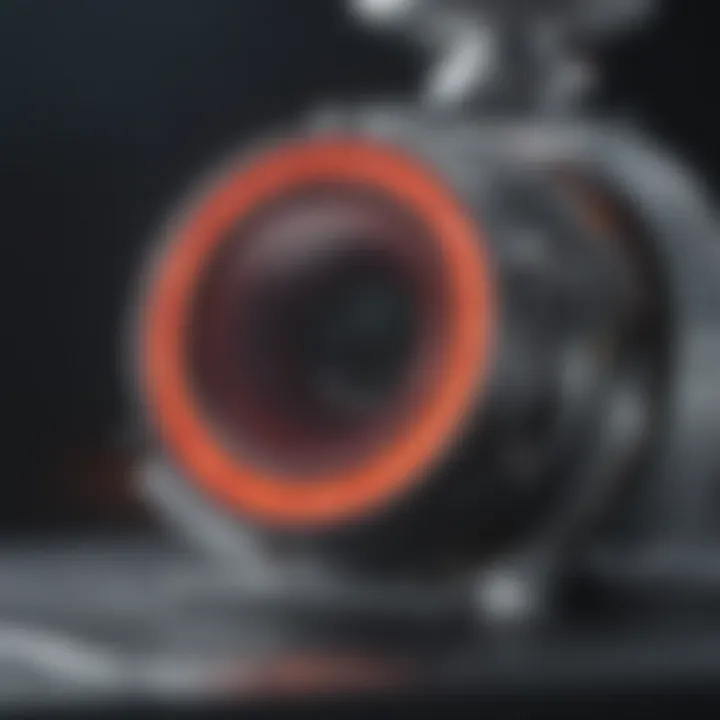
Mechanical Design Considerations
When considering mechanical design aspects, it’s important to evaluate how piezoelectric actuators will be assembled within a system. Design must take into account the actuator’s dimensions, mounting arrangements, and load capacities. Accurately calculating forces and ensuring minimal backlash will help attain higher accuracy levels, which are critical in applications such as optics and semiconductor equipment.
Challenges in Piezoelectric Technology
The field of piezoelectric technology carries significant promise, yet it is not without its hurdles. Understanding these challenges is essential for pushing advancements in this area. Material limitations, fabrication issues, and cost considerations are three prominent obstacles that researchers and engineers face. Addressing these challenges can enhance the performance and feasibility of piezoelectric actuators in various applications.
Material Limitations
Material selection plays a critical role in the performance of piezoelectric actuators. Most actuators rely on specific types of materials that can exhibit piezoelectric properties effectively. The most common materials include piezoelectric ceramics such as lead zirconate titanate. However, these materials have limitations in terms of mechanical strength and temperature stability. They tend to be brittle, which makes them vulnerable to cracking under stress.
Additionally, current materials often have restricted operational bandwidths. For instance, high-temperature applications might require special materials that can withstand heat, which are often not as efficient in piezoelectric properties. The pursuit of new and improved materials is ongoing, with researchers exploring options like polymeric materials and single-crystal configurations. The exploration of more durable and versatile materials may resolve some existing limitations, paving the way for future innovations.
Fabrication Issues
The fabrication of piezoelectric devices presents another layer of complexity. The processes involved often require precise control of various parameters, including temperature, pressure, and electrical fields. Any deviation during manufacturing can lead to defects in the piezoelectric ceramics which directly impacts their functionality.
Moreover, scaling up production while maintaining quality is a significant challenge. As demand increases across industries, manufacturers often struggle with the balance between cost-efficiency and product quality. Advanced techniques, such as 3D printing and additive manufacturing, have shown potential to address these fabrication issues. However, more development is needed to ensure these methods can produce commercially viable piezoelectric actuators.
Cost Considerations
Cost remains a fundamental challenge in piezoelectric technology. The materials often used in high-performance piezoelectric actuators, like lead-based ceramics, may not only be costly, but they are also subjected to regulatory scrutiny due to environmental concerns. These factors contribute to higher production costs, making it difficult for certain industries to adopt piezoelectric technology at scale.
Furthermore, the lack of widespread understanding of the advantages and applications of piezoelectric actuators can limit market growth. Investing in awareness and education can help to offset some cost concerns, but initial investment remains a barrier for broader implementation.
Addressing the challenges in piezoelectric technology could redefine applications in areas such as robotics, medical devices, and precision engineering.
Future Perspectives
The topic of future perspectives in piezoelectric actuators is crucial as it encapsulates the directions and innovations that may shape the landscape of technology. This section delves into two significant components: emerging materials and techniques, and the trends within the market and innovations. Both elements are instrumental in understanding how piezoelectric actuators can evolve to meet increasing demands across various applications.
Emerging Materials and Techniques
Recent developments in materials science are paving the way for novel piezoelectric materials that promise improved performance. Researchers are focusing on composites and nanomaterials that exhibit enhanced piezoelectric properties. For instance, materials such as lead-free sodium-potassium niobate offer a more environmentally friendly alternative to traditional lead-based ceramics.
These emerging materials are not just about sustainability but also open new avenues in actuator miniaturization and energy efficiency. Techniques such as additive manufacturing have attracted attention, enabling the fabrication of complex geometries not possible with conventional methods. By harnessing these advanced materials and techniques, engineers can develop actuators that are not only more efficient but also adaptable to various applications, including robotics and medical devices.
"The advancement in piezoelectric materials will likely dictate the performance limits of actuators in the next decade."
Market Trends and Innovations
The market for piezoelectric actuators is experiencing a shift as industries seek more precise and efficient solutions. There's a noticeable trend towards the integration of piezoelectric technology in consumer electronics, automotive systems, and aerospace applications. This shift is driven by the push for smarter devices and increased automation.
Innovations in control systems and software that manage piezoelectric actuators are also fundamental. The ongoing research into machine learning algorithms will likely enhance performance by optimizing response times and reliability in real-time applications.
Furthermore, the development of piezoelectric devices that can harvest energy from ambient sources is becoming an attractive prospect. This feature can lead to self-sustaining systems that mitigate the dependence on traditional power sources.
The End
The conclusion serves as an essential segment of this article, summarizing the core themes and insights acquired throughout the discussion of piezoelectric actuators. By synthesizing the major elements, it encapsulates the intricate relationship between theory and application. This section is beneficial not only for reinforcing key takeaways but also for framing the topic within the broader context of technological advancements and endless possibilities that piezoelectric systems present.
One primary element addressed is the adaptability of piezoelectric actuators in various fields, from robotics to medical technology. By highlighting their crucial role in precision movements and automation, readers gain a clear understanding of their significance in enhancing efficiency and effectiveness in various applications. Furthermore, the ongoing advancements in materials and manufacturing techniques could suggest that the future is promising for further integration of these actuators in diverse industries.
The summary enhances the article’s scope, allowing scientists, researchers, and professionals to contemplate how piezoelectric actuators can influence their work. Such insights underscore the need for continued exploration into their capabilities, addressing challenges and maximizing benefits.
"The potential for innovation in piezoelectric technology represents an exciting frontier in engineering and applied sciences."
Summary of Key Insights
The key insights presented throughout the article emphasize multiple aspects of piezoelectric actuators:
- Understanding the principles of piezoelectricity provides a foundation for grasping how these actuators operate.
- Different types, including stack, bender, and shear mode actuators, each serve unique applications.
- Performance characteristics such as displacement, frequency response, and efficiency are critical for evaluating the efficacy of actuators.
- The integration of piezoelectric technology into fields like robotics and medical devices shows great potential for future innovations.
Each of these insights contributes to a holistic view of piezoelectric actuators in modern technology. It elucidates their diverse applications and encourages readers to delve deeper into ongoing research and development.
Implications for Future Research
As piezoelectric technology continues to evolve, several implications arise for future research:
- Material Innovation: There is an ongoing need to explore new materials that can enhance piezoelectric properties. Research into composite materials and nanostructures could yield improvements.
- Application Expansion: Future research should focus on expanding the applications of piezoelectric actuators into emerging fields like renewable energy harvesting and smart material integration.
- Cost Reduction: Investigating ways to reduce manufacturing costs while maintaining high-quality performance will be crucial for broader adoption of these technologies.
- Control Systems Development: Developing advanced control strategies could improve precision and responsiveness in actuator performance across applications.
By addressing these research areas, professionals and researchers can facilitate further advancements and ensure that piezoelectric actuators remain at the cutting edge of technology. The continuous exploration and understanding of piezoelectric systems promise a transformative impact on various sectors, inviting ongoing dialogue and investigation.